Stay Up to Date
Submit your email address to receive the latest industry and Aerospace America news.
The work of the Adaptive Structures Technical Committee enables aircraft and spacecraft to adapt to changing environmental conditions and mission objectives.
Purdue University’s Programmable Structures Lab tested a selective stiffness morphing wing section in a wind tunnel in May. The lightweight wing combines high stiffness for bearing aerodynamic loads and high compliance for aerodynamic adaptability. Geometrically bistable elements grant rigidity or compliance on demand via internal topology conversion. The wind tunnel campaign revealed that switching stiffness at low airspeeds triggers no aeroelastic instabilities, clearing an important hurdle for selective stiffness in aircraft structures.
Also in May, researchers at the German Aerospace Center, DLR, demonstrated a variable chord rotor in a Bristol wind tunnel and a DLR Braunschweig whirl tower. The demonstrator, developed by the European Union’s Shape Adaptive Blades for Rotorcraft Efficiency project, includes a structural concept for chord morphing in the blade root region. The tests confirmed that increasing chord length improves the demonstrator’s performance characteristics for hover. These results point to future rotor blades that morph across flight regimes, using a longer chord for hover flight and a shorter chord for fast forward flight.
A team at the Research Laboratory in Active Controls, Avionics and Aeroservoelasticity, or LARCASE at the University of Quebec’s School of Higher Technology, or ETS, in Montreal validated another morphing wing design. Tested in the Price-Païdoussis subsonic wind tunnel, the modified UAS-S4 wing airfoil has a morphing camber system that alters both leading and trailing edges. The tests confirmed the morphing camber system improves aerodynamic performance, including reducing the stall angle and drag. The morphing camber system uses the same servomotor as in the UAS-S4 to ensure the morphing actuation does not increase the overall weight.
The Harbin Institute of Technology in China conducted the first on-Mars application of shape memory polymer composites. A self-deployable mechanism released the national flag of China during the Tianwen-1 mission. Images sent back to Earth in June showed the rolled flag was flattened when two epoxy-based SMPC release devices recovered their original flat configurations. The validation of the self-deployable flag mechanism extends the application of SMPCs from geosynchronous orbit to deep space explorations.
Texas A&M University researchers eyed morphing in space for thermal control, finalizing a composite design for the Shape Memory Alloys for Regulating Thermal Control Systems in Space, or SMARTS, a NASA Tipping Point project. Researchers initiated fatigue testing of the intricate composite laminate in August. Test results show promise for the integration of the SMA-driven radiator into future lunar habitat thermal control systems.
Also at Texas A&M, researchers actuated additively manufactured SMA tensile bars via interior liquid metal circuitry for the first time in April, using current densities as high as 25 amps per square millimeter. These high current densities are difficult to achieve due to spontaneous liquid metal rupturing, but the circuits could increase the actuation power densities of SMAs to new regimes with multifunctional induction heating and fluid convection cooling.
In March, a team at Arizona State University demonstrated an automatic damage diagnosis technique through in-situ composite fatigue testing with funding from the U.S. Army Research Laboratory. The semi-supervised technique uses ultrasonic Lamb waves and machine learning to detect and classify fatigue damage in composite structures. In the tests, the team captured damage by identifying statistically significant patterns in waves and then classified it by analyzing patterns in the extracted damage features using a clustering algorithm. The same group extended its diagnosis and prognosis expertise to in-air flight safety, including data-driven aircraft health monitoring using an autoencoder with funding from the NASA University Leadership Initiative Program. The performance of the techniques was validated through integration into an air traffic management framework module in late July.
Researchers at California-based AlphaSTAR also focused on structural health monitoring with a customizable digital twin sensing and computing architecture. The approach includes both event detection and damage identification using onboard sensors, real-time analysis and feedback to estimate the remaining useful life.
Stay Up to Date
Submit your email address to receive the latest industry and Aerospace America news.
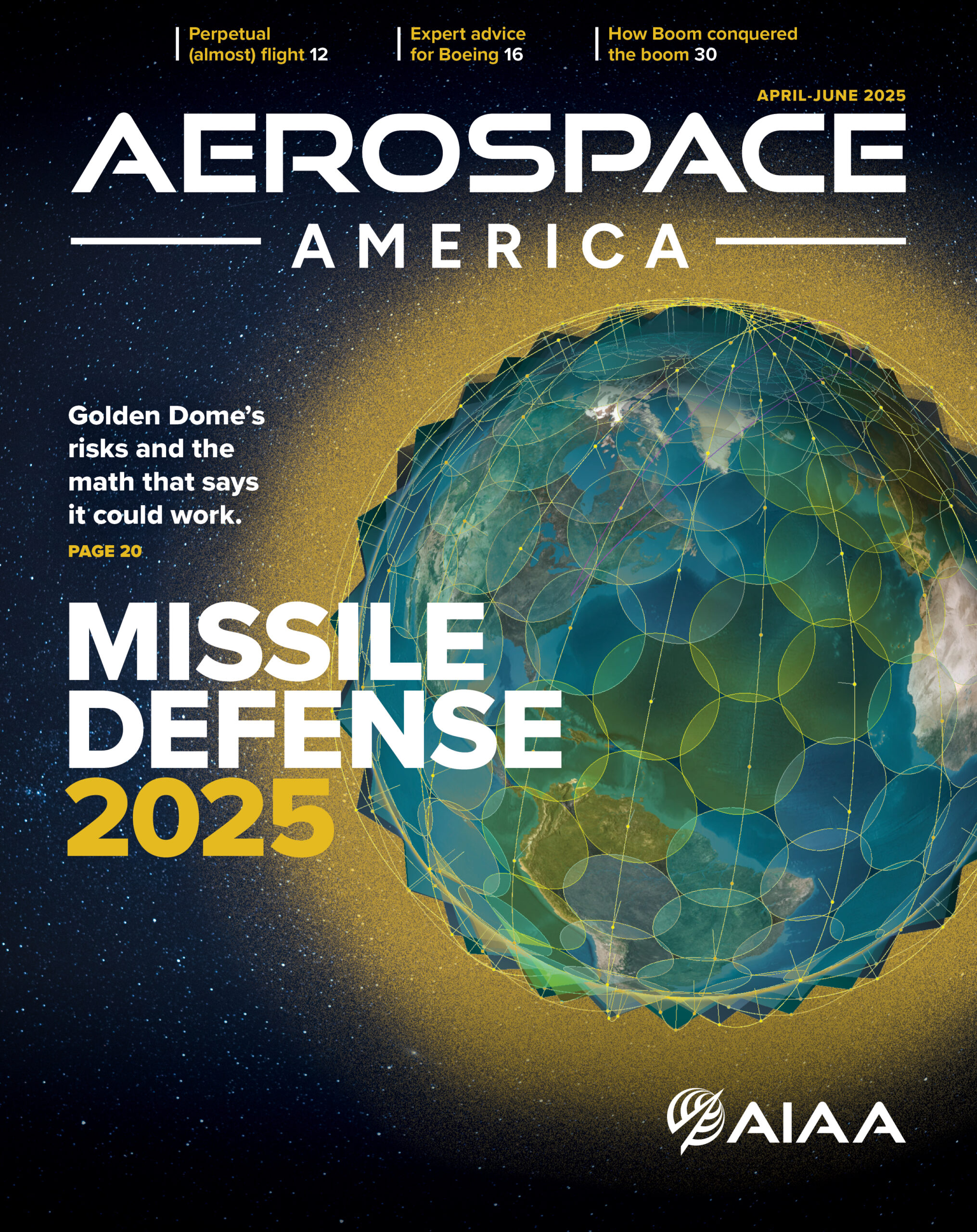