Stay Up to Date
Submit your email address to receive the latest industry and Aerospace America news.
The Hybrid Rockets Technical Committee studies techniques applied to the design and testing of rocket motors using hybrid rocket systems.
In the realm of academic research, several groups tackled fundamental problems in hybrid rocket combustion this year. Between January and March, the Propulsion Research Lab at Utah State University developed a new oxidizer for hybrid rockets. This oxidizer, called Nytrox, is blended by percolating oxygen under pressure into nitrous oxide until the solution reaches saturation. The addition of molecular oxygen mitigates the risk of inadvertent thermal or catalytic decomposition and leads to a system that is safer and more compact than existing alternatives.
In April, researchers at the Technion-Israel Institute of Technology shared the results of their investigation into the use of expandable graphite to enhance fuel regression rates. This type of intercalated graphite forms long, thin strings that protrude from the fuel surface and facilitate the heat transfer to the solid grain; this process gives rise to a two- to threefold increase in the burn rate of polymeric fuels without compromising any of their mechanical properties. Moreover, adding 5% expandable graphite to paraffin waxes was shown to produce up to 50% regression rate enhancement.
Researchers at Stanford University used experience with laser ignition systems to study the two-dimensional propagation of flame sheets above fuel slabs. Their measurements, published in August, show that flames spread evenly in all directions from the point of ignition despite the presence of oxidizer crossflow in hybrid chambers.
In February, Sierra Nevada Corp. tested a novel hybrid rocket engine under the DARPA Operational Fires program that demonstrated high-energy density and the capability for deep throttling and smooth shutdown on command. Along similar lines, bluShift Aerospace of Maine had a busy year proving its new modular, carbon-neutral engine in the wake of nearly 100 hot-fire tests. A final series of static test firings in August paved the way for the forthcoming launch of its Stardust 1.0 rocket.
In Europe, Nammo of Norway improved its flight-proven 30-kilonewton engine by redesigning the catalyst assembly, which converts hydrogen peroxide into a hot steam and oxygen mixture that fuels combustion. Further, the German startup HyImpulse Technologies developed a 75 kN Paraffin-LOX hybrid motor, called HyPLOX75, and completed the first hot-fire tests in September at the German Aerospace Center in Lampoldshausen. With this milestone, HyImpulse moves one step closer to the 2022 first launch of its small launch vehicle, which will use 12 Turbopump-fed HyPLOX75 engines in the first and second stages.
Across the Pacific, Gilmour Space Technologies of Australia completed a 110-second, mission-duration test firing of the company’s new single-port hybrid motor in mid-July. The Taiwanese TiSPACE completed the flight model hot-fire qualification for its four-engine second-stage propulsion system, while a group at the Advanced Rocket Research Center of the National Chiao Tung University in Taiwan demonstrated stable hovering flight of a hybrid rocket platform in early September.
Contributors: Yen-Sen Chen, Marty Chiaverini, Sascha Deri, Alon Gany, Mario Kobald, Veronika Korneyeva, Tony Whitmore and Jong-Shinn Wu
Related Posts
Stay Up to Date
Submit your email address to receive the latest industry and Aerospace America news.
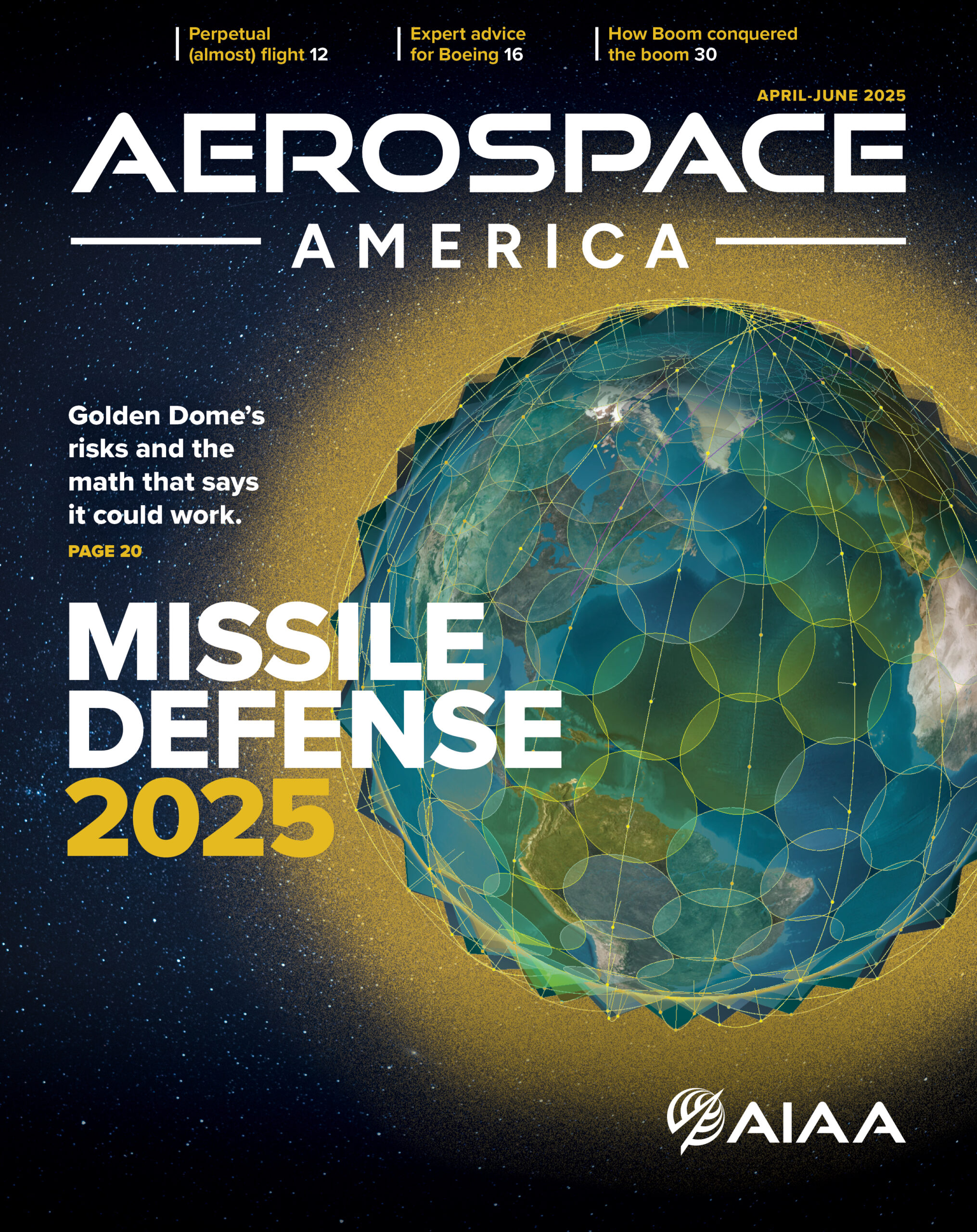