Stay Up to Date
Submit your email address to receive the latest industry and Aerospace America news.
The Structures Technical Committee works on the development and application of theory, experiment and operation in the design of aerospace structures.
Purdue University’s multiscale structural mechanics group in June completed the two-year development of an integrated design framework that empowers engineers without expert knowledge in finite element analysis and composite materials to quickly perform parametric studies, design optimization, sensitivity analyses and uncertainty quantifications. The framework is called iVABS because it is based on Variational Asymptotic Beam Sectional Analysis, a powerful cross-sectional analysis code for composite slender structures such as helicopter rotor blades. The code was released to the public in July.
Arizona State University this year continued research with its multiphysics methodology to model ceramic matrix composites, CMCs. By May, researchers had implemented the methodology in finite element analysis and demonstrated it on a representative CMC to investigate the strain acceleration of stressed oxidation experiments and analyze differences in various temperature regimes. Developed with U.S. Department of Energy funding, the methodology avoids the overarching homogenization assumptions by explicitly modeling complex temperature dependent oxidation, degradation and gaseous diffusion through microstructural constituents in CMCs.
This year, the U.S. Air Force Institute of Technology experimentally and analytically evaluated additive manufactured lattice structures made from Inconel 718 alloy. The optimized designs were placed in the nose of a projectile traveling at 200 meters per second, and the results of the projectile effectiveness were promising.
The Air Force Research Laboratory, in collaboration with Boeing, Lockheed Martin, Northrop Grumman, Israel Aerospace Industries, Rafael and the Israel Ministry of Defense made significant progress in developing and validating progressive damage modeling approaches for composite structures with damage arresting features. Multi-axial stiffened panel validation testing began in November 2021 at Wright Patterson Air Force Base and was to continue through this December.
SAFE Inc. of Colorado in July began coupon-level testing to validate the use of cold spray manufacturing technology for structural repair. This technology restores repaired parts to net shape with near net static strength and fatigue properties. The testing, which was to continue through November, showed repaired material properties near that of undamaged coupons, resulting in the validation for its use for structural repair on a Bell UH-1Y skin tube. Aircraft flight demonstration was to begin in December. This repair technology will allow the U.S. Navy and Marines Corps to improve fleet readiness, limit part scrap rate and reduce maintenance time.
Mississippi State University’s Raspet Flight Research Laboratory conducted flight testing in July of a prototype unoccupied aerial system capable of carrying payloads approaching 180 kilograms and achieving 24-hour flight endurance. Researchers at MSU are focusing on the rapid deployment of widescale ad hoc communications networks in post-disaster and communication-denied scenarios.
Boeing early in the year began assessing the results of tests conducted in 2021 with a large linerless composite cryotank. Originally designed to hold liquid propellant for the DARPA/Boeing Experimental Spaceplane Program, the tank has several design advancements, including the use of commercial aircraft materials and manufacturing processes, a permeation-resistant laminate design, reusable insulation materials and a bonded slosh baffle. Boeing and NASA pressure tested the tank at NASA’s Marshall Space Flight Center last year using liquid nitrogen, and it sustained multiple pressure cycles and 250% of its design operating pressure without failure. This technology offers the promise to reduce launch vehicle tank weights by 30%-50%, enabling heavier payloads to be launched into orbit. The tank could also provide a lightweight storage solution for future commercial aircraft powered by liquid hydrogen.
Contributors: Aditi Chattopadhyay, Stephen Clay, Sarah Galyon Droman, Anthony Palazotto, Jake Schichtel, Rani Sullivan, Steve Wanthal and Wenbin Yu
Stay Up to Date
Submit your email address to receive the latest industry and Aerospace America news.
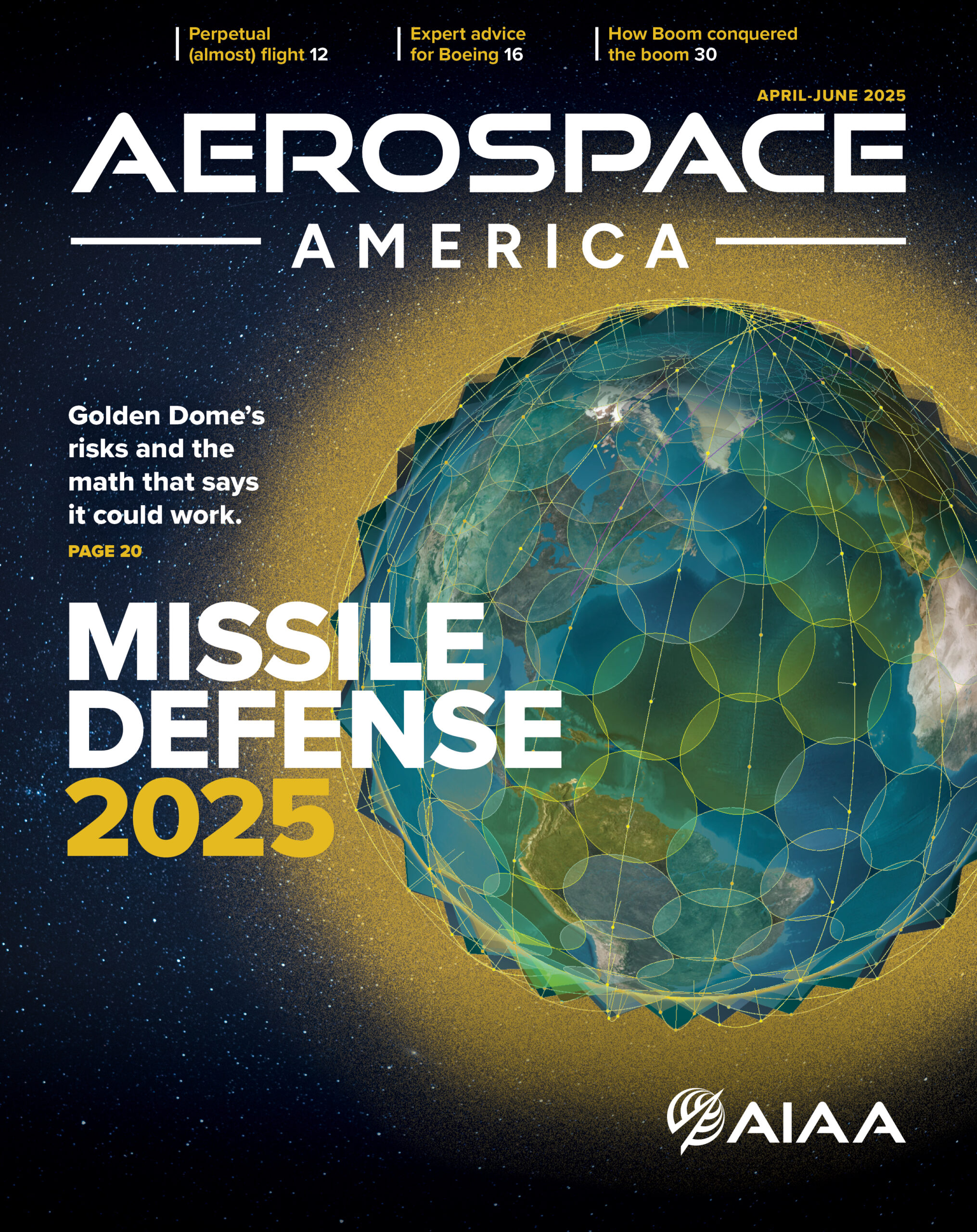