Stay Up to Date
Submit your email address to receive the latest industry and Aerospace America news.
The thinking on this question varies
Two of the world’s leading electric aircraft developers, Joby Aviation in California and BETA Technologies in Vermont, have divergent strategies for cooling their aircraft’s batteries after they land to avoid any risk of dangerous overheating and to maximize battery life.
Most of us today are familiar with our smartphones warming up during charging or intensive use. The issue for electric aircraft is that lithium-ion batteries warm up when there’s a sudden, large demand on the electricity from them, such as when landing vertically. This is the most energy-hungry portion of the flight, because the aircraft need to slow down and maneuver precisely. After landing, the batteries must be brought back into the optimal temperature range of 10 degrees Celsius to 45 degrees Celsius to keep them from dangerously overheating or degrading, and to achieve efficient charging.
“Rapid charging with poor thermal management can result in uneven charging and heating, resulting in degradation,” explained battery researcher Yashraj Tripathy, head of product for About:Energy, a London company that tests batteries for electric aircraft companies. The company also monitors battery temperature and other factors with software.
The company does not refer to specific customers, but Tripathy said the batteries that his company monitors are typically at the high end of the safe temperature range after landing vertically. Often, “they’re running at 60 degrees Celsius” — 140 degrees Fahrenheit.
He said a fully charged battery that’s also hot would be the worst scenario because of the risk that a cell could rupture, catch fire and cause thermal runaway fire in the entire battery. But also, hotter cells create more side reactions that reduce transmission of electrons or power output.
On the other hand, if a battery is charged when its temperature is below 10 C, the risk grows for lithium plating, which is when metallic lithium deposits coat the anode, reducing battery capacity.
Joby says its battery-cooling method is designed to get the aircraft charged and ready for another fare quickly, safely and with minimal battery degradation. Each charging station for the company’s four-passenger S4 air taxis has a built-in thermal management system. As the battery packs are recharged, a pump circulates coolant near the aircraft’s four battery locations to remove heat.
The charging stations for BETA’s five-passenger ALIA aircraft, on the other hand, have no coolant, but BETA has designed a standalone coolant thermal management system that can be collocated with the charging station. BETA’s coolant also circulates around the battery packs, which are in one location under the cabin, while they are being charged.
There’s a couple more differences in these cooling approaches. Joby’s S4 carries some coolant on board to keep the batteries from heating too much during flight, whereas the ALIA does not. That’s because BETA has opted for prechilling batteries, so it does not have to add the weight of the coolant to the aircraft. Also, Joby’s charging stations have two electric cords, and both can be plugged into the S4’s dual electric ports simultaneously to speed up charging. ALIA has one port for electric charging.
So far, Joby has deployed two charging stations. BETA has placed 30 of its “Charging Cube” stations in the eastern United States — mostly at regional airports — two of them with colocated thermal management units. Some of BETA’s charging stations are in parking lots accessible only to electric cars, which is part of the company’s business model. Because electric cars have onboard coolant, these chargers don’t need to be matched with thermal management units.
Two additional companies in the industry, Archer Aviation in Silicon Valley and Lilium in Munich, Germany, have announced that they intend to use BETA’s Charging Cubes and coolant stations. Volocopter, based near Stuttgart, has decided to resolve the rapid charging issue by swapping out batteries.
Joby and BETA both say their coolant methods maximize efficiency and battery longevity through optimal battery conditioning.
Chip Palombini, BETA’s head of charge product, told me that the company believes it is important to keep coolant and electricity separate. For one thing, the separation means charge stations can be placed independently of the coolant.

Get the latest news about advanced air mobility delivered to your inbox every two weeks.
“Typically, you don’t want to mix liquid and high voltage,” he said.
I asked what he meant by that, and if he thought there were risks.
“Yeah, I think it’s partially that,” he replied, “and for internal structural reasons, where you might want the coolant going could be different than where the charge goes.”
Eric Allison, Joby’s chief product officer, said the company believes the S4’s dual charging ports mean the aircraft can charge more efficiently for rapid turnaround without jeopardizing thermal management.
“We are able to charge and cool or condition two of those batteries simultaneously,” Allison said. “We need to be able to fast-charge these batteries while we’re loading and unloading people.”

About paul brinkmann
Paul covers advanced air mobility, space launches and more for our website and the quarterly magazine. Paul joined us in 2022 and is based near Kennedy Space Center in Florida. He previously covered aerospace for United Press International and the Orlando Sentinel.
Related Posts
Stay Up to Date
Submit your email address to receive the latest industry and Aerospace America news.
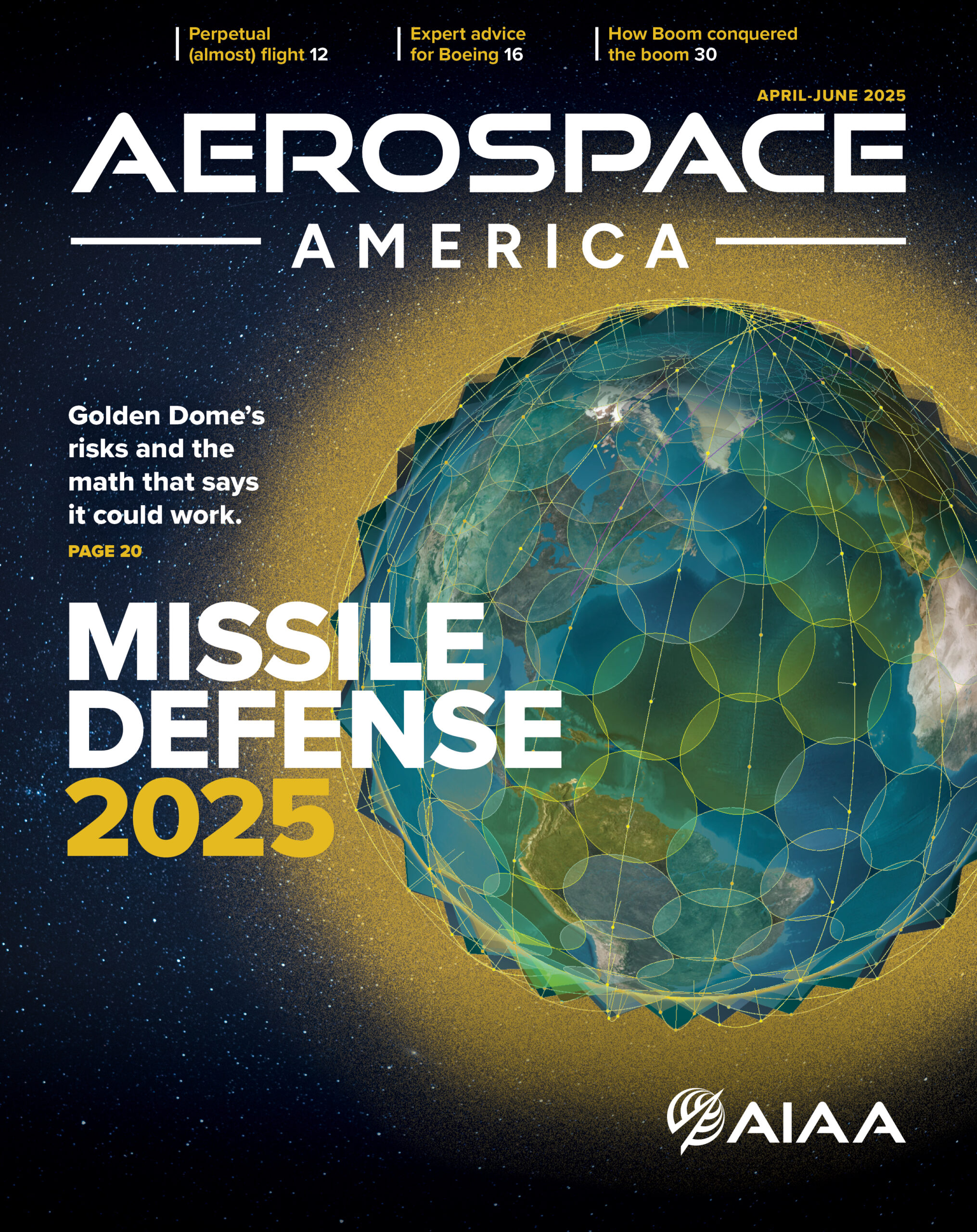