Stay Up to Date
Submit your email address to receive the latest industry and Aerospace America news.
The Computer Systems Technical Committee works on advancing the application of computing to aerospace programs.
In April, NASA’s Voyager 1 resumed returning science data from its instruments. Voyagers 1 and 2 are the only spacecraft to directly sample interstellar space. In November 2023, Voyager 1 data was suddenly stuck in a repeating pattern. After studying decades-old engineering documents, the Voyager team sent a “poke” command to the spacecraft in early March; it revealed that a single memory chip in the Flight Data Subsystem, one of the three onboard computers, had failed after 46 years of spaceflight. The team moved code to other parts of FDS memory and in mid-April, uplinked code for returning the spacecraft’s engineering data. With Voyager 1 at a distance of 22.5 light hours from Earth, it was two days before they learned that the modification had worked. They then began rebuilding the code that returns science data. In May, two of the four science instruments began returning good data, and all four instruments were returning data as of June. When it was launched, the Voyager FDS had a software testbed and assembler. Decades later, with no expectation that Voyager would last so long, they were decommissioned. Now, however, a new simulator and assembler development effort is underway.
NASA’s High-Performance Spaceflight Computing program got its first silicon parts for the PIC64-HPSC family of microprocessors by Microchip, based in Arizona. This first Microchip component is a pin-compatible engineering model for software development activities. Announced in July, the PIC64 chip has eight processor cores built on the SiFive X280, a 64-bit central processing unit that uses the RISC-V open standard architecture. The chips are fabricated with the 12-nanometer 12LP+ process at New York-based GlobalFoundries, a Department of Defense-accredited Trusted Foundry. The PIC64 effectively replaces the RAD750 from BAE Systems, the primary processor for numerous NASA missions, including the Curiosity and Perseverance Mars rovers and the James Webb Space Telescope. PIC64 was designed to achieve a 100-times improvement in performance per watt compared to NASA’s current space-qualified computers. Additionally, X280 vector extensions that enable artificial intelligence and machine learning workloads should allow spacecraft to operate farther from Earth with greater autonomy. Microchip plans to build two versions of the chip: the radiation-hardened PIC64-HPSC1000 for medium and geosynchronous Earth orbits and deep space and planetary missions, and the radiation-tolerant PIC64-HPSC1100 for low-Earth orbit.
In July, Meta Platforms Inc. of California introduced Llama 3.1, a state-of-the-art, open-source large language model that could potentially transform the aerospace industry. Building upon its predecessor, Llama 3.1 has the ability to be fine-tuned with aerospace-specific data, enabling a wide range of applications. Pre-trained on vast amounts of information, such models significantly reduce the computational resources and amount of time required for training, making them cost-effective and environmentally sustainable. The open-source nature of Llama 3.1 allows organizations to customize the model within their own secure computing environments, ensuring that sensitive information remains protected. Open-source models such as BERT and RoBERTa are already used in the aerospace requirements engineering domain, while generative AI models like GPT-3.5-turbo have demonstrated significant potential for enhancing accident and incident analysis by processing extensive textual reports found in accident and incident databases to extract safety lessons. These models could also power advanced pilot assistance technologies, enabling natural language interaction with avionics, real-time analysis of in-flight communications to detect anomalies and improved maintenance support through natural language queries. Such advancements are predicted to significantly enhance safety, efficiency and reliability within the aerospace industry.
Stay Up to Date
Submit your email address to receive the latest industry and Aerospace America news.
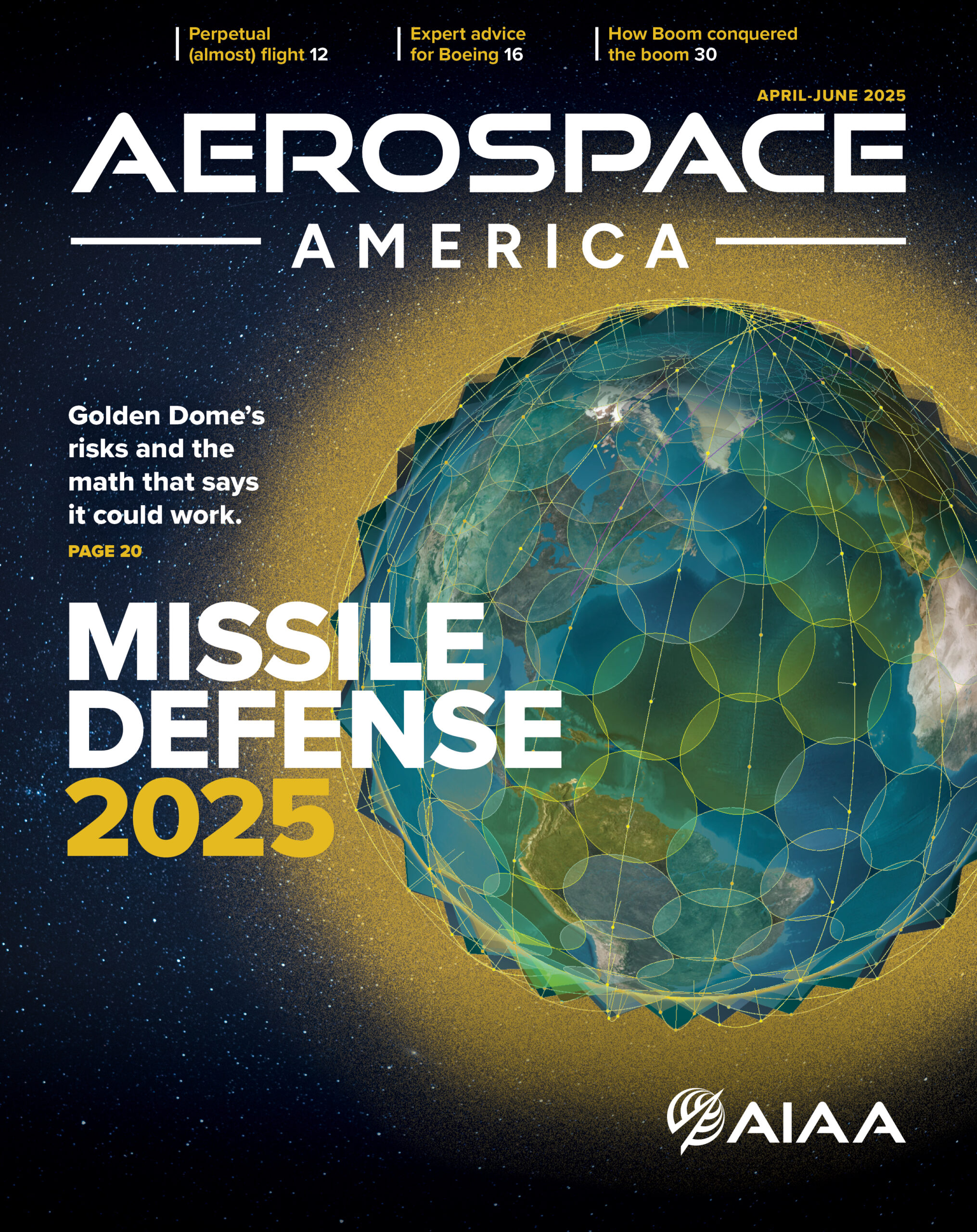