Stay Up to Date
Submit your email address to receive the latest industry and Aerospace America news.
The Survivability Technical Committee promotes air and spacecraft survivability as a design discipline that includes such factors as crashworthiness and repairability.
The U.S. Army is developing a durable lightweight composite sandwich core structure to mitigate the effects of blasts internal to an enclosed helicopter fuselage. Two full-scale subcomponent test articles were subjected to blast and ballistic fragmentation from a high-explosive incendiary round. Residual strength testing of the damaged components was then conducted to demonstrate that sufficient strength remained to carry loads corresponding to level flight. The components did carry these loads, as well as increased maneuvering loading. Simulation models previously improved with building block test data were critical in designing this structure to tolerate damage while providing adequate residual strength.
Wright-Patterson Air Force Base in Ohio completed the 10th and final live-fire test and evaluation series for Boeing’s KC-46 Fuel Tanker. Included was a long-term burn test (over 30 minutes) with airflow to assess cascading structural damage. The results were transitioned into Boeing’s Systems Integration Laboratory for pilot-in-the-loop developments for KC-46 training, tactics, operations and procedures.
Air Force officials at Wright-Patterson are collaborating with the Army and Navy to assess thermo-mechanical failure effects on aircraft composite materials. The goals are to determine composite material loss of strength from fire and lasers, generate time-dependent damage data, and quantify the fire-resistance of selected thermal barriers. The results will be applied to aircraft vulnerability assessments and to protective system designs.
Wright-Patterson, along with the other military branches and industry organizations, is also assessing unmanned air vehicle vulnerabilities to high energy lasers. Tests include quantifying penetration times and thermal effects, investigating the potential for fuel fires, examining power and signal loss in wire bundles, assessing control box and actuator dysfunctions, and assessing hardening concepts for delays in damage onset of effects. Data obtained will be used to support laser effects modeling.
The Air Force base also completed an F-35B fuel tank ullage test that enabled the aircraft’s program office to meet its critical initial operational capability milestone. The test addressed critical fuel tank vulnerability issues affecting flight operations. The results enabled the F-35 program to prevent suspension of a critical halt of F-35B fleetwide low-rate initial production regarding fuel tank modifications, which led to cost savings. Test data allowed lifting a 10-nautical mile Lightning flight restriction that resulted in direct benefit to training, operation, tactics and procedures.
For pilot survivability in the three versions of the new F-35 fighter, Lockheed Martin has chosen the British company Martin-Baker over a rival competitor, United Technologies Aerospace System, to provide an upgraded version of its current US16E pilot ejection seat. Three nitrogen-filled bags around the pilot’s head are instantly inflated to protect the head and prevent neck whiplash, among other improvements.
For space systems, the heat shield of the Orion re-entry module and capsule for the mission to Mars is being redesigned to withstand 4,500 degrees Fahrenheit instead of 4,000. NASA contractor Lockheed Martin and its partner Textron are reconfiguring the shield’s Avcoat epoxy resin material in a different design to avoid a shield cracking problem during re-entry into Earth atmosphere. In addition, to protect the crew against solar radiation near Mars, the contractor is collaborating with StemRad of Israel in developing a crew vest to be worn over the space suit inside the Orion when radiation is above an acceptable level, and also in spacewalks if outside repairs to the Orion are needed. ★
Stay Up to Date
Submit your email address to receive the latest industry and Aerospace America news.
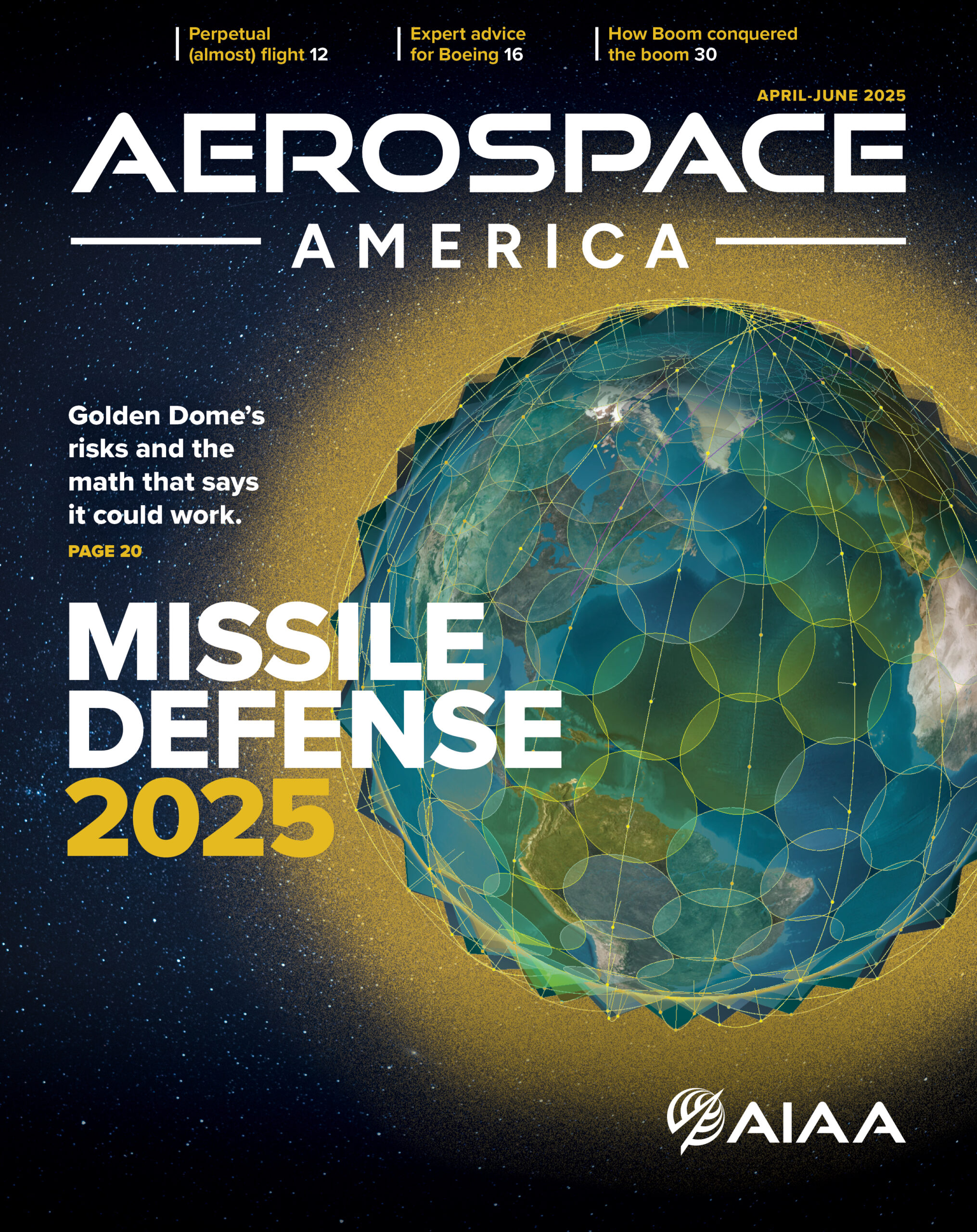