Stay Up to Date
Submit your email address to receive the latest industry and Aerospace America news.
No news was good news
The maxim when flying a demonstrator for the first time is that it’s OK — even welcome — if not everything goes perfectly, because it’s better to find a technical issue early than late . The story is different when taking a production model up for the first time.
Kyle Clark, founder and CEO of electric aircraft developer BETA Technologies, views the inaugural flight on Nov. 13 of the first production model of the company’s ALIA CX300 plane as a success because there were no surprises.
Clark’s nearly hour-long flight of the conventional takeoff and landing aircraft over the company’s headquarters in Burlington, Vermont, yielded plenty of insight about how the controls worked and how the aircraft responded. But a week later, there was a lengthy discussion about a mundane issue: how Clark felt in the aircraft.
“The fact that we are not worried about propulsion, batteries, flight controls, and we’re worried about how the pilot feels when the door is actually closed is, well — it’s cool to be at that point,” Clark told me.
He hand flew the plane in “direct law” mode, not on autopilot. “We climbed immediately, 1,500 feet a minute, up to 7,000 feet. And as soon as I got up there, I realized I didn’t even have to think about controlling this airplane. It flew just like the simulator. It was enjoyable,” he says.
For more about advanced air mobility, receive the True Mobility newsletter in your inbox.
During the three weeks leading up to the flight, Clark flew in the company simulator two to three hours a day, practicing emergency procedures, contingency plans, rerouting to alternate airports and emergency descents.
“So it’s almost like I expected one of those things to happen,” he says. “Then all of a sudden, whoa, I realize this all works. So the surprising thing was that it just worked so well.”
Next, Clark and other BETA pilots will fly the aircraft for 50 hours before other pilots fly outside of the Burlington area to train additional pilots, under an FAA certificate for Experimental Research & Development, Market Survey, and Crew Training.
BETA’s 18,580-square-meter (200,000 square feet) production facility in Burlington will turn out another CX300 within a month, Clark says. But he adds that turning out another plane quickly isn’t the goal at this point.
“In this phase of production and industrialization, we’re identifying the limiting factors in the production facility, things that could be obstacles in mass production,” he says. “Then we apply the engineering and resources and root it out now, because we have to be able to build at a high rate eventually.”
And yet, “we have already built five or six wings, and three to four fuselages,” he adds.
BETA is also developing a vertical takeoff and landing version of ALIA, and these parts could be used for either the six-seat CTOL or early versions of the VTOL. BETA intends to sell and certify the CTOL first as it continues development of the VTOL.
The CTOL has a single pusher propeller in the rear that accelerates the aircraft horizontally to liftoff speed. For the VTOL, BETA adds booms that are fitted with four propellers to take off and land vertically.
As an aircraft comes together, it is moved down the line to subsequent stations until it reaches final assembly. About 100 people work directly on the production line, while hundreds more engineers and support staff work nearby, Clark says.
He says that BETA’s work philosophy requires every engineer to be on the production floor “when their design is built for the first time” to “reach their hand through the hole and put the screwdriver on the head of the Phillips screw” to work directly on the aircraft.
BETA is among several electric aircraft companies that are building production facilities. Joby Aviation has a small factory in Marina, California but plans call for a larger plant to be constructed in Dayton, Ohio, for its four-passenger S4 . Another California company, Archer Aviation, is installing manufacturing equipment at its plant in Covington, Georgia, southeast of Atlanta, where it plans to build its four-passenger Midnight.

About paul brinkmann
Paul covers advanced air mobility, space launches and more for our website and the quarterly magazine. Paul joined us in 2022 and is based near Kennedy Space Center in Florida. He previously covered aerospace for United Press International and the Orlando Sentinel.
Related Posts
Stay Up to Date
Submit your email address to receive the latest industry and Aerospace America news.
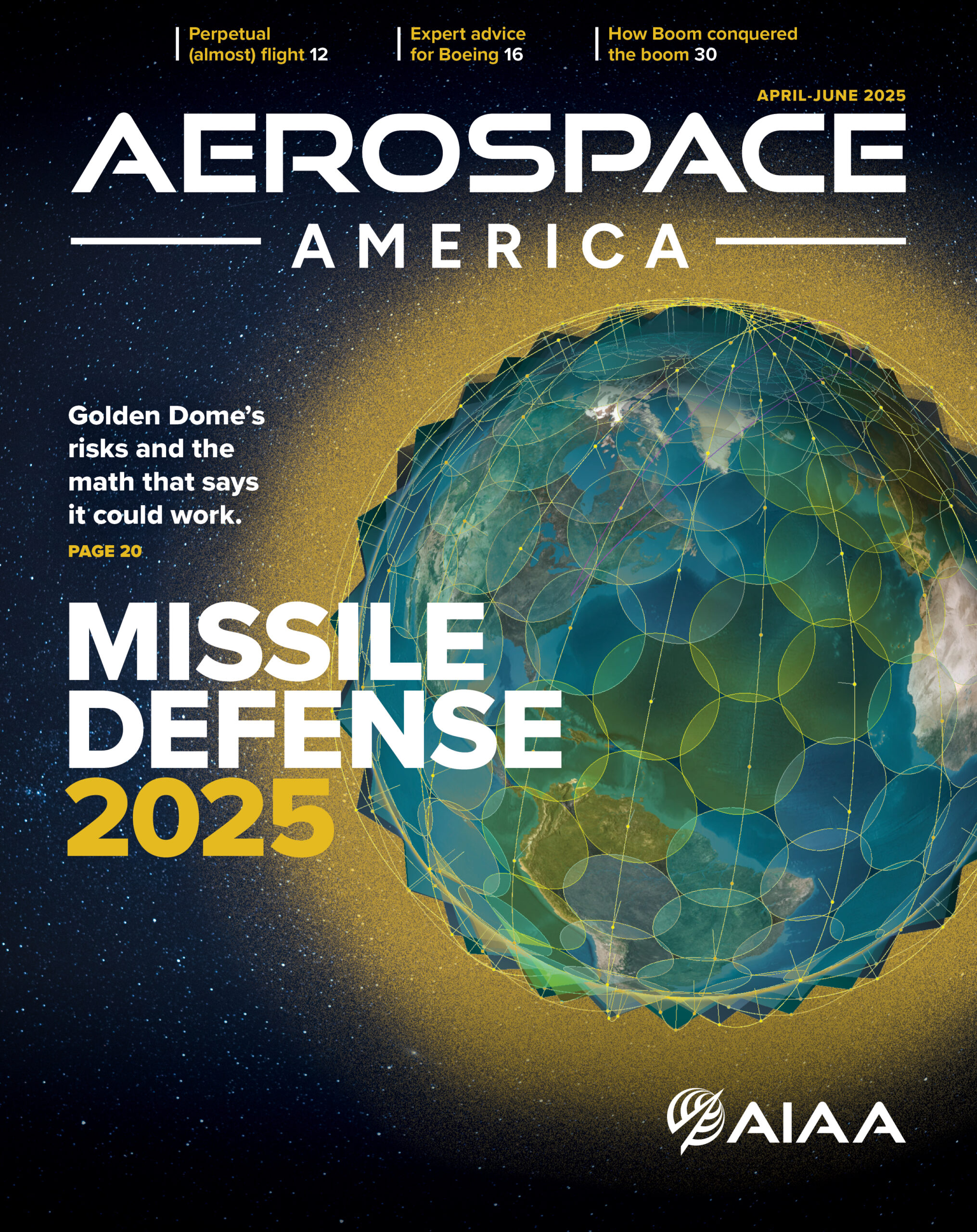