Stay Up to Date
Submit your email address to receive the latest industry and Aerospace America news.
The Energy Optimized Aircraft Systems Integration Committee works to promote a better understanding of energy optimized aircraft and equipment systems, from concept development to vehicle production, including relevant international academic and industrial experience.
Aircraft power and thermal management continued to mimic the automotive industry’s electrification trend. Early this year, the U.S. Air Force wrapped up its INtegrated Vehicle ENergy Technology, or INVENT program, which began in 2011. INVENT laid the foundation for future military power and thermal management development programs by advancing new technologies sized for insertion into today’s aircraft while testing these technologies in power and thermal systems targeting next-generation aircraft. INVENT also improved the aerospace industry’s understanding of how to develop and apply model-based engineering tools to design and test. The Air Force is using these tools to apply hybrid-electric propulsion and power technologies to unmanned aircraft to increase range and endurance.
New infrastructure that supports power and thermal management systems research and development rated from tens of kilowatts thru megawatt-class was moved into a systems integration facility in Dayton, Ohio. The Air Force repurposed the building in late 2017. It once housed a 5-foot wind tunnel with connections to Wilbur Wright.
At the Farnborough International Airshow in July, Britain’s Department for Business, Energy and Industrial Strategy announced a £255 million ($331 million) investment in greener flight technologies, including the Airbus E-Fan X hybrid-electric demonstrator. The Airbus, Rolls-Royce and Siemens partnership is projecting component development in 2019 and flight testing in 2020. The E-Fan X will replace one of the four gas turbines on the British Aerospace 146 flying testbed with a 2 MW electric motor to explore high-power propulsion system challenges. Also at Farnborough, United Technology Corp. Aerospace Systems announced it was building a high-voltage electric systems lab in Rockford, Illinois, with plans to double the energy density of today’s generators, motors and motor controllers from 5 kilowatts per kilogram to 10 kW/kg over the next few years.
The second annual Uber Elevate Summit took place in Los Angeles in May. Several companies announced plans for small air vehicles with passenger or package delivery capability. In October, Safran Helicopter Engines was selected to provide engines for Zunum Aero’s 12-seat ZA10 hybrid-electric aircraft with first commercial flights planned for the early 2020s. The ZA10 is being designed for 700 miles of range, targeting regional airport operation. Initial flight tests are planned for 2019. The fatal crash in May of the eFussion aircraft, developed by Siemens and Magnus, was a reminder that experimental aircraft must be fully vetted before entering commercial operation.
The NASA Electric Aircraft Testbed, or NEAT, near Sandusky, Ohio, is focused on testing electric aircraft components and powertrains. NEAT completed its first end-to-end powertrain testing in early 2018. NASA is developing the testbed to support aircraft relevant powertrain testing under flight-like scenarios, which include elements of high voltage, distribution over realistic/large wingspan, electromagnetic interference and high power research hardware. The first flight altitude simulation testing of electrical components was scheduled to begin late in 2018 in a chamber designed to support up to 50,000-foot climb conditions within a 20-foot diameter, two-story chamber.
In October, NASA held a public review at the Ohio Airspace Institute of nine contracts that cover aircraft and component design for single-aisle-class hybrid or turboelectric vehicles. Component development highlights included General Electric Global Research Center’s completion of a motor controller (inverter) that provides conversion for 1 MW at continuous power at greater than 99 percent efficiency and 17.5 kW/kg power density. The University of Illinois Urbana-Champaign, or UIUC, and Ohio State University also reported design completion and build progress for 1 MW motor designs. Testing for the UIUC motor was scheduled to start late in the year at the United Technology Corp. Aerospace Systems lab in Illinois.
Editor’s note: Michael Ikeda works at United Technology Corp.
Photo: Hardware prototypes of an inverter for high-density, low-inductance electric motors. The metal heatsink version, top, achieves an efficiency of 98.6 percent, and a power density above 17 kilowatts per kilogram. The version with micro-heatsinks and 3D printed plastic enclosure, bottom, is undergoing tests, and is expected to yield approximately a 50 percent power density improvement. Credit: University of California, Berkeley
Stay Up to Date
Submit your email address to receive the latest industry and Aerospace America news.
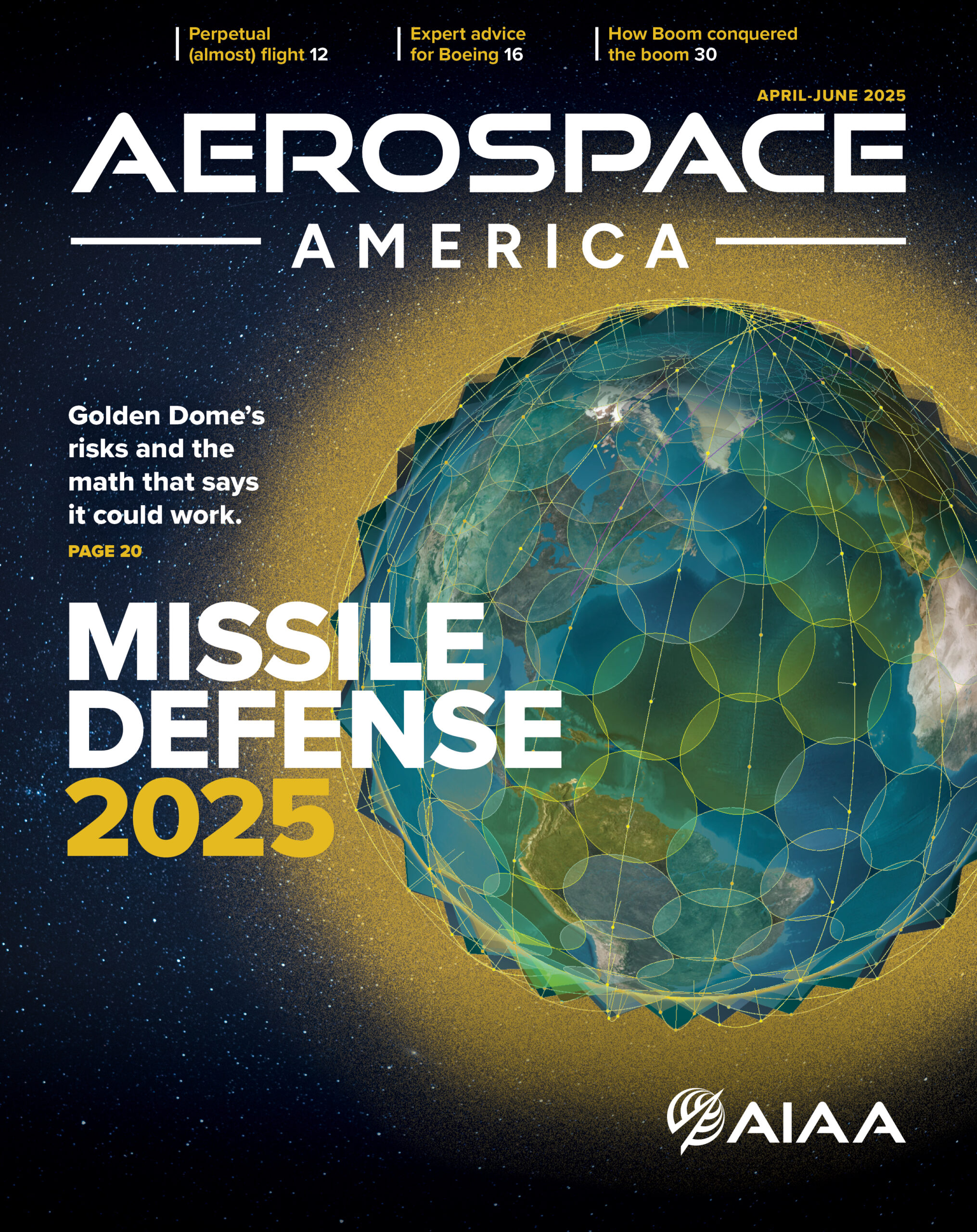