Stay Up to Date
Submit your email address to receive the latest industry and Aerospace America news.
The Energetic Components and Systems Technical Committee provides a forum for the dissemination of information about propellant and explosive-based systems for applications ranging from aircraft to space vehicles.
The PacSci EMC satellite arrived in orbit in June, carrying the Smart Telemetry and Release System, or STARS, consisting of electronic controller cards, firmware and a communications interface. STARS precisely sequenced the firing of four pyrotechnic devices and four solid propellant rocket motors, called the Modular Architecture Propulsion System or MAPS. The motors were fired in pairs by STARS as commanded from a ground station in Irvine, California. PacSciSat’s velocity and altitude were changed by the significant and precise amounts predicted.
Together, STARS and MAPS occupied one 10-centimeter cube of the three-unit PacSciSat cubesat. The remaining units were dedicated to hardware for power, communications, and guidance, navigation and control.
Today’s cubesats typically lack propulsion. PacSci EMC, of Arizona and California, which developed the technologies on the PacSciSat, is one of the companies trying to solve this problem. Incorporating STARS and MAPS into the designs of future cubesats would extend the orbital lives and enable decommissioning and deorbiting of future cubesats.
In the future, STARS could fire tens to hundreds of devices connected by a low power electronic bus. Applications would include deploying satellites and solar arrays.
In the area of launch technology, NASA in June announced the selection of Dynetics of Huntsville, Alabama, to develop and build the Universal Stage Adapter that will carry payloads and connect NASA’s Orion spacecraft and service module to the forthcoming Space Launch System rocket. Dynetics then awarded a contract to Systima Technologies of Kirkland, Washington, to build the adapter’s Separation Joint System consisting of two rings bolted together and an energetic separation mechanism. One side of this ring assembly will hold the Exploration Upper Stage and the other will hold the adapter with Orion and its service module. This system will bear the structural loads between the upper stage and Orion. In orbit, a solid propellant will burn to generate pressure to break and separate the two rings and release the upper stage from the adapter and deploy the payloads.
The Systima Separation Joint System includes the Low Shock Separation or LS3 technology. Overall, the system applies heritage and known energetics and mechanisms in an innovative way to create one of the largest spacecraft separation systems.
In the research realm, Systima in February demonstrated one of the world’s largest pyrotechnic devices when a cable cutter severed a braided steel cable measuring about 13 centimeters in diameter. An oil and gas company is planning to use this cable cutter in place of higher-risk systems to effectively and safely decommission offshore installations. Future applications may be found in the defense and aerospace industries. Pyrotechnic cutters of various configurations are used on launch vehicles, missiles, and parachute deployment and payload release systems.
Contributors: Peter Current, Steve Stadler, Hunter Golden
Steve Nelson is vice president for the commercial product line at Pacific Scientific EMC; Stephanie Sawhill is director of business development at Systima Technologies; Peter Current is the technical lead at Pacific Scientific EMC; Steve Stadler is a mechanical engineer at Pacific Scientific EMC; Hunter Golden is chief engineer for missile and space systems at Systima Technologies.
Related Posts
Stay Up to Date
Submit your email address to receive the latest industry and Aerospace America news.
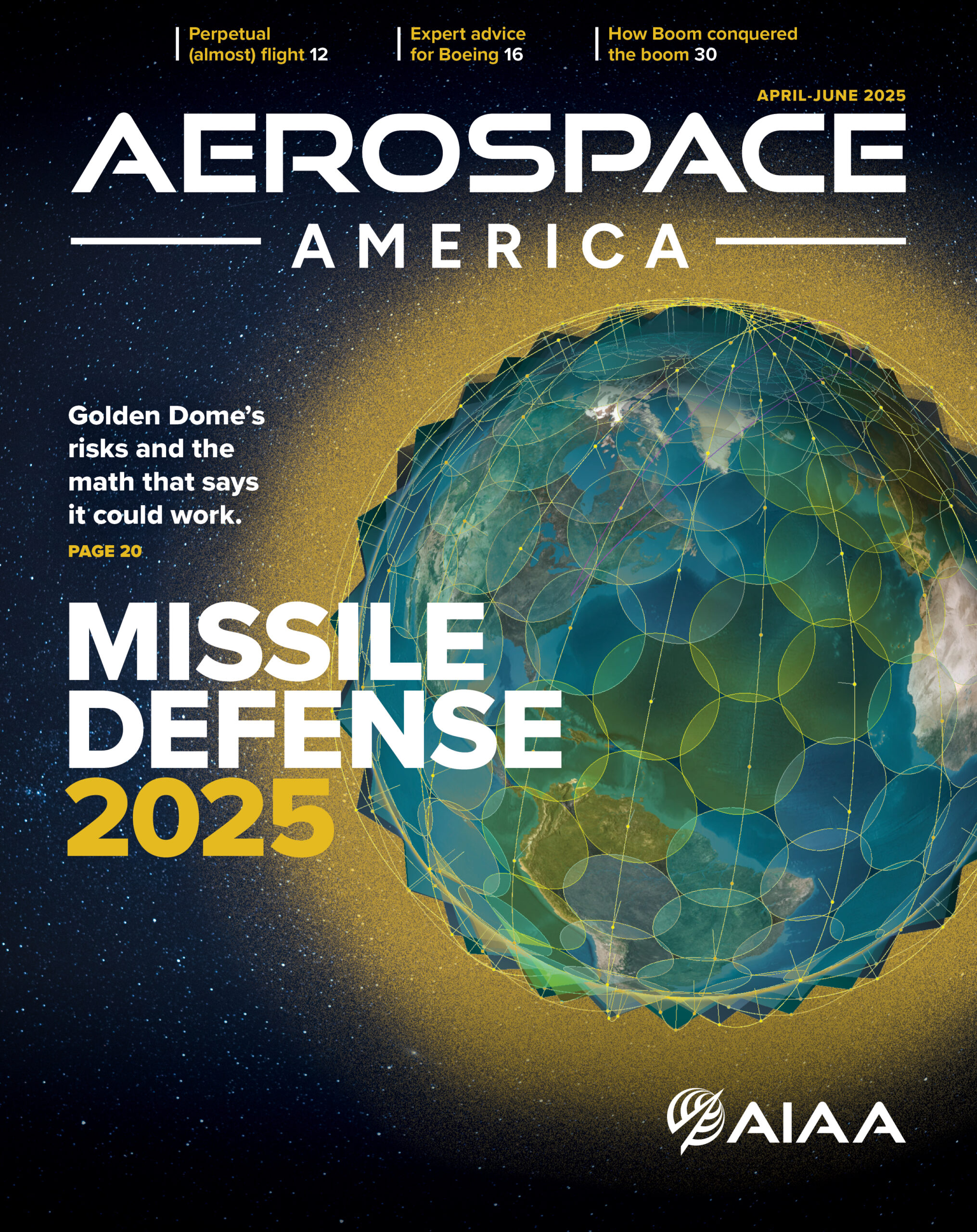