Stay Up to Date
Submit your email address to receive the latest industry and Aerospace America news.
The Microgravity and Space Processes Technical Committee encourages the advancement and public awareness of low-gravity studies in physics, materials, biological sciences and related fields.
In March, researchers from Rensselaer Polytechnic Institute in New York, in collaboration with Tec-Masters Inc. of Alabama, sent an experiment to the International Space Station. The Microgravity Research for Versatile Investigations-Phase Change in Mixtures, or MaRVIn-PCIM, experiment focuses on how fluid mixtures, particularly liquid and vapor, influence the functionality of wickless heat pipes under the conditions of microgravity. The pipes were installed in the Microgravity Science Glovebox in August, where one end of a pipe is heated to evaporate a liquid while the other end is cooled to condense the vapor back. This allows the researchers to observe and map shifts in the vapor-liquid boundary. Drawing upon previous experiments, the researchers chose a 50/50 mixture of pentane and isohexane liquids. Results from this investigation may enhance the efficiency of heat pipes, which are integral to various space applications, including satellites, rovers and space telescopes, where maintaining optimal temperature levels is crucial. The results could also further the research and development of advanced, lightweight and efficient cooling mechanisms tailored for future space missions. On Earth, heat pipes are pivotal in thermal management of microelectronic components present in laptops, graphics cards, avionics, hypersonic systems and nuclear reactors.
In May, researchers from Auburn University in Alabama and the University of California-Davis published their findings from the Pore Formation and Mobility Investigation-Asymmetric Sawtooth and Cavity-Enhanced Nucleation-Driven Transport study. They demonstrated a passive cooling system for electronic devices in microgravity via a microstructured surface, meaning one textured like saw teeth. In microgravity, boiling fluids over flat, heated surfaces creates larger vapor bubbles due to the absence of buoyancy force, leading to inefficient heat transfer. This inefficiency can result in unpredictable surface temperature spikes, potentially damaging electronic devices. Sponsored by NASA, funded by the National Science Foundation and developed by Techshot Inc., which Redwire Corp. of Florida acquired in 2021, a series of experiments were conducted between December 2022 and January 2023. Observations indicated that in microgravity, vapor bubbles rode on the crests of the saw teeth, whereas the baseline flat surface yielded stationary vapor bubbles that expanded in situ. The microstructure granted access to liquid pockets within the troughs for vapor bubbles upon reaching a specific mobility diameter, which enlarged with the elevation of heat input within the low heat flux range assessed. A comparable mobility was noted for the downward- facing terrestrial surface, with larger vapor slugs gliding over the microstructure in the direction of the extended slope. Conversely, the baseline surface yielded static vapor slugs that enveloped the entire heated region, devoid of a noticeable thin liquid layer. The identified vapor mobility could address a persistent microgravity issue, facilitating two-phase high-heat flux dispersion in electronic devices.
In February, Gravitilab Aerospace Services Ltd. conducted its first microgravity experiment aboard a drone at the Predannack Airfield testing site in Cornwall, United Kingdom. This facility offers an alternative to the ZARM drop tower in Bremen, Germany, which provides microgravity for between 4.74 and 9.3 seconds. Gravitilab’s drone climbed to an altitude of 610 meters and then dropped an unspecified payload inside the company’s LOUIS drop pod, providing microgravity for a handful of seconds. The test was commissioned by the Cornwall and Isles of Scilly Local Enterprise Partnership in an effort to enhance the U.K.’s space industry prominence. With the potential to provide gravity-free testing durations of up to 12 seconds, this technology has the potential to transform how a myriad of industries test.
Stay Up to Date
Submit your email address to receive the latest industry and Aerospace America news.
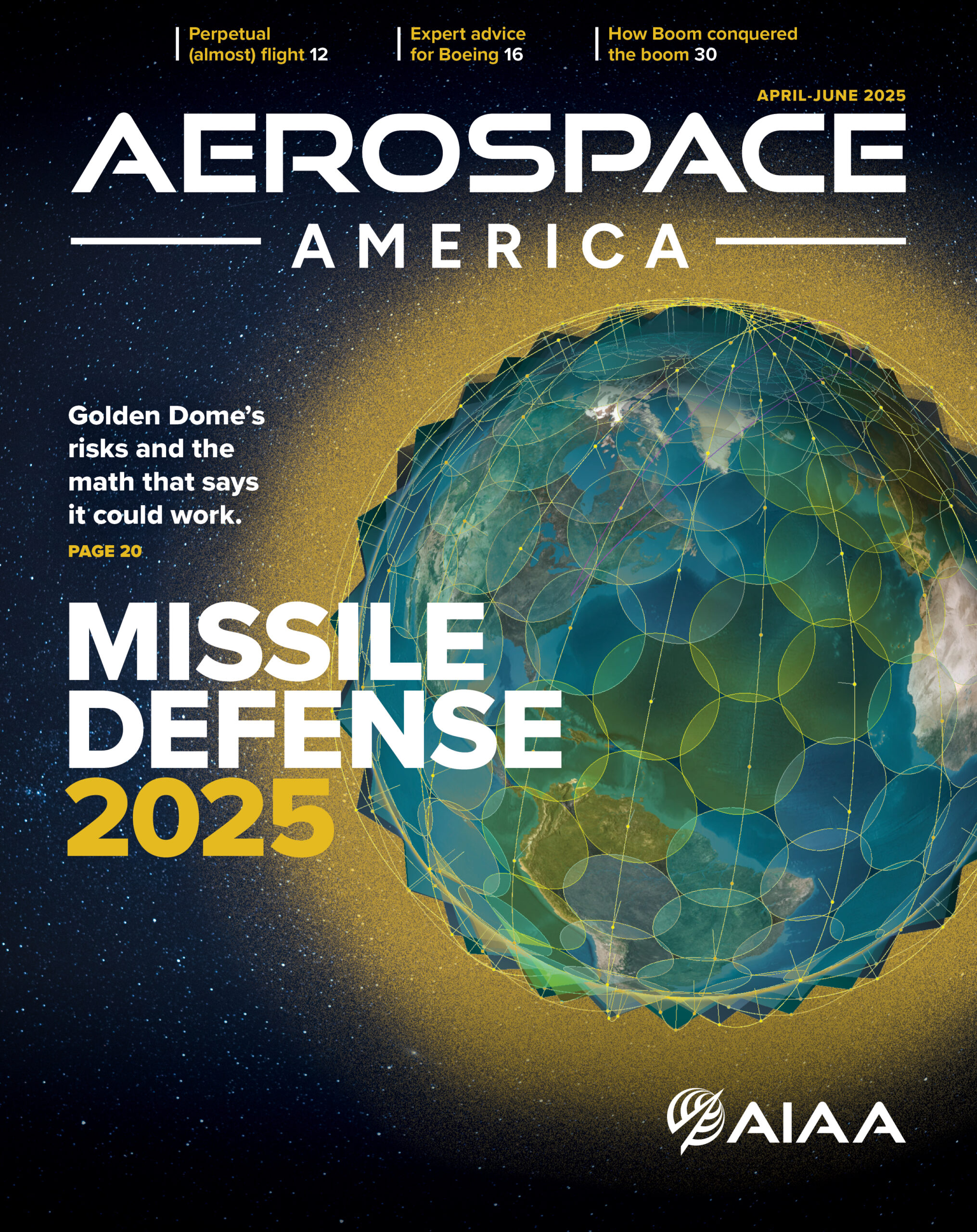