Stay Up to Date
Submit your email address to receive the latest industry and Aerospace America news.
The Structures Technical Committee works on the development and application of theory, experiment and operation in the design of aerospace structures.
Mississippi State University’s ongoing delamination studies with the U.S. Air Force Research Lab, or AFRL, continued this year with the primary objective to increase composite delamination resistance by optimizing stitching parameters for the university’s Marvin Dow Advanced Composites Institute’s unique 3D stitching capabilities. Experimental setups designed to load samples under idealized delamination modes were used to investigate the ability to capture delamination front shapes and locations. To date, measured strains compare favorably with finite element results.
Under an AFRL contract that will continue into 2019, Boeing investigated two different progressive damage and failure analyses, developed by the University of Texas–Arlington, to accurately predict damage initiation and progression in military aircraft composite components by comparing analytical and experimental results. Boeing’s fabricated hat-stiffened composite skin replicates mechanically fastened aluminum ribs. AFRL tested two configurations: skins under constant compression with rib pull-off in static and fatigue loadings, and rib pull-off performed in 4-point bend without end loading in static and fatigue modes. Good correlation was seen between predictions and test results, improving the Air Force’s ability to safely extend service longevity.
Engineers at NASA’s Marshall Space Flight Center in Alabama installed structural test hardware for NASA’s deep space rocket, the Space Launch System, and began testing. The test hardware is structurally identical to the intertank flight hardware that connects the core stage’s two fuel tanks, serves as the upper-connection point for two solid rocket boosters, and houses critical electronics. The test facility’s cranes and design features duplicate extreme spaceflight conditions. The SLS hardware is pushed, pulled and bent with thousands of kilonewtons to ensure it can withstand launch and ascent forces.
In aircraft modeling, engineers at the University of Pisa and San Diego State University created an automatic finite element model generator to produce structural models of boxed-wing aircraft, known as PrandtlPlanes. The work was performed under a European Commission-funded project called PARSIFAL, short for PrandtlPlane Architecture for Sustainable Improvement of Future Airplanes. The aim is to demonstrate how the adoption of boxed-wing aircraft can bring significant improvements to air transportation.
In February, a biologist at Carleton University in Ottawa, Canada, while recording Nessus sphinx hawkmoth caterpillars emitting whistle-like sounds, could not determine the mechanism behind the sound. Subsequently, Carlton aerospace faculty performed aeroelastic studies that included plate and shell models combined with internal fluid flow to determine this mechanism. The sound was found to be generated by flow exiting the caterpillar’s stomach into its mouth, which acts like a resonator. This is the first time that a fluid-structure interaction has been identified as a sound generation mechanism in insect acoustics.
Meanwhile, the Air Force Institute of Technology worked on a range of Air Force engineering structural research topics, including continuing research on the internal-vacuum lighter-than-air vehicle (both NASA and the Air Force have shown interest), impact welding at velocities greater than 700 meters per second, hybrid composite structures, laser shock peening, sensor design, and heat flow around a sphere.
NASA’s Johnson Space Center in Texas and Langley Research Center in Virginia are examining the integrity of inflatable airlock structures for use on future deep space exploration missions and the lunar orbiting gateway. This year’s development work focused on an internal secondary structure, rigidizeable handrails, and soft opening hatches for quick ingress and egress and will continue into 2019. As part of NASA’s Aeronautics Research Mission Directorate Convergent Aeronautics Solutions program, Langley and NASA’s Ames Research Center in California and Glenn Research Center in Ohio in April completed the Multifunctional Structures for High Energy Lightweight Load-bearing Storage, or M-SHELLS, project, demonstrating production feasibility of multifunctional honeycomb sandwich panels where the core serves as a battery. Test results demonstrated that cores can sustain service level loads without any noticeable multifunctional performance degradation. System level studies of M-SHELLS cores in a 2030 single-aisle hybrid-electric transport aircraft indicate up to 11 percent potential mass savings vs. standard cores combined with separate batteries.
In the photo, a test version of the intertank for NASA’s Space Launch System rocket is readied for structural tests at NASA’s Marshall Space Flight Center in Alabama. The test article was pushed, pulled and bent this year to ensure the design can withstand launch and ascent. The tank is structurally identical to the one that will connect the core stage’s fuel tanks. Credit: NASA
Stay Up to Date
Submit your email address to receive the latest industry and Aerospace America news.
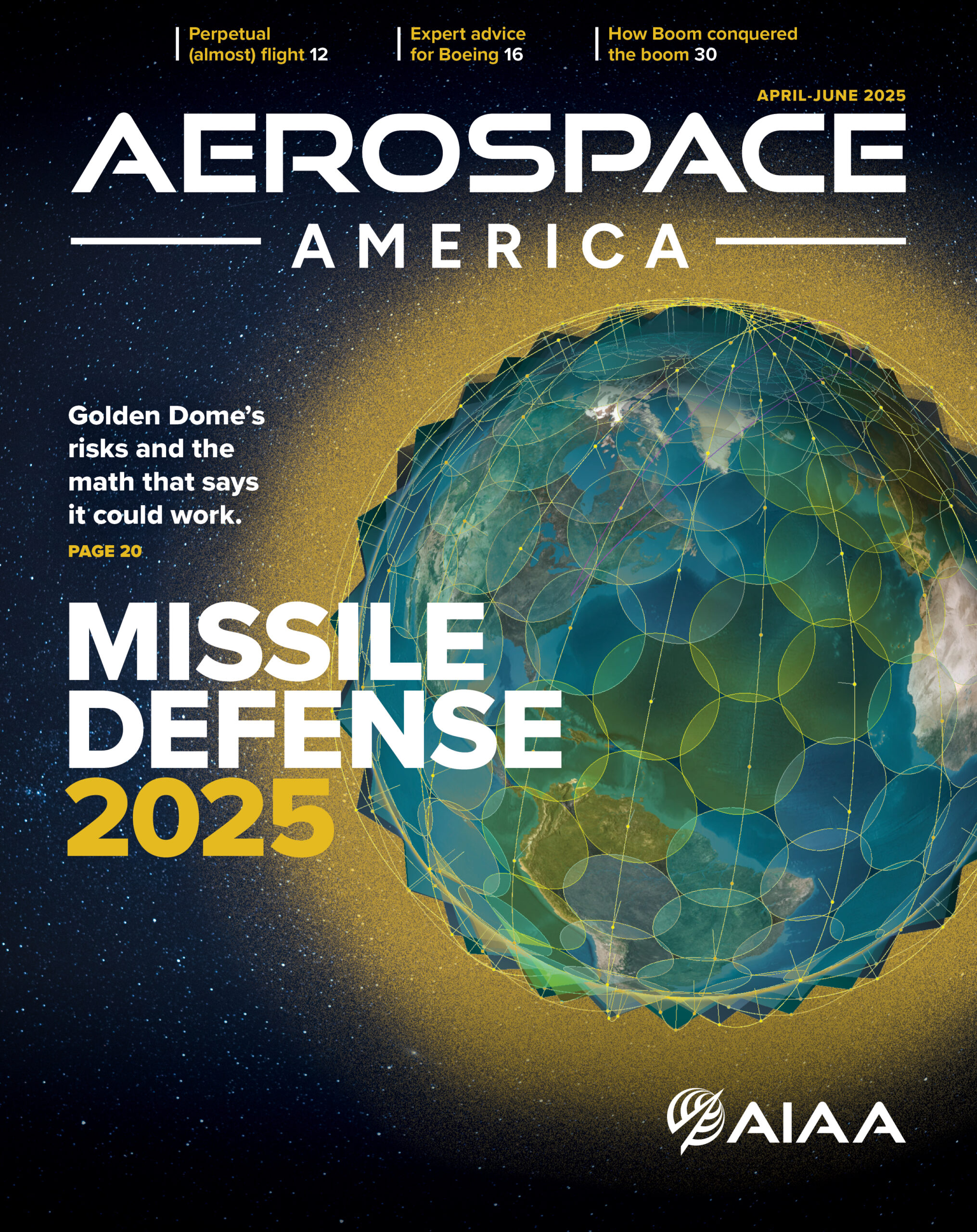