Stay Up to Date
Submit your email address to receive the latest industry and Aerospace America news.
Now that Airbus has chosen the design for its future ZEROe airliner, the next major milestone is a planned 2027 ground test of the engine components. Keith Button spoke to engineers and program executives about the work ahead and the revised target for beginning passenger flights.
If all goes well, in two years, Gregg Llewellyn will be peering through a window from the control room in an Airbus facility just outside Munich. On the other side of the glass, attached to a metal frame the size of a small car, will be an early version of the components for a hydrogen-electric engine that the company hopes will someday propel a 100-passenger plane with a range of 1,850 kilometers and no carbon emissions.
While this setup doesn’t mimic the final planned flight configuration for the engine, a successful demonstration would nevertheless mark a “major step forward,” says Llewellyn, who leads the ZEROe hydrogen plane project that Airbus began in mid-2020. The company spent nearly five years assessing different airliner concepts before announcing its choice in March: a hydrogen-electric design driven by four engines. In this configuration, liquid hydrogen will be pumped from two large tanks to the engines, each of which contains fuel cells to convert the hydrogen, combined with atmospheric oxygen, into electricity. This electricity will flow to a motor control unit, which in turn will send the current to an electric motor that will drive a gearbox, which turns a propeller.
“With fuel cells, we believe we’ve found the right technology,” Llewellyn says. The concept beat out the other three contenders [see chart below] — all of which relied on direct combustion of liquid hydrogen. That was partly because hydrogen-electric propulsion would produce no nitrogen oxide emissions and potentially no contrails, both of which are leading contributors to aviation’s portion of atmospheric warming, alongside carbon dioxide. Electric power also gives aircraft designers more options for how to distribute the propellers across the airframe, he says.
Already, Airbus has revised the original concept it unveiled in 2020, reducing the number of engines from six to four based on early testing that indicated each engine would produce more power per kilogram than engineers initially predicted. Fewer engines will also reduce the overall cost of the planes, says Mathias Andriamisaina, head of testing for the ZEROe technologies.
Despite the progress, it could be another 20 years before the first passengers ride in these airliners. Airbus had been working toward entry-to-service in 2035 but dropped that target earlier this year due to what executives have described as the slow development of a global hydrogen supply network. While a new official target date has yet to be announced, Airbus predicts that the fuel market will take five to 10 years to mature, Bruno Fichefeux, head of future programs, said at a company summit in March. This would put the ZEROe aircraft’s debut sometime between 2040 and 2045.
Engineers could use that extra time. Among the challenges: proving that they can transform today’s bulky, heavy hydrogen-electric components suited for ground transportation and industrial uses into light, compact engines with more power per kilogram.
And so, chief among their tasks before the 2027 demo are identifying ways to boost engine power per kilo, manage fuel cell heat more efficiently and develop software that can control engine power during flight. Weight reduction goes hand in hand with these goals. Over the course of a year, engineers conducted some 1,000 ground tests over 500 hours with early engine components. The setup was similar to that planned for the 2027 demo, but with key differences. First, an industrial high-pressure tank supplied room-temperature gaseous hydrogen — not liquid hydrogen at cryogenic temperatures, as will be required for flight. Likewise, the off-the-shelf engine components were state-of-the-art for fuel-cell cars, trucks or boats, but they aren’t designed with the size and weight considerations for aircraft, Andriamisaina says.
“You can use the boat or ship propulsion system,” he says, “but it’s so bulky that you will never take off.”
Plans call for swapping out these components by the end of this year for aircraft-specific components, Llewellyn says, including upgraded fuel cells, electric motors and gearboxes. Also, the stainless steel tanks will be replaced with lighter ones that can keep the hydrogen at the required minus-253-degrees Celsius for it to remain liquid. By next year, Airbus plans to reduce the size of the test engine components by roughly half — shaving off weight by constructing fuel cells and motors out of lighter materials, Andriamisaina says.
“One of the challenges is to make them all very, very compact.”
Tank design will play a part here as well. Liquid hydrogen has several advantages over gaseous, starting with the lighter weight of a double-walled, vacuum-insulated tank versus the bulky tank needed to keep the gaseous fuel pressurized, typically at 350 to 700 times sea-level air pressure. So Airbus and Air Liquide Advanced Technologies of Paris are testing whether the tanks and their piping can be constructed from aluminum alloys and carbon-reinforced plastics, Llewellyn says.
While relatively new to aerospace, these double-walled tanks were adopted years ago by other industries. BMW’s Hydrogen 7 sedan from the early 2000s and Norled’s hydrogen-powered MF Hydra ferry that Norway debuted in 2023 rely on the technology, as do household thermos bottles. “It’s not a fundamentally new technology, but it’s certainly new for aerospace and commercial aviation applications,” Llewellyn says.

Other benefits of liquid hydrogen are that it packs more energy per liter than pressurized hydrogen gas, and it can boost overall engine performance by doubling as coolant for its electronics. For instance, keeping the engine circuits at near-cryogenic temperatures reduces electrical resistance, Llewellyn says, which allows for “nearly unimpaired” power transmission. The company’s Airbus UpNext subsidiary is designing a cooling loop that would circulate hydrogen-chilled helium to the engine’s cables, motors and electronics to induce superconducting properties.
That’s not to say that a fuel cell engine doesn’t come with challenges, Andriamisaina says. There’s heat management, for one. “When we are using conventional jet engines, the heat is just ejected to the outside,” he says. In contrast, fuel cell engines require temperature management via powerful heat exchangers. Typically, metal tubing circulates a liquid coolant between the warm fuel cells. The warm coolant flows through a heat exchanger cooled by ambient air and recirculates.
This function will be especially important for the ZEROe aircraft, Andriamisaina says, because for every megawatt of power generated by the fuel cells, they will also produce 0.4-0.6 megawatts of heat. Engineers believe they will need a combined 8 megawatts of engine power for the 100-plus-passenger plane — that’s 2 megawatts per engine, with up to an additional 1.2 megawatts of heat.
Off-the-shelf exchanger components won’t be up to the task, so they’ve been bench-testing prototypes of alternative heat exchangers in France, Germany and Spain. Among the options: a single large cooling loop versus several small loops and oil versus glycol-based coolants. In general, the smaller the heat exchanger and the less cooling liquid it needs, the greater the improvement in engine power per kilo.
Also to be determined is the shape of the air intake channel on the engine’ exterior, which must direct outside air through the heat exchanger to an air compressor feeding the fuel cells without imparting significant drag on the aircraft. For wind tunnel tests in Spain, engineers constructed channels out of wood, resin and metal and attached them to the top, bottom or sides of scaled-down engine models. The models were then placed in the wind tunnels, where high-speed cameras recorded the air flow around and through the engines, as traced by strands of smoke or wire, Andriamisaina says. Tests were conducted at various temperatures, wind speeds and angles of flow to simulate takeoff, landing and cruise phases of flight. Once fed into computer models, the test results showed engineers in detail where the shapes disrupted air flow.
And then there is software, which will be essential for controlling the propulsion power of the engine, Llewellyn says. The fuel cells will produce electric current by combining oxygen from the ambient air — pulled in by the air compressor — with liquid hydrogen from the on-board tanks that has been vaporized to gas. A motor control unit changes the continuous electrical current produced by the fuel cells into alternating current that can be controlled, which then turns the motor, which powers the gearbox, which powers the propellers.
The control software must be able to manage failures of any of those individual components, Llewellyn says. “You want to be able to continue safe flight and landing in the event of any of those kind of failures.”
In such a scenario, the software may need to shut down adjacent components or redirect power from redundant fuel cells or electrical units in the same engine. So engineers are conducting ground tests that simulate the failure of individual components, as well as simultaneous failures of multiple components, to see how the software responds. Several versions of the software have also been tested for controlling engine power and fuel efficiency via the supplies of hydrogen and oxygen to the fuel cells and via the electrical power through the motor control units, Llewellyn says.
For throttling, for example, regulators at FAA and the European Union Aviation Safety Agency, or EASA, require that engines be able to go from idle to full thrust in eight seconds once commanded by a pilot.
“What we have to do with a fuel cell engine is show that we can achieve the same sort of requirements as what a gas turbine engine can achieve,” he says.
For the 2027 demonstration, the engine will be more tightly packaged than the current ground testing setup, but not yet small enough to fit in an engine fairing, Andriamisaina says. A dynamo will stand in for the propeller, so the engine can operate under simulated propeller loads for takeoff, cruise flight and wind gusts, and the loudest noise emanating from the engine will be the whoosh of the air compressor.
Even if all goes as planned, there will still be plenty more to do before the first hydrogen airliner is ready to take to the skies.
“2027 is not the end of the story,” Andriamisaina says.

About Keith Button
Keith has written for C4ISR Journal and Hedge Fund Alert, where he broke news of the 2007 Bear Stearns hedge fund blowup that kicked off the global credit crisis. He is based in New York.
Related Posts
Stay Up to Date
Submit your email address to receive the latest industry and Aerospace America news.
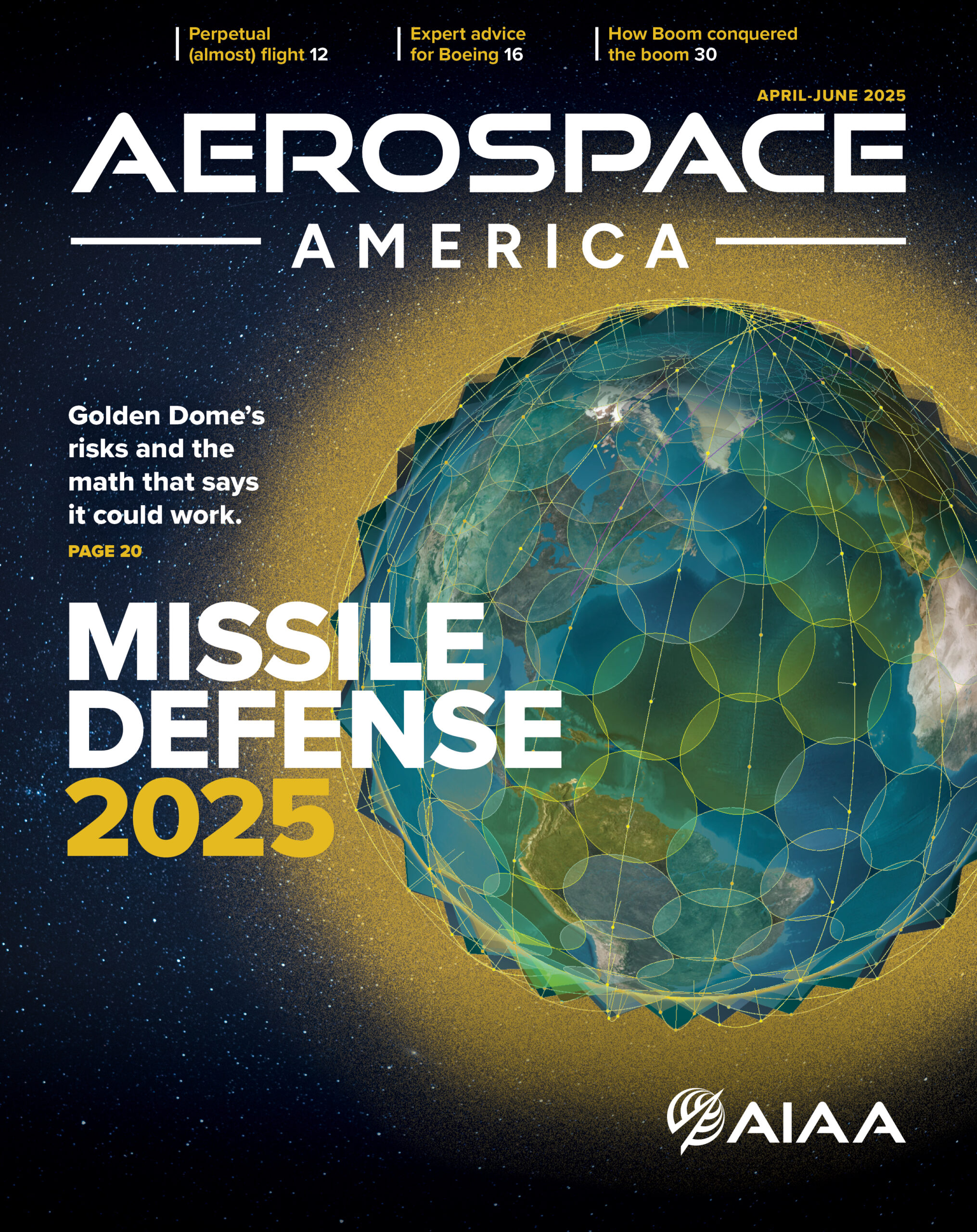