Stay Up to Date
Submit your email address to receive the latest industry and Aerospace America news.
The work of the Adaptive Structures Technical Committee enables aircraft and spacecraft to adapt to changing environmental conditions and mission objectives.
Around the world, researchers are studying both active materials and the structures that use them. Regarding materials developments, a team from the Harbin Institute of Technology first showed in January that a new shape memory polymer composite could be additively manufactured in such a manner that resulting components exhibit remotely actuated self-expandable behavior under an alternating magnetic field.
Also, researchers at Arizona State University, funded by the U.S. Army, this year advanced the development of novel “mechanophore” materials that change color under mechanical loading to detect damage in aerospace composites. Early this year, this team conducted demonstrations of damage detection in composite specimens undergoing fatigue loading using the mechanophore materials, and damage was indicated, as expected.
The U.S. Navy this year supported researchers at the University of Central Florida in developing an approach for detuning resonance in structures using electro-mechanically coupled materials. This approach was experimentally validated on a bladed disk in late 2018. This research will reduce maintenance, repair and overhaul costs associated with blade high-cycle fatigue and failure by effectively reducing harmful vibrations across multiple vibration modes.
U.S. Air Force researchers have developed a suite of materials called liquid crystal elastomers that can be configured to generate out-of-plane surface topography upon actuation from a flat state. Complex material patterns resulting in advantageous surface topological features have been simulated with high fidelity models and were experimentally characterized under realistic pressure loads during wind tunnel tests completed in March. Such features can act as vortex generators and distributed roughness elements, enabling decreased drag and increased stability and control authority across a range of flight conditions.
Enhancing wind tunnel testing of more conventional concepts using active materials, and specifically solid state, rugged, and highly compact shape memory alloy, or SMA, components, was also a focus in 2018. Traditional wind tunnel testing involves changing out numerous fixed parts, but remotely controlled wind tunnel models replace these nearly rigid parts with moving, controllable alternatives, enabling increased productivity and improved data quality, and reducing the cost of wind tunnel testing. This year, a team comprised of Boeing, the European Transonic Windtunnel, NASA’s Langley Research Center in Virginia, and Deharde Maschinenbau of Germany developed and tested numerous such SMA-based remote controlled components in cryogenic high-speed wind tunnels to validate this technology. Testing will continue into 2019.
NASA also worked with Texas A&M University researchers this year to solve problems regarding both subsonic and supersonic aircraft noise. In phases of low-speed flight, the deployment of control surfaces can lead to substantial noise. The NASA/Texas A&M team developed an adaptive structures/SMA solution to altering air flow around these surfaces. Collaborating also with the University of Bristol, this team showed in March and April for the first time that both composite and SMA solutions could be feasible.
Regarding supersonic flight, although aircraft such as the NASA/Lockheed Martin X-59 QueSST — for quiet supersonic technology — can be designed to quiet the sonic boom perceived at the ground under certain atmospheric conditions, Texas A&M and Utah State researchers, supported by NASA, showed for the first time in June that the strength of this boom will vary by more than 10 decibels across the country on a given day due to local changes in the atmospheric profile. Specific morphing concepts will be developed in 2019 to soften booms regardless of changing conditions. The feasibility of such large-scale morphing was proved during separate experiments by NASA and Boeing in June, which showed that large SMA torque-tube actuators capable of 564 newton meters could move a full-sized wing section of an F/A-18 Hornet under flight loads. This milestone for largest aircraft-tested SMA actuator was then scheduled to be surpassed in late 2018 by an actuator rated at 2,260 newton meters.
In the Texas A&M University image at the top, velocity contours and streamlines around a retracting leading-edge slat treated with the NASA/Texas A&M shape memory alloy “slat cove filler” as computed from full fluid-structure interaction analysis. When deployed, the novel device fills the volume behind the slat, reducing local turbulence and radiated noise; the slat cove filler then deforms as needed to allow full retraction of the slat.
Related Posts
Stay Up to Date
Submit your email address to receive the latest industry and Aerospace America news.
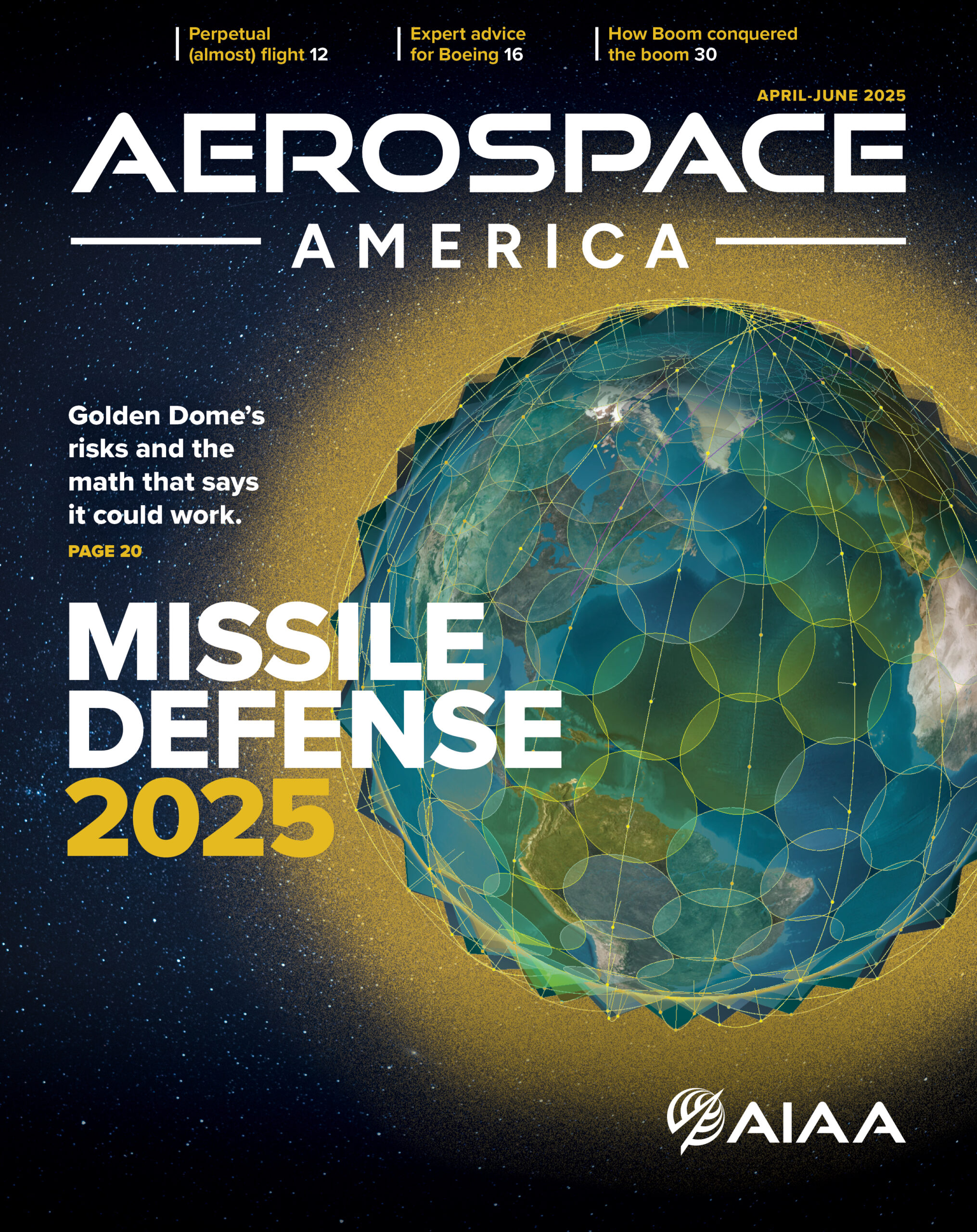