Stay Up to Date
Submit your email address to receive the latest industry and Aerospace America news.
The Non-Deterministic Approaches Technical Committee advances the art, science and cross-cutting technologies required to advance aerospace systems with non-deterministic approaches.
In June, Southwest Research Institute, or SwRI, broke ground on the Center for Accelerating Materials and Processes, a 3,200-square-meter facility for “research and development of high-speed aerospace engines,” the organization said in a press release. Initial projects are to focus on “demonstrating faster, more efficient techniques for manufacturing high-speed propulsion systems,” with probabilistic and uncertainty quantification, or UQ, approaches being applied to drive qualification of new manufacturing techniques.
In January, during AIAA’s SciTech Forum in Orlando, Florida, the Fluid Dynamics Technical Committee hosted two special sessions on its proposed solution to a UQ challenge problem. During the session, meant to encourage engagement between the UQ and fluid dynamic communities, attendees compared the costs and strengths of different techniques. A follow-on challenge problem is under development.
Also in January, SwRI produced a first-of-its-kind study quantifying sources of uncertainty in aircraft structural integrity and lifing. With inspection and teardown data from the U.S. Air Force’s T-38 fleet, researchers performed a sensitivity analysis of the equivalent initial flaw size distributions required for single flight probability of failure, or SFPOF, assessments. This study concluded that better characterization of crack growth rate uncertainty and alternative inspection methods below a certain crack size threshold would best reduce uncertainty in SFPOF.
In March, SwRI — in support of NASA’s multiyear effort to determine the continued fitness-for-service of aging, noncoded layered pressure vessels — developed a critical flaw size analysis approach for cleavage fracture. The analysis employed the NASGRO software to guide nondestructive evaluation requirements. Recent developments included probabilistic approaches to understand uncertainty in geometry, loading and material properties and their impacts on critical flaw size predictions.
In May, University of Maine researchers explored UQ and design optimization methods to advance integrated process and product design of large additive manufacturing of fiber-reinforced thermoplastic and composite structures with the Factory of the Future 1.0 printer. The multifidelity modeling and simulation workflow relies on high-performance computing, with data-driven process-structure-property relationships accounting for uncertainties throughout the product realization process.
In July, the Advanced Structures and Optimization Lab at Virginia Tech proposed a novel methodology for UQ in magnetic phase transitions, effectively capturing long-range interactions and their effects on free energy and magnetization. The methodology highlighted the potential of quantum computing to address computational challenges in modeling of these complex systems.
In July, researchers from the University of California, San Diego and the University of Michigan-Dearborn introduced a new methodology for diagnosing and predicting pitting corrosion via multiscale simulations, a convolutional neural network and Bayesian updating.
In July, SwRI calibrated adhesive properties of a pi preform joint demonstration article, which are challenging to measure experimentally in the bonded joint configuration. This calibration was performed with SwRI’s CENTAUR tool and is part of a multiyear program applying verification, validation and UQ methods to develop computational analysis tools to reduce testing of bonded 3-D carbon/epoxy textiles for certification.
From June to August, SwRI developed and applied a probabilistic workflow to characterize anomaly distributions of additive manufactured parts for risk-based life assessments. Anomaly distributions and exceedance curves are needed for probabilistic damage tolerance analysis of fatigue-critical aerospace parts, with the developed approach using extreme value statistics and additive manufacturing-specific adaptations for implementation in the SwRI software DARWIN.
In August, researchers from the University of California, San Diego proposed a new multifidelity method to estimate the entire distribution of quantities of interest of complex engineering systems. The method was demonstrated on a high-dimensional model, and its surrogate, to model the brittle fracture behavior of a fiber-reinforced matrix.
Contributors: Pinar Acar, Barron Bichon, Andrew Cary, Ender Eger, Michael P. Enright, Zhen Hu, Laura Hunt, Matthew Kirby, Boris Kramer, Masoud Rais-Rohani, David Riha, Vicente Romero, Markus Rumpfkeil, James Sobotka and Marcus Stanfield
Stay Up to Date
Submit your email address to receive the latest industry and Aerospace America news.
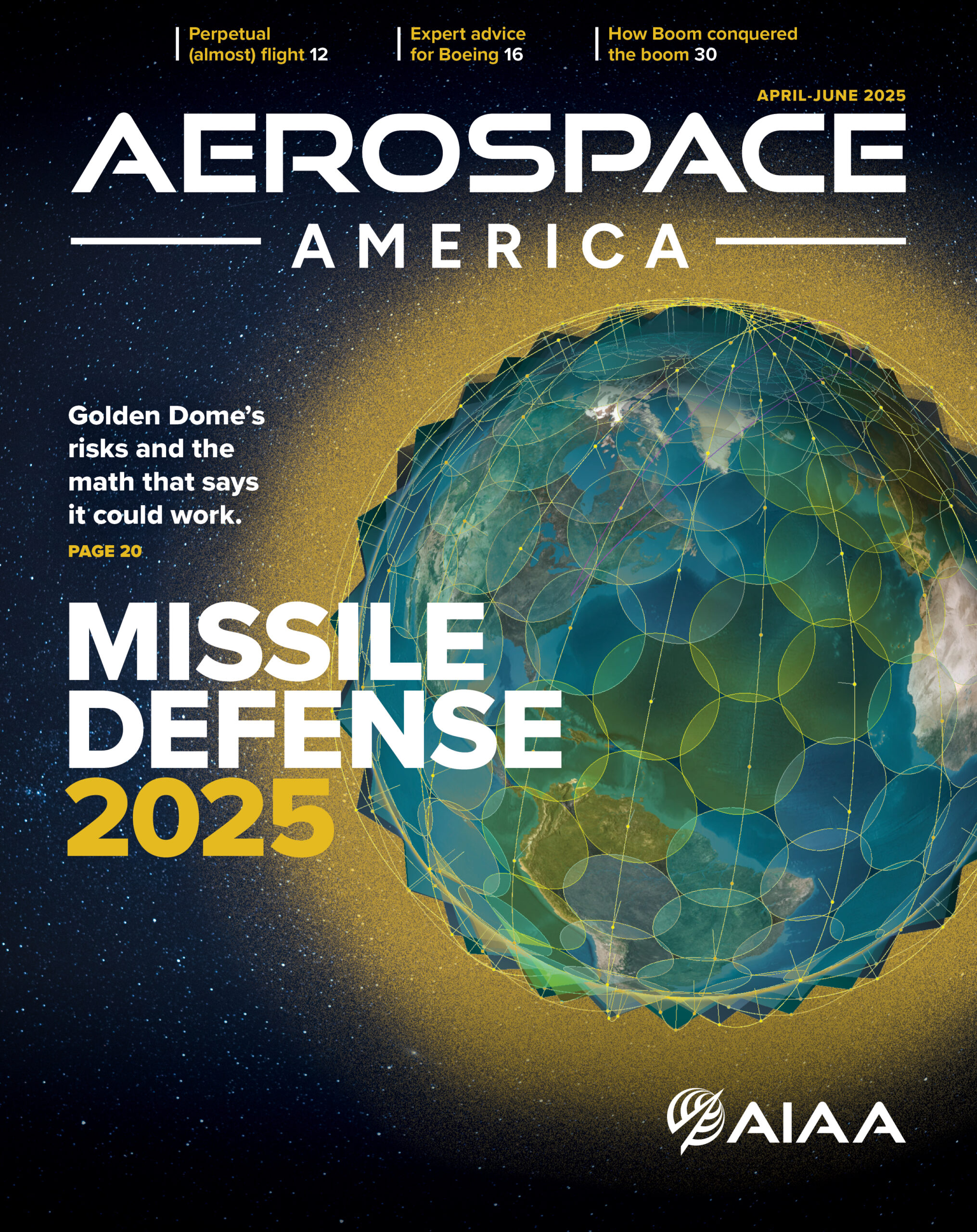