Stay Up to Date
Submit your email address to receive the latest industry and Aerospace America news.
UPDATE: Southwest Airlines has completed fan blades inspections on its share of the engines affected by the FAA order with “no additional findings of subsurface cracks,” the airline said in a May 17 statement. “The inspections were part of an existing CFM56-7B engine inspection program that Southwest voluntarily accelerated.”
In the wake of the fatality aboard a Southwest Airlines flight in April, aircraft technicians are in the process of sending ultrasonic waves through the fan blades of thousands of jet engines to check for metal fatigue.
Investigators quickly suspected that a blade broke off from the left engine of the Southwest Boeing 737-700, spraying debris into the fuselage and causing the deadly decompression that killed a passenger.
The U.S. National Transportation Safety Board said Thursday that investigators discovered six crack lines from metal fatigue in pieces of the blade discovered inside the CFM56-7B engine built by CFM International, the joint venture of Safran Aircraft Engines and GE Aviation. The FAA had already ordered U.S. airlines to inspect the fan blades on any CFM56-7B engines that have completed 30,000 or more takeoffs and landings. The order affected an estimated 3,716 engines. The FAA also ordered more frequent blade inspections after the NTSB reported that the fan blades on the Southwest plane were last overhauled 10,712 engine cycles before the accident.
There are several methods to do ultrasonic inspections, but the post-accident FAA directive and CFM service bulletin provide instructions for these tests. The engines will be kept on the wings, and technicians must remove and clean the 24 titanium fan blades from each engine. They will look for cracks or flaws with their eyes before covering the blades with glycerin, a gel, that transmits the sound from an ultrasound probe to the surface of the blade. In fact, glycerin is often one of the ingredients in the gel that doctors spread on the skin during ultrasound exams, such as those for pregnant women.
If there is an irregularity in the fan blade, such as a microscopic crack, this shows up on a handheld display as a peak in amplitude of the signal that echoed from the crack.
The reading must fall within the acceptable range set by the calibration standard or the inspector will run a separate test in which electromagnetic signals are transmitted into metal. These should form eddy currents. But if there are indeed cracks, these will prevent eddy currents from forming around the compromised section. These gaps will show up on the device’s voltage display screen, and the fan blade will be set aside and replaced. Such eddy tests require attaching separate probes with electromagnetic conductor coils to transmit the current.
FAA-certified inspectors told me this effort is well above the typical demand for fan blade inspection. Victor Sloan, president of an FAA certified repair center called Victor Aviation in California, says there are a limited number of inspectors certified to do fan blade tests, so the order from the FAA “could very well overload the capacity of people in the field.”
A spokeswoman from CFM International told me “we do have the resources in place to support the mandated inspections, including a team of more than 500 experts worldwide supporting our airline customers.”
Southwest Airlines says its inspections are underway and that it expects to have all aircraft equipped with those engines inspected by May 18.
In the Southwest Airlines photo at the top of this page, a company technician examines a CFM56-7B engine whose fan blades have been removed, exposing the vanes that direct air through the engine.
About Tom Risen
As our staff reporter from 2017-2018, Tom covered breaking news and wrote features. He has reported for U.S. News & World Report, Slate and Atlantic Media.
Related Posts
Stay Up to Date
Submit your email address to receive the latest industry and Aerospace America news.
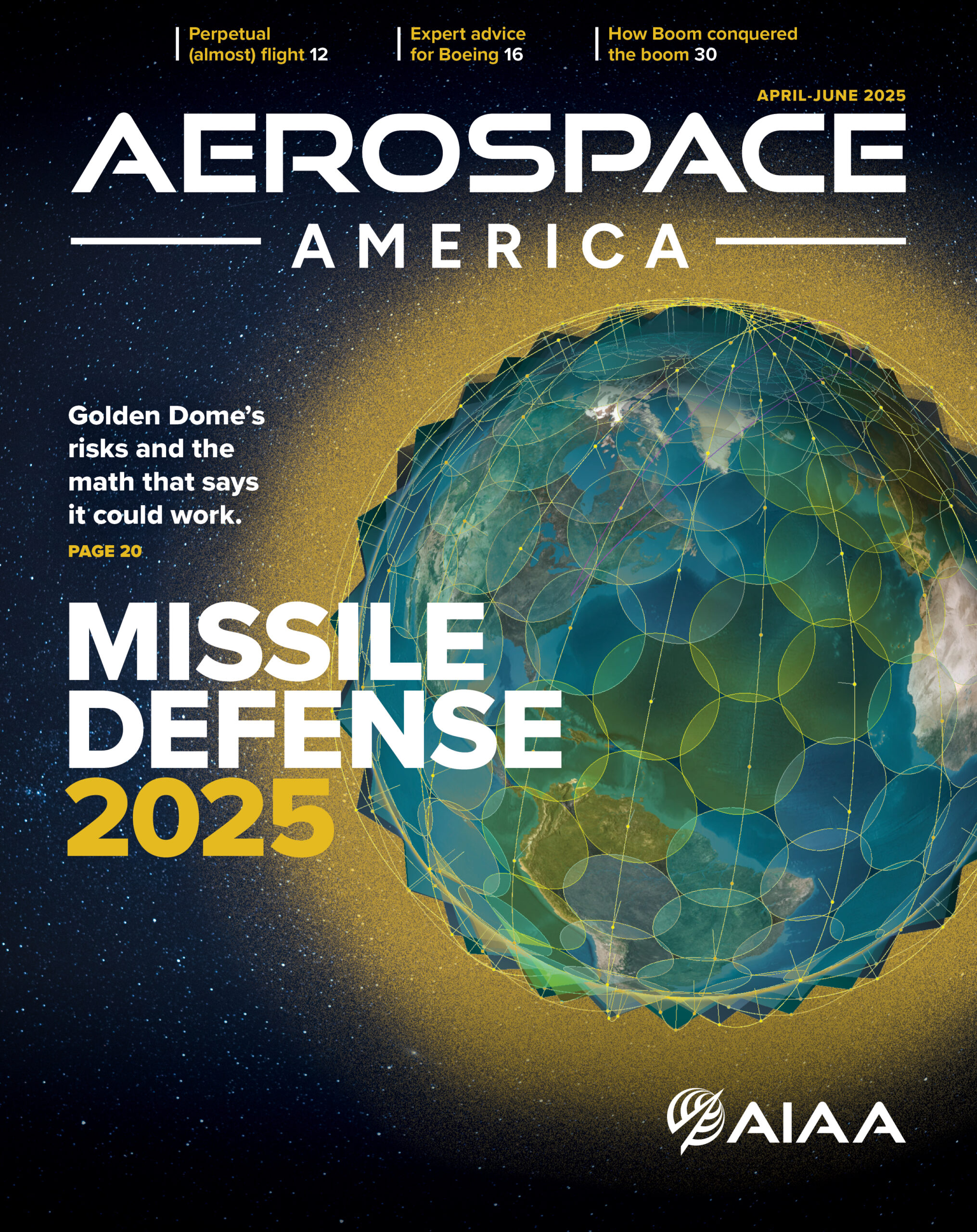
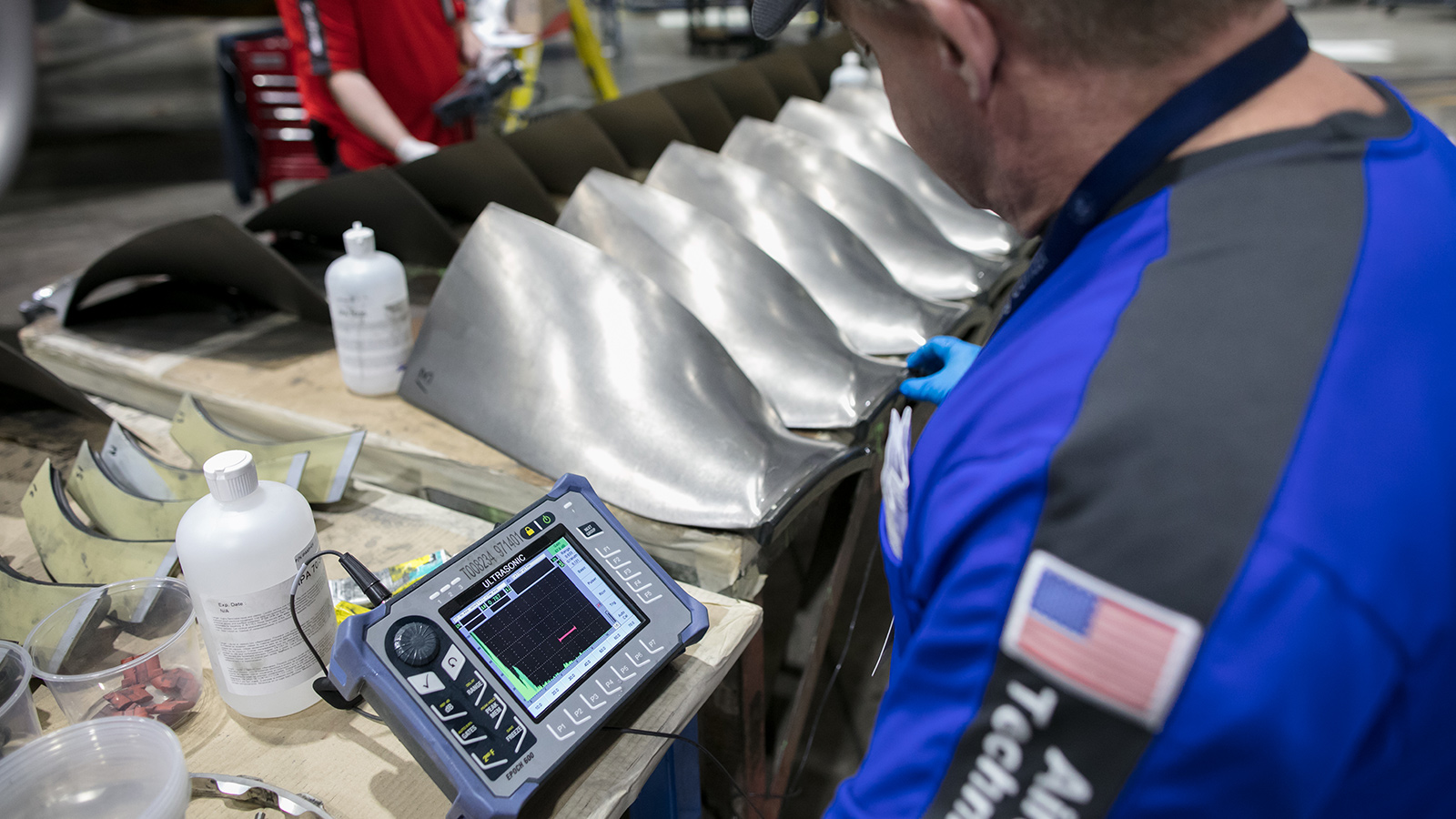