Stay Up to Date
Submit your email address to receive the latest industry and Aerospace America news.
The Energetic Components and Systems Technical Committee provides a forum for the dissemination of information about propellant and explosive-based systems for applications ranging from aircraft to space vehicles.
To burn solid propellants more quickly,
propulsion engineers often turn to burn rate modifiers, chemical compounds that speed up combustion. However, conceptual roadblocks remain in describing how these burn rate modifiers control combustion. In June, researchers from Texas Tech University tackled the problem by designing a material intentionally packed with all the properties predicted to play a role in modifying propellant burn rates. The new material is called a metal-inorganic-framework, or MIF. The molecular structure of a MIF resembles a metal-organic framework, except the linker molecule is inorganic and the whole compound is oxidizer rich. With the MIF powder, researchers tailored propellant burn rates with new intuition — one that takes specific aim at the confusion between material properties and their functional relationship with combustion performance. Key properties include a targeted decomposition energy threshold, high porosity, surface chemistry to trigger catalysis and metal cations that incite exothermicity. They published their breakthroughs in August in the journal Advanced Engineering Materials.
In February, researchers from Purdue University in Indiana and the Lawrence Livermore National Laboratory in California published an editorial in the journal Propellants, Explosives, and Pyrotechnics. The focus was on embracing anisotropy in energetic materials made via advanced and traditional manufacturing methods. In the editorial, the researchers issued a call to industry to develop new diagnostic and analysis techniques to assess anisotropic properties of next-generation propellants. In this vein, researchers from Purdue University’s Zucrow Laboratories presented their new technique for measuring the adhesion between dissimilar polymer materials at the AIAA SciTech Forum in January. In their experiments, adhesion between 3D-printed thermoplastics and hydroxyl-terminated polybutadiene was quantified for the first time. Quantifying interfacial properties as a function of material and manufacturing techniques could provide new data for assessing anisotropy in new energetic systems.
In June, the University of Minnesota’s Plasma Power Propulsion Laboratory began a partnership with the U.S. Army Research Laboratory to expand the laser-induced air shock from energetic materials, or LASEM, technique for customized propellant development. LASEM assesses shock velocity generated by a high-energy laser pulse on small solid fuel samples to evaluate novel tailored propellants. Nanoenergetic materials are crucial for propulsion due to their high-energy density and faster burn rates, which surpass conventional propellants such as hydroxyl-terminated polybutadiene. The Minnesota lab applied a physics-driven approach to tailor coat nano aluminum particles by exploring the fundamental multistage complex combustion dynamics. When exposed to a high-energy laser pulse, the aluminum nanoparticles vaporized and underwent a two-stage combustion process. The initial microsecond combustion phase enhanced laser-induced shock speed, potentially correlating with detonation velocities of nanoparticles. In the subsequent millisecond phase, ejected materials underwent solid-phase combustion, allowing for the exploration of heterogeneous aspects of metal nanoparticle combustion. Because shock velocity is influenced by propellant reactivity, that factor is a valuable tool for the rapid development of highly reactive propellants. With the LASEM technique, the researchers conducted cost-effective testing of new propellant formulations with milligram- to gram-sized samples, eliminating the need for expensive testing with kilogram-sized samples.
Contributors: Sayan Biswas, Mitch Donoughue, Monique McClain, Michelle Pantoya and Binit Singh
Stay Up to Date
Submit your email address to receive the latest industry and Aerospace America news.
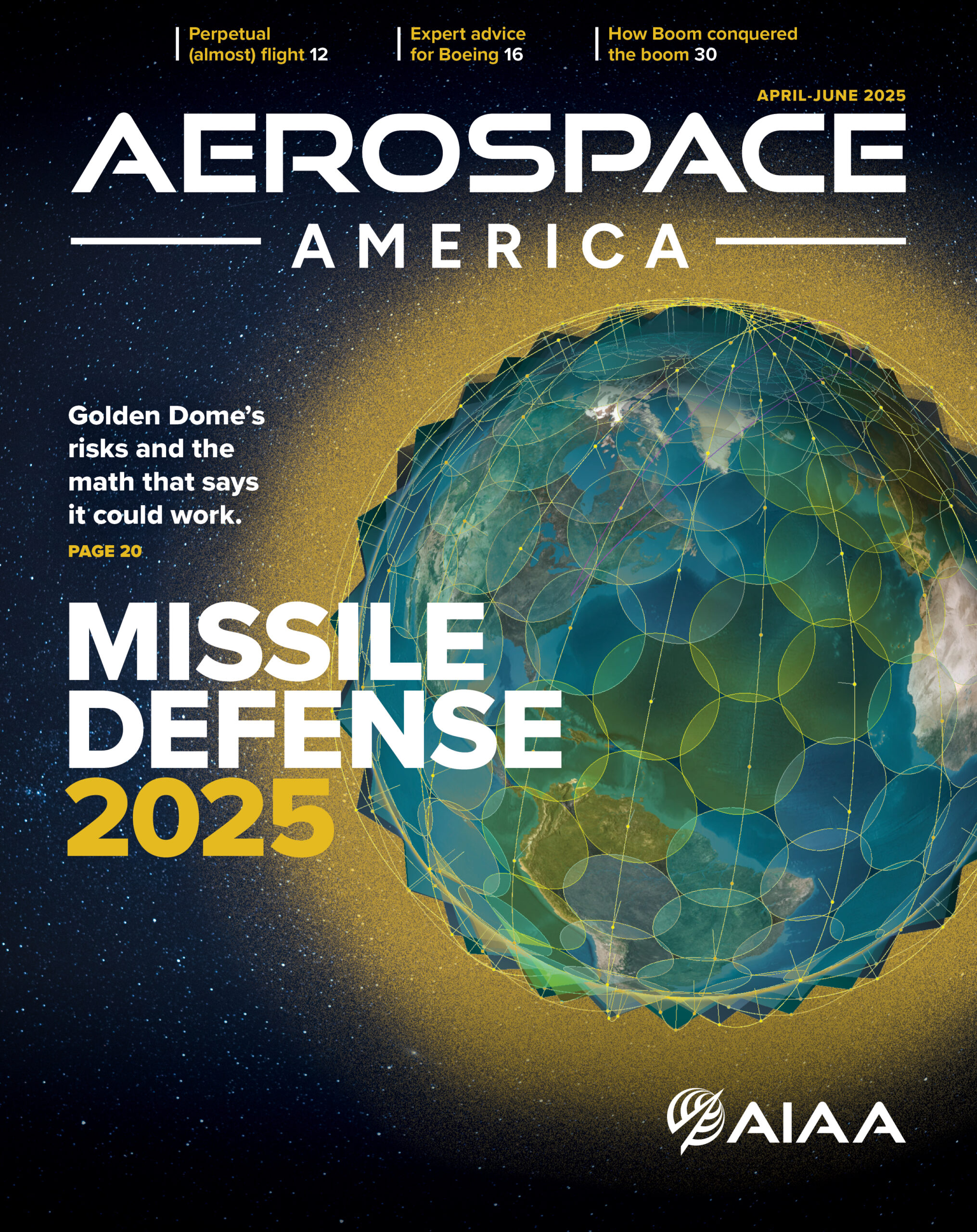