Stay Up to Date
Submit your email address to receive the latest industry and Aerospace America news.
The airline industry is anxious to get on the right side of the climate change issue sooner rather than later. Karen Kwon tells us about a fuel with a limitless feedstock that could be the way to net-zero, provided it can be produced in high enough quantities.
On a Sunday in February 2008, a Virgin Atlantic Boeing 747 with two pilots and some technicians took off from London bound for Amsterdam for a history-making test flight. One of the jet’s four engines burned a mix of 80% conventional fuel and 20% fuel derived from coconut and babassu palm seed oil, making Virgin the first airline to fly a jet at least partially on biofuel.
“This pioneering flight will enable those of us who are serious about reducing our carbon emissions to go on developing the fuels of the future, fuels which will power our aircraft in the years ahead,” proclaimed Richard Branson, the founder of Virgin Group, in a press release at the time.
Just as Branson predicted, various classes of alternative jet fuels have been introduced in the years since, most lately in the name of meeting a goal of achieving net-zero carbon emissions by 2050. On the one hand, commercial aviation accounts for just a few percent of global carbon emissions — 2.4% as of 2018. On the other hand, if those emissions came from a country, that percentage would place the country sixth in terms of highest carbon dioxide emissions, between Japan and Germany. Also in the years since 2008, the industry adopted the term “sustainable aviation fuel,” or SAF, to capture the idea of fuels produced from a variety of possible feedstocks whose production won’t deplete natural resources.
First to catch on were the biofuels, and then came fuels derived from waste including municipal garbage, used cooking oils and discarded animal fats. Now, a fierce competition is playing out to be first to affordably mass produce the next class of SAFs, and one that arguably could be the most environmentally friendly yet. Carbon dioxide would be culled from the air in massive volumes, mixed with water, and this brew would be electrified to create hydrocarbons.
The plans of two rivals in the field are emblematic of the contrasting strategies and the drama ahead as they and a handful of others race to meet a goal of making electrofuel SAFs widely available to airlines, possibly by 2025. One of the companies is Johnson Matthey, a multinational chemicals and sustainable technologies firm headquartered in England with 14,000 employees that licenses key technologies to SAF producers. Another is Prometheus Fuels, a California startup of about 30 employees. In 2019, investors such as Maersk and BMW valued Prometheus at $1.5 billion, making it the world’s first electrofuels company to be valued at over a billion dollars.
Johnson Matthey and Prometheus share the goal of contributing to, and perhaps even dominating, the airline industry’s effort to become carbon neutral by 2050, and doing so without creating new societal or environmental negatives. Like all SAFs, the electrofuels must be similar enough, chemically speaking, to conventional jet fuels that they could someday replace today’s Jet A and Jet A-1 fuels without any engine modifications. Current regulations don’t allow a plane to fly solely on such “drop-in” SAFs of any form. The fuels must be mixed in with the conventional kind to a maximum blend of 50/50.
This cautious rollout ensures that “airplanes [burning SAFs] don’t start falling out of the sky all of a sudden,” says Martin Junginger, a professor of bio-based economy at Utrecht University in the Netherlands. However, that fact also means that engines powered by SAFs emit almost exactly the same amount of carbon dioxide as those burning conventional fuels, though preliminary research shows that SAF may produce less soot than conventional fuels, yielding less environmental harm at high altitudes.
So how can any SAF, electrofuel or otherwise, bear the “sustainable” moniker? In the case of an electrofuel, no more carbon dioxide would be released during combustion than was culled from the atmosphere, although combustion is not the only place the carbon question arises. In the case of a biofuel, such as the one demonstrated by Virgin, the emissions from the aircraft would be offset by the fact that new fuel crops are continually growing, and as they do they extract carbon dioxide from the air to create the carbon compounds that form their stems, leaves and fruit. The International Civil Aviation Organization, the United Nations agency that sets guidelines for deciding whether a fuel should be considered a SAF, considers such sequestration of carbon a “negative” in the mathematical sense of sequestration subtracting carbon from the atmosphere. Another example of a negative would be the amount of methane gas averted when municipal garbage is turned into SAF, rather than being allowed to rot in a landfill.
The ideal sum in each case would be a self-sustaining cycle that does not add carbon dioxide to the atmosphere. However, one big proviso looms. ICAO assesses the entire carbon footprint of SAF production, meaning the complete life cycle spanning from the fuel’s origins as a feedstock to its processing and transport. Just how sustainable a SAF truly is depends on how much fossil fuel, if any, was burned to power the tractor that plowed the fields or the equipment that harvested or processed and transported the feedstock.
Looking through that lens,“not everything is sustainable; there’s actually quite a lot of variation,” says Nikita Pavlenko, fuels program lead for the International Council on Clean Transportation, a Washington, D.C.-based nonprofit research group.
Prometheus thinks it has an edge here. By taking charge of the entire process, from capturing carbon dioxide from the air to creating the SAF in a multistep process, the company plans to make sure the energy for each step comes from renewable sources such as solar panels. And the company sees another benefit:
“It turns out being able to integrate all of the engineering from air capture to fuel delivery allows you to be very low cost,” says Rob McGinnis, founder and CEO of the company.
With a commercial-scale prototype in hand, the company announced a deal with American Airlines last July in which American would purchase up to 10 million gallons (38 million liters) of SAF from Prometheus by 2025.
Johnson Matthey, in contrast, leaves the carbon dioxide capture to others and is focusing on the chemical conversion aspect. Deciding what constitutes environmentally friendly should be up to legislation passed by governments around the world, says Paul Ticehurst, who develops new business opportunities for the company, adding, “we take sustainability really seriously.”
So how do their respective technologies work? There is more than one way to make jet fuel from carbon dioxide, but all involve electrolysis, in which electricity flows between a cathode and anode in a container of some kind and provides electrons to water molecules to produce oxygen and hydrogen gases. This is where the “electro” part comes from in the name electrofuel, and why this fuel-making process is often called “power-to-liquid.”
Beyond that, the plans of Johnson Matthey and Prometheus differ markedly. Prometheus plans to expand from its prototype to build shipping-container-sized devices it calls Titan Fuel Forges. Just as with the prototype, air will be sucked into each device, where water will absorb carbon dioxide gas. Electrolysis then breaks down the water, with the resulting hydrogen combining with the carbon dioxide to form bicarbonate that will be converted to alcohol. This synthesized alcohol will be transformed into SAF through a process called alcohol-to-jet. The company plans to apply the same overall technology to produce gasoline and diesel as well.
In another difference, Johnson Matthey avoids the alcohol step. Hydrogen gas combines with carbon dioxide to create carbon monoxide, which then combines with more hydrogen to produce synthesis gas, or syngas. Syngas will be further processed via a chemical process called Fischer–Tropsch into synthetic crude oil, which will then be transformed into diesel, gasoline and SAF.
No matter whose strategy turns out to be best, backers of electrofuels see an additional environmental and social advantage to their products that has nothing to do with carbon. Between 2009 and 2011, auto fuel-makers received backlash as production of bioethanol, such as corn ethanol, caused food prices to spike in some locales. That experience made the aviation industry “extremely reluctant in using any vegetable- or food-crop-based fuels,” says the Utrecht professor Junginger.
Cost, not surprisingly, was also an issue.
“When you’re growing a crop, you need a lot of land, you need a lot of sunlight, you need a lot of fertilizer, you need a lot of water,” says Aaron Robinson, senior manager of environmental strategy and sustainability at United Airlines, “which ultimately makes it rather expensive to go and produce it.”
At least for the near term, the airlines are showing more interest in SAFs made from waste. In December, for example, a United Airlines Boeing 737 MAX 8 took off from Chicago on a regularly scheduled flight to Washington, D.C., becoming the first passenger jet to fly on 100% SAF in one of its two engines. The SAF was made from cooking oil and discarded animal fats.
“The great thing about waste is it’s relatively affordable to procure because no one really wants it or has another good use for it,” says Robinson.
At the same time, Robinson thinks that the industry will eventually have to shift away from concocting SAFs this way as society moves toward reducing waste and more people look to travel by air.
“Ultimately, there’s not going to be enough waste to be able to source to produce [fuels] for all the needs,” he says.
Here’s how Junginger sums it up: “The problem is that we have to basically eat french fries for probably 10 years in order to be able to fly short distance.”
Because of its size, electrofuel-maker Johnson Matthey says it’s especially well positioned to meet the growing demand for jet fuel.
“We think that it’s important that the big companies are involved in [the electrofuel production], not just the small developers, because we can get to that scale that’s required so much quicker,” Ticehurst says.
As for where matters stand, the competitive development of electrofuels is playing out against a backdrop of research toward hydrogen-powered aircraft by Airbus and research into radical new aircraft designs that move away from tubes with wings.
The electrofuel companies are well aware of this, but Ticehurst says time is on their side.
“We’re saying sustainable aviation fuel is key because it’s something that can be done today.”
“It turns out being able to integrate all of the engineering from air capture to fuel delivery allows you to be very low cost.”
Rob McGinnis, Prometheus Fuels

About Karen Kwon
Karen is a science journalist based in the Washington, D.C., area, and is the associate editor of Optics & Photonics News. She holds a doctorate in chemistry from Columbia University and previously wrote about physics, space science and technology for Scientific American.
Related Posts
Stay Up to Date
Submit your email address to receive the latest industry and Aerospace America news.
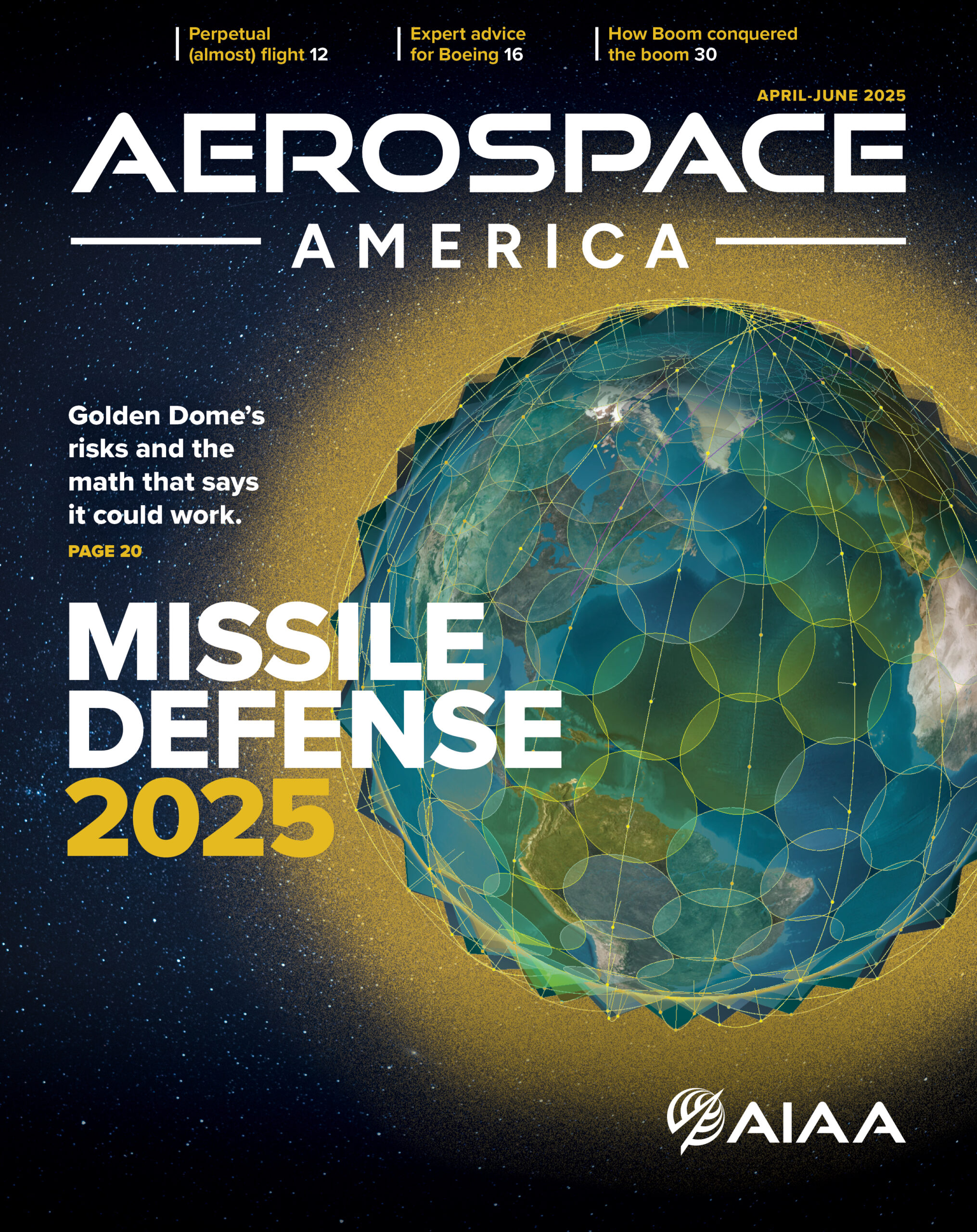
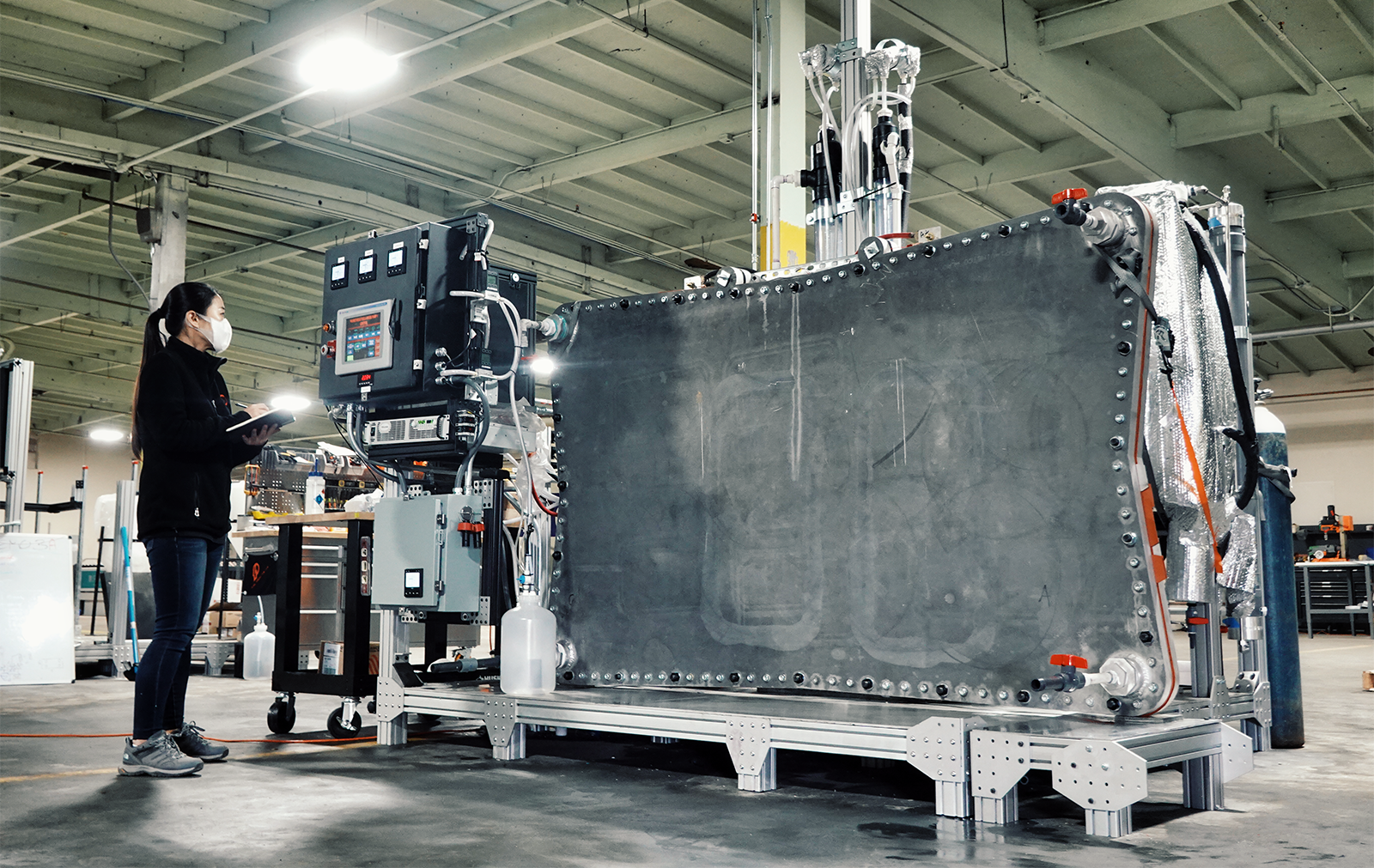
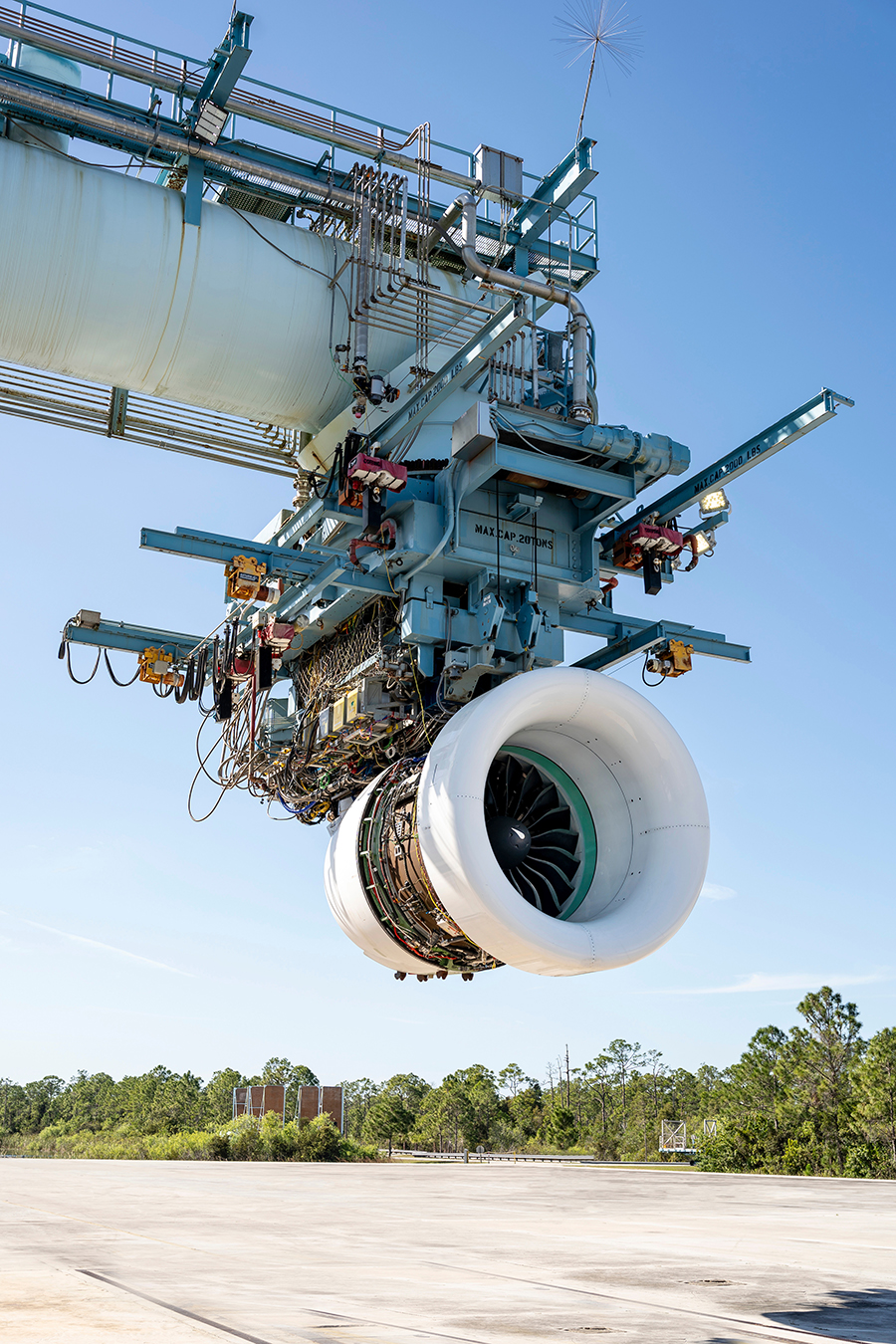