Stay Up to Date
Submit your email address to receive the latest industry and Aerospace America news.
The Inlets, Nozzles and Propulsion Systems Integration Technical Committee (formerly Air-Breathing Propulsion Systems Integration) focuses on the application of mechanical design, fluid mechanics and thermodynamics to the science and technology of air vehicle propulsion and power systems integration.
Boundary layer ingestion received renewed attention this year as a potential way to significantly reduce drag and increase fuel efficiency of future commercial aircraft.
A major step forward came with the analysis throughout the year of the tests of a first-of-kind boundary layer ingesting inlet and distortion tolerant fan stage completed in December 2016 in the transonic test section of the 8-by-6-foot supersonic wind tunnel at NASA’s Glenn Research Center in Ohio. The tests were designed to measure the performance and operability of a BLI inlet and fan embedded in the upper surface of a blended wing body aircraft.
The United Technologies Research Center designed the propulsor with input from NASA and Virginia Tech as part of a broader joint research effort led by NASA. The BLI inlet-fan system ingests the lower-velocity airflow over the aircraft’s surface into the engine, enabling it to generate the required thrust with less power input. This results in significantly less fuel being burned to accomplish a given aircraft mission. A key challenge in designing a propulsor of this type is the highly non-uniform flow into the inlet and the structural impact on the rotating fan as its blades move through regions of distorted flow.
To experimentally evaluate the embedded BLI propulsor, an aircraft flow field simulator was designed and constructed between October 2011 and February 2016. The 8-by-6-foot tunnel is the only test facility in the world capable of evaluating embedded BLI propulsors with proper control of the incoming inlet flow. The BLI propulsor was operated from November to December 2016 for a total of 104 hours and produced a large dataset that was analyzed in 2017, including aerodynamic performance, aeromechanical response and many other measurements.
The propulsor exhibited good operating characteristics across the extent of its operating map. Through this effort to address the key challenges to BLI propulsion — integrated inlet-fan design, airflow distortion and aeromechanics including high-cycle fatigue — the door has been opened to further exploration of boundary layer ingesting propulsors for highly efficient subsonic commercial aircraft.
Also in propulsion systems integration, Rolls-Royce hit its seventh year of partnership with the University of Virginia to improve the performance of engine air particle separators, or EAPS, for gas turbine engines operating in austere environments. As presented at the 2017 AIAA Propulsion and Energy Forum in July, an EAPS flow path designed under this partnership completed coarse dust testing. The new flow path allowed unprecedented reductions in system power consumption combined with increased particle removal fraction. Flow visualization and particle image velocimetry revealed complex vortical separation structures related to the combination of flow split and adverse pressure gradient separation.
The EAPS uses minimal engine power to filter out particles that could otherwise damage engine components. This allows aircraft landings at deserts, beaches or anywhere with potential brownout conditions. The flow path is designed with an inner surface shaped so that larger particles will bounce into an outer scavenge region and an outer surface shaped so that smaller particles will be centrifuged to the scavenge region via flow turning.
The partnership added significant computation resources to the project in 2017 to support the experimental efforts. The Rolls-Royce and University of Virginia research team will continue to use bifurcated wind tunnel testing to study particle trajectories in a prototypical flow field that captures the highly unsteady and separated flow field features.
Contributors: David Arend, Bill Cousins and Eric Loth
Related Posts
Stay Up to Date
Submit your email address to receive the latest industry and Aerospace America news.
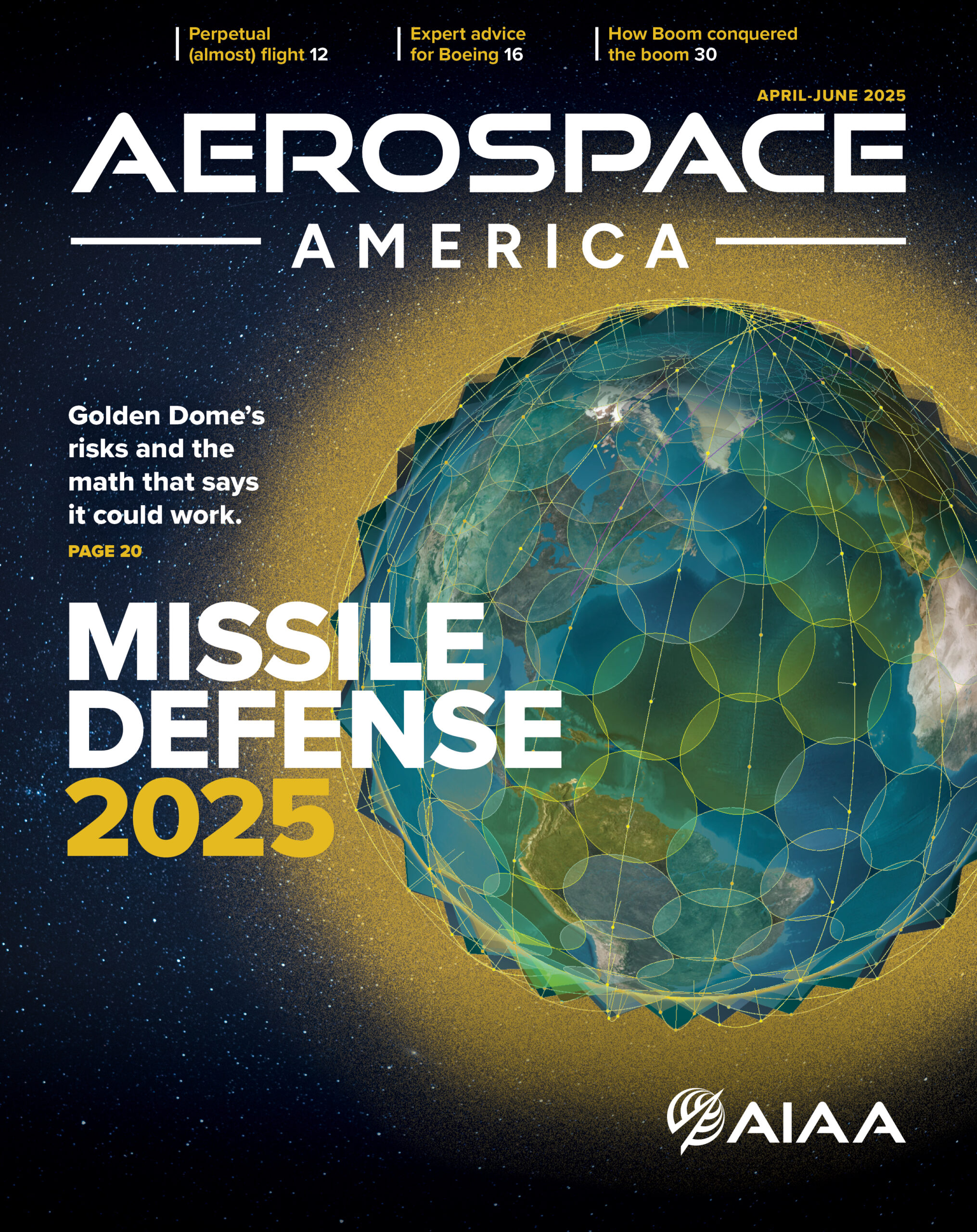