Stay Up to Date
Submit your email address to receive the latest industry and Aerospace America news.
The Propellants and Combustion Technical Committee works to advance the knowledge and effective use of propellants and combustion systems for military, civil and commercial aerospace systems.
The aviation community continues to emphasize sustainability — with many efforts focused on thermal and propulsive efficiency — while also urging higher-speed flight regimes. This has motivated researchers to use disruptive technology with fundamental and applied efforts to tackle the new and extreme operating conditions. One such movement is the adoption of hydrogen as fuel, which was a pillar in the August establishment of the Combustion and Propulsion for Aviation Research Center at the University of Tennessee Space Institute. The center’s goals are to improve flame stabilization and injector design and to reduce nitrogen oxide emissions in hydrogen-fueled gas turbine combustors.
A joint experimental and computational research program of Georgia Tech, General Electric and the FAA’s Center of Excellence for Alternative Jet Fuels and Environment, or ASCENT, in January began investigating novel low-emission gas turbine combustors for supersonic civil transport. The unusual conditions that occur in the combustors of supersonic transports make it challenging to control pollutant emissions. The team is leveraging advanced manufacturing techniques and the high temperature air created at supersonic flight speeds to rapidly premix the fuel and air prior to combustion. The researchers are using laser-based measurements of the fuel/air mixing, velocity field and nonvolatile particulate matter to explain the flame stabilization process within and beyond the design-intent parameter space. Large-eddy simulations are both supplementing the experimental data and exploring the cost/accuracy tradeoff for this type of combustor. The effort is helping to enable the rapid pursuit of higher speed civil propulsion systems while also aligning with the aviation sector’s sustainability goals.
In January, researchers at the University of Michigan and Georgia Tech published the results of their experiments using a machine learning model to look for a smarter means of mitigating combustion behavior that can lead to catastrophic mechanical failure. They trained the model using existing swirl combustor experimental data, which exhibited two flame states, lifted and attached, for the same operating conditions. While the transition between states was spontaneous, the machine learning approach captured the key features in the flame velocity field when trained using only one of the states. Moreover, a prediction of the impending transition between states was also possible using a different machine learning tool based on clustering of data, which enables a reduced probabilistic interpretation of the system state. Researchers are using the results for real-time prediction of extreme events that ultimately lead to mechanical failure in combustors. Due to the small timescales associated with extreme events, predictions must occur in real time. This motivates a combination of reduced order models and low-latency hardware, which in turn motivates machine learning. As such, the fusion of probabilistic modeling, unsupervised learning and low-energy — for example, graphics processing unit — computing is key to extreme event prediction. By extracting patterns from experimental data with machine learning algorithms, researchers are using low-overhead probabilistic models to map the evolution of patterns to extreme event identifiers in interpretable ways. Essentially, the input is a flow pattern obtained from operational sensors, and the output is the likelihood of observing an extreme event in the near future.
Contributors: Shivam Barwey, Michael Benjamin, Daniel Jacob, Ellen Mazumdar, Joe Oefelein, Paul Palies, Venkat Raman, Jerry Seitzman, Adam Steinberg and Krishna Venkatesan
Stay Up to Date
Submit your email address to receive the latest industry and Aerospace America news.
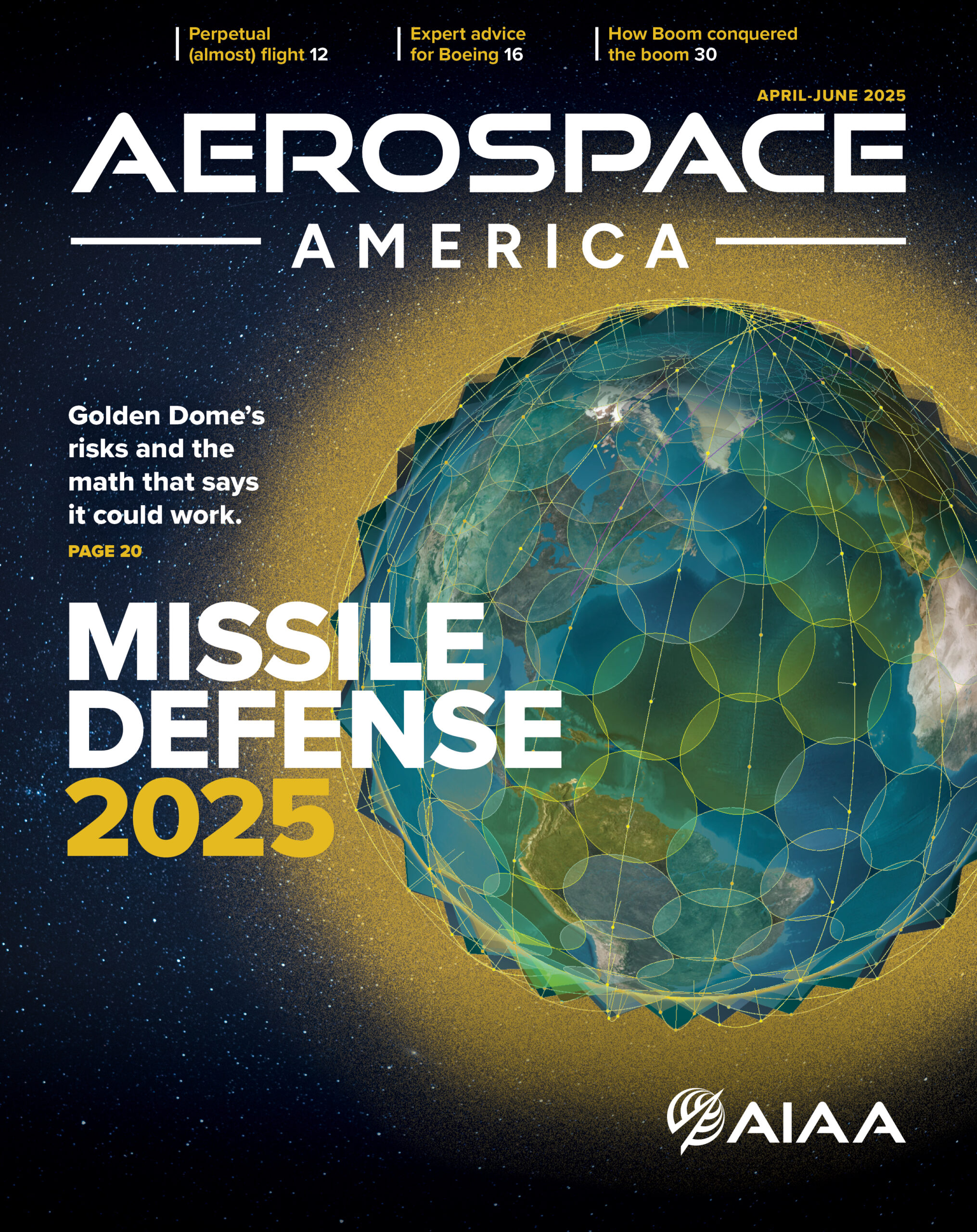