Stay Up to Date
Submit your email address to receive the latest industry and Aerospace America news.
Divergent strategies for production software share an embrace of artificial intelligence
Electric air taxi developers are counting on various kinds of production software, including some driven by artificial intelligence, to give them an edge on production speed, cost and quality once they start mass producing their aircraft.
Two of the leading companies in the United States plan to begin that serial production next year, and for them, acquiring or creating the right manufacturing execution systems, or MES, has been a high priority.
Joby Aviation, the California company that’s among a handful of leaders in the field, in 2020 purchased MES software from First Resonance, a Los Angeles-based startup.
The company’s founder, Karan Talati, used to work at SpaceX. After leaving in 2016 to establish First Resonance, he created the production software, ION, by drawing on lessons he learned in Hawthorne, where for three years he built software that assisted with “scaling up” production of Falcon 9 rockets and Dragon spacecraft.
“Manufacturing generates a lot of data, and the problem for people managing the process is actually just accessing that data in a systematized and programmatic way,” Talati tells me.
Joby has used ION to produce and improve prototypes of its four-passenger S4 air taxis at its plant in Marina, California. The company plans to continue managing its manufacturing with ION once it begins mass production at a plant planned near Dayton International Airport in Ohio.
Already with the prototypes, the ION software has monitored and adjusted such procedures as the written instructions for cure times of carbon composite parts, when the parts are heated to dry them in an oven-like autoclave.
Joby expects that to be a timesaver once serial production begins.
“Changing the cure process for 500 parts could be very time consuming, but we only need to change one procedure now and our (ION) software inserts that change into every part affected,” Joe Brennan, Joby’s manufacturing lead for composites, tells me. “These are incremental changes we need to be able to make quickly as we evolve and grow.”
Brennan says recording the history of each part as it is built and assembled into the aircraft is crucial.
“We needed to be able to update or modify production methods quickly, and trace those modifications, to keep a history of what we changed. But what was available in the market was really either very basic, online instruction tools without traceability or software that took a long time to reconfigure,” he says.
At the moment, ION incorporates very little AI, but plans call for coders to gradually add AI to look for issues more quickly. For example, parts could be compared to a model to flag any differences, so that the production process can be tweaked across the facility. The software would “automatically detect anomalous behavior or spot problems that human eyeballs alone wouldn’t be able to catch,” Talati says.
By contrast, BETA Technologies, the Vermont company that’s among those vying with Joby and others to pioneer the air taxi sector, has developed manufacturing software in-house, including with AI features, and has also procured what it calls “legacy aerospace software,” which it declined to identify. BETA is in the process of equipping and starting up a production facility in South Burlington.
“We’ve been developing software and processes for the better part of two years, leveraging proven aerospace production software alongside our BETA-developed human and AI assets to ensure thorough checks and balances while streamlining efficiencies,” BETA says.
BETA has designed its software to pull manufacturing data directly from machines and the larger factory environment, which will be analyzed by AI to alert quality control personnel if necessary.
Get the latest news about advanced air mobility delivered to your inbox every two weeks.

About paul brinkmann
Paul covers advanced air mobility, space launches and more for our website and the quarterly magazine. Paul joined us in 2022 and is based near Kennedy Space Center in Florida. He previously covered aerospace for United Press International and the Orlando Sentinel.
Related Posts
Stay Up to Date
Submit your email address to receive the latest industry and Aerospace America news.
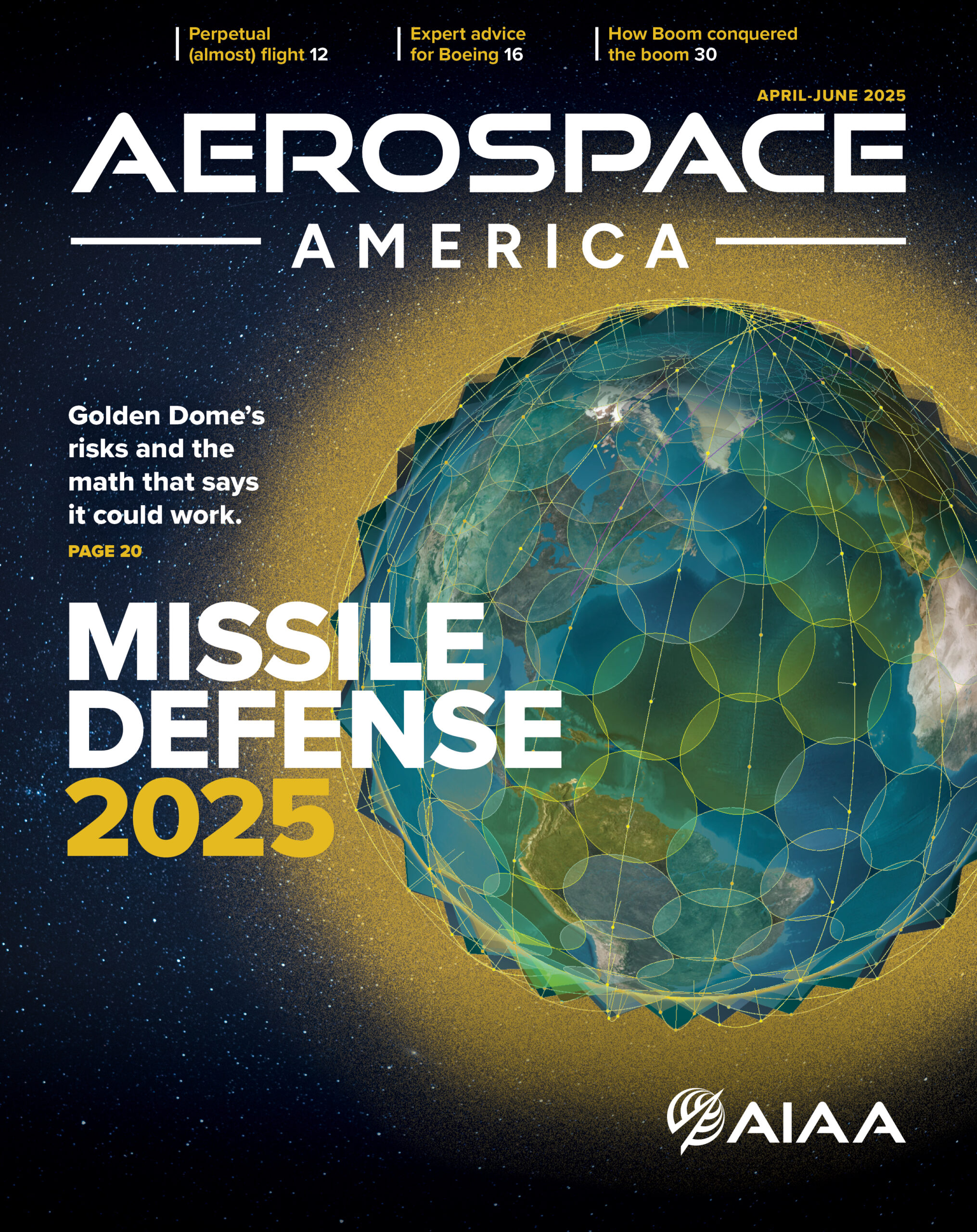