Stay Up to Date
Submit your email address to receive the latest industry and Aerospace America news.
In-space manufacturing is reaching a crucial point. Dozens of companies are now developing technologies to make use of the microgravity environment to beat the efficiency and quality of goods and materials made on Earth. The question has been how to bring products home safely in sufficient quantities. Jonathan O’Callaghan tells the story of two startups vying to show the way.
Editor’s note: This story has been updated. A previous version incorrectly referred to Redwire as a conglomerate.
Getting stuff into space has never been easier. SpaceX, Rocket Lab and other launch companies have vastly lowered the cost of going to space and increased the rate of launches, with 135 launches in total in 2021 — more than any other year in history.
Yet while space is the most accessible it’s ever been, coming back is more difficult. At the moment, the only U.S.-made vehicles capable of bringing anything back are SpaceX’s Dragon spacecraft. Not quite ready yet are Boeing’s Starliner capsules and Sierra Space’s Dream Chaser spaceplanes, and of course Russia has its Soyuz capsules and China its Shenzhous.
Much more return capacity will be needed for entrepreneurs to springboard in-space manufacturing into a capability that can transform entire industries on our planet. So far, the ability to make useful items in space, such as optical fibers that can be made into cables, has been demonstrated on the International Space Station. Enough material has been brought home aboard the Dragons to show the promise of in-space manufacturing, and now, startups are eyeing novel and cheaper ways of getting material back from space.
“It’s absolutely an exciting time,” says Shelli Brunswick, chief operating officer of the Space Foundation in Colorado. “The possibilities are endless.”
Mary Poppins
Today, cargo returning to the U.S. from ISS must fit on racks or inside compartments aboard the van-sized Dragon capsules. And there’s a wait, with such returns only happening every few months at best. Anything made in space, therefore, currently faces lengthy delivery times.
In the United Kingdom, however, one startup has another idea. Called Space Forge, the company based in Cardiff is developing a method to protect each of its reusable small spacecraft as they plow through the atmosphere. If successful, materials and products could be made in orbit and dropped back to Earth as needed, without having to schedule a trip on a Dragon, or someday a Dream Chaser or Starliner.
“We’re building the world’s first returnable and relaunchable satellite platform,” says Joshua Western, the company’s co-founder and CEO. “We’ll be able to scale in-space manufacturing to a position where it’s economically viable.”
The company plans to soon launch a small demonstration spacecraft called ForgeStar-0 from the U.K. on an air-launched Virgin Orbit rocket in what would be the first orbital launch from the country. The spacecraft will test the company’s proprietary re-entry shield, which during future operational missions would protect a satellite traveling through the searing heat of the atmosphere, targeting a landing ellipse of just hundreds of meters. While the exact technology is under wraps, Western says each shield has an “umbrella-like” deployment, unfurling upside down ahead of the spacecraft to start. Then, once through the thick atmosphere, the shield doubles as a parachute, slowing the spacecraft for a gentle touchdown.
“I describe it as Mary Poppins from space,” says Western.
ForgeStar-0 will be purposefully oriented to burn up in the atmosphere, providing useful data points about how the shield copes with re-entry. But a true test will come possibly as early as next year, when the company launches its ForgeStar-1 satellite to demonstrate in-space production of semiconductors, which have a 10-to -100-time performance improvement over semiconductors made on Earth.
“You can reduce the energy consumption of major infrastructure by more than 50%,” says Western.
Space Forge is being taken seriously. In 2021, it closed Europe’s largest seed-funding round for a space company, raising $10.2 million. The company hopes to begin commercial operations by the end of 2023 at the earliest.
“They’re envisioning manufacturing facilities in space that can produce flawless electronics, exquisite metal alloys and perfected pharmaceuticals,” says the Space Foundation’s Brunswick. “The cost-benefit analysis is exponential.”
Special delivery
In the U.S., another company is hoping to achieve a similar goal, albeit by slightly different means. SpaceWorks of Georgia is designing a more traditional return capsule with funding from NASA. The idea is that the capsule would pass through the atmosphere, protected by an ablative heat shield, then deploy a guided parafoil to gently lower itself to the ground.
In October 2021, the company tested a prototype of its RED-4U capsule — RED stands for Re-Entry Device. The capsule dropped from a balloon at an altitude of some 32 kilometers (100,000 feet) and deployed its parafoil, simulating the final stages of re-entry and landing.
“That last 100,000 represents the re-entry conditions that we’ll see from space,” says John Bradford, the company’s president and chief technology officer.
SpaceWorks ultimately plans to launch larger versions of its capsules to orbit. Each would be launched by a conventional rocket, and once released, a booster module would send it to ISS or to one of the planned private stations. The capsule would enter the station airlock and be collected by astronauts.
“They could just bring it inside,” says Bradford, and pack it with space-made materials or products for return to Earth. For return, crew members would push the capsule back out of the airlock, and its booster module would propel it toward Earth.
SpaceWorks is also designing a free-flying version of the capsules. A manufacturer could install production hardware in the capsule and make the materials or products on orbit, and then the capsule would bring the payload down to Earth.
“We can go up to about 120 days in orbit,” says Bradford. The company is targeting a suborbital test in 2023 before beginning orbital operations in 2024.
SpaceWorks ultimately hopes to have one capsule returning every week, while SpaceForge is aiming for about one a month.
What could drive such a high cadence? One possibility is ZBLAN, short for zirconium barium lanthanum aluminum sodium fluoride. This glass-like material can be robotically pulled into strands and bundled to form fiber optic cables with a wider range of frequencies than Earth-made cables comprised of silica fibers. A handful of companies have produced ZBLAN on ISS, including the now-defunct Made in Space. Another California company, Fiber Optic Manufacturing in Space, is currently manufacturing such fibers and forming them into cables via a remotely controlled machine in the station’s Destiny Lab, which can produce a kilometer of cable in just “minutes to hours,” says Leo Volfson, owner of Torrey Pines Logic in California, which builds the machine for FOMS.
But the company that acquired Made In Space, Florida-based Redwire, also sees a much wider demand. The company has tested a host of in-space technologies in orbit including tissue growth equipment.
“Biotech is the low-hanging fruit,” says Mike Gold, Redwire executive vice president for civil space and external affairs. “It’s an existing market, there’s a great deal of need, and there’s vast quantities of money.”
And while much progress has been made, having additional methods to return material from orbit could be invaluable.
“We could certainly use more,” says Gold. “The ability to get more down-mass options on demand, as opposed to waiting months, would be very attractive.”
All eyes now will be on Space Forge and SpaceWorks, to see if their efforts can be successful.
“Everyone’s been focused on sending things up,” says Bradford. “Now we’re starting to think about bringing things back.”

About Jonathan O'Callaghan
Jonathan is a London-based space and science journalist covering commercial spaceflight, space exploration and astrophysics. A regular contributor to Scientific American and New Scientist, his work has also appeared in Forbes, The New York Times and Wired.
Related Posts
Stay Up to Date
Submit your email address to receive the latest industry and Aerospace America news.
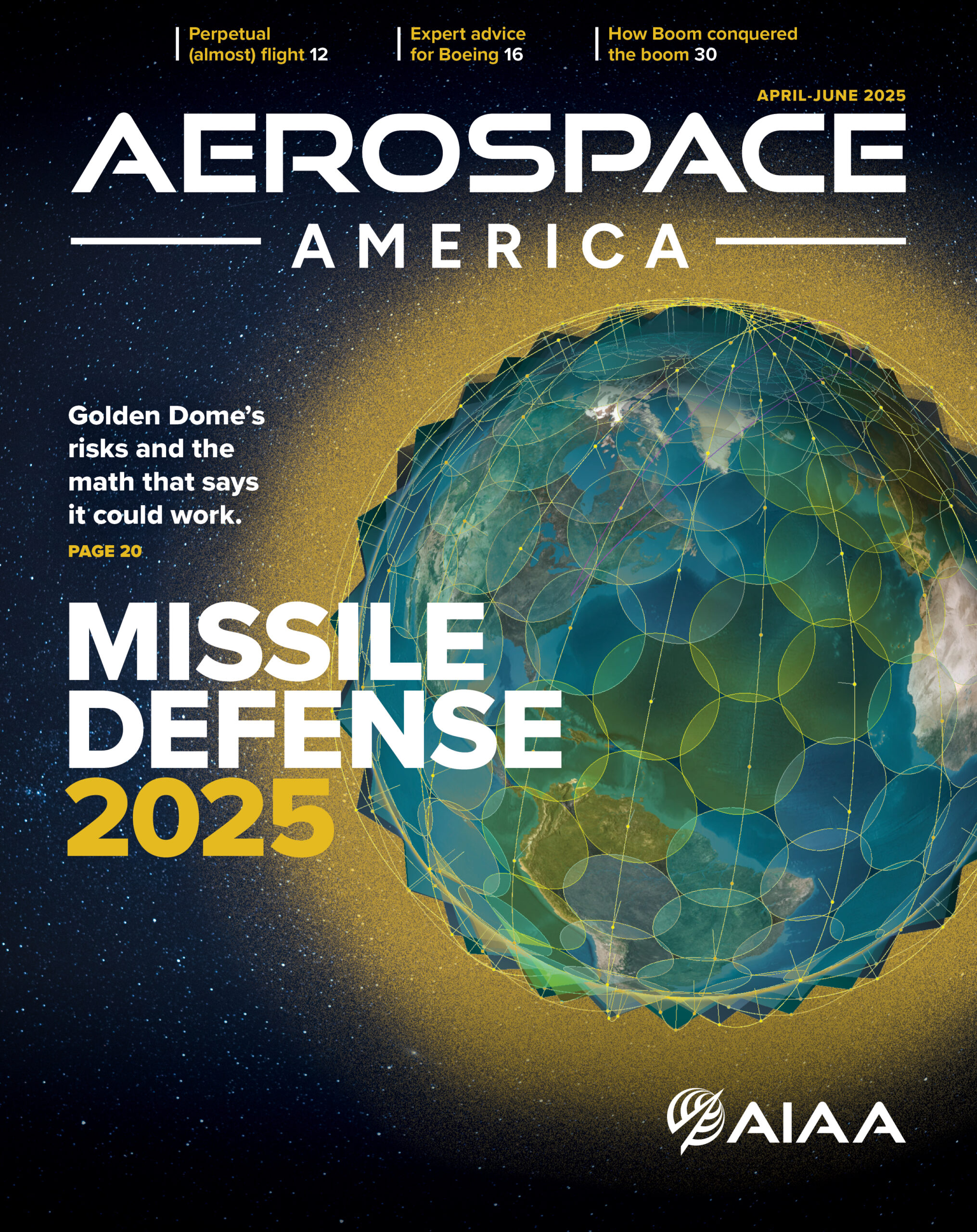
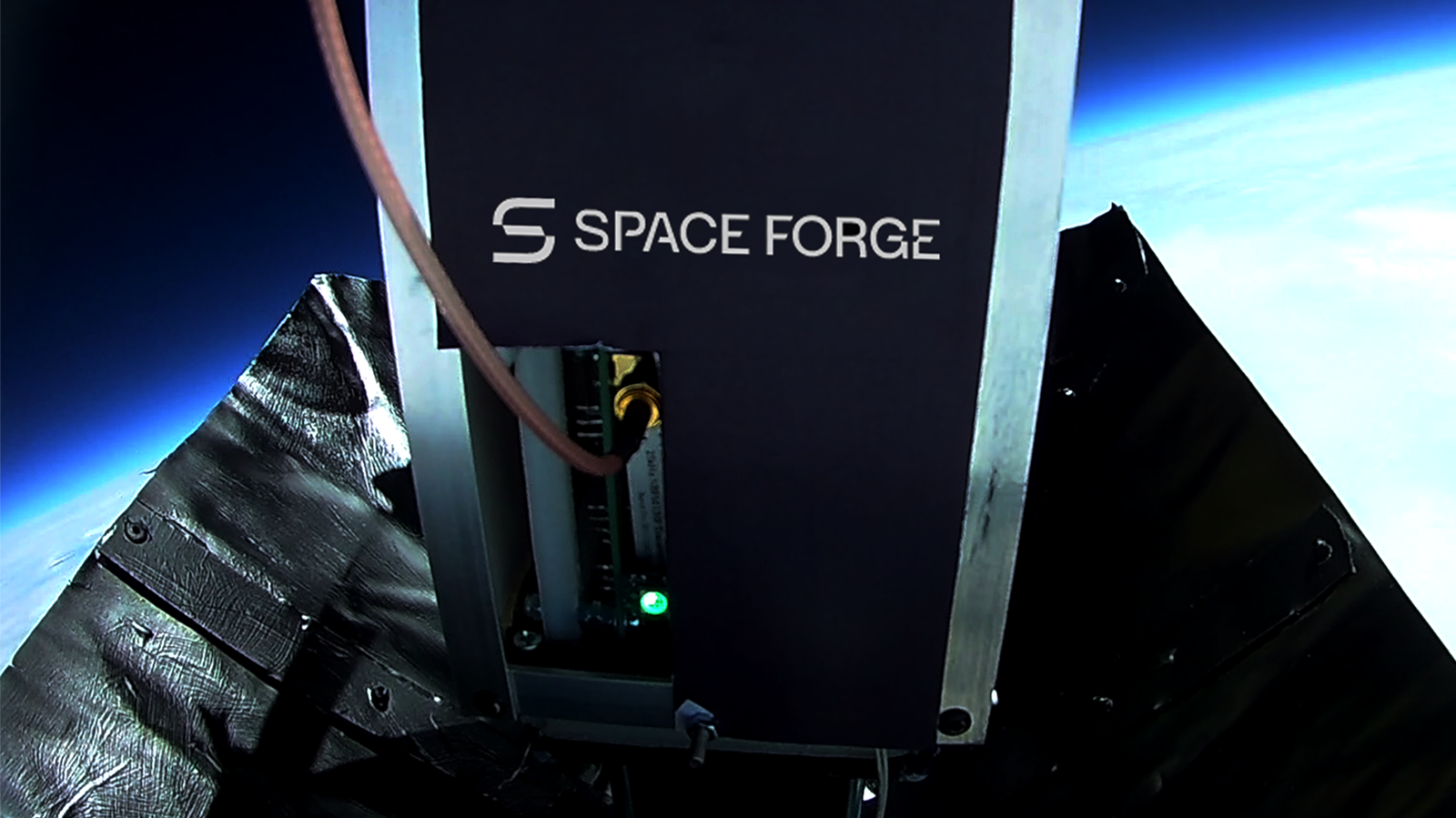
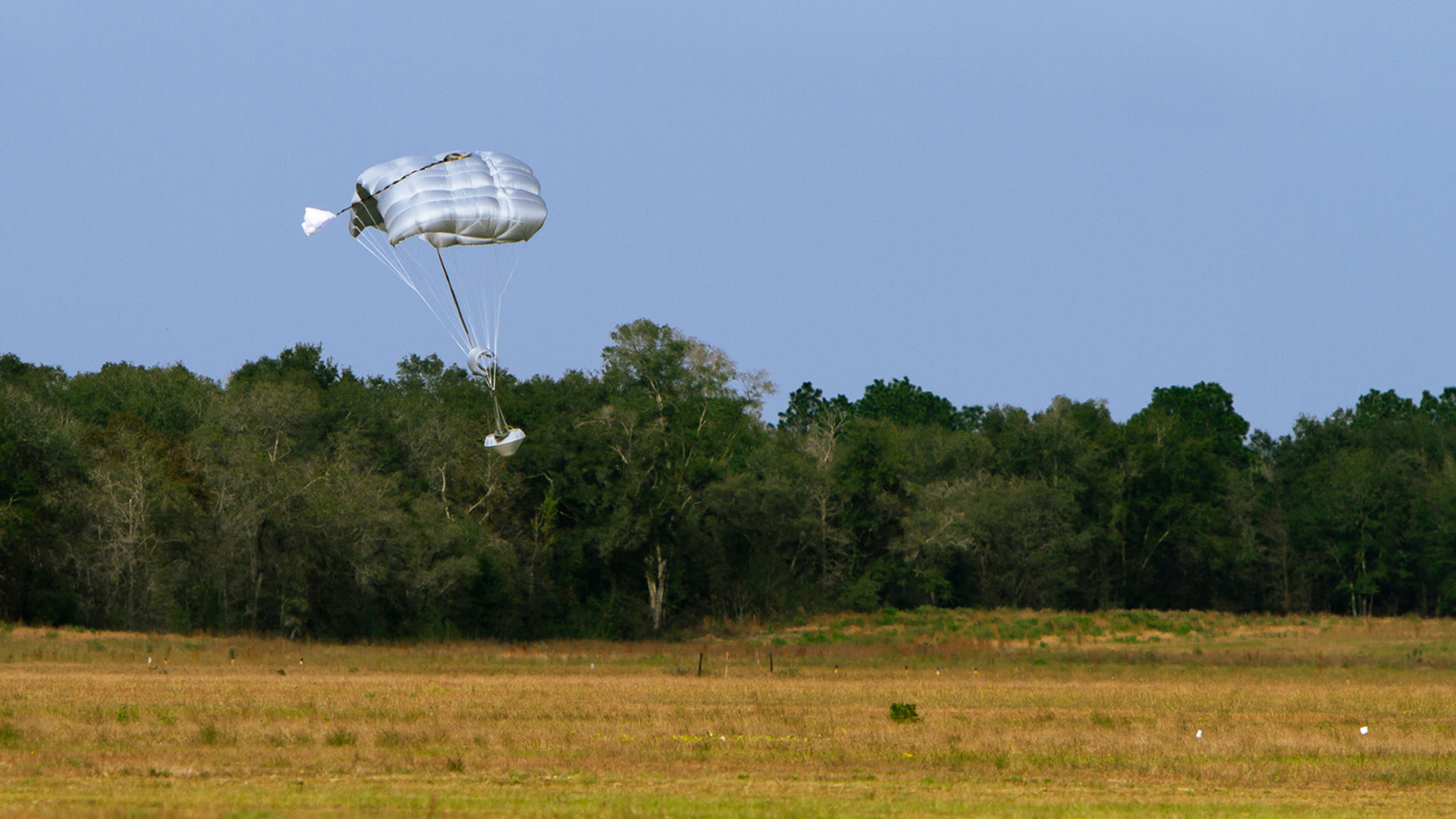