Stay Up to Date
Submit your email address to receive the latest industry and Aerospace America news.
The Structures Technical Committee works on the development and application of theory, experiment and operation in the design of aerospace structures.
The Air Force Institute of Technology in 2016 conducted experimental research to determine the optimum topology of hard-target penetrating warheads. By removing some of the warhead’s exterior case mass and replacing it with an optimized current material interior support structure, a design is achievable that has comparable stiffness and increased lethality. The potential for designing warheads tailored to their intended targets was demonstrated, which are additively manufactured by operational military forces. Finite element methods, dimensional analysis, design of experiments, response surface methodology feasibility studies, and design of a vacuum lighter than air vehicle will be used.
Massachusetts Institute of Technology researchers have demonstrated improved composite properties via nanocomposites and hierarchical advanced composite nanoengineering. New Archimedean scrolled fibers of graphene and polymer were created. Large increases in in-plane strength derived from the reinforced interfaces have been realized.
The main applications of remotely piloted aircraft systems, or RPAS, are photo and video production, agriculture, maintenance services, security and law enforcement. Advantages of light (less than 25 kilograms) and very light (less than 4 kg) multicopter drones are low cost and high safety levels for activities performed in visual line of sight; whereas fixed-wing RPAS are mainly used for 10-100 kilometer ranges and greater than one-hour endurances. A promising aerodynamic concept is the high-efficiency PrandtlPlane configuration developed by SkyBox Engineering of Italy and is not limited to drones.
NASA’s Marshall Space Flight Center in Alabama completed the first series of high-tech composite tests. A composite cylindrical barrel was tested to failure under compressive loads of 900,000 pounds to achieve lighter, stronger primary future structures. Forces were increasingly applied to the composite barrel top to evaluate structural integrity. Predicted failure loads were within 1 percent of actual ones. Tests were performed on the 8-foot-diameter, 8.4-foot-tall graphite-epoxy, honeycomb-core sandwich composite barrel outfitted with 300 individual sensors and approximately 16,000 fiber optic sensors to evaluate the barrel’s structural integrity.
Tests have been conducted at NASA’s Langley Research Center in Virginia on stitched, low-weight, high-strength Pultruded Rod Stitched Efficient Unitized Structure, or PRSEUS, composites developed by Boeing’s Blended Body Group at Huntington Beach, California. The multibay box represents a center section wing part and is made of a low-weight, damage-tolerant stitched composite. The PRSEUS concept significantly improves structural efficiency and lowers manufacturing costs of composite primary structures for large transport aircraft.
Researchers at the AIMS Center at Arizona State University are investigating the multi-axial fatigue behavior of aerospace grade alloys under diverse loading conditions. The goal is to understand the effects of complex loading on microstructural deformation, crack growth behavior and fatigue life. Severely retarded crack growth was observed immediately after overload occurrences and the retardation was found to be directly proportional to the magnitude of the overload. Overloads of higher magnitudes cause increased crack closure due to larger plastic zones around crack tips. The research is supported by technical data analysis.
Gulfstream Aerospace has completed load testing for its G500 aircraft for FAA and European Aviation Safety Agency certifications. Bending and torsion tests focused on the fuselage, wing, vertical and horizontal stabilizers and control surfaces and contained more than 6,000 channels of instrumentation to gain real-time insight into structural behavior. Additional tests will be conducted to determine structural destruction points.
NASA’s Johnson Space Center and Bigelow Aerospace engineers worked to launch, attach and deploy the first human-rated, inflatable spacecraft module. The Bigelow Expandable Activities Module, or BEAM, was launched and expanded for a two-year durability. Crews will enter the module periodically to retrieve recorded data. The module will further the understanding of material susceptibility to creep in both the BEAM bladder and the restraint layer. ★
Stay Up to Date
Submit your email address to receive the latest industry and Aerospace America news.
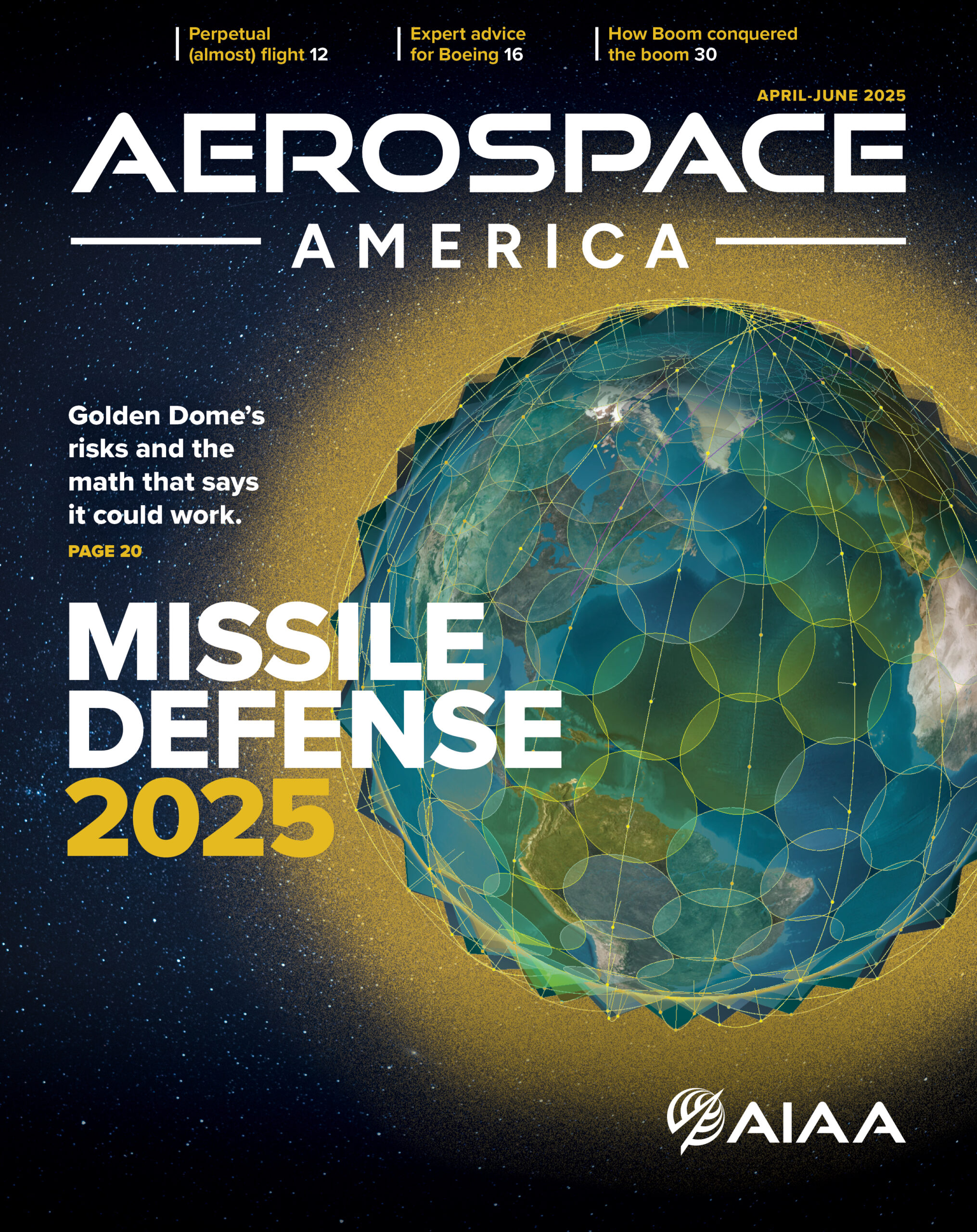