Stay Up to Date
Submit your email address to receive the latest industry and Aerospace America news.
The Liquid Propulsion Technical Committee works to advance reaction propulsion engines employing liquid or gaseous propellants.
Rocket reusability came into sharp focus this year with SpaceX and Blue Origin making significant strides. California-based SpaceX launched a series of communications satellites with its Falcon 9 rocket and landed its booster stage. In April, after launching a resupply mission to the International Space Station, it landed its booster stage on a drone ship at sea. Similarly, Washington- based Blue Origin demonstrated reuse of its liquid hydrogen/liquid oxygen BE-3 engine with four suborbital flights of its New Shepard rocket. The upper-stage variant, BE-3U, saw significant development, including the design of an extendable nozzle as part of the U.S. Air Force’s Rocket Propulsion System program. Blue Origin’s liquefied-natural gas/liquid oxygen BE-4 engine slated for Colorado-based United Launch Alliance’s Vulcan launch system is undergoing risk reduction and powerpack testing at Blue Origin’s West Texas site. As part of NASA’s Commercial Crew Program, the landing system on SpaceX’s Dragon 2 spacecraft underwent testing in McGregor, Texas, at the end of 2015. These tests included reduced-thrust firing of the Dragon’s eight SuperDraco engines for a five-second hover test.
NASA conducted tests on Aerojet Rocketdyne’s RS-25 engine, four of which will comprise the core stage of the Space Launch System. Building on the first SLS flight slated for 2018, which will use Aerojet Rocketdyne’s RL10-B2 engine for the interim upper stage, NASA selected the RL10-C3 engines to power the exploration upper stage for the second and third SLS flights. In June, NASA and the European Space Agency conducted a critical design review for Orion’s European-built service module that will propel Orion in deep space. The review culminates a series of reviews for three human exploration systems development programs that will enable the journey to Mars. The propulsion system of the module comprises three different types of engines and thrusters, including an orbital maneuvering system engine of space shuttle heritage that is undergoing acceptance and qualification tests.
Orbital ATK in Virginia revamped its Antares rocket, replacing the AJ-26 engines with RD-181 engines. The re-engineered rocket completed a 30-second hotfire test on the launch pad in May at Wallops Island in Virginia and in October resumed cargo launches to the ISS with its Cygnus cargo spacecraft.
In Europe, Airbus Safran Launchers continued development on Vulcain 2.1 and upper-stage Vinci propulsion systems for the Ariane 6 launcher. Between December 2015 and October this year, ASL carried out hotfire tests of its reusable 400-kilonewton LOX/Methane thrust chamber demonstrator at the German Aerospace Center, or DLR, in Lampoldshausen, proving combustion performance and re-ignition. The construction of a facility to test the upper stage of the Ariane 6 launcher at DLR-Lampoldshausen was initiated in June.
NASA’s Green Propellant Infusion Mission involving Ball Aerospace of Colorado, the Air Force and Aerojet Rocketdyne took another step toward demonstrating the capabilities of a safer and more efficient propellant. In March, NASA announced that the mission’s spacecraft passed a major flight-readiness milestone when it completed functional and environmental testing of its systems. In other green propellant work, Aerojet Rocketdyne is partnering with NASA’s Glenn Research Center in Ohio and Goddard Space Flight Center in Maryland to revise a design for a 1-newton thruster; Massachusetts-based Busek, Glenn and NASA’s Marshall Space Flight Center in Alabama are partnering to mature the Busek 5-newton green monopropellant thruster; Orbital ATK is partnering with Marshall and Plasma Processes LLC in Alabama to test an LMP-103S propellant-based 445-newton thruster.
The Satellite Servicing Capabilities Office made significant advances for NASA’s Restore-L robotic spacecraft in maturing fluid transfer system technology equipped to extend the lifespan of satellites in orbit. Developments this year include testing the transfer of simulant propellants at flight conditions and developing a propellant transfer subsystem that allows the robotic servicer to transfer propellant to the client propulsion system. ★
Stay Up to Date
Submit your email address to receive the latest industry and Aerospace America news.
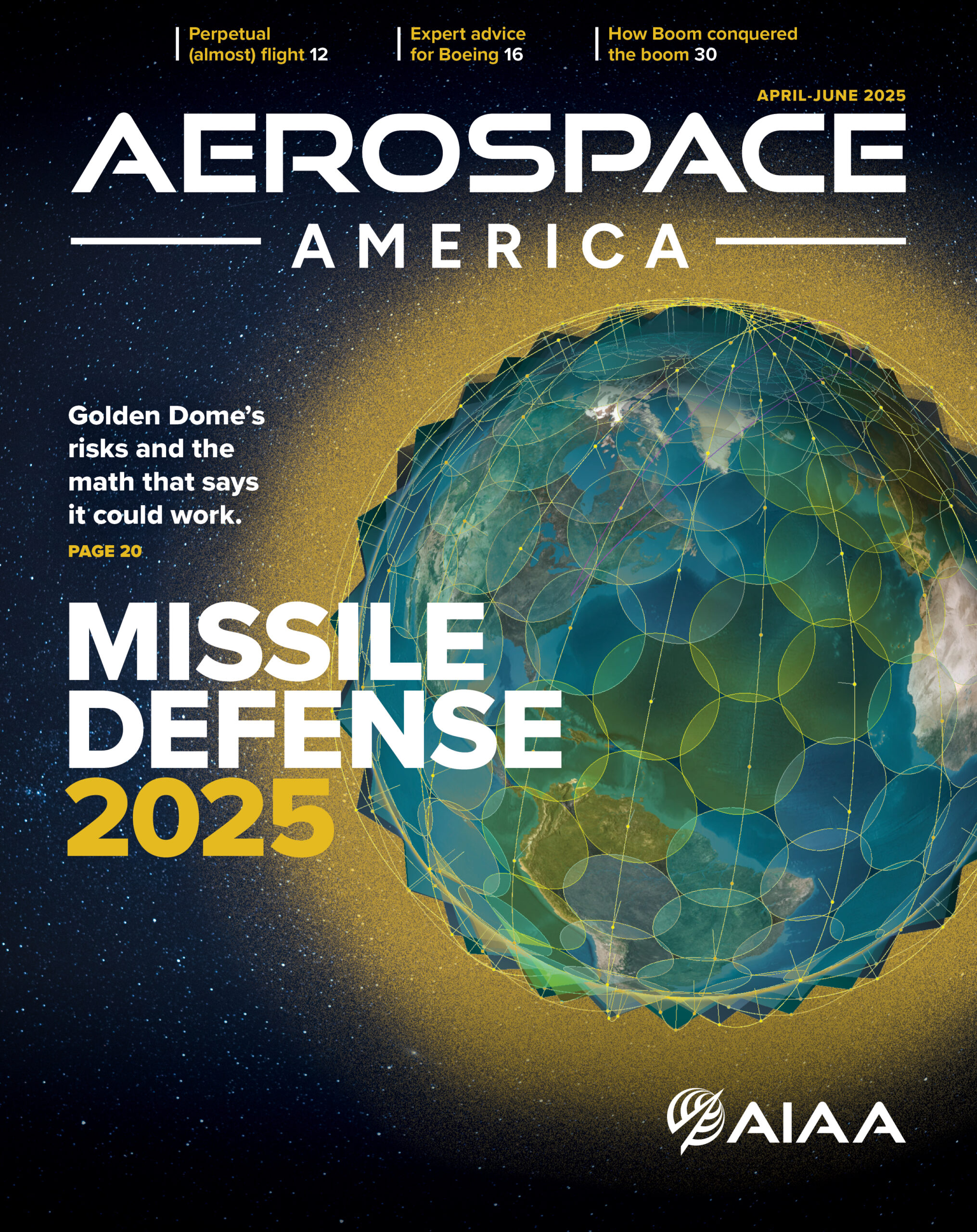