Stay Up to Date
Submit your email address to receive the latest industry and Aerospace America news.
The Gas Turbine Engines Technical Committee works to advance the science and technology of aircraft gas turbine engines and components.
Rolls-Royce gas turbine engine technology has experienced another strong year, manifested in major technology development programs, development testing and certification of numerous engines, and continued investment in research facilities and quality education for future generations of gas turbine engineers.
In June, the U.S. Air Force Life Cycle Management Center awarded Ohio-based GE Aviation and Connecticut-based Pratt & Whitney each a $1 billion contract via the Adaptive Engine Transition Program to mature three-stream adaptive cycle engines. The AETP program seeks to demonstrate a 25 percent fuel-efficiency improvement, 10 percent increase in thrust and significantly improved thermal management. AETP is set to run through 2021 with extensive component, rig and engine testing.
GE Aviation began testing its first full GE9X engine in March at its Peebles, Ohio, testing facility. The test brought together all the GE9X technologies to demonstrate their operability as a complete propulsion system.
The Rolls-Royce Trent 1000 Thrust, Efficiency and New Technology engine took flight in March for the first time on a Boeing 747 test aircraft over Tucson, Arizona. The Trent 1000 TEN will power all Boeing 787 Dreamliner variants. The engine draws on technologies from the Rolls-Royce Trent XWB engine, delivering thrust and efficiency improvements. The Trent 1000 powered the first 787-8 entry into service in 2011 and the first 787-9 in 2014.
Williams International in Michigan was awarded the FAA Part 33 type certificate for its FJ33-5A engine in June. The new engine has more than 900 kilograms of thrust and market- leading fuel economy enabling a greater than 6-to-1 thrust-to-weight ratio, a breakthrough in FAA-certified single-engine jet aircraft. The FJ33-5A has been chosen to power the Cirrus Vision and the Flaris LAR1.
In July, the Leading Edge Aviation Propulsion engine marked its first delivery on the Airbus A320neo to Turkey’s Pegasus Airlines. The engine is the newest from Ohio-based CFM International, a joint venture between GE Aviation and Safran Aircraft Engines. Additionally, the LEAP engine for the Boeing 737 MAX aircraft was certified in May with first delivery of the new aircraft scheduled for next year.
Facility upgrades at Penn State’s Mechanical and Nuclear Engineering Department enabled the Steady Thermal Aero Research Turbine lab to complete its first test campaign from February through May. The facility upgrades included mass flow rate and temperature increases as well as additional instrumentation. Testing focused on sealing methods between turbine stages and interactions between the main gas path flow and cooling airflow. Results will be used to develop new predictive models for turbine designers, leading to increased component durability and higher engine efficiency.
The Gas Turbine Engines Technical Committee concluded another successful year of the Undergraduate Team Engine Design Competition at the AIAA Propulsion and Energy Forum in July. The goal was to design a replacement for the J-85 engine as a power plant for a new generation of trainer aircraft. The mission profile included a supersonic dash up to Mach 1.3 as well as cruise at Mach 0.85. Additional requirements focused on life, engine size, fuel efficiency and a low turbine inlet temperature. Teams around the globe submitted a record 13 reports. Based on the written reports, the top three teams were invited to participate in an oral presentation at the Propulsion and Energy Forum in Salt Lake City. The finalists represented the University of Cincinnati, Istanbul Technical University and the University of Kansas, with the top honors going to Kansas. ★
Contributors: Daniel Jensen, John Sordyl, Jay Neal, Magdy Attia and Jimmy Tai
Stay Up to Date
Submit your email address to receive the latest industry and Aerospace America news.
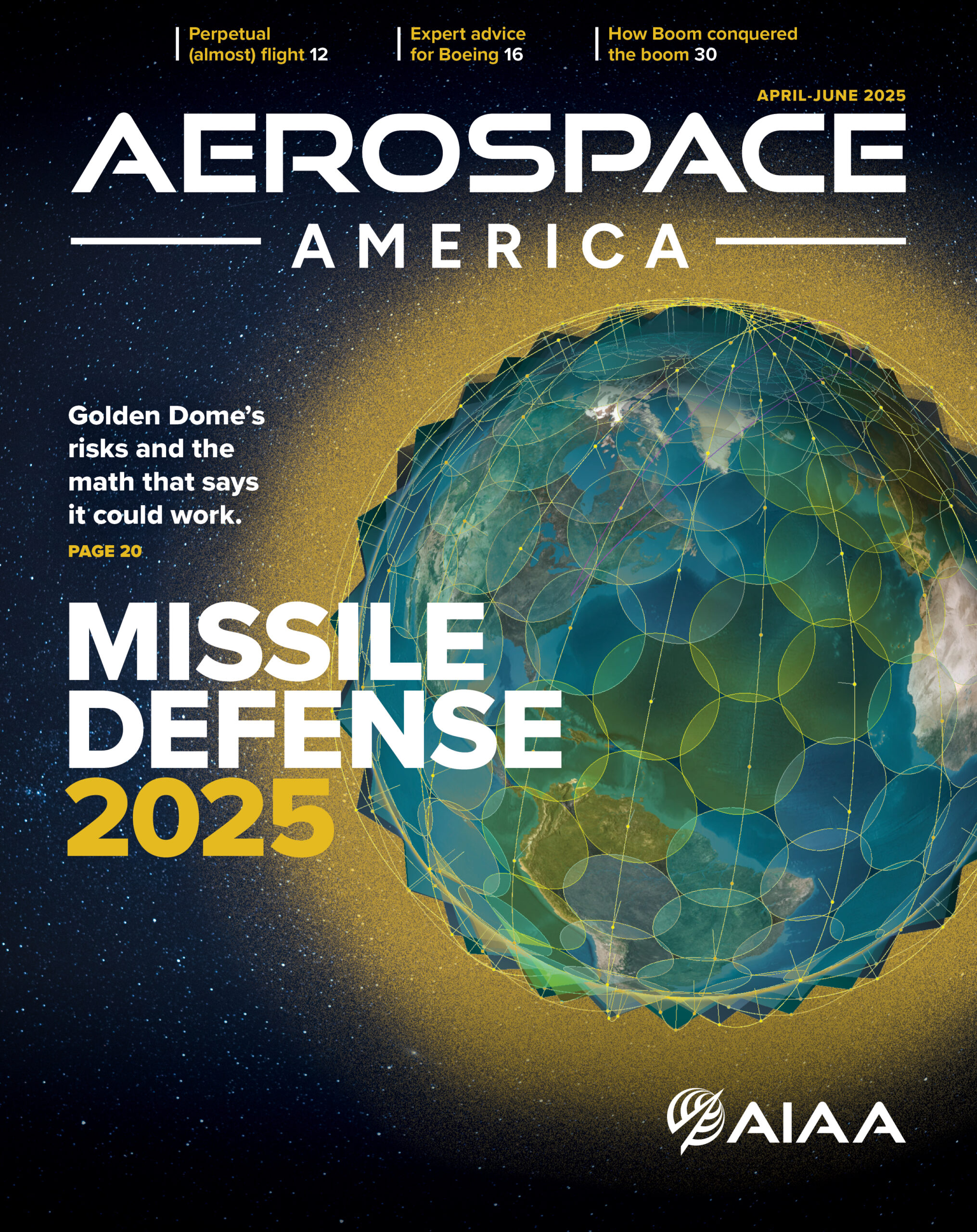