Stay Up to Date
Submit your email address to receive the latest industry and Aerospace America news.
The Inlets, Nozzles and Propulsion Systems Integration Technical Committee focuses on the application of mechanical design, fluid mechanics and thermodynamics to the science and technology of air vehicle propulsion and power systems integration.
The quest for hybrid-electric aircraft continued this year, marked by a few notable initiatives.
In July, Pratt and Whitney and Collins Aerospace announced the inception of the Scalable Turboelectric Powertrain Technology demonstrator program, a testbed for hybrid-electric propulsion concepts for advanced air mobility vehicles, drones and single-aisle commercial aircraft. The companies will develop high-voltage, distributed hybrid-turboelectric propulsion concepts in the 100- to 500-kilowatt class, with the ability to scale to 1 megawatt and above. The demonstrator, comprising a high-efficiency turbogenerator, energy storage, power electronics and modular electrically driven propulsors, enables rapid prototyping and demonstrations of configurations. Having completed proof of concept studies earlier this year, ground testing is planned for late 2022.
Daher announced in May that its hybrid-electric EcoPulse technology demonstrator, developed with Airbus and Safran, will make its first flight by the end of the year. At that point, the demonstrator had been powered up and completed a thermal runaway test. The TBM 900-series-based airframe is powered by a distributed hybrid propulsion system consisting of six wing-mounted 50 kW electric motors and a Pratt and Whitney Canada PT6 turboprop engine. Safran will oversee the integration of the distributed hybrid propulsion system. Airbus is responsible for the aerodynamic and acoustic integration of the distributed propulsion system and development of a high-energy-density 350 kg, 350-kW main battery system. Daher will oversee flight and airworthiness testing and overall test results analysis.
In April, Stuttgart-based fuel cell developer H2FLY flew its hydrogen-electric HY4 test passenger aircraft at an altitude of 7,230 feet, which the company believes to be a world record. The flight occurred the day after H2FLY completed a 124-kilometer cross-country flight between two major airports, another first. In July, the company announced that the HY4, which currently uses gaseous compressed hydrogen-powered fuel cells, will be modified to run on liquid hydrogen, which will double its range capability. Ground testing is scheduled to begin in early 2023 with the new fuel tank.
In February, Airbus introduced its ZEROe demonstrator. The company plans to convert its first A380 ever produced, the MSN1 test aircraft, into a flight laboratory platform to demonstrate and mature hydrogen technologies that will be integrated into hydrogen-powered commercial aircraft that are expected to begin service around 2035. The demonstrator will house four liquid hydrogen storage tanks and a liquid hydrogen distribution system, as well as a hydrogen-combustion engine. This will be a modified GE Passport turbofan mounted on the rear fuselage, developed in collaboration with CFM International, a joint venture between GE and Safran. CFM will adapt the combustor, fuel system and control system of the turbofan to run on hydrogen. The engine was selected due to its physical size, advanced turbomachinery and fuel flow capability.
In August, NASA’s Glenn Research Center in Ohio powered heat pumps with acoustic energy that traveled over a 10-meter-long, twisting acoustic wave-guide tube, refrigerating 100 watts of heat using an input of only 35 watts. This was an early demonstration of a novel thermal energy conversion method to refrigerate an electric powertrain without the use of pumped fluids, while synergistically managing and recycling the low-grade waste heat from electrical components and the high-grade waste heat from engine components. The system will utilize acoustic mechanical energy distribution to elevate waste heat to a higher temperature while simultaneously cooling sensitive electrical components. It will then redistribute and reuse the higher temperature heat throughout the aircraft via solid-state multibranched heat pipes, which can improve the overall fuel efficiency of the aircraft.
Contributors: Dyna Benchergui and Rodger W. Dyson
Stay Up to Date
Submit your email address to receive the latest industry and Aerospace America news.
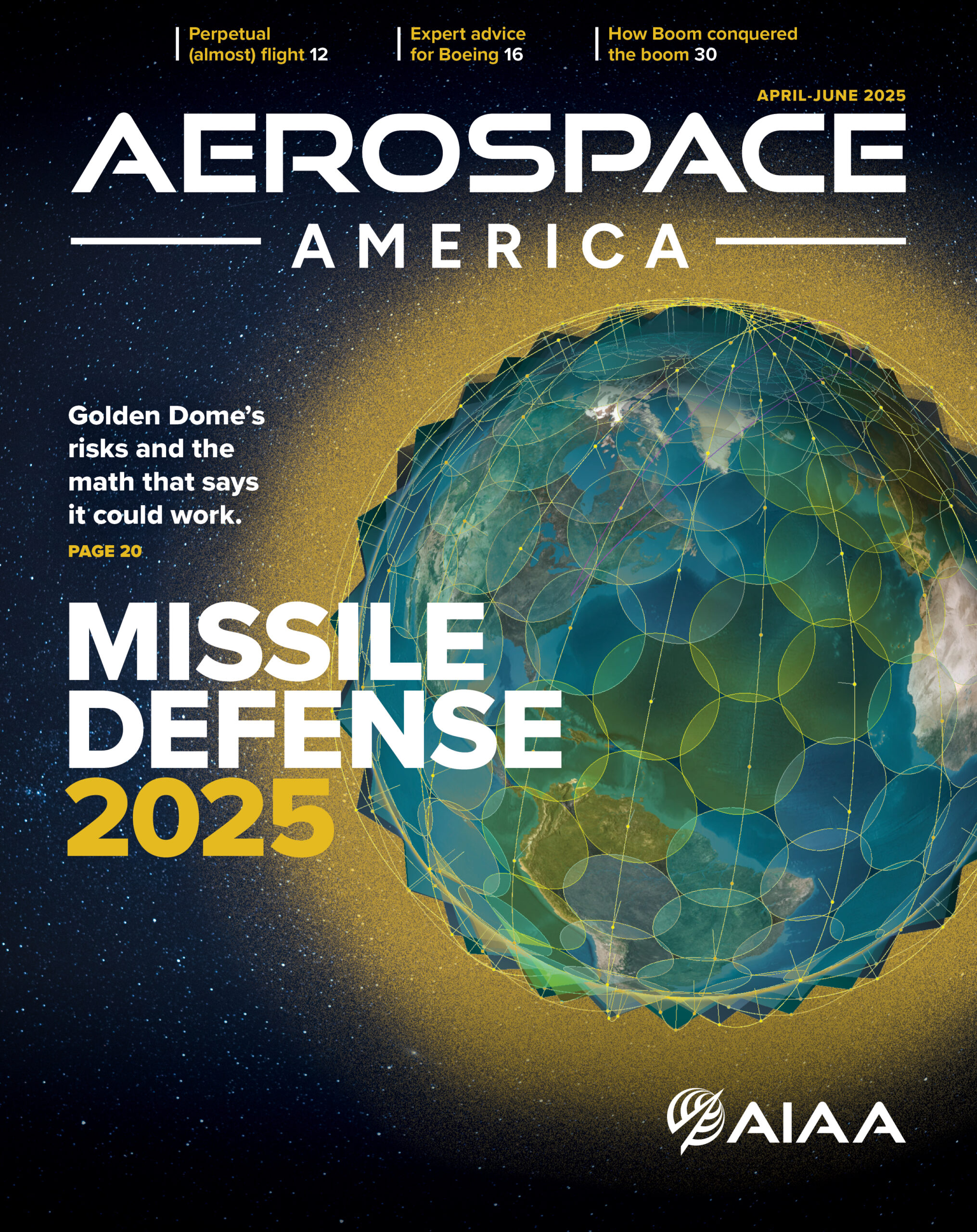