Stay Up to Date
Submit your email address to receive the latest industry and Aerospace America news.
The Structures Technical Committee works on the development and application of theory, experiment and operation in the analysis and design of aerospace structures.
The U.S. Air Force Institute of Technology conducted research this year on a variety of projects funded by the Air Force Office of Scientific Research, or AFOSR. Researchers introduced a new design for a lighter-than-air vehicle with internal vacuum. Related to this project and in collaboration with the University of Colorado, computational fluid dynamics was used to assess the effect of a vehicle during reentry into the atmosphere. A second project used heat transfer methods and structural mechanics to mimic the wear present in the Holloman test track at lower speeds. The final project determined the ideal heat treatment to optimize the residual stress field after a nickel-based alloy specimen has undergone a shot peening process.
Beginning in October, researchers from Mississippi State University’s Aerospace Engineering Department, working with M4 Engineering of California under a NASA Small Business Innovation Research grant, conducted gas permeation studies of stitched composites under thermal and mechanical loads. These projects identified barrier concepts to reduce gas permeability and prevent through-thickness cracking in cryogenic propellant tanks. MSU also performed experimental and computational studies under a separate Air Force Research Lab-funded project to determine optimum stitch parameters to limit facesheet core debonding in 3D-stitched sandwich composites.
MIT and Metis Design Corp. of Boston developed lower-cost, energy-efficient manufacturing techniques for aerospace grade composites. Joule heating is provided conductively to laminates out-of-oven, or OoO, by carbon nanotube networks integrated into thermally insulating tools. Nano-porous-network subplys are stacked between each prepreg layer to aid full resin consolidation. Using faster, more accurate uniform OoO heaters, a model-derived cure cycle was implemented, accelerating cure processes by 35% to 50%. Researchers deployed this OoO process to fabricate and test aerospace-grade carbon fiber laminates in dimensions of up to 0.6 by 0.6 meter, demonstrating equivalent or improved mechanical properties versus autoclave cured panels. The method consumes 100 to 1,000 times less energy than conventional methods and is performed with cheaper tooling without high-pressure cycles, leading to significant cost savings.
MIT, Analog Devices of Wilmington, Massachusetts, and Metis Design developed a tool for aerospace structural condition-based maintenance. This Wireless Integrity Sensor Platform, or WISP tool, captures maximum data with minimum infrastructure such as cables or connectors. WISP hardware with fatigue crack gauges was evaluated for airworthiness this year. These gauges are undergoing probability of detection analyses where they exhibit better than 1 millimeter at 90% probability of detection.
Widespread use of primary structure adhesive joints is hampered by the current inability to predict and measure the adhesive bond strength. As a result, industry and the U.S. Department of the Navy demands for lower structural weights and reduced part counts on their assets must compete with the high safety standards demanded by the certification authorities. In January, Clarkson University received an $800,000 grant from the Office of Naval Research Advanced Naval Platforms Division to develop physics-based, analytical and computational models for predicting the strength of bonded joints. This research is in collaboration with the Carderock Division, U.S. Naval Surface Warfare Center in Maryland.
With U.S. Department of Energy and AFOSR funding, Arizona State University developed multiphysics-based experimentally validated multiscale analyses for ultra-high-temperature ceramic matrix composites. High-fidelity stochastic volume elements, obtained from material characterization image processing algorithms and machine learning techniques are used for length-scale dependent morphology, architecture and variability representations. Three-dimensional orthotropic viscoplasticity creep and fracture-mechanics damage models were developed. In September, a machine learning-based reduced order damage model was also developed, in collaboration with Raytheon Technologies Research Center in Waltham, Massachusetts, to increase computational efficiency.
Stay Up to Date
Submit your email address to receive the latest industry and Aerospace America news.
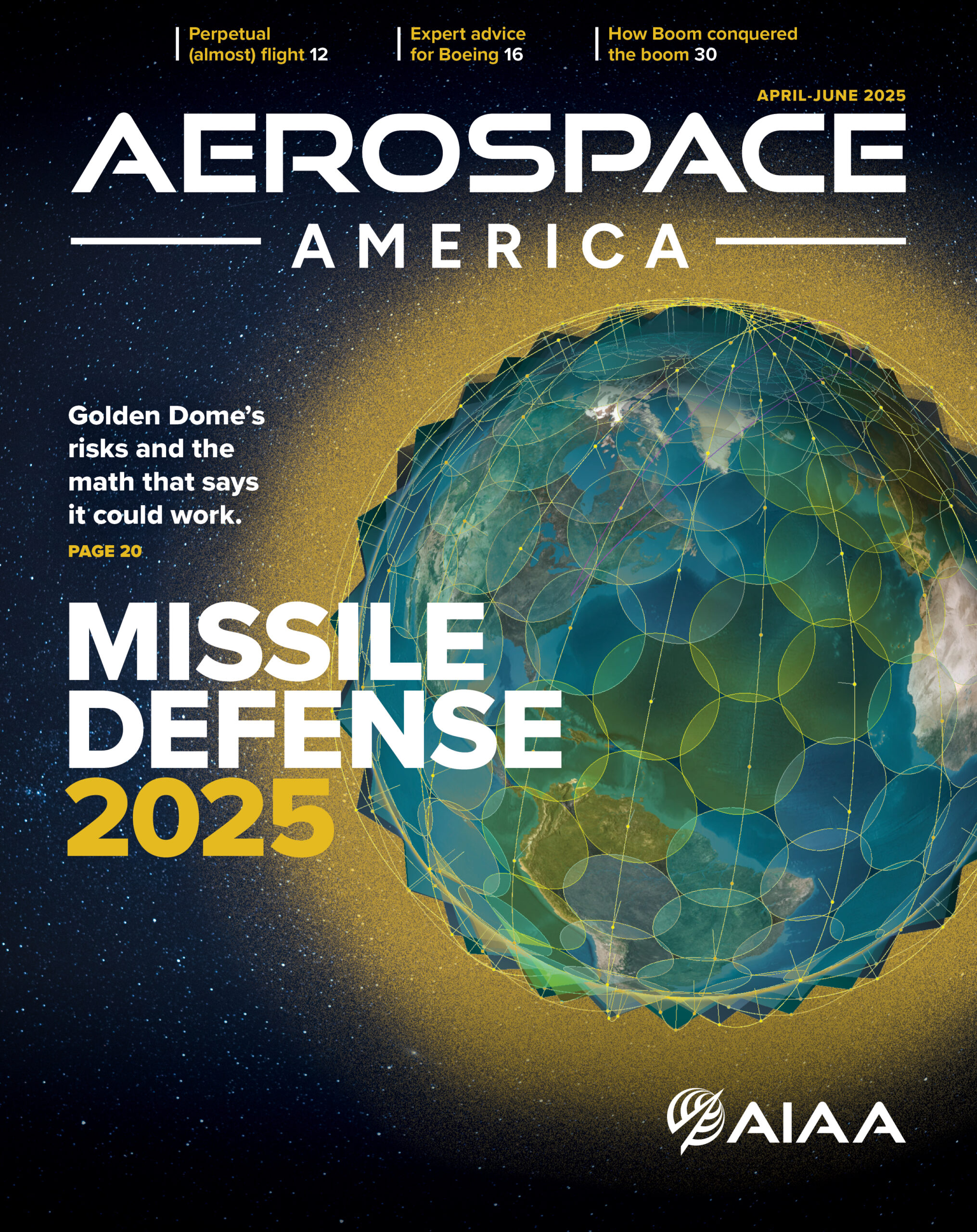