Stay Up to Date
Submit your email address to receive the latest industry and Aerospace America news.
The Aeroacoustics Technical Committee addresses the noise produced by the motion of fluids and bodies in the atmosphere and the responses of humans and structures to this noise.
In the field of urban air mobility noise, researchers at the University of Cincinnati’s Advanced Mobility Propulsion Lab conducted novel flow-field experiments on an electrically driven propulsor in March. The experimental measurements included time-resolved, phase-averaged velocity fields measured with high-speed particle image velocimetry and established relationships between the far-field acoustic measurements and the flow physics. The goal of this research is to improve the understanding of various installation effects on acoustic source mechanisms for propellers operating at low-tip Mach numbers.
The University of California, Davis extended the capabilities of the physics-based rotor broadband noise prediction tool UCD-QuietFly by coupling it with high-fidelity computational fluid dynamics under a November 2021 contract with Washington, D.C.-based Supernal, with plans to develop low-noise propeller designs using this computational tool. Many companies developing electric vertical takeoff and landing vehicles have adopted UCD-QuietFly. The latest software version, released in October, includes new predictive capabilities, including blade leading-edge noise and noise reduction through blade trailing-edge serrations.
Increasing bypass ratios of turbofan engines have changed acoustic liner requirements, necessitating novel approaches for design and optimization for low noise and reduced footprint. Penn State University and its Applied Research Laboratory in partnership with Raytheon Technologies Research Center in Connecticut and NASA’s Langley Research Center in Virginia are funded by FAA through the Aviation Sustainability Center to develop methods to rapidly design, manufacture and evaluate complex 3D structures as the next generation of acoustic liners. Throughout the year, the team designed, simulated, additively manufactured and tested several metamaterial-based liner backings and demonstrated significant acoustic tunability, highlighting their potential to enable more compact next-generation acoustic liners.
Under FAA’s Continuous Lower Energy, Emissions, and Noise initiative, or CLEEN III, North Carolina-based Collins Aerospace is advancing nacelle technologies, including novel acoustic liner cores for commercial turbofan engine exhausts, targeting low-frequency combustor noise. Development includes manufacturability validation confirming technology readiness for installation aboard next-generation passenger airliners. The team completed the exhaust acoustic conceptual design in April and fabricated novel core samples for mechanical testing in August. Ground testing is planned for 2025, targeting a cumulative reduction in effective perceived noise level of 0.9-1.5 decibels.
In June, NASA published a series of papers detailing the first comparisons between the Aircraft Noise Prediction Program, or ANOPP, and an extensive database of acoustic measurements collected with a Boeing 787 aircraft as part of Boeing’s 2020 ecoDemonstrator program. This assessment marks the first rigorous validation of ANOPP with modern flight test data and establishes a basis to further quantify the state of NASA’s predictive tool capabilities, to develop improvements in the fidelity of aircraft system noise predictions and to develop new noise reduction approaches.
Studying new airframe configurations, NASA performed the first system noise assessment of a single-aisle Transonic Truss-Braced Wing transport concept and published the results in June. This work highlighted the potential noise advantage of a TTBW relative to conventional tube-and-wing designs, stemming from the higher lift-to-drag ratio and improved propulsion-airframe aeroacoustic installation effects from the high-wing design. The paper, presented at the AIAA/Council of European Aerospace Societies’ Aeroacoustics 2022 conference, includes a roadmap to meeting NASA’s noise goal via noise reduction technologies and outlines a path to additional noise reduction for the TTBW design.
In a continuing effort by U.S. Naval Air Systems Command to reduce noise emitted from U.S. Navy aircraft with supersonic exhausts, engineers from the Naval Air Warfare Center Aircraft Division and GE Aviation analyzed, designed and fabricated prototypes of modified engine exhaust seals with chevron tips for noise reduction throughout the year. The team completed acoustic testing of ground and flyover operations of an F/A-18E Super Hornet aircraft with installed chevron exhaust seals to quantify the noise reduction potential.
Contributors: Jose Alonso, Daniel Cuppoletti, Jason June, Seongkyu Lee, Jeffrey Mendoza, Russell Powers, Timothy Simpson, Russell Thomas and Nickolas Zawodny
Stay Up to Date
Submit your email address to receive the latest industry and Aerospace America news.
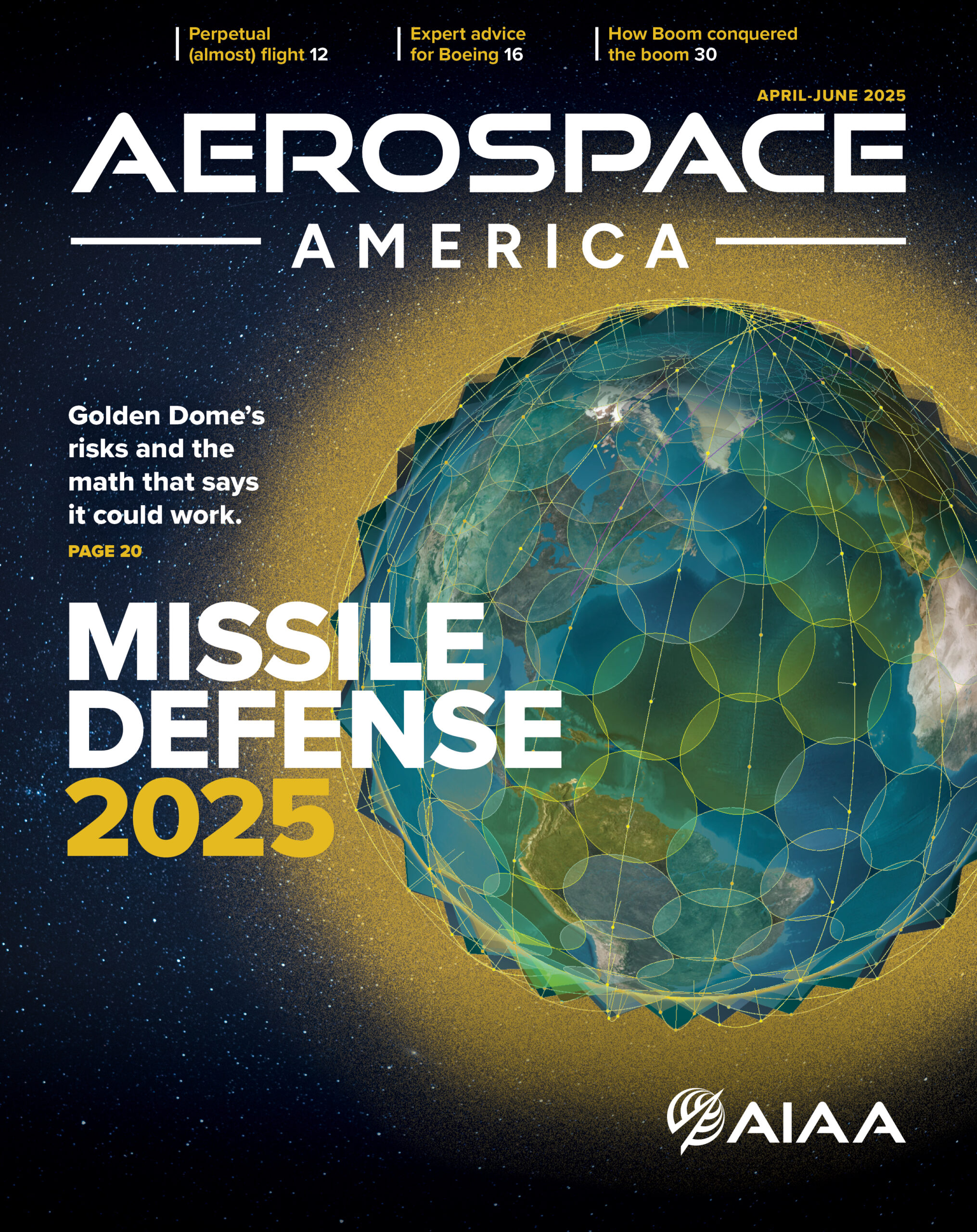