Stay Up to Date
Submit your email address to receive the latest industry and Aerospace America news.
The Materials Technical Committee promotes interest, understanding and use of advanced materials in aerospace products where aerospace systems have a critical dependency on material weight, multifunctionality and lifecycle performance.
This year the Massachusetts Institute of Technology and Metis Design Corp. collaborated to demonstrate an “out-of-oven” composite curing process that addresses the limitations of conventional oven- and autoclave-based processes. Those drawbacks include poor energy efficiency, high operational cost, long cure times and geometrical constraints on the components to be cured. In August, the team demonstrated carbon nanotube heaters for conductively curing composite structures without an oven, achieving equivalent thermophysical and mechanical performance to conventionally cured composites, while reducing cure time by 60% and energy consumption by two orders of magnitude. The team believes that this process contributes to the design and manufacturing of next-generation multifunctional architectures by leveraging nanoengineered laminate capabilities such as sensing, structural health monitoring and ice protection systems.
In July, KAI LLC, the University of Texas at Austin, RMIT University of Melbourne, Australia, Arkema Inc. and Western Washington University collaborated on a study to utilize high-temperature fused filament fabrication technologies to manufacture five unique ultraperformance polymers: SABIC PEI ULTEM 9085, Roboze PEEK, Smart materials 3D PEEK, Arkema Kepstan 7002 PEKK and a modified PEI (ULTEM 1010) material. These can be used in low-heat-flux spacecraft application. The goal of the research was to develop a class of materials and additive manufacturing processes that could one day substantially reduce the manufacturing and assembly costs of space vehicle thermal protection systems. All five ultraperformance thermoplastics were able to withstand aerothermal testing at a heat flux of 100 watts per square centimeter for as long as 30 seconds without disintegrating. Based on thermogravimetric analysis char yield results, Kepstan 7002 PEKK has the highest char yield of 64% and ULTEM 9085 has the lowest char yield of 43%. High char yield usually indicates material has good ablation performance. In addition to experimental study, computational fluid dynamics analyzed the heat transfer between the specimens under various scenarios compared with material response obtained experimentally.
In February, Nanoarmor LLC and the U.S. Naval Research Laboratory manufactured 70% dense zirconium carbide composites using additive manufacturing. These ultra-high-temperature ceramics, or UHTC, offer superior properties that enable their use in leading edges and engine components in extremely high-temperature platforms. Existing refractory ceramics do not offer adequate mechanical and thermal properties to handle extreme environments. Furthermore, corresponding manufacturing methods cannot yield customizable and cost-effective leading-edge components for high-performance aerospace systems. The Nanoarmor-Naval Research Lab technique produced inexpensive UHTC zirconium carbide ceramic matrix composites with nanostructured reinforcements that maximize density, hardness and durability under high temperatures and mechanical stress. The polymer-based reaction bonding synthesis route yields net shape carbides, nitrides and borides from compressed powder mixtures of metal precursors and carbon-rich resins with high char yields. In addition, the approach is pressureless and incorporates a one-step reactive melt infiltration process that converts preceramic mixtures into dense custom forms at 1,400 degrees Celsius. The approach is significantly less expensive than existing alternatives. They reinforced the ceramic matrix composites with metals, fibers, nanocarbons and secondary ceramic phases in order to improve their mechanical strength, thermal conductivity, and resistance to oxidation and ablation. Blends of these precursor materials with polymer binders into suspensions with controllable viscosities unlock capabilities for inexpensive rapid prototyping of customized shapes with tunable dimensions, geometries and properties.
Contributors: Boris Dyatkin, Joseph H. Koo and Brian L. Wardle
Related Posts
Stay Up to Date
Submit your email address to receive the latest industry and Aerospace America news.
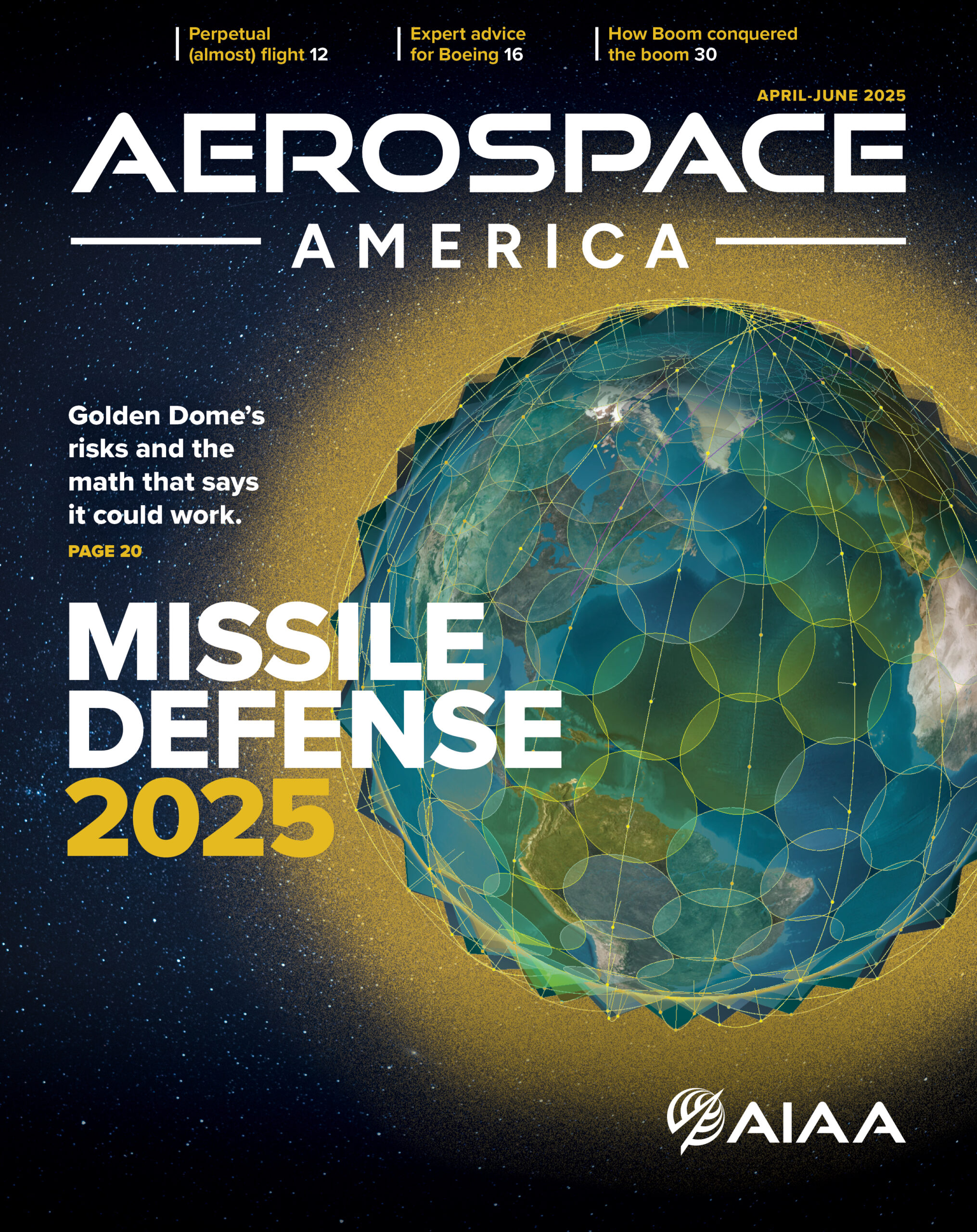