Stay Up to Date
Submit your email address to receive the latest industry and Aerospace America news.
The Non-Deterministic Approaches Technical Committee advances the art, science and cross-cutting technologies required to advance aerospace systems with non-deterministic approaches.
In July, an AIAA Certification by Analysis Community made up of industry, academia and government/regulatory representatives completed the draft document “Recommended Practices When Flight Modeling Is Used to Reduce Flight Testing Supporting Aircraft Certification” to guide commercial applicants when flight modeling is being developed, proposed and used to reduce flight testing relative to traditional aircraft certification practices. The document strongly recommends model verification and validation and uncertainty quantification analysis components.
In May, Sandia National Laboratories released its Dakota software with multilevel uncertainty quantification and optimization capabilities. Multifidelity methods for uncertainty quantification and optimization are essential for reducing the costs of computation without sacrificing accuracy compared to exhaustive, high-cost, high-fidelity simulations. Researchers at Sandia investigated the use of these techniques in mission applications that feature complex model ensembles, such as wind and fusion energy, geological waste disposal and cybersecurity. These experiences led to the development of generalized multifidelity algorithms that support more complex model dependency graphs. This work, in collaboration with the University of Michigan, has spanned sampling and surrogate approaches.
For noise prediction, DLR, the German Aerospace Center, and Empa, the Swiss Federal Laboratories for Materials Science and Technology, continued research by applying a perturbation approach to carry out spatial and temporal uncertainty quantification of noise. The study revealed the relationship of uncertainty changes with individual flight paths depending on input data, noise source ranking, specific operating conditions and propagation distance. Also, a team of DLR, Empa, Technical University Braunschweig and the University of Alabama compared the perturbation approach and higher-order methods for uncertainty quantification in system noise prediction and quantified the effect of dependence or correlation of different variables.
The University of Alabama has developed a novel in-situ self-healing carbon-reinforced thermoset composite system wherein embedded thermoplastic particles and shape-memory polymers act as healing agents. The healing is activated through high-frequency vibrations using macrofiber composite actuators. This year, researchers achieved repeatable healing for at least five cycles under Mode-I fatigue loading and presented initial results at the AIAA SciTech Forum in January and complete results at the American Society for Composites 35th Technical Conference in September. The healing efficiency, critical loads and crack length are uncertain due to inherent material uncertainties and non-uniform heating during crack healing, and these uncertainties are quantified using different techniques, including machine learning.
Researchers in the Computational Optimal Design of Engineering Systems Laboratory at the University of Arizona developed a toolbox for aero-structural stochastic design optimization of composite wind turbine blades with fully parametric capability and shared efficiency and accuracy at the ASC conference in September. The toolbox enables uncertainty quantification to consider the randomness in material, geometric and loading conditions.
Southwest Research Institute continued developing software to predict the fatigue life of composite bonded and bolted joints. A model verification and validation framework is used to identify and reduce uncertainties in models and experiments to achieve the required accuracy of predictions of new bonded joint designs. Elder Research Inc. based in Virginia, MESI Technologies of Texas and SwRI have jointly developed a probabilistic damage tolerance methodology to assess the effectiveness of protective coatings for critical rotating aircraft gas turbine components that are susceptible to hot corrosion fatigue. To enhance condition-based maintenance efforts of in-service military aircraft, SwRI developed a novel likelihood-based corrosion rate modeling approach in partnership with the Air Force Life Cycle Management Center. Convergent Manufacturing Technologies US and SwRI, with funding from the Air Force Research Laboratory, developed fast-running response surface models of composite curved beam process models to investigate the relationship between vacuum bagging and part quality. These models predict local flange thickness and porosity development as a function of processing.
Contributors: Samit Roy and Lothar Bertsch
Related Posts
Stay Up to Date
Submit your email address to receive the latest industry and Aerospace America news.
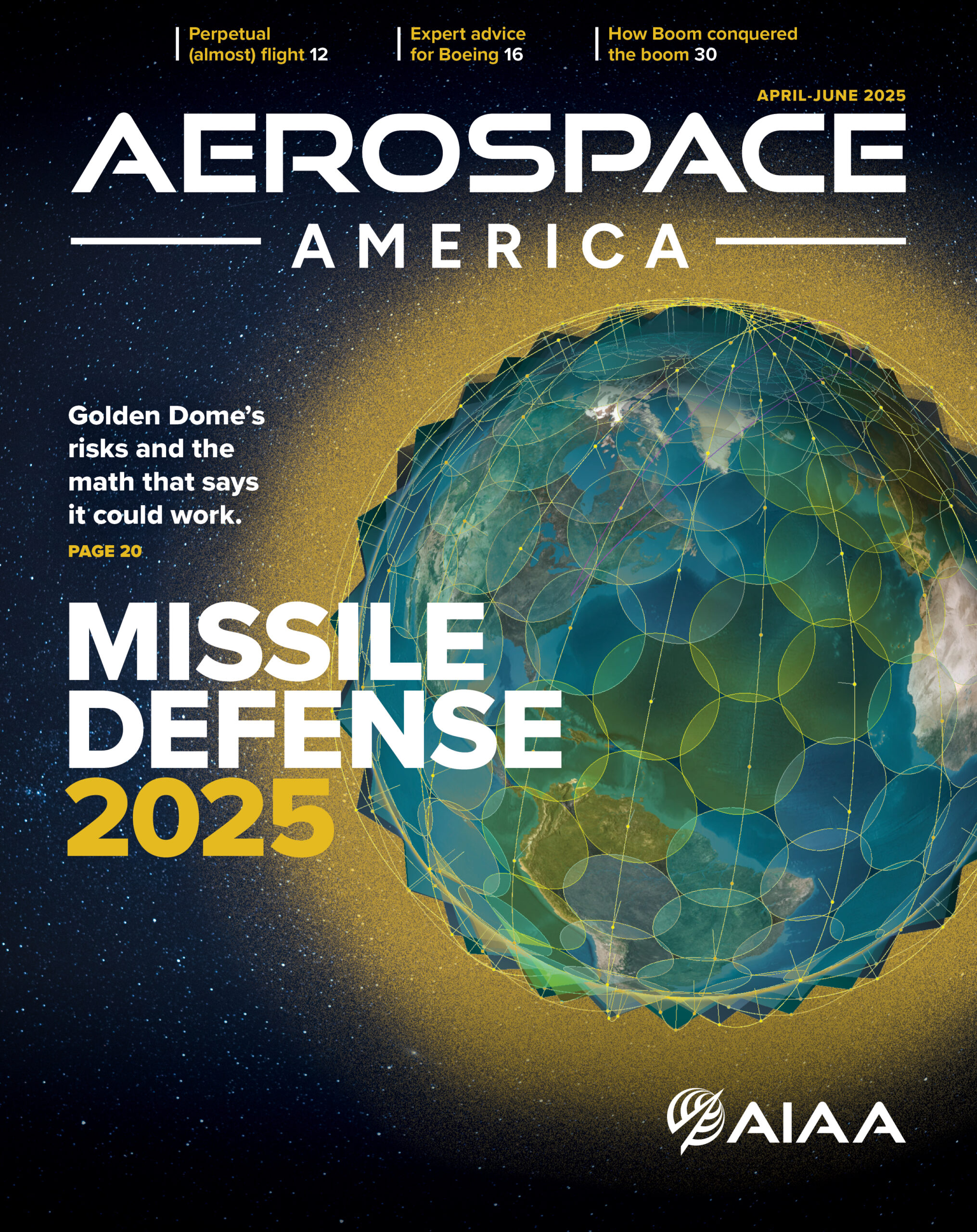