Stay Up to Date
Submit your email address to receive the latest industry and Aerospace America news.
The work of the Adaptive Structures Technical Committee enables aircraft and spacecraft to adapt to changing environmental conditions and mission objectives.
The U.S. Air Force Research Laboratory’s Spacecraft Structural Health Monitoring program concluded experiments in geosynchronous Earth orbit in 2020. It was the third flight in a series started in 2017 on the Space Test Program-Houston 5, or STP-H5, a NASA-U.S. Defense Department testbed for experiments on the International Space Station. Previous experiments focused on monitoring launch events, characterizing spacecraft changes in orbit, evaluating damage-detection techniques and cataloging thermal profile influence. This year’s experiment focused on radiation effects, which are most noticeable in low-Earth orbit and corrupt measurement data on stored volatile memory. Long-term data storage in non-volatile memory also was corrupted in LEO but showed no degradation in GEO.
In January, the Harbin Institute of Technology in China validated a flexible solar array in another on-orbit demonstration. A key system element is a pair of shape-memory-polymer composite tubes for clamping and releasing the solar array. Instead of traditional electro-explosive devices or deployment motors, the SMPC tubes unlocked with minimal shock load. The SMPC solar array then automatically unfolded over the next minute to its designed shape and maintained stiffness once deployed. The team indicated this result will lead to SMPCs being built into larger deployable space structures and new release and locking mechanisms.
Researchers at Texas A&M University and engineers at Arizona-based Paragon Space Development Corp. developed and tested a shape-memory-alloy-actuated prototype radiator that used a single-loop, two-phase fluid flow in February. It was the first passively adapting SMA radiator ever built. The test results make researchers think that an SMA torque tube-driven radiator can outperform current two-loop radiators and provide new insight into the potential operation of SMA thermal control devices configured as heat pipes.
The adaptive structures community also performed groundbreaking tests for aeronautical applications. In August, researchers at the Delft University of Technology in the Netherlands hastened the next leap in smart aeronautical structures with wind tunnel tests of the SmartX-Alpha active morphing wing demonstrator. The sensor- and actuator-rich demonstrator featured a distributed chordwise and spanwise seamless morphing trailing edge, piezoelectric flow sensors and fiber optics. The SmartX project, conceived in 2016, focuses on integrating existing and newly developed sensing and actuation smart technologies into a wing. In the wind tunnel tests, the researchers optimized the static and dynamic wing shape for real-time optimal high-lift and cruise flight performance, as well as simultaneous active maneuver and gust load alleviation using data fusion control algorithms.
A team at the University of Central Florida tackled morphing on a smaller scale, conducting tests in a towing tank in March and September. Funded by the U.S. Navy’s Office of Naval Research, the tests showed dynamic spanwise airfoil twisting during unsteady acceleration can augment aerodynamic lift.
Also in March, the first set of acoustic beamforming tests of a slat gap filler configuration were completed in the Texas A&M 3-foot-by-4-foot wind tunnel under the sponsorship of NASA’s Langley Research Center in Virginia. These test results will help engineers design and demonstrate SMA-based self-deploying slat gap fillers for reducing aerostructural noise in transport-class aircraft.
Researchers at Arizona State University focused on airframe structures, developing a new framework to accelerate the design of complex nano-enhanced composites. Funded by the Office of Naval Research, the researchers’ atomistically informed damage evolution law links nanoscale phenomena to structural-scale damage and response, and a high-fidelity homogenization technique captures material behavior across multiple length scales. The team validated the framework in March using test data for carbon-nanotube-based polymer composites.
Related Posts
Stay Up to Date
Submit your email address to receive the latest industry and Aerospace America news.
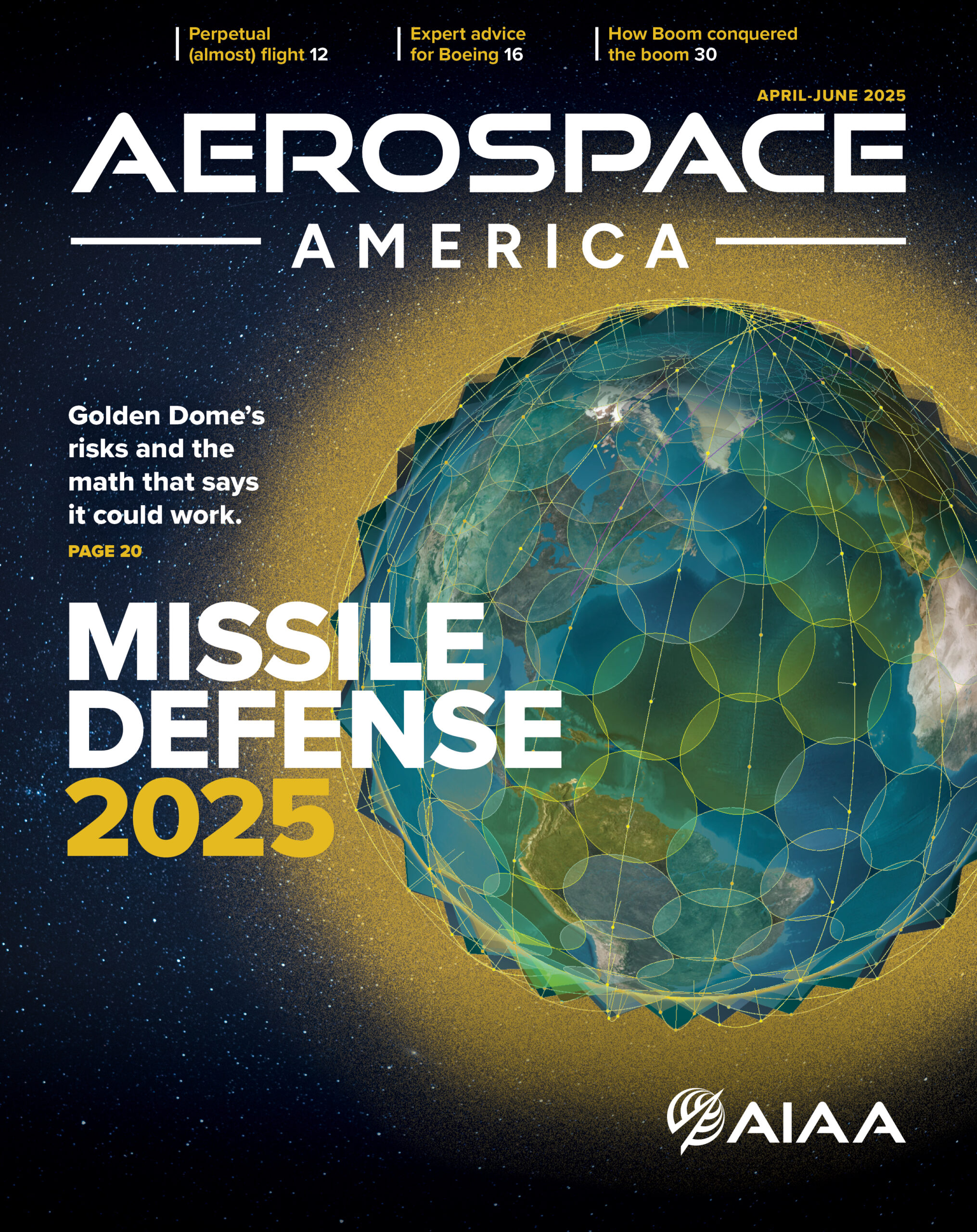