Stay Up to Date
Submit your email address to receive the latest industry and Aerospace America news.
A look at the payoffs and challenges of removing wires from airlines
If you removed all the wires from a widebody passenger jet and strung them end-to-end, you could connect St. Louis to Chicago or London to Amsterdam, distances of approximately 500 kilometers. If you rolled these 100,000 wires into a ball with the harnesses that hold them to the aircraft structure and put the ball on a scale, it would tip to nearly 7,400 kilograms or about 3 percent of the aircraft’s weight.
Many of these wires supply electricity to components, but many others transmit operational data, including avionics, flight-control commands and sensor data on the performance of components like pneumatic and hydraulic systems. Research engineers think that in five years they will have cleared enough technical and regulatory hurdles to begin replacing many data-carrying wires with wireless transceivers.
First to go would be wiring for non-avionics functions, such as control of cabin lighting and passenger audio-video equipment or devices gathering routine health-management data from around the plane. Next might be safety-related wiring linked to smoke detectors, emergency lighting, cabin-pressure sensing and avionics, and eventually even commands that move the plane’s flight-control surfaces.
All told, it might be possible for a modern widebody to shed up to 1,800 kilograms of wiring, according to Mauro Atalla, vice president for engineering and technology at United Technologies Corp.’s Sensors and Integrated Systems division in Minnesota, one of the companies researching internal wireless communications for airliners.
Removing that much wiring is an ambitious goal, driven in part by a pressing desire among airlines to accommodate more and more health-monitoring equipment to identify failing parts before they pose a safety risk or disrupt airline schedules. The shift toward wireless communications also would enhance safety and make it easier to upgrade components, advocates say.
Some of the world’s top avionics and airframe experts have taken up the challenge under a project called WAIC, short for wireless avionics intra-communications, coordinated by Texas A & M University’s Aerospace Vehicle Systems Institute. The work is self-funded by participating organizations and includes a growing list of avionics companies and aircraft manufacturers.
U.S. component suppliers Honeywell and United Technologies have been involved, as have Airbus, Boeing, Bombardier of Canada, GE Aviation, Embraer of Brazil and Gulfstream. Most recent to join are NASA, Lufthansa Technik of Germany, Thales of France and Zodiac Inflight Innovation of California and Germany. They will contribute their expertise to laboratory and flight tests.
How might a wireless system work? United Technologies, better known as UTC, agreed to describe its approach for us. Transceiver modules weighing less than 13 grams would be installed on components throughout the plane. Each would send data from the component or receive commands from the flight crew or automated systems.
To power these modules, UTC is considering different methods. Power could be supplied by a long-life lithium battery or by harvesting ambient energy and storing it in super capacitors. Any batteries would be non-recharging to avoid risks of overheating and fire.
These transceiver modules, or nodes, would be connected to remote data concentrators, weighing less than 200 grams, located strategically around the plane. These concentrators, similar to routers in homes and buildings, would be powered by the aircraft’s electrical system. They would collect data from (or send it to) transceiver modules and route it where it needs to go. That could mean to the aircraft interface device for transmission to the ground by radio, broadband or cell network. If the crew needed to see the data, it would be transmitted to a cockpit tablet interface module that would be connected wirelessly or by wires to tablet PCs for display to the pilots.
The WAIC research is aimed at the boldest part of the wireless shift, which would be transmission of data related to safety and regularity of flights. Passenger entertainment and communications are going wireless too, but with different systems, although partly for the same reasons: to reduce weight, cost and complexity.
The need for replacing wiring is increasing, especially for widebody aircraft. In 1984, a Boeing 767-200ER had 140 kilometers of wiring. Today, a modern twin-aisle aircraft like the Boeing 787 has about 500 kilometers of wiring. Wiring weight on a single-aisle jet is about half the twin-aisle total, but the proportional burden is the same.
David Redman heads the Aerospace Vehicle Systems Institute’s efforts to coordinate research on WAIC. He recalls it took from 2008 to 2015 to take the first regulatory step: securing a dedicated WAIC frequency of 4,200 to 4,400 megahertz from the World Radiocommunication Conference, which meets every three to four years to make decisions about radio spectrum.
Redman is coordinating research to help the RTCA, an association founded in 1935 as the Radio Technical Commission for Aeronautics, to establish performance standards for WAIC equipment. A key aim is to ensure that WAIC applications won’t interfere with those on other aircraft, with each other or with radio altimeters, which derive altitude by measuring the time it takes a radio wave to reflect from the ground and return to the plane. All of these devices operate in the same 4,200 to 4,400 megahertz band.
Atalla of UTC expects the minimum operational performance standard for WAIC to be developed by mid-2019. Redman expects certified WAIC applications in about five years.
Wireless nodes must be light, small, low power and cheap if they are going to be attractive and realistic replacements for wires. How to power the nodes remains a major question. Lithium batteries and harvesting ambient energy are among the options, but there is a third idea. Passive radio-frequency identification tags might remain dormant until powered briefly by signals from the RFID readers that interrogate them.
For both nodes and power, Redman hopes that WAIC can piggyback on advances in consumer or other industrial markets that have much higher volumes on which to recover investments.
As confidence in the technology grows, some of the wires that carry data in fly-by-wire jets might be replaced. That would be a big breakthrough, because safety-related connections now require two or three redundant wires to ensure functions if one of the wires chafes or fails for some other reason. If a wireless link were installed in place of one wire, the result would be what Redman calls a dissimilar redundancy, which is often a preferable strategy. The same safety data would be carried by both wire and wireless connections, rather than relying solely on wires that could all fail for the same reason.
And Redman notes that the weight reduction for WAIC might be proportionally greater than if engineers could reduce the wiring required to supply electricity to components. Wires that carry data, including fiber-optic cables, are typically heavier and more expensive and complex than those that carry electric power.
Redman observes that eliminating wires also frees up space, always at a premium on aircraft. Wires take up space themselves and need additional room for their separation.
Upgrading equipment on today’s jets can be a major undertaking, but with the new approach mechanics would just have to replace the component and attached module, rather than disentangle, remove and safely replace bundles of wires. Especially for new aircraft, installing wireless devices could be much easier than installing all those connecting wires.
On top of these benefits, advocates suspect there will be payoffs that haven’t yet been anticipated. In today’s designs, sensors need wires, and that limits where they can be placed. Functions that are not practical or economic today with wired systems might suddenly make sense.
Potential wireless safety uses
The Aerospace Vehicle Systems Institute says wireless technology potentially could be used throughout an aircraft, including these safety applications:
Smoke detection
Door sensors
Fuel tank and line monitor
Temperature
Engine sensors
Humidity and corrosion detection
Cabin pressure
Emergency lighting
Ice detection
Flight controls position feedback
Air data
Flight deck and cabin crew imagery/video
Landing gear
Avionics communications bus
Structural health monitoring
Active vibration control
Related Posts
Stay Up to Date
Submit your email address to receive the latest industry and Aerospace America news.
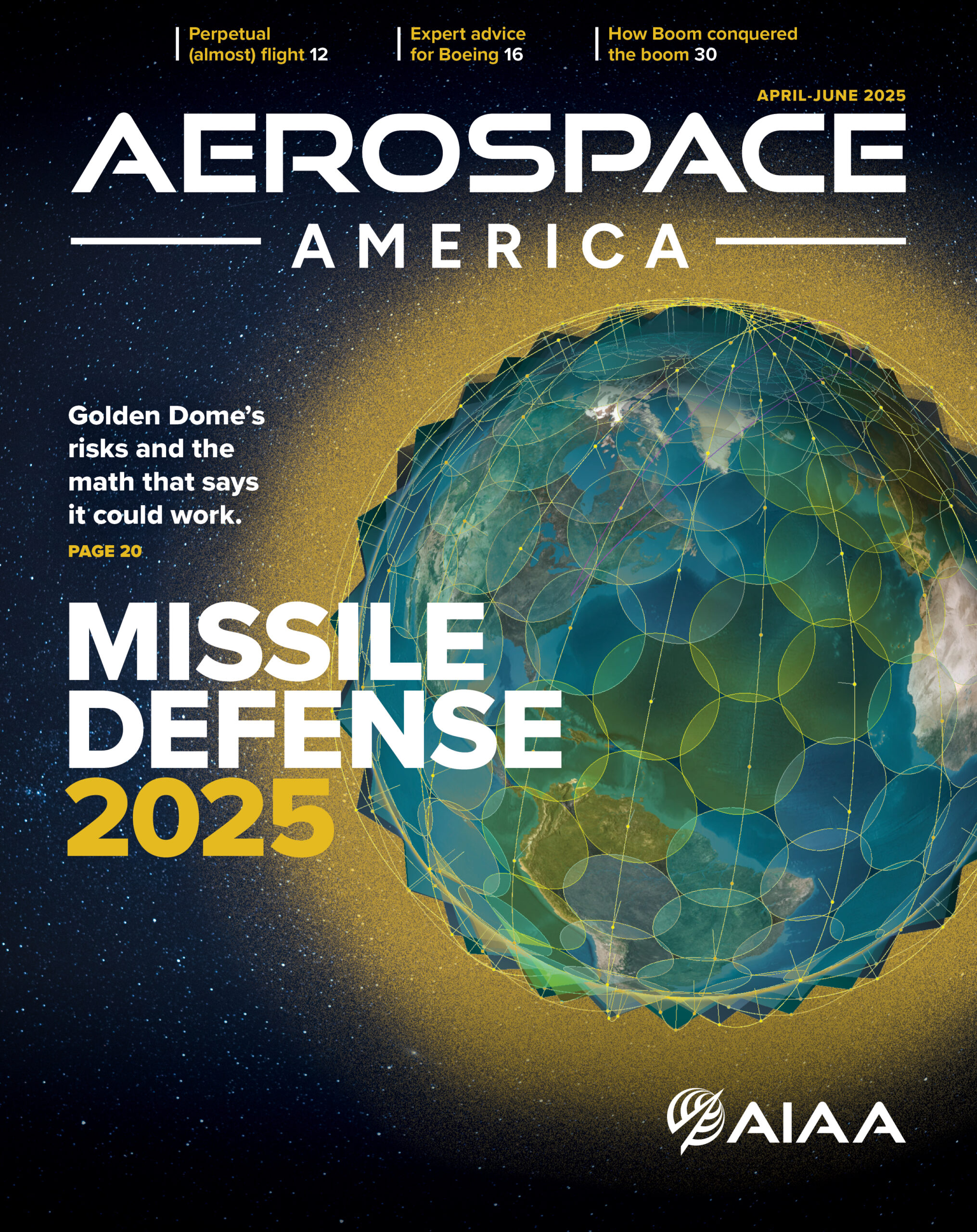