Stay Up to Date
Submit your email address to receive the latest industry and Aerospace America news.
Boeing is seeking to climb out of the most difficult period in its 110-year history, which began with the 737 MAX 8 crashes that killed 346. Just when it appeared quality was improving, a door plug flew off an Alaska Airlines jet in early 2024. Today, production of the MAX and 787 remains below targets. In the space domain, the company hasn’t said when another Starliner capsule will be flown. CEO Kelly Ortberg has promised to “fundamentally transform” the company culture, one of the pillars of the Safety & Quality Plan created after the door plug incident to remake its culture, among other changes. I asked experts from Congress, industry and academia what else should be done.
Congress can’t legislate corporate cultural change, but the culture has to change. Boeing has to assure people that they are going to prioritize quality and safety and deliver on that message. What the House Transportation Committee found in its investigation was that during the design and certification of the 737 MAX, numerous people spoke up and said, “Hey, you can’t design the MCAS software to activate with input from only one Angle of Attack indicator.” And Boeing management said, “Oh yeah, we can. We got to get this thing out the door.”
To shed that culture, there’s probably a fair number of upper management people who need to go, and Boeing needs a new and active board of directors to push the management. They must have a system where the line workers, the engineers, the safety supervisors, the quality people all feel absolutely free to whistle blow and report problems — and be rewarded for doing so. I’d have all of management take a 10% pay cut and put that money in a fund for people who report quality or safety problems. You could change the culture fairly quickly that way, if it was clear that is the priority instead of “Watch the stock ticker,” or “Jam these things out the door as fast as we can.”
Kelly Ortberg may be the person who can get Boeing back to where it used to be, but the problems aren’t limited to the MAX. There are also ongoing production delays and problems with the 787 in South Carolina. [Boeing CFO Brian West told investors in January that plans call for increasing monthly production from five to seven “sometime this year.” — CH] Boeing should hire an outside group to come in and audit them. These experts could come in and say, “If you really want to make safety and quality your highest priority, here’s the things you need to do internally to make that happen.” Also, have the experts look at what their suppliers are doing and what needs to change there. [Boeing in early 2024 appointed former U.S. Navy Adm. Kirkland Donald to “conduct a thorough assessment of Boeing’s quality management system for commercial airplanes.” The company says that review is ongoing. — CH]
The other piece of this is transparency. I haven’t seen Ortberg or anybody else in senior management give interviews where they talk at length about changes that they’re making or have been made to increase the safety and quality culture. They need to essentially run a public relations campaign. Bring in the press. Let reporters walk the line and talk to the workers without a supervisor looking over their shoulder. Now, Boeing has done some retraining of workers with special emphasis on safety, so I would hope that things are better at the line. But they have to show the world that things really have changed, if they have changed.
Boeing can recover, but it’s going to require a gargantuan and transparent effort. This was once the greatest aerospace manufacturing company in the world, and they need to get back to that gold standard.
The first thing I’d like to see is some active trust building and trust repairing with the public. Take the February announcement that Stephanie Pope will now just be head of Boeing Commercial Airplanes instead of also having the dual role of Boeing’s company-wide chief operating officer. In statements to the press, Boeing indicated that this was done to focus on 737 MAX production, but it could have been explicitly discussed in relation to Boeing’s commitment to safety. Instead, the company has largely left the public to draw their own conclusions.
Trust is not just a cognitive assessment; there’s an emotional component to it, a gut reaction. That’s why the stories about Boeing’s machinists going on strike and the astronauts who rode on the Starliner capsule having to stay longer on orbit have gained so much traction — it’s the human element. And with all the aircraft-related incidents that have happened recently, the public is feeling very vulnerable. So this is an opportunity for Kelly Ortberg and Boeing to be transparent about the changes they’ve made, to show they understand those concerns and demonstrate that they take the public welfare seriously.
On the business side, there needs to be tighter control of production and quality assurance. In the past few decades, Boeing had started to rely on external suppliers a lot more, and its supply chain has become massive. That model works in other industries, but it’s difficult in a safety-critical one like aviation. I see Ortberg trying to correct this by reacquiring Spirit AeroSystems, for instance.
Strong control over production and quality should be reflected in the organizational culture as well. There needs to be a restructuring so all the decision making and information is coming from a central place. Boeing’s realignment of its engineering chain of command is a good example of this. [Boeing in September 2019 announced this shift in its reporting chain, where every engineer would report to another, up to chief engineer Greg Hyslop. — CH] If the employees see leadership taking that accountability, then the employees will start regaining their trust in the system and can provide powerful testimony to the general public. When leadership comes out and says “We’re trustworthy,” people will always take that with a grain of salt. But if it’s employees speaking out and saying “We’re proud of our work and the company we’re a part of,” that will help shift the public perception, especially in the age of social media.
On the other hand, employees are very attuned to any differences between the stated or publicly espoused culture — what leadership is saying — and the actual enacted culture that is occurring. Think of the news reports about employees reporting problems and getting passed over for promotions afterward. That culture is very at odds with what Boeing leadership has said about how people are encouraged to speak up. So if the employees don’t see evidence of a new way of doing things, they aren’t going to change their behavior and help bring about that culture change needed to improve safety and rebuild trust.
There are a lot of theories on why things got to where they were, and Kelly Ortberg has talked about those. We were chasing a delivery rate and as a result, work traveled to the right on the schedule and tasks were completed out of sequence. There were issues in terms of how we managed our subcontractors, and we let defects come into the factory and then we dealt with them there.
Boeing has all the right changes underway to address those problems, but it’s a big company. It’s like turning an aircraft carrier — it takes a long time, but it will turn. So the most important thing is to stay the course. In 2019, one of the things we did after the MAX crashes was realign the company so that every engineer reported to another engineer all the way up to me. That achieved a degree of independence for engineering and was important to strengthening the engineering culture of the company.
Continuing this culture change will require constant reinforcement all the way from the CEO and the board to the individual employees. Quality is a lot like having a security clearance: It resides with the individual and the choices they make. So the mission has to be owned by every engineer, every mechanic on the production floor, every quality inspector. Similarly, leadership has to create an environment where if people make a mistake, they believe that they can speak up without fear of punitive action. When I worked in Boeing’s missile defense programs, we gave everybody a halt card that they could throw if they saw something they weren’t comfortable with. Then work had to stop until that issue was dealt with. We’ve got to have that same attitude across the company now, where we’re willing to miss a quarter’s deliveries because somebody raised a question on the factory floor. Now, the nature of the work in our industry means there will always be pressure to meet deadlines, but we can’t let that cause people to make bad decisions. The financials have to be a lagging indicator of progress but never take precedence over quality and safety goals.
A big near-term priority is to get 737 production stabilized, because that comprises the majority of orders waiting to be fulfilled. Then get the entire commercial airplane business stabilized. That will generate the cash needed to get a new airplane going. It’s important for the business, but also so important for the workforce. You’ve got to build excitement and hope, and the best way to do that for a bunch of aerospace people is a new airplane.
I still believe Boeing has the best engineers in the world. Yes, there were bad design decisions made on the MAX based on bad assumptions. [Former CEO Dennis Muilenburg told a congressional panel in 2019 that Boeing “made some mistakes” in designing the MAX, specifically in designing the Maneuvering Characteristics Augmentation System software to take input from only one of the two Angle of Attack sensors — CH] We’ve learned from that. That’s why you hear Kelly say that MAX production will be back at 38 a month when they’re ready. Wall Street hates hearing that, but it’s the right answer. I think they’ll be successful; they’ve just got to stick with it even when the criticism comes.
Boeing used to be the gold standard for human factors. Look at the 757 and 767 cockpits; pilots were directly involved in their development from the design to testing to deployment to training. Since then, the company has made a series of decisions that eroded and decentered human factors, and that in part is what led to the MAX crashes. The Maneuvering Characteristics Augmentation System that drove the noses of the planes down was poorly designed, it wasn’t listed on the pilot manuals, and the Lion Air and Ethiopian Airline pilots never knew the software existed.
For our report, we reviewed 4,000 documents from Boeing, visited six of the company’s facilities and interviewed 250 employees. Our 53 recommendations are a road map to building a strong safety culture with human factors at the center of it, so I’d advise everyone in Boeing leadership to read it. I was encouraged to hear that they implemented one of our recommendations last year by hiring a chief human factors engineer, former astronaut Nicholas Patrick. But for him to make a difference, he must be able to sit at the table with the chief engineer and have his voice carry equal weight. If the structure of the airplane is king, as they say at Boeing, then human factors has to be queen at least.
As far as regaining the public trust, the very first step is for Boeing to regain the trust of its employees and their unions. In our employee interviews, we saw a disconnect between the rhetoric of the C-suite and what people experienced on the shop floor. So even if the leadership believes that safety is a priority, it appears that message is not trickling down. We were wrapping up our report when the Alaska Airlines door plug incident occurred in early 2024, so it wasn’t part of our review. But it amplified the expert panel’s concern that the safety-related messages or behaviors are not being implemented.
Bringing Boeing headquarters back to Seattle would help tremendously with that. Give the executives offices in Renton on the shop floor so they’re really close to where the technical work is happening. Change the makeup of the board of directors to reflect an emphasis on human factors and system safety. Don’t just appoint lawyers, former governors or business people; get technical experts who understand the technology and have experience in safety management systems. Get people from other safety-critical industries — nuclear power and oil refining — with fresh ideas about how to improve the safety culture and provide lessons learned from their own experiences.
Change is possible, but only if it starts at the top, and only if the CEO and board of directors become personally involved.

About cat hofacker
As acting editor-in-chief, Cat guides our coverage, keeps production of the print magazine on schedule and edits all articles. She became associate editor in 2021 after two years as our staff reporter. Cat joined us in 2019 after covering the 2018 congressional midterm elections as an intern for USA Today.
Related Posts
Stay Up to Date
Submit your email address to receive the latest industry and Aerospace America news.
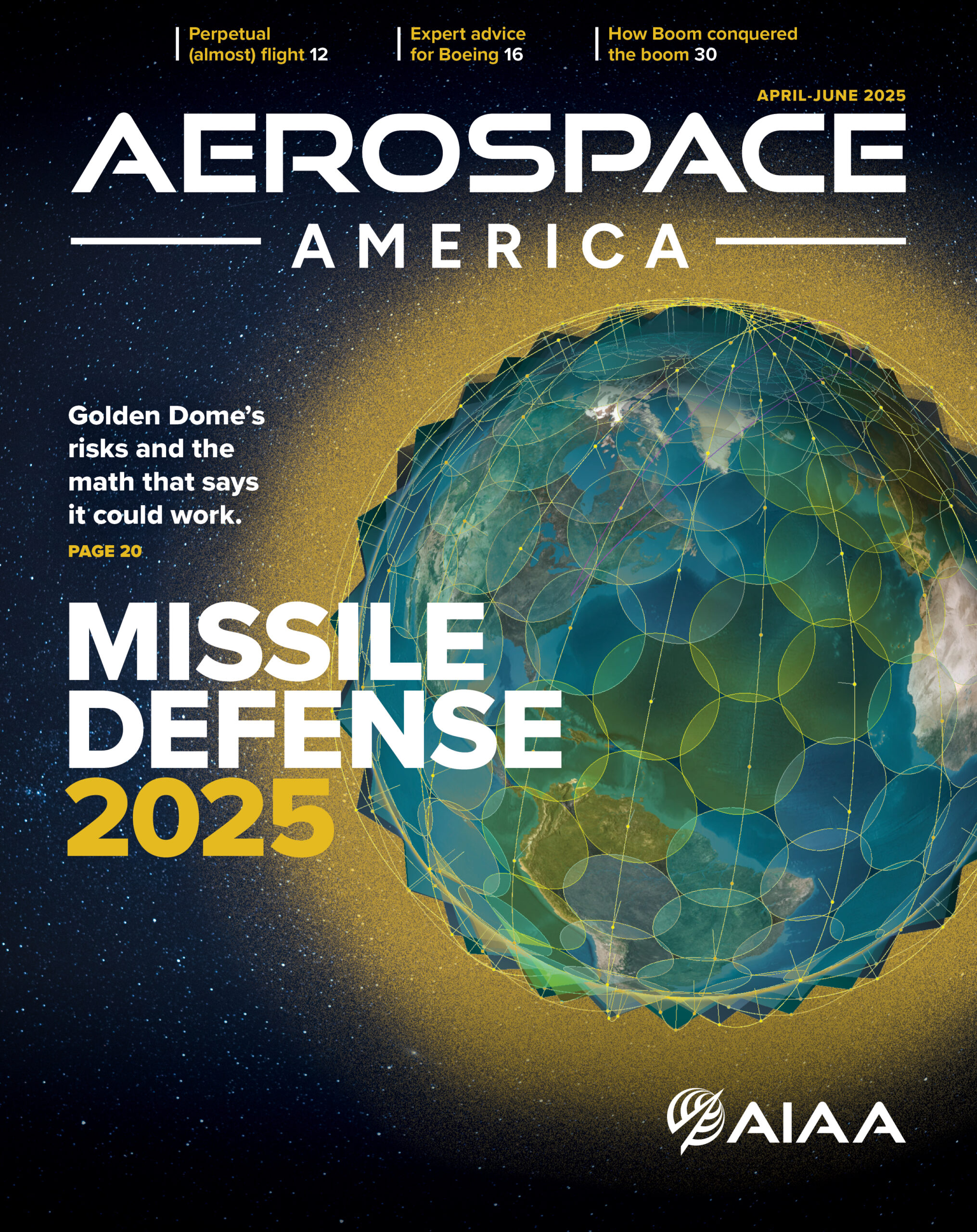