Stay Up to Date
Submit your email address to receive the latest industry and Aerospace America news.
The Structures Technical Committee works on the development and application of theory, experiment and operation in the design of aerospace structures.
In March, an ultra-lightweight and low-power sensor developed by MIT, Metis Design Corp. and Analog Devices in Massachusetts was installed on a U.S. Navy destroyer. Comprised of polymer nanocomposites, the 10-gram sensor was designed for structural health monitoring. In August, one of the 25-millimeter-long sensors was installed on a U.S. Air Force F-15. The Air Force evaluated the sensor’s sensitivity to detecting cracks in airframes and found there was a 90% probability that the design would detect cracks less than 0.5 mm. An FAA evaluation of the design for commercial aircraft yielded similar results. Plans call for Analog Devices to develop a smaller version that would weigh about 1 gram and be 12.5 mm long.
In June, researchers at Oklahoma State University developed a nonconformal mesh modeling approach to determine the curved beam design that would maximize the critical buckling load for aircraft wing panels. The model simulated increasing amounts of material deposited along the base structures of curved stiffening members. The researchers identified an 87% increase in the buckling load with no weight penalty compared to designs using traditional straight stiffeners and uniform plates.
In January, NASA selected Boeing to build a full-sized transonic truss-braced wing demonstrator, which in June was designated the X-66A. Driven by the target of achieving net-zero carbon emissions by 2050, NASA is conducting the Sustainable Flight Demonstrator project to develop technologies for next-generation single-aisle aircraft designs, in collaboration with academia and industry. Boeing estimates the truss configuration could reduce fuel consumption up to 30% compared to today’s passenger aircraft, when paired with advanced engines. In August, Boeing delivered an MD-90 airframe to its facility in Palmdale, California, where the company will modify the airframe into a truss-braced wing.
In a project funded by the U.S. Air Force Research Laboratory, Mississippi State University’s Aerospace Engineering Department developed a composite landing gear strut door with a stitched sandwich polymer matrix. The composite door is 50% lighter than its titanium counterpart and stitches through the foam layers with optimized parameters, reducing the likelihood of delamination damage, in which interior cracks cause the composite layers to separate.
Using the Abaqus software, University of Michigan researchers developed a high-fidelity framework to model composite materials. The enhanced semi-discrete damage model tool set consists of a meshing strategy with failure mode separation, a version of the enhanced Schapery theory and a probabilistic modeling strategy. To validate the model, multiple laminates were simulated under a quasi-static tensile load condition. For the given loading conditions, the model captured complex damage progressions and predicted failure loads with reasonable accuracy. With this framework, researchers can conduct simulations via the Monte Carlo probability method to represent different virtual specimens. A team is also developing an Abaqus plugin to simulate the curing process to quantify residual stresses and how materials deform after manufacturing.
In March, University of Michigan researchers tested a 3D-printed mock-up of a solar array in a vacuum chamber. The tests were funded by DARPA under its Novel Orbital Moon Manufacturing, Materials, and Mass-Efficient Design program, in which researchers are studying innovative structures that are additively manufactured, assembled and serviced in space to enable the design of very large structures — about 100 meters — that are between 1 and 5 mm thick. Under the grant, the researchers designed a 66-meter hexagonal array with a truss meant to increase structural damping with only minimal loss in structural stiffness and a creased, thin elastic facing sheet that increases the structure’s fundamental frequency without substantially increasing the mass. In the vacuum tests, the vibrations of the 1.3-meter-wide mockup matched the fundamental frequencies predicted by numerical models.
Stay Up to Date
Submit your email address to receive the latest industry and Aerospace America news.
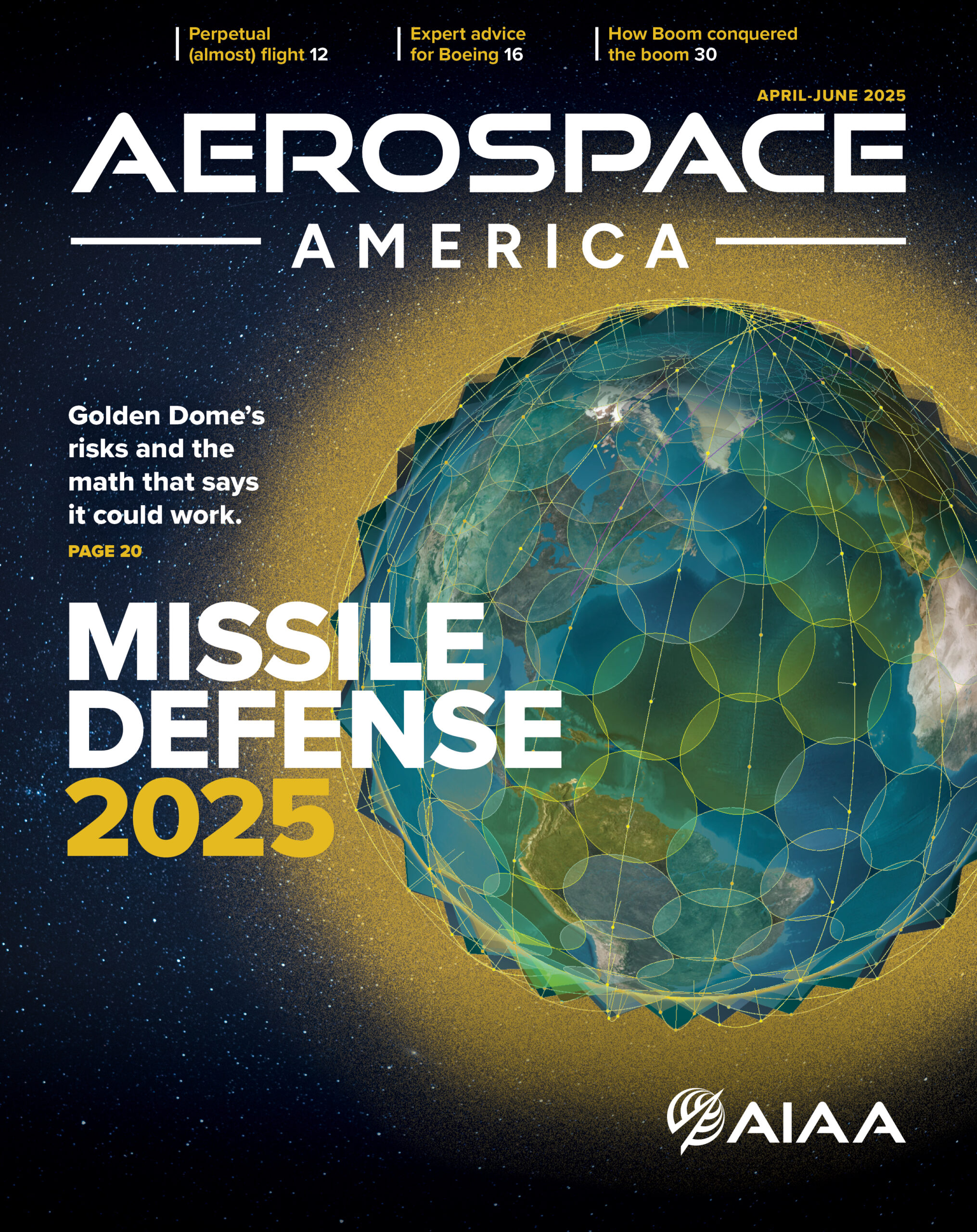