Stay Up to Date
Submit your email address to receive the latest industry and Aerospace America news.
The work of the Adaptive Structures Technical Committee enables aircraft and spacecraft to adapt to changing environmental conditions and mission objectives.
The Institute of Composite Structures and Adaptive Systems of the German Aerospace Center, DLR, in July completed fabrication of a morphing wing trailing-edge demonstrator for fluid-actuated morphing. The wing has metal-reinforced elastomeric hydraulic chambers that deflect under fluid pressurization. The 1-meter span demonstrator was manufactured by TU Braunschweig under the European Union’s Clean Sky 2 program and consists of fiber-optic shape sensors for closed-loop control, supplied by PhotonFirst. DLR plans to complete testing by mid-2023.
Researchers at the Delft University of Technology also fabricated a smart wing section in the quest for ultra-lightweight structures and sustainable aviation. In April and August, they conducted wind tunnel tests of the section, which comprises a control surface and spoiler to test active aeroelastic control, including physics-based and data-driven nonlinear algorithms.
In supersonic applications, in September NASA’s University Leadership Initiative team led by Texas A&M demonstrated its first multisegment morphing panel. Formed from 15 aluminum plates driven by shape memory alloy torque tubes, the panel deformed into optimal “bump” and “dent” configurations to reduce a sonic boom’s strength, a key requirement for quiet supersonic flight.
Speeding to the hypersonic regime, researchers at the University of Kansas in June and July conducted shock, wind tunnel and range testing of adaptive flight control actuators for 20-millimeter guided hypersonic aerial gunnery ammunition.
The U.S. Army Research Laboratory developed and tested a tip-strike mitigation system for small, fixed-wing unoccupied aerial vehicles. The passive method combines a buckling member to resist sweep in normal flight and linear springs to restore wing position after impact. Wind tunnel testing demonstrated that the system significantly reduces the impact loading on drones and that aerodynamic loading further damps the detrimental moments associated with tip strike.
In July, researchers at the University of Central Florida uncovered the mechanisms behind unique nonlinear stiffness and damping behavior in a biomimetic fish-scale structure. Inspired by swimming fish, the researchers leveraged intricate scale sliding motion to program critical mechanical properties, which could lead to lightweight structures that minimize aerodynamic drag.
Birds in flight were the inspiration for new stretchable piezoelectric polymers. In May, researchers at the University of Michigan used technology based on precipitation printing to manufacture anatomically correct prosthetic feathers. Looking ahead, the feathers will enable in-flight aerodynamics sensing.
Also in May, researchers at Concordia University fabricated and controlled a magnetoactive soft continuum robot for minimally invasive therapies. The team developed a novel 4D printing technique to fabricate the robot and create complex geometries with various magnetic patterns. The tests confirmed the robot’s dynamic response matches their computationally efficient model, enabling the accurate planning needed for sensitive biomedical applications.
A team from AlphaSTAR and the University of Maryland developed a diagnostic-prognostic active structural health monitoring system fusing sensors and software for the U.S. Navy. The system combines real-time damage measurements with damage evolution models to predict remaining life of critical welded structures.
In July, researchers from Arizona State University validated a physics-based machine learning framework for a cruising aircraft under high-altitude stall. The framework predicted a 3D risk region of the aircraft state and designed an optimum recovery trajectory.
In January, a team from Boeing, Paragon Space Development Corp. and Texas A&M University demonstrated with NASA engineers a five-panel shape memory alloy-based morphing radiator. The composite radiator panels responded to changing thermal loads by autonomously opening and closing in a thermal vacuum test at NASA’s Johnson Space Center in Texas.
In January, the China National Space Administration’s Lunar Exploration and Space Engineering Center released photos from the Tianwen-1 Mars orbiter taken by a camera using shape memory polymer composites from the Harbin Institute of Technology. The camera deployed in November 2021 after Tianwen-1 reached its Mars remote-sensing orbit. After taking the deep space selfies, the composites folded back, stowing the camera.
Stay Up to Date
Submit your email address to receive the latest industry and Aerospace America news.
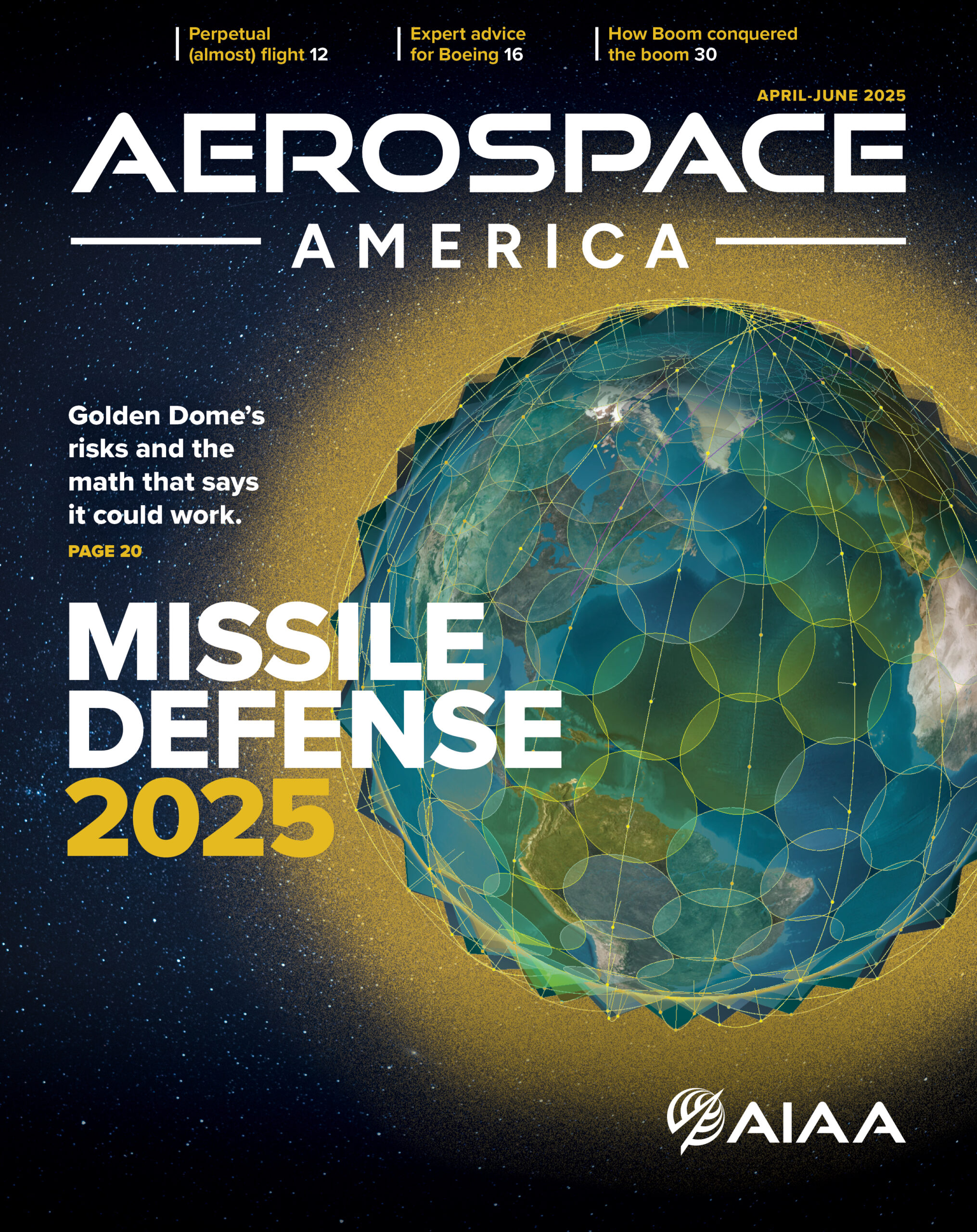