Stay Up to Date
Submit your email address to receive the latest industry and Aerospace America news.
The Electric Propulsion Technical Committee works to advance research, development and application of electric propulsion for satellites and spacecraft.
Industry and government engineers made key advancements this year on electric propulsion for science spacecraft, commercial communications satellites, cubesats and human exploration missions.
Eight colloid micronewton thrusters on the European Space Agency’s LISA (Laser Inteferometer Space Antenna) Pathfinder spacecraft were commissioned in February during the spacecraft’s journey to its demonstration location in space, and then began counteracting disturbance forces to enable the science mission’s gravimetric measurements. The thrusters, developed by Busek Space Propulsion and Systems in collaboration with NASA’s Jet Propulsion Laboratory, now provide precision spacecraft control in normal operations and are the first operational electrospray thrusters in space.
The primary mission for the Dawn probe ended in June after it investigated the dwarf planet Ceres, but NASA approved an extended mission around the planet. Dawn’s xenon-fueled ion propulsion system has operated for more than 48,000 hours and provided an acceleration of over 11 kilometers per second, both records.
Qualification testing of the PPS 5000 Hall thruster has begun at Safran Aircraft Engines, and the first flight set is nearing completion for an expected flight in 2017. The European Space Agency, Thales Alenia Space, and Airbus Defense and Space jointly selected the 5-kilowatt PPS 5000 for the Neosat new-generation telecommunications satellite platform. The first PPS 1350 Hall thrusters are being readied for delivery to Space Systems Loral. The first arcjet system, developed and built by Aereojet Rocketdyne for Boeing’s 702 satellites, launched Aug. 24 on Intelsat 33e.
On the Asteroid Redirect mission, Boeing, Lockheed Martin, Orbital ATK, and Space Systems Loral completed solar electric design studies for the unmanned phase of the mission, called Asteroid Redirect Robotic Mission, or ARRM. NASA’s Glenn Research Center in Ohio and JPL have continued development of a 12.5 kilowatt Hall thruster system through wear testing, environmental testing, and integration testing of the thruster and power processing unit. ARRM entered phase B, meaning the definition phase, in August and is targeting a launch readiness date of December 2021. NASA’s Evolutionary Xenon Thruster-Commercial project, or NEXT-C, completed a preliminary design review and received approval to transition to the implementation phase. The NEXT-C system is the baseline ion propulsion system for the Double Asteroid Redirection Test, led by Johns Hopkins University Applied Physics Laboratory.
George Washington University developed a 4-microcathode arc thruster propulsion system for CANYVAL-X, short for Cubesat Astronomy by NASA and Yonsei University using the Virtual Telescope Alignment Experiment. This is a cubesat technology demonstration mission by NASA’s Goddard Space Flight Center and Yonsei designed to validate technologies that allow two spacecraft to fly in formation along an inertial line of sight.
Busek, of Massachusetts, in collaboration with Glenn, is developing the newest generation of 100-micronewton electrospray propulsion subsystems. Flight hardware delivery for the six-unit cubesat Pathfinder Technology Demonstrator mission, led by NASA’s Ames Research Center, is scheduled for 2017. Iodine electric propulsion continues with two Space Launch System Exploration Mission-1 payloads using iodine radio-frequency ion thrusters and the iodine satellite project to demonstrate iodine Hall thruster propulsion. Development of iodine propulsion components continues at Busek, Glenn, Colorado State University, NASA’s Marshall Space Flight Center and VACCO Industries of California.
NASA continued work on 100 kW subsystems for human exploration. Aerojet Rocketdyne, the University of Michigan, JPL and Glenn are developing a nested-channel Hall thruster, which has been operated to thermal steady state at 16 kW. ★
Stay Up to Date
Submit your email address to receive the latest industry and Aerospace America news.
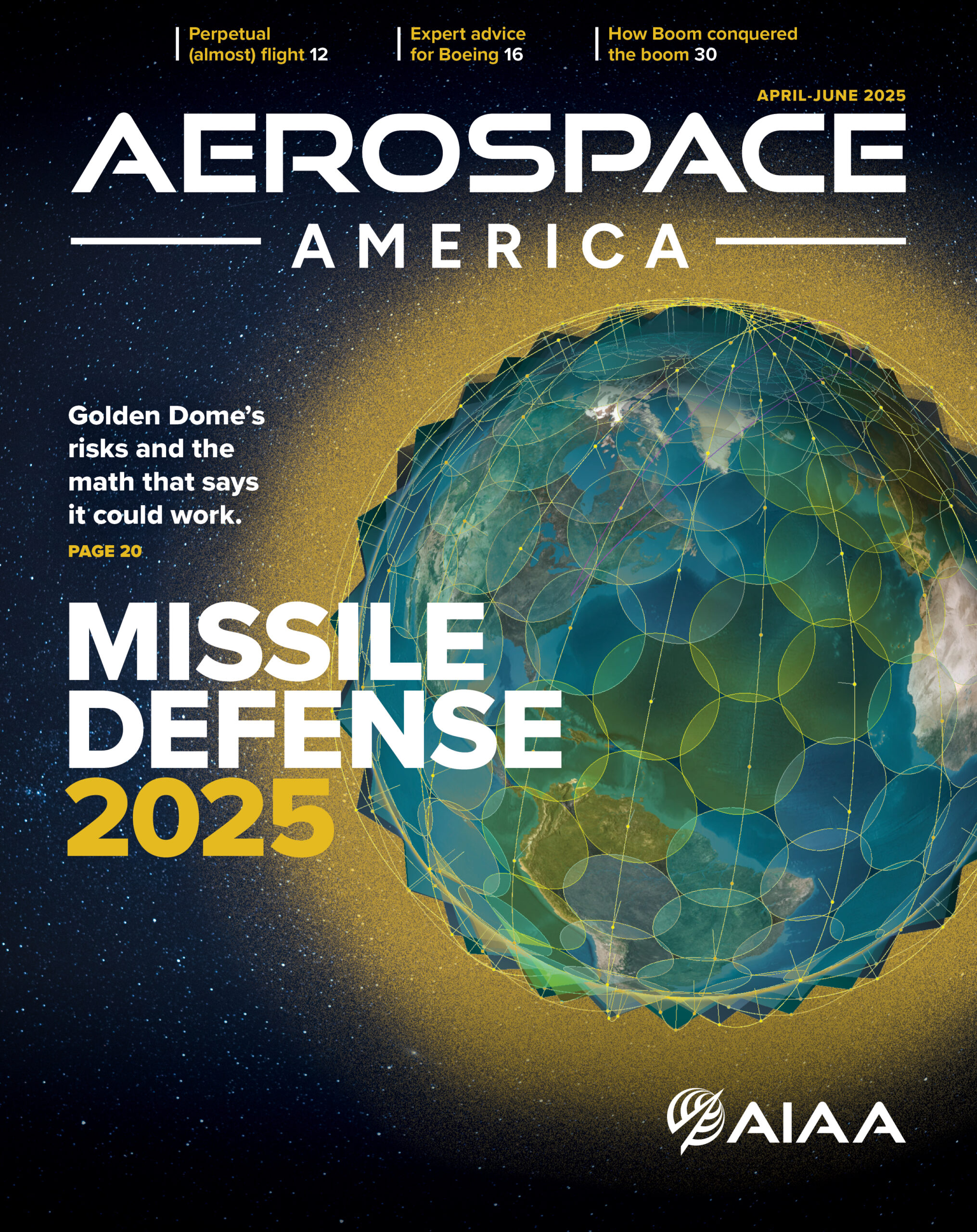