Stay Up to Date
Submit your email address to receive the latest industry and Aerospace America news.
Every spring over the United States, aircraft contracted by the U.S. Geological Survey and partner agencies bounce laser light off terrain, buildings and bridges. Computers on the planes record the signal transit times, and back on the ground software turns this lidar data into stunning 3D images.
This is the U.S. Geological Survey’s 3D Elevation Program, or 3DEP, in action. Plans call for mapping the entire United States this way by 2023 to produce color-coded elevation maps that organizations at all levels would consult to identify areas at high risk of flooding and inspect buildings, bridges and other infrastructure, among other applications.
Lidar is the technique of choice for these tasks because, unlike aerial photography, “we don’t have to worry about the shadows, we don’t have to worry about a light source,” says Jeff Lovin, senior vice president and market director at Woolpert Inc. of Ohio, one of the companies that has been conducting lidar flights since 2015 for USGS and its partners in the federal government and at the state and local levels. The company is under contract to map parts of Wyoming, where officials plan to combine terrain maps with pictures to aid in invasive species detection. The company mapped the entirety of Tennessee between 2015 and 2017 to help state officials avoid a repeat of 2010 and 2011, when it was caught off guard by flooding.
Mapping begins with installing a lidar sensor and computers for data processing onboard an aircraft, a monthslong process that costs almost as much as the plane itself, Lovin says.
“You buy a $300,000 airplane,” like a 12-passenger Cessna or Beechcraft, “it’s not unimaginable to spend at least $200,000 on getting the plane ready to hold a sensor,” he says.
Before technicians can cut a 50-centimeter hole in the aircraft belly to make room for the sensor, FAA must sign off on the plans because “the whole structure of the airframe itself has to be changed to accommodate for that” hole, Lovin says. “You have to go in and brace [the airframe] and make sure the plane is as rigid and safe and operates just as it did originally.”
After FAA gives the OK, technicians strip the plane’s interior and cut the hole. Most of the barrel-shaped sensor sits inside the aircraft, with only its large lens peering out from underneath the plane like a circular window. Once equipped, the plane receives a final FAA inspection.
Scanning occurs during the early spring when the ground below is clear of snow and leaves. Pilots fly aircraft back and forth in straight lines at about 8,200 feet while the sensor shoots laser pulses through the circular lens, measuring the time it takes reflections to arrive at its receiver. A sensor operator sits in the back of the plane, monitoring incoming data on computer screens.
A four- to five-hour flight generates billions of lidar data points. These value tables, stored on a hard drive, are then mailed to Woolpert’s Ohio headquarters, where software combines them with GPS coordinates and other data to create the color-coded 3D maps.
Once the national database is completed, USGS plans to update the terrain maps as needed.

About cat hofacker
Cat helps guide our coverage and keeps production of the print magazine on schedule. She became associate editor in 2021 after two years as our staff reporter. Cat joined us in 2019 after covering the 2018 congressional midterm elections as an intern for USA Today.
Related Posts
Stay Up to Date
Submit your email address to receive the latest industry and Aerospace America news.
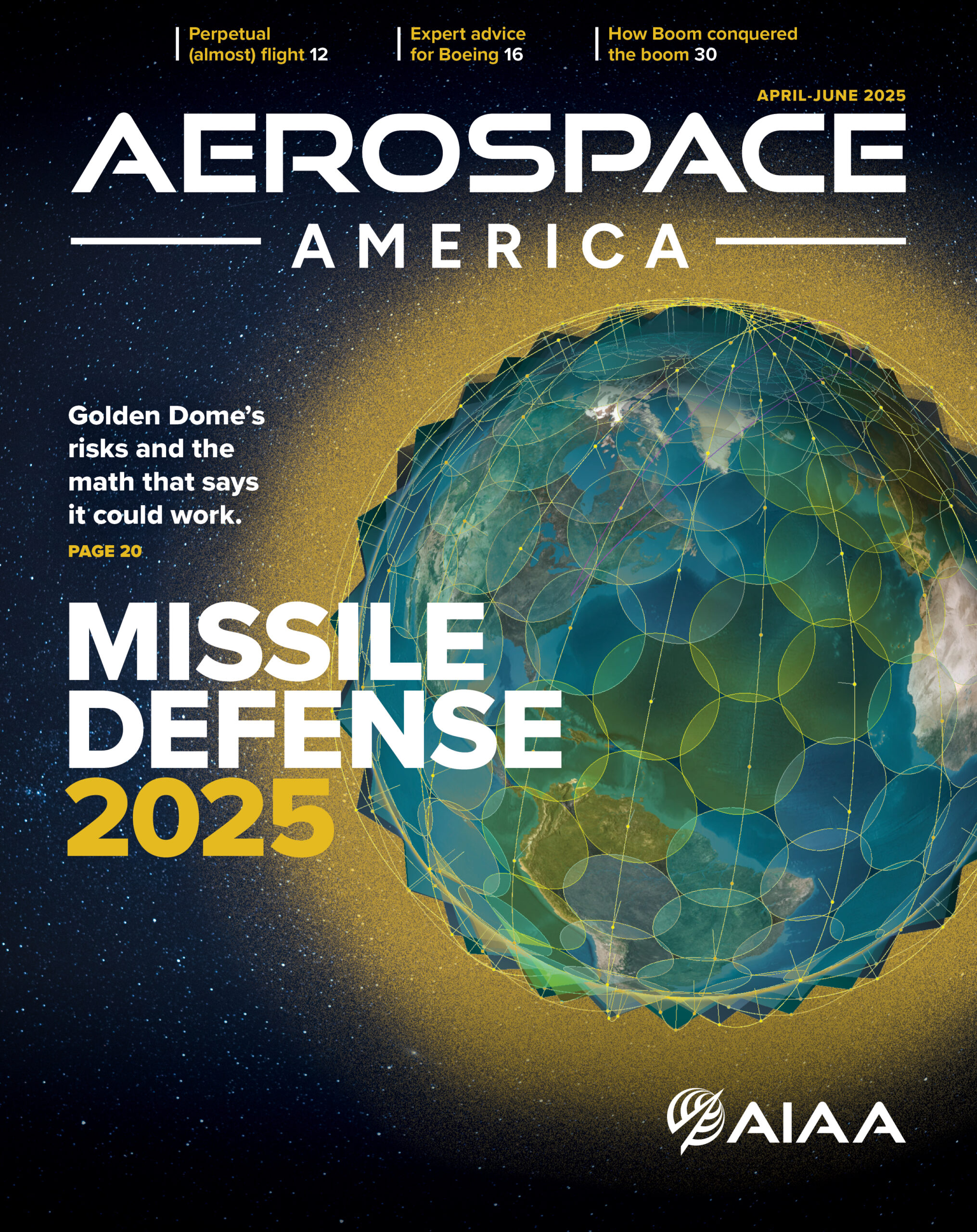
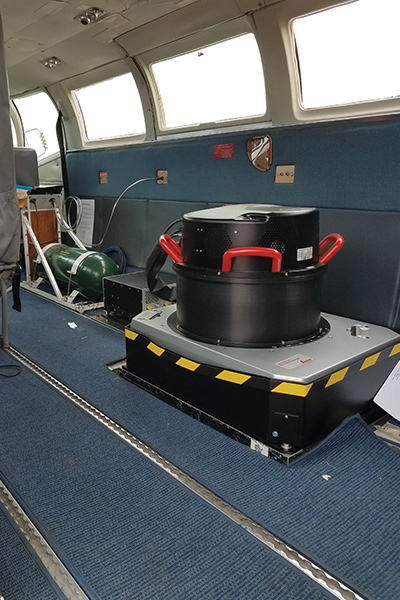