Stay Up to Date
Submit your email address to receive the latest industry and Aerospace America news.
Those who want to expand society into space have long dreamed of a space-made product that will prove to be uniquely lucrative. A stunning return on investment, the thinking goes, would induce others to flock to orbit with their own dreams, just as Americans headed west in the 19th century. This year, a fiber optic material called ZBLAN is receiving its moment in the limelight for its potential to ignite the space economy. Debra Werner tells the story.
At Made In Space in Silicon Valley, CEO Andrew Rush handed NASA Administrator Jim Bridenstine a palm-sized spool of clear fiber made of ZBLAN, short for zirconium barium lanthanum aluminum sodium fluoride.
ZBLAN is among a group of glasses discovered by accident in 1974 by French scientists Marcel and Michel Poulain at the University of Rennes. In the years since, manufacturing challenges have relegated ZBLAN to specialty optical applications such as laser-generating mediums and optical fibers for medical endoscopy and scientific spectroscopy.
Enter Made In Space and its two rivals in the ZBLAN field, FOMS, short for Fiber Optics Manufacturing in Space, of San Diego and Physical Optics Corp. of Torrance, California. The three are racing to be first to commercialize ZBLAN fibers by making them in orbit, as each company has so far done only in small batches aboard the International Space Station.
True believers think that space-made ZBLAN fibers could gradually replace silica fibers as the product of choice for modernizing or expanding the millions of kilometers of fiber optic cables back on Earth. This would require mastering production of long fibers in space facilities sized for commercial production.
Such an outcome would mark an unusual twist in the long search for a product that will spark creation of an economy in space. Such visions often center on additive manufacturing or 3D printing. Rockets, space habitats and other equipment could, in theory, be made this way instead of launching them assembled from Earth. Material ranging from human tissue to composites would be laid down a layer at a time with techniques tailored to take advantage of microgravity.
The ZBLAN in Bridenstine’s hand last August was not made that way. A machine crafted by Made In Space produced this particular batch on the ground as a prelude to the firm’s campaign to produce fiber aboard the ISS through a process known as pulling. The end of a glass rod is melted, and as it melts, a drop breaks away, pulling behind it a fiber about the width of a human hair that is wound around a spool as it solidifies.
Beating silica
Fiber optic engineers have long been intrigued by ZBLAN because, in theory, fibers made of the material should be clearer over a wider range of frequencies than today’s silica fibers. The improved frequency range comes from the fact ZBLAN incorporates lightweight elements and heavy elements rather than just silica. Being clearer, the laser-encoded bits and bytes of our television programming, web pages and phone calls would travel much farther with less signal loss. Laser repeaters might only be needed after thousands of kilometers instead of hundreds of kilometers with silica, says Dmitry Starodubov, chief scientist at FOMS.
All told, ZBLAN fiber could transmit signals up to 100 times more efficiently than silica optical fibers, says Michael Roberts, the interim chief scientist for the ISS U.S. National Laboratory, a nonprofit organization formerly known as CASIS, short for the Center for the Advancement of Science in Space. His organization helped the three competitors send their manufacturing equipment to the space station.
Theoretical superiority is one thing. ZBLAN, it turns out, can’t be produced in high volumes on Earth, because gravity makes it hard to combine ZBLAN’s elements into a uniform material. The heavier elements settle, the lighter elements rise to the top and crystals form as the material solidifies. Humidity also causes defects and crystals that reduce clarity and make the fibers brittle.
So far, none of the competitors have managed to consistently produce long strands of high-quality ZBLAN. “If the companies can produce ZBLAN in space repeatedly, there is a ready and growing market for the higher-quality fibers,” says Lynn Harper, integrative studies lead for NASA’s Emerging Commercial Space Office. Harper, who is based at NASA’s Ames Research Center in Silicon Valley, co-authored a series of NASA studies about promising microgravity research.
The companies plan to achieve the desired consistency by tweaking their machine designs and trying again in an iterative approach. Rush of Made In Space compares the strategy to developing a new version of the iPhone, but with some key distinctions: “We don’t have the capital Apple has, our hardware is orbiting Earth and you can only go up there a couple of times a year.”
So far, Made In Space has sent a microwave-oven-size ZBLAN device to ISS four times. The company plans to send an upgraded version to the station this year. Made In Space isn’t saying how much ZBLAN it produced in orbit. The company is still trying to prove the on-orbit manufacturing technology works before gradually scaling it up to produce longer ZBLAN fibers. “I would love to have a 1,000-kilometer-class ZBLAN manufacturing plant in orbit in two years, but there’s a lot of steps between here and there,” says Rush.
Starodubov of FOMS announced at an optical fibers conference in November that the company produced its first strands of high-quality ZBLAN aboard ISS in its suitcase-size machine. Astronauts inside the station installed the machine in the U.S. Destiny Lab by hooking up cables and screwing in bolts. FOMS controlled the equipment remotely from NASA’s Marshall Space Flight Center in Alabama. The company says it produced tens of meters of ZBLAN close to the desired uniformity. “If we can make it just a little bit better, the current market price of the specialty fiber would be $200 per meter or about $6 million for 30 kilometers or 1 kilogram,” Starodubov says. “Then we can grow our orbital manufacturing for years to come.”
Commercial space stations
At some point, the ZBLAN pioneers will need an alternative to the space station’s diminutive Destiny module, which at 8.4 meters long and 4.2 meters wide is about the volume of a small apartment. Also, it’s not clear how long ISS will be available for research. The Trump administration called in 2018 for ending funding for its portion of the station after 2024 but has backed off that stance. Legislation pending in Congress would extend station funding until 2030.
Bridenstine’s NASA is trying to lay out a clear path between ISS and commercial space stations through a program called NextSTEP, short for Next Space Technologies for Exploration Partnerships. Among other things, NextSTEP invites companies to match at least 20% of the money they win from NASA to design and develop free-flying commercial space stations and a commercial space station that would be attached to the ISS Harmony module. NASA plans to spend about $561 million on these programs over the next four years. NASA intends to pick one company to link its space station with ISS by 2024. It’s not clear how many companies NASA will select to build the free-flying space stations.
Among the contenders, Bigelow Aerospace in September showed off a prototype station built in part with NextSTEP dollars. The Bigelow B330, named for its 330-cubic-meter volume, would be a larger version of the Bigelow Expandable Activity Module that docked with ISS in 2016 and which astronauts continue to float in and out of. The station’s walls would be made of a proprietary flexible material that expands to shape when pressurized. Bigelow wants to dock the B330 with ISS and later fly it on its own.
Nanoracks of Texas in 2017 signed a NASA NextSTEP contract to study the concept of turning a spent upper stage into a space station called the Nanoracks Outpost. The initial NextSTEP contracts are small, but they put companies in the running for follow-on contracts to develop and eventually build commercial space stations geared for different audiences. One space station might be set up for astronauts or tourists while another is optimized for manufacturing equipment to pull ZBLAN fiber or 3D-print satellite antennas. The manufacturing facility in orbit could be crew-tended, meaning equipment would be controlled remotely and people would visit to perform repairs or maintenance.
For any of these space stations to succeed in creating a new orbital infrastructure, the U.S. government must provide significant funding like it did for the U.S. Interstate Highway System in the 1950s and ’60s, says Adrian Mangiuca, commerce director at Nanoracks. “A bunch of transcontinental truckers didn’t get together and say, ‘Let’s self-fund the American highway system because we want to get fruit from California to New York in three days,’” says Mangiuca. Instead, the U.S. government paid for the infrastructure. Creating an infrastructure in space will be similar, but this time Nanoracks and others will own the infrastructure in exchange for helping to fund and extend it. The U.S. government and industry will have to work together, through what Mangiuca calls “a whole-of-nation” approach to creating a low Earth orbit economy.
Vying with additive manufacturing
As hopeful as ZBLAN’s fans are, they like to emphasize that building a space economy does not rest entirely on any single product. “When you remove gravity from the equation, you unlock a different universe of physics,” says Ioana Cozmuta, CEO and co-founder of G-Space, a Silicon Valley startup developing software to quantify gravity’s effect on materials. “I compare it to the time when the semiconductor industry was transformed because people recognized the benefit of ultra-low temperatures. It unlocked a new universe of physics.”
Companies plan to produce several classes of optical fibers in orbit, and NASA managers remain bullish about the potential for additive manufacturing to act as a springboard for the nascent space economy for one simple reason. They’ve seen the impact of 3D printing in factories on the ground. “It’s one of the most disruptive technologies I’ve seen in my 30-plus years of aerospace,” says John Vickers, NASA principal technologist for advanced materials and manufacturing.
As an example, he notes that Rocket Lab, the Huntington Beach, California, startup, says it can print the combustion chamber, injectors, pumps and main propellant valves for one of its Rutherford engines in 24 hours. Vickers estimates that 10 years ago, a Rutherford engine would have taken months or even years to manufacture.
Made In Space sent the first 3D printer to the space station in 2014. The microwave-oven-size printer churns out spare parts and tools for astronauts. Made In Space also makes money operating a second printer on ISS, the Additive Manufacturing Facility. NASA and other customers pay Made In Space to print objects in the latest microwave-size machine. Beyond spare parts and tools, NASA sees additive manufacturing as a path to constructing space telescopes and communications antennas too large to fit in rocket fairings.
Archinaut One is a good example. Made In Space is preparing to launch the refrigerator-size satellite in 2022 with an on-board 3D printer and robotic arm. Once in low Earth orbit, Archinaut One will attempt to additively manufacture a solar array stretching 20 meters from tip to tip and plug the array into a Northrop Grumman instrument. Northrop Grumman and Made In Space won’t elaborate on the job of the Northrop Grumman instrument except to say it will be tested in space for the first time.
In-space manufacturing and assembly means you can design satellites for their intended role in orbit rather than building them specifically to “fold up origami-style inside a launch fairing and survive intense forces and vibrations,” says Justin Kugler, Made In Space vice president for advanced programs and concepts.
In addition to creating structures in orbit, NASA expects future planetary habitats to be additively manufactured. To demonstrate the potential, NASA awarded $701,000 last May to two teams that relied on additively constructed shelters out of materials like the soil and rocks found on the moon and Mars. It was the second round of the 3D-Printed Habitat Challenge, where competitors robotically built one-third-scale semi-permanent shelters.
Additive manufacturing technology is progressing so quickly, it should have its own Moore’s Law, Vickers says. A few years ago, 3D printers were known for manufacturing small plastic parts. Those early printers have given way to larger machines employing new techniques for printing metals and composites.
Whether the catalyst turns out to be additive manufacturing or ZBLAN, or a mix of both, true believers are sure the space economy is coming. Rush of Made In Space predicts it will “blossom from a factory to an industrial park to cities in space.”

About Debra Werner
A longtime contributor to Aerospace America, Debra is also a correspondent for Space News on the West Coast of the United States.
Related Posts
Stay Up to Date
Submit your email address to receive the latest industry and Aerospace America news.
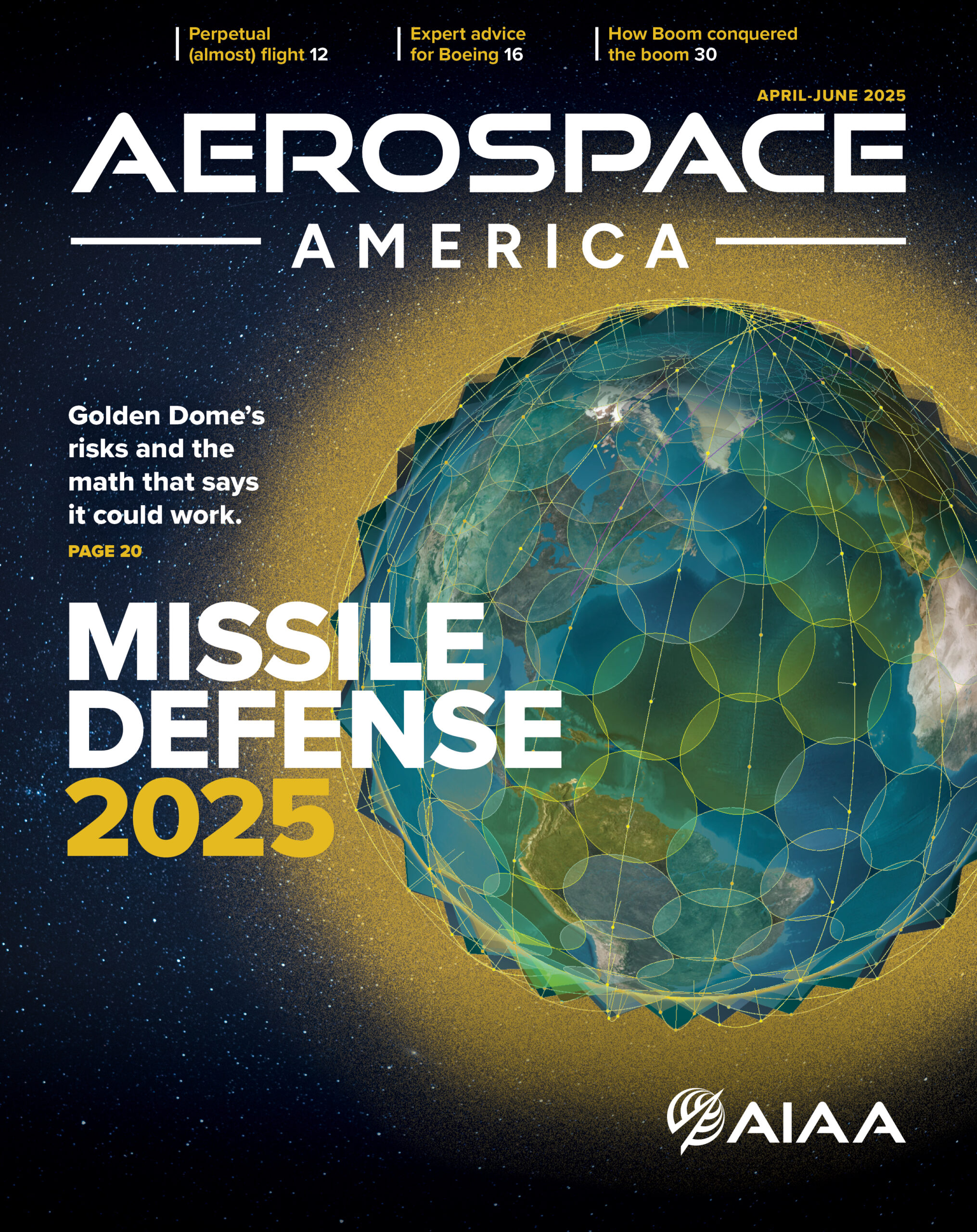
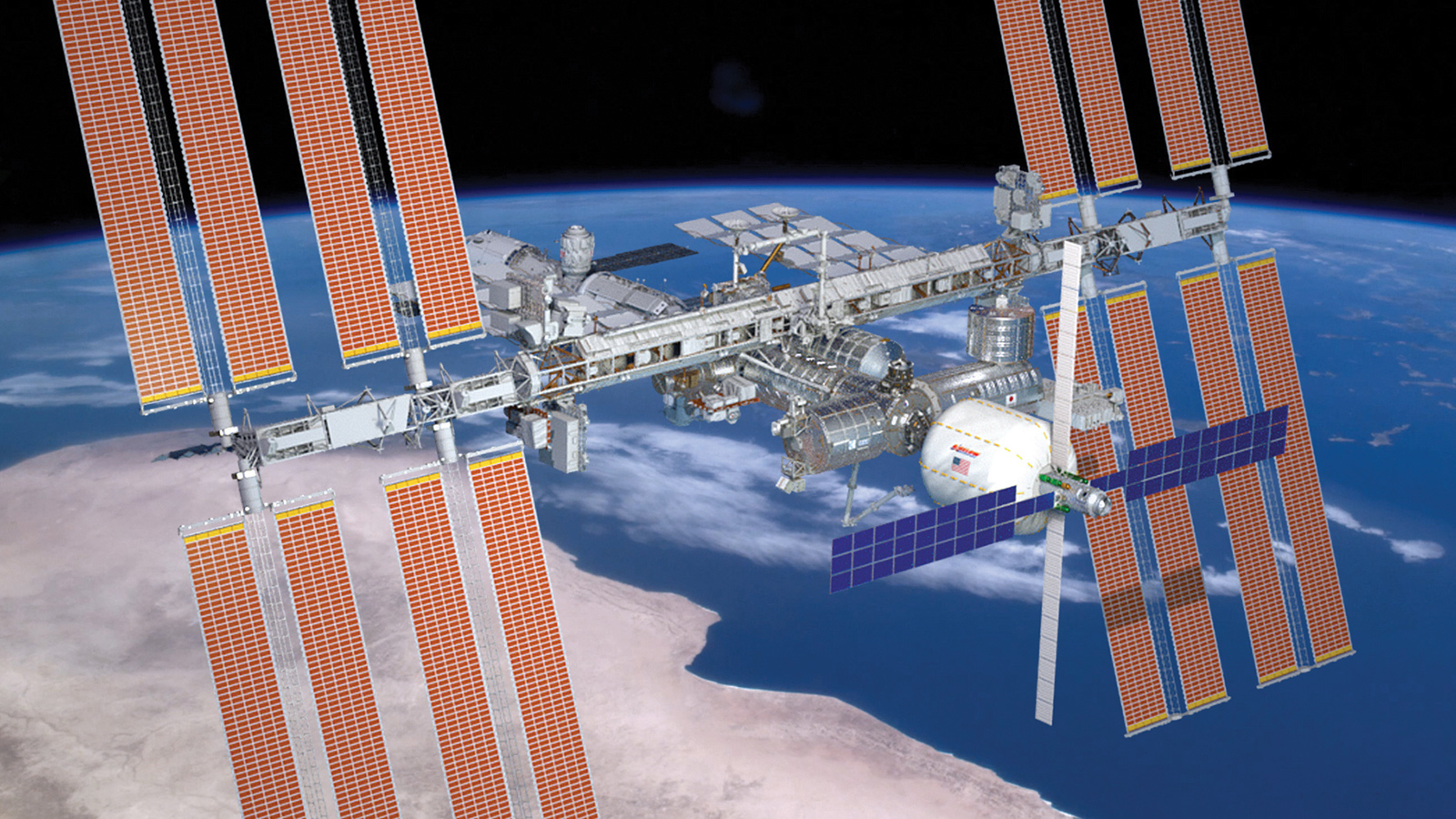

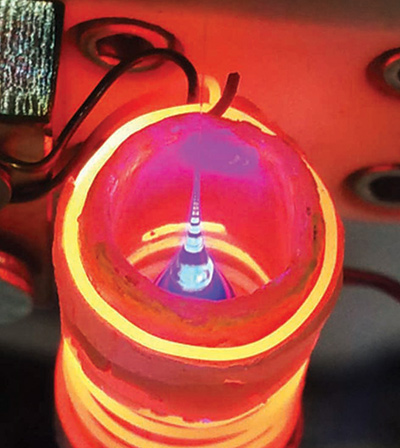
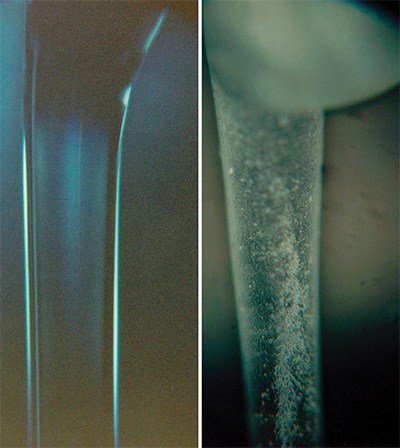
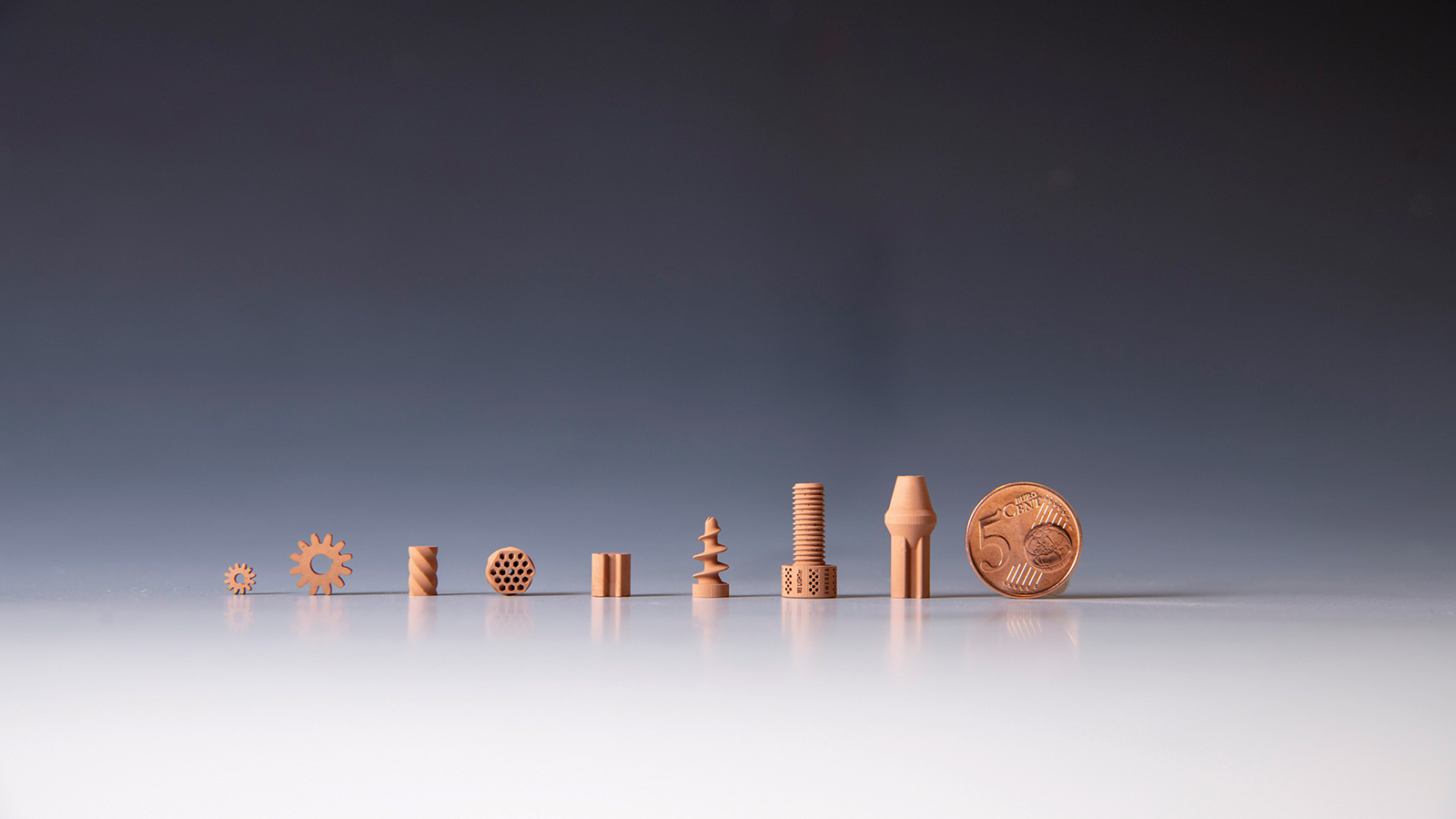