Stay Up to Date
Submit your email address to receive the latest industry and Aerospace America news.
The Hybrid Rockets Technical Committee studies techniques applied to the design and testing of rocket motors using hybrid rocket systems.
Virgin Galactic in February launched Virgin Space Ship Unity into space with a crew of three aboard, 10 weeks after its first trip beyond the 80-kilometer space boundary. Powered by a hybrid motor that provided 320 kilonewtons of thrust for nearly 60 seconds, this spaceship reached Mach 3.04 and an apogee of nearly 90 km before returning to the Mojave Spaceport in California.
Researchers at Stanford University demonstrated laser ignition of a hybrid fuel grain in a lab-scale slab burner. They presented high-speed imaging results in July that identified the underlying ignition mechanism as the entrainment and laser heating of small soot particles formed during fuel pyrolysis or chemical decomposition. A small and lightweight laser diode, combined with a few simple optical elements, provided energy to a specific point on the fuel surface and heated soot particles well beyond the temperature required for fuel pyrolysis. These particles then transferred energy to the vaporized propellant mixture, igniting the motor. Experiments have confirmed that only those fuels that produced soot were compatible with this technique, but the method holds promise for broader applicability. Tests in a single-port motor that aimed the laser at a small target area of a compatible fuel embedded in a larger, non-soot-producing fuel grain demonstrated ignition of the motor at both atmospheric and vacuum exit conditions.
NASA’s Jet Propulsion Laboratory in California and Marshall Space Flight Center in Alabama continued to lead technology development for a Mars Ascent Vehicle intended to deliver samples from the surface of Mars into orbit. To this end, Whittinghill Aerospace of California carried out full-scale motor testing of a wax-based fuel with MON-25, a mixed oxide of nitrogen, in April and July at the Mojave Spaceport. Test motors and oxidizer were conditioned to an assumed Mars operational temperature of minus 20 degrees Celsius. In this study, researchers achieved high-performance, stable burns with durations of 60 seconds. The Space Propulsion Group of California and Montana performed similar but smaller, separate tests in Butte, Montana, in January and April and had the same results. In addition, researchers at Purdue University in August presented findings that they demonstrated the hypergolic ignition and multiple relights of a paraffin-based hybrid motor with various hypergolic solids added to the headend of the fuel grain containing MON-25. Tests showed good agreement with previously completed MON-3 testing, with some tests experiencing ignition delays.
The additive manufacture of advanced hybrid rocket motors to enhance burn rates and efficiencies continued to grow. This year, the Aerospace Corp. of California produced hollow liquid fuel grains that used 3D-printed features to meter the delivery of liquid fuels such as kerosene. This arrangement combined the capabilities of liquid-engine performance with the safety and simplicity of hybrids. In the first half of the year, Aerospace Corp. flight-tested an advanced hybrid rocket with these new liquid grains and a 54-millimeter rocket motor.
In a separate program, Aerospace Corp. and Penn State continued development of a hybrid propulsion unit for cubesats. Collaborators at Penn State demonstrated start, stop and restart capabilities of the unit early in the year before returning it to the Aerospace Corp. for further development. The propulsion unit consists of a 3D-printed solid fuel grain in a combustion chamber integrated into and surrounded by a toroidal oxidizer tank. The chamber/tank component was created with direct metal laser sintering, a form of 3D printing that melts metal powder together with lasers. This technique eases the production of intricate parts that possess the necessary thermal and mechanical properties for use in propulsion systems.
Contributors: David Dyrda, Andrew Cortopassi and George Story
Related Posts
Stay Up to Date
Submit your email address to receive the latest industry and Aerospace America news.
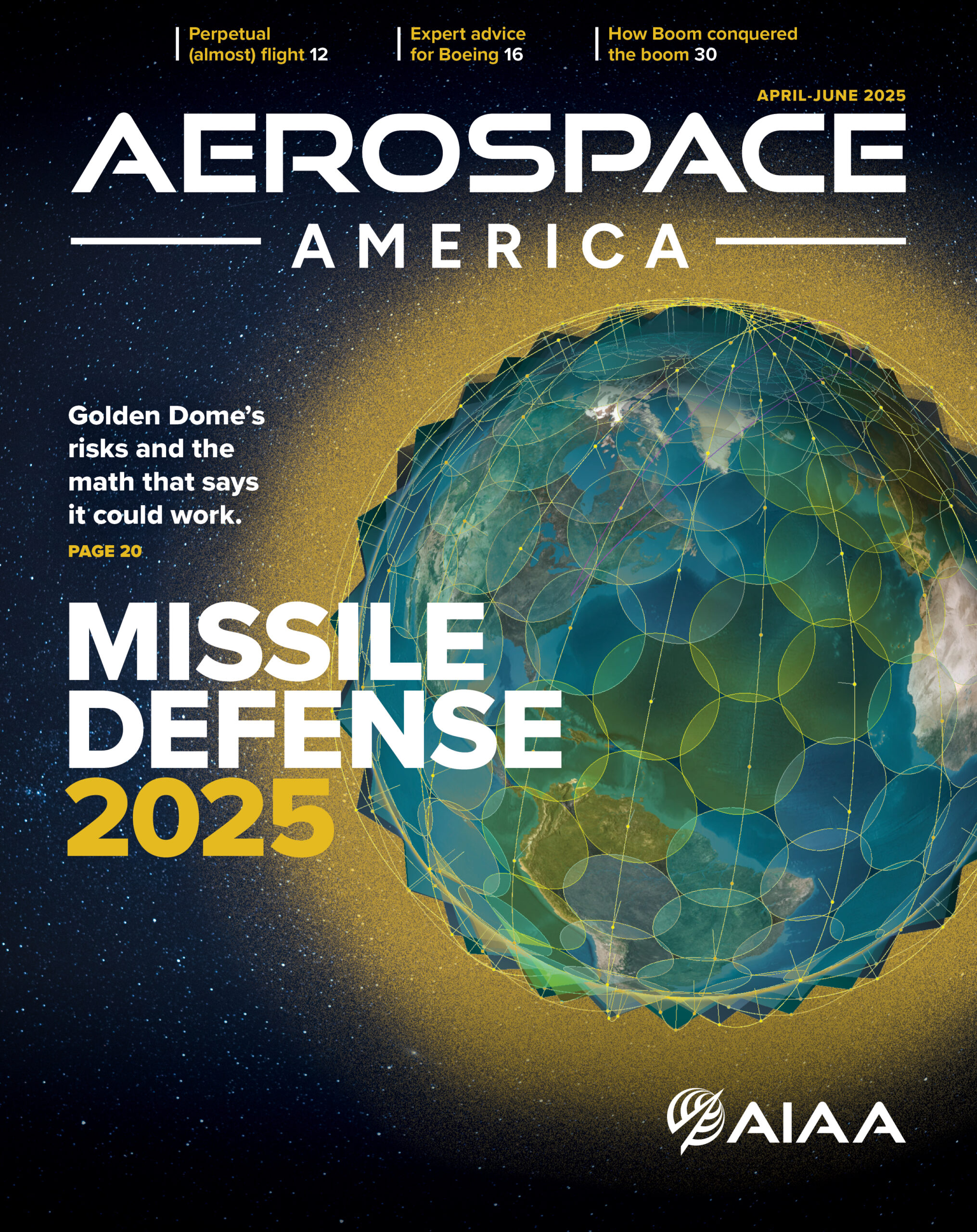