Stay Up to Date
Submit your email address to receive the latest industry and Aerospace America news.
The Liquid Propulsion Technical Committee works to advance reaction propulsion engines employing liquid or gaseous propellants.
In March, NASA began launch preparations for Artemis I, the first in a series of missions to take humans back to the moon and the first integrated flight test of a Space Launch System rocket and Orion spacecraft. The rocket and spacecraft launched in November, after attempts in August and September were scrubbed due to weather and a fuel supply line leak. The SLS Block 1 variant, which will be used for the first three Artemis missions, is capable of sending 27 metric tons to orbits beyond the moon with 39.1 million newtons of thrust at liftoff. Every SLS variant includes a core stage with four RS-25 engines based on a staged combustion cycle with liquid hydrogen and liquid oxygen. Each Orion is powered by 33 engines, a combination of bipropellant and monopropellant thrusters operating with mixed oxides of nitrogen and monomethyl hydrazine. The Orion Main Engine is regeneratively cooled and produces nearly 27,000 newtons of thrust.
SpaceX made progress toward its first Starship orbital test, with static firings of Raptor 2 engines installed on the Starship 24 second stage and Super Heavy Booster 7. Starships are powered by nine Raptor 2 engines, while Super Heavy boosters each have 33 engines. The Raptor engine has a full-flow staged combustion cycle powered by liquid oxygen and liquid methane. The Raptor 2 has a lower mass and higher thrust than its predecessor, with a main combustion chamber pressure of 4,350 pounds per square inch (300 bar) — which SpaceX says is the highest MCC pressure of any rocket engine.
In Europe, the first test firing of the Ariane 6 upper stage liquid propulsion module was completed at the German Aerospace Center’s, or DLR’s, P5.2 facility. Main contributors of the Ariane 6 Launcher are ArianeGroup, the European Space Agency and CNES, the French space agency.
Additionally, ArianeGroup completed the first hot firing test campaign of a 5-kilonewton storable hypergolic nitrogen tetroxide/monomethyl hydrazine engine in July. The test campaign at DLR’s Lampoldshausen facility lasted three months and covered 179 hot firings with a total test duration of 2,380 seconds. The engine is being developed to power the future innovative Astris kick stage for the Ariane 6. Through Astris, the versatility of Ariane 6 would be increased and enable deep space exploration missions with destinations including the moon, Mars and asteroids. ArianeGroup also integrated its Prometheus M1 liquid oxygen/liquid methane engine on its test bench T1G in Vernon, France, in preparation of first test firings. In parallel, ArianeGroup’s development activities of a more powerful engine upgrade with a 20% higher thrust were ongoing.
In November, NASA’s Cislunar Autonomous Positioning System Technology Operations and Navigation Experiment cubesat arrived in its near-rectilinear orbit around the moon after a valve malfunction in September that caused the spacecraft to begin spinning. Mission controllers regained control of CAPSTONE in October. CAPSTONE is the first spacecraft to test this unique, elliptical lunar orbit and is a pathfinder for NASA’s Gateway lunar outpost. The oven-sized cubesat is propelled by its novel electric micropump developed by California-based Flight Works Inc. that takes hydrazine stored at low pressure in the tank and feeds it at high pressure to the small thruster.
In June, Blue Origin installed a BE-4 engine, which will power Blue Origin’s New Glenn and United Launch Alliance’s Vulcan Centaur heavy-lift rockets, into a refurbished test stand at NASA’s Marshall Space Flight Center in Alabama in preparation for commissioning tests. The BE-4 uses liquid oxygen and liquid methane and is designed for restart and deep throttle operation, providing 2.4 million newtons of thrust. Blue Origin delivered the first two BE-4s to ULA in October.
In August, Sierra Nevada Corp. of Colorado completed a critical design review of the VR35K-A, a liquid oxygen/liquid hydrogen upper stage engine developed in conjunction with the Air Force Research Laboratory. The engine would have 155,000 newtons of thrust and is designed to lower costs while achieving higher thrust and specific impulse when compared to existing upper stage engines.
Contributors: Eric Besnard, Rohan Gejji, Anne Lekeux, Dieter Preclik, J. Arthur (Chip) Sauer and Steven Shark
Stay Up to Date
Submit your email address to receive the latest industry and Aerospace America news.
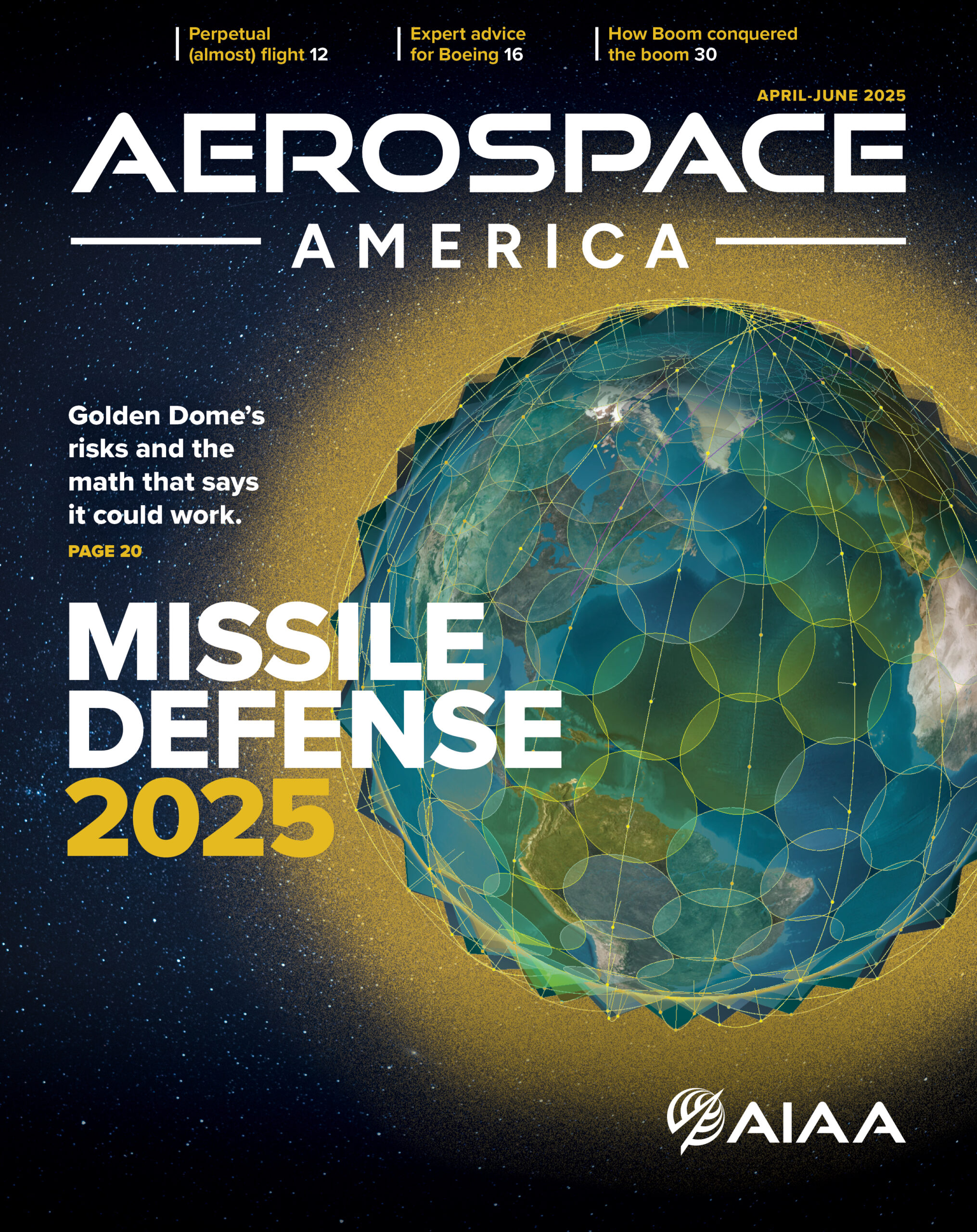