Stay Up to Date
Submit your email address to receive the latest industry and Aerospace America news.
The Structures Technical Committee works on the development and application of theory, experiment and operation in the design of aerospace structures.
The Air Force Institute of Technology in Ohio this year continued research on a lighter-than-air-vehicle that has an internal vacuum. A 1.5-meter-diameter vehicle was designed using graphene and nano composite material. Another AFIT project related to the design of a projectile using additive manufacturing material. The projectile was optimized to create the maximum energy at impact with a target. The specimen was tested and the results were very favorable. Another project related to the investigation of an airfoil undergoing flutter and chaotic behavior, and yet another considered the effect of laser shock penning on the residual stresses surrounding a crack. Work was also done associated with an improved Goodman Diagram for the evaluation of material endurance limits.
Turning to space launch, NASA in May announced completion of a series of structural tests on the Space Launch System upper stage and adapters at Marshall Space Flight Center in Alabama. The initial SLS configuration will have a minimum 70-metric-ton lift capability and be powered by twin solid rocket boosters and four RS-25 engines.
In Europe, researchers this year announced European Commission funding for an effort called PARSIFAL, short for PrandtlPlane Architecture for the Sustainable Improvement of Future Airplanes. It is a joint venture with San Diego State University. This breakthrough innovation project is coordinated by the University of Pisa in Italy and funded under the Horizon2020 Program. Researchers aim to demonstrate how the adoption of a boxed-wing structure, known as a PrandtlPlane, can bring significant improvements for air transportation. Among the challenges of the study is the design of an aircraft that must satisfy the increasing amount of passenger traffic and at the same time drastically reduce noise and emissions while increasing safety and comfort in flight. Researchers plan to demonstrate that the PrandtlPlane configuration is flexible and may be used for both the transport of passengers and cargo in a wide range of missions. Additionally, the project is to develop scaling procedures to look into the possibility of applying the PrandtlPlane configuration to aircraft of different dimensions and payload capabilities, including both regional aircraft and ultra-large aircraft, bigger than an A380, for instance.
DARPA in March awarded Boeing a $146 million contract for its Experimental Spaceplane or XS-1 program. Boeing’s design, called Phantom Express, will have advanced capabilities such as autonomous flight, agile launch and reusable propulsion systems. It could revolutionize the U.S. satellite launch process for both military and commercial programs. With a wing span of 19 meters, Boeing’s Phantom Express would lift off like a rocket, release its payload into orbit and return to the launch site like an airplane. It would enable rapid, on-demand, low-cost access to space. DARPA has approved progression to Phases 2 and 3, which are fabrication and flight. At Phase 3 in 2020, Phantom Express is expected to demonstrate its capability to carry up to 1,360 kilograms into low Earth orbit 10 times in 10 days. Its reusability is projected to lower the current recurring costs by a factor of 10 to as little as $5 million per flight.
Mississippi State University, University of Illinois at Urbana-Champaign and Israel Military Industries worked on a program to develop analytical and experimental protocols for the characterization of viscoelastic materials in real time. Both quasi-static and dynamic experiments are performed. The possible influences of material nonlinearities are also being investigated.
Contributors: Anthony N. Palazotto, Bruce Willis, John Zappay, Luciano Demasi, Zhenning Hu
Stay Up to Date
Submit your email address to receive the latest industry and Aerospace America news.
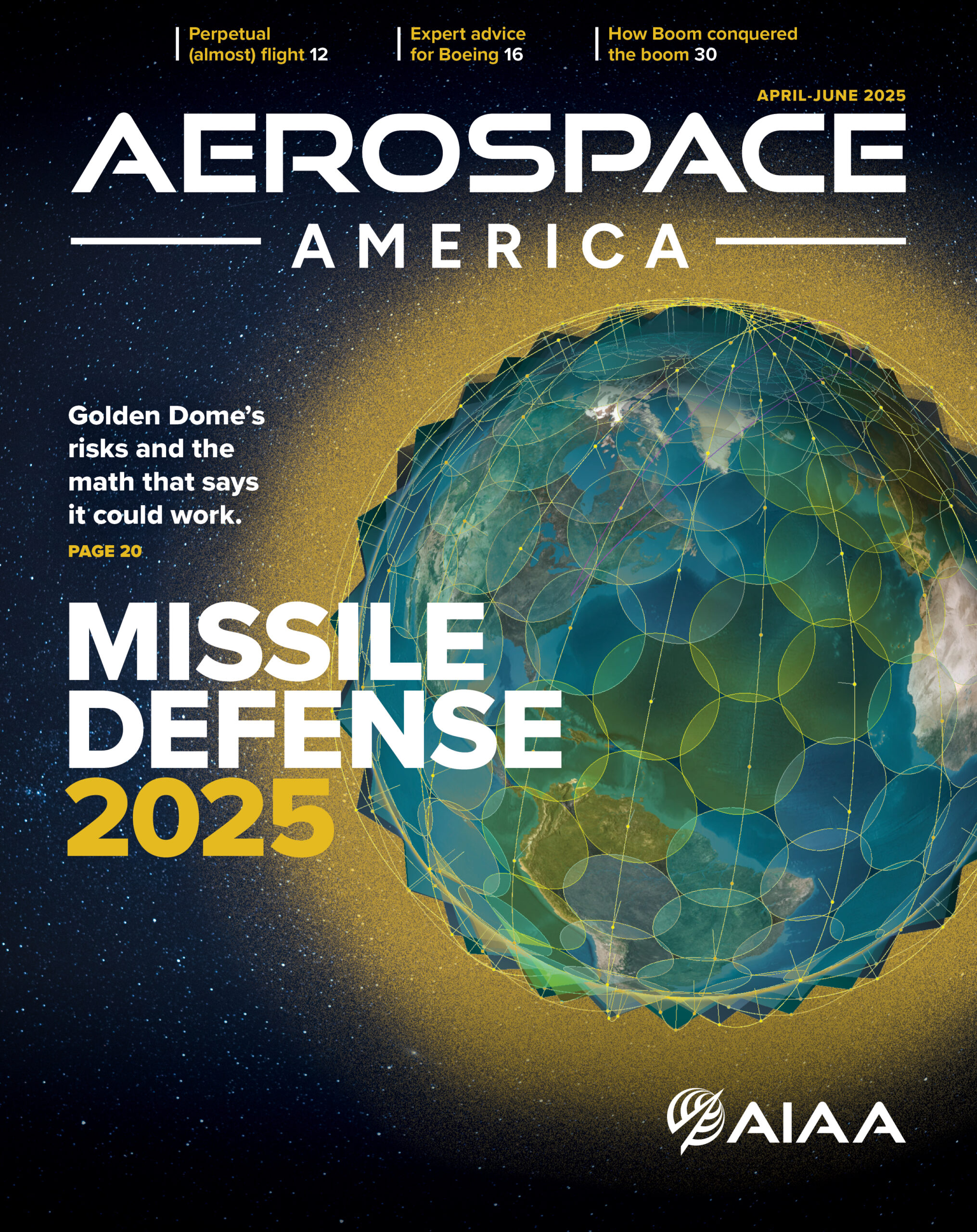