Stay Up to Date
Submit your email address to receive the latest industry and Aerospace America news.
The Non-Deterministic Approaches Technical Committee advances the art, science and cross-cutting technologies required to advance aerospace systems with non-deterministic approaches.
Next-generation aerospace systems aim for greater efficiency and safety. However, the ever-growing complexity of aerospace systems brings increased test costs. Alternatives to traditional, hardware-focused testing are crucial to the cost-effectiveness of developing new technologies for flight. This presents significant challenges due to the presence of uncertainties and increasingly expensive-to-evaluate simulation models.
In January, the AIAA Certification by Analysis Community of Practice chartered an international team of representatives from industry, academia and governmental agencies to establish formal guidelines for applying virtual flight modeling to reduce the burden of flight-testing. Among the areas of focus are model verification and validation methods and uncertainty quantification analysis.
Multifidelity methods that enhance information with cheaper lower-fidelity information sources are key to making design optimization under uncertainty computationally feasible. In January, researchers from the multifidelity, multi-information source, multiphysics, or M3, team led by the Massachusetts Institute of Technology under the U.S. Air Force Multidisciplinary University Research Initiative introduced active learning methods through multifidelity Efficient Global Reliability Analysis. In July, M3 introduced a novel Monte Carlo variance reduction method via the Information Reuse for Importance Sampling in reliability-based design optimization. These new methods enable computationally efficient implementations of robust optimization to ensure safe, efficient designs.
Fleet managers and regulators rely on probabilistic risk analysis to make sure their systems continue to maintain safety throughout their service life. Broader application of these models relies on efficient modeling of material failure. In July, researchers from the University of Illinois at Urbana-Champaign and École Nationale Supérieur de Mécanique et d’Aerotechnique, Poitiers, France, began an analytic study of structural material deterministic and stochastic failure criteria. Their work focuses on reducing the dimensionality of material failure analysis under complex loading.
Following the in-service failure of a commercial jet engine in 2018, the non-deterministic approaches community has been engaged in supporting all sectors of the aviation enterprise as it addresses the unique challenges of engine sustainment. In May, Southwest Research Institute of Texas released a software package to support the probabilistic damage tolerance methodology required by the upcoming FAA Advisory Circular AC33.70-5 for FAA certification risk assessment of axial blade slots in aircraft engine disks containing random manufacturing-induced anomalies. The methodology was implemented in the DARWIN probabilistic damage tolerance software (developed by SwRI). The software was created under the guidance of an industry steering committee composed of major international aircraft gas turbine engine manufacturers. Released to the steering committee for review in May, the software will be available to licensed users in early 2020. In July, as part of a joint contract with the U.S. Air Force Research Laboratory and the Probabilistic Analysis Consortium for Engines, SwRI completed a multiyear project to develop new probabilistic methods and tools for assessing uncertainty in turbine engine component life prediction in the presence of limited data.
Related Posts
Stay Up to Date
Submit your email address to receive the latest industry and Aerospace America news.
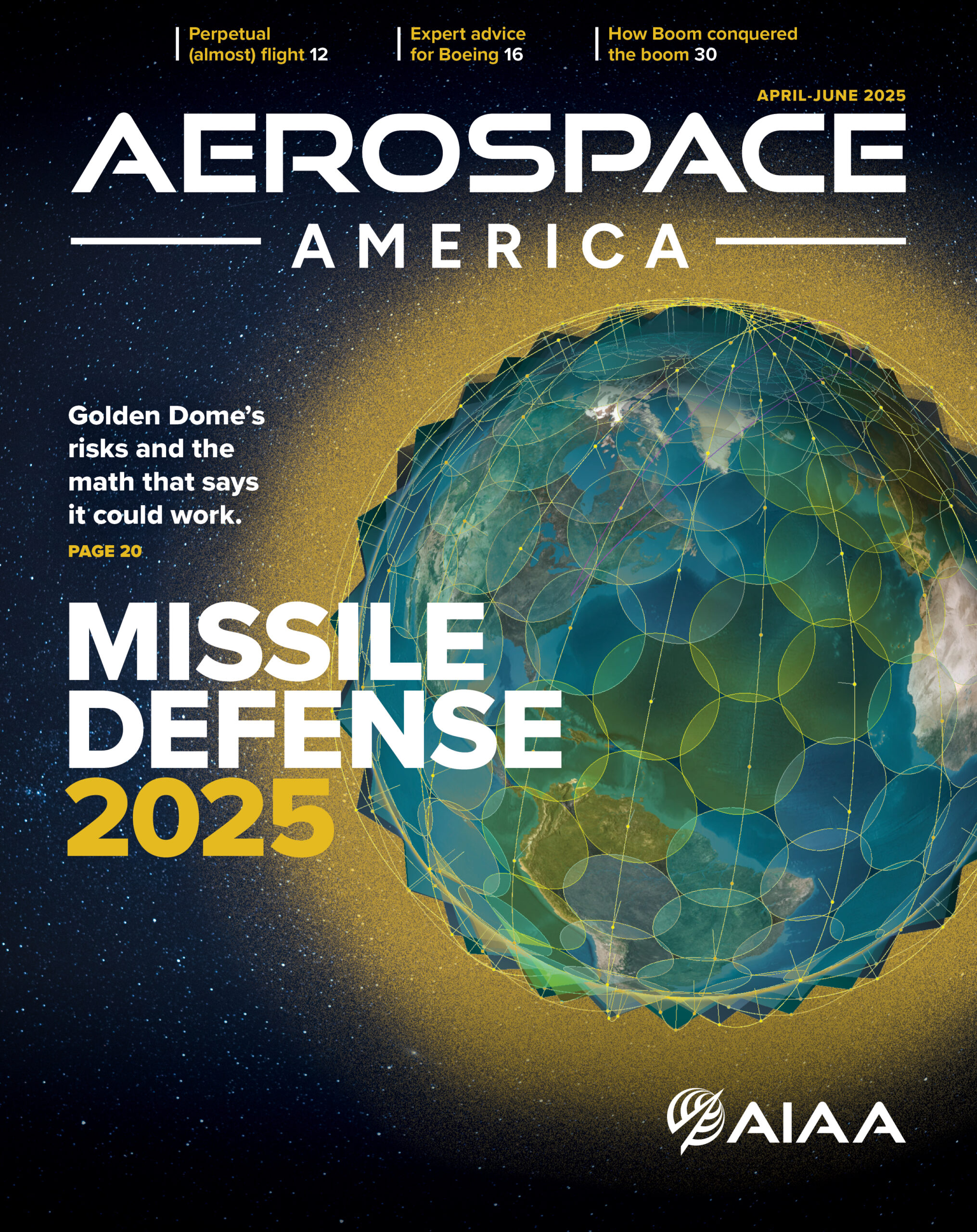