Stay Up to Date
Submit your email address to receive the latest industry and Aerospace America news.
The Non-Deterministic Approaches Technical Committee advances the art, science and cross-cutting technologies required to advance aerospace systems with non-deterministic approaches.
The Probabilistic Design and Optimization Laboratory at GE Research of New York leads research on design, development and application of non-deterministic approaches on industrial problems for GE businesses. In January, the group, in collaboration with the University of Notre Dame and with funding from the Advanced Research Projects Agency-Energy’s DIFFERENTIATE program, developed novel probabilistic methods toward the explicit inverse design of industrial gas turbine blades and additive manufacturing via powder-bed fusion. The methodological innovation includes a two-orders-of-magnitude input-space dimensionality reduction for high-dimensional engineered systems. NASA’s Jet Propulsion Laboratory in California and Sandia National Laboratories in New Mexico continued their multiyear joint seminar series, “Quantification of Uncertainty Across Disciplines,” aimed at communicating state-of-the art practices in model verification, validation and uncertainty quantification, or V&V/UQ, between the two institutions; organizing training sessions and seminars to broaden a community of practice in V&V/UQ across technical disciplines; and initiating research and development that improves the state-of-the-art in V&V/UQ.
In January, the Aerospace Systems Directorate within the U.S. Air Force Research Laboratory secured U.S. Patent No. 10902089 for its development of a “method for predicting stochastic output performance or scaling stochastic inputs.” In August, the directorate awarded a contract for the EQUATE* research programto Northrop Grumman. EQUATE focuses on the role and impact of UQ in multidisciplinary aircraft design through a physics-based approach that enables trades of risk and performance.
Early in the year, the Southwest Research Institute based in Texas wrapped up its part of a Small Business Innovation Research award to reduce variability in carbon-carbon composites manufacturing for hypersonic applications. Funded by the FAA and NASA, the SwRI investigated applicability of its Design Assessment of Reliability With Inspection, or DARWIN, software for probabilistic damage tolerance analysis, to aerospace components of higher criticality made by additive manufacturing. The SwRI is also leading a team to develop simulation tools to predict the fatigue life of composite bonded and bolted joints, under an Air Force Research Laboratory contract.
Sandia researchers continued investment in multifidelity UQ approaches, with a focus on methods that retain efficiency in the presence of the general nonhierarchical modeling relationships that are often encountered in production-scale applications. Multifidelity activities have included neural network training in collaboration with the University of Notre Dame, functional tensor train surrogates with the University of Michigan, dimension reduction with the University of Southern California, stochastic simulations, hyper-parameter model tuning and nonhierarchical model management. In May, new algorithmic advancements were released in Sandia’s Dakota software, including improved dimension reduction by basis adaptation and support for embedded cross validation within greedy refinement for multifidelity surrogates.
Also in May, the optimization group at the Mathematics and Computer Science Division at Argonne National Laboratory completed a project funded by the U.S. Department of Energy’s Advanced Scientific Computing Research office to develop a suite of derivative-free stochastic optimization methods for decision-making in the presence of uncertainty, with limited and expensive information. This novel approach, inspired by the game of chess, uses a Bayesian framework to “look ahead” several steps to make optimal decisions that hedge against risks with future decisions, thereby resulting in using limited information. Software that implements the suite of methods is slated to be published as “open source” for broader use by the scientific community.
In August, the University of Alabama developed a new regularization technique to solve an underdetermined and ill-conditioned system of equations, especially obtained in the application of polynomial chaos. Researchers carried out uncertainty quantification of delamination of composites using the new regularization technique with polynomial chaos.
Contributors: Barron Bichon, Michael Eldred, Edwin Forster, Gianluca Geraci, Sayan Ghosh, Sameer Mulani and Vicente Romero * Enabling Quantification of Uncertainty in Aerospace Technology Evaluation
Stay Up to Date
Submit your email address to receive the latest industry and Aerospace America news.
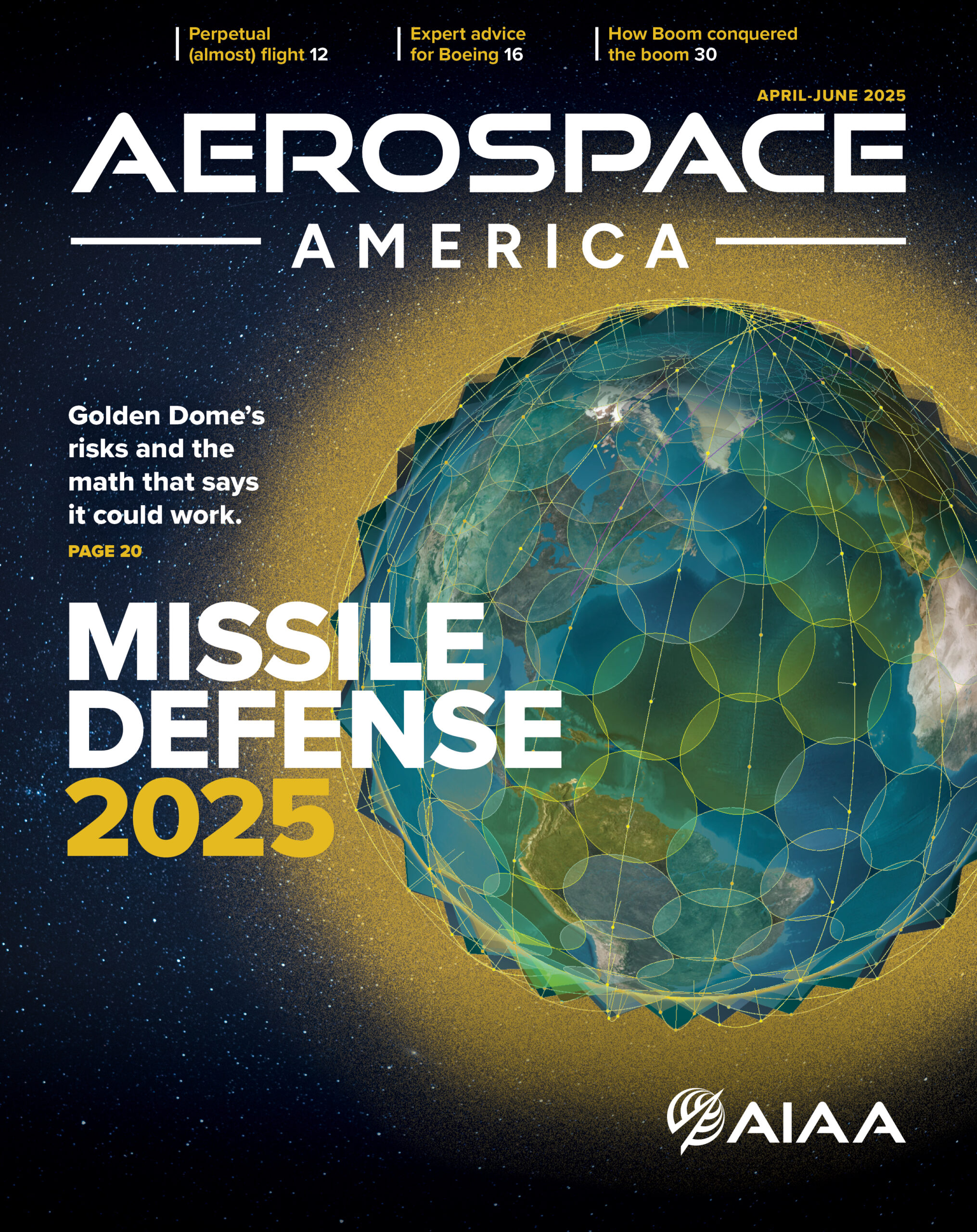