Stay Up to Date
Submit your email address to receive the latest industry and Aerospace America news.
Businesses are racing to meet an FAA mandate for training
Despite very different circumstances, a common thread runs through the fatal crashes of a Colgan Air aircraft near Buffalo, New York, in February 2009 and of Air France Flight 447 off Brazil just four months later. In each case, the plane lost lift and fell through the sky, with the pilot’s reactions inadequate to save the plane from this aerodynamic stall. The aviation world was stunned that 377 people could lose their lives in a span of months because airline pilots, who are among the most selectively recruited and best trained of airmen, could not recover from stalls under admittedly difficult and confusing conditions.
These events precipitated years of discussion and rulemaking by FAA about the need to train pilots to recover from stalls in those rare cases when they fail to avoid this deadly form of upset. Now, just two years before a tough new FAA mandate on airlines is set to go into effect, simulation companies and airlines are pursuing two divergent technical approaches. One approach requires obtaining test-flight records from aircraft manufacturers, while an alternative relies on computational fluid dynamic models, wind tunnel tests and other data.
How did we get here?
Historically, student pilots have practiced stall recovery in light aircraft early in their training curriculum. Later, in a simulator designed to replicate a passenger plane, they would train for stalls only to the point of activating a horn, buzzer or stick shaker, a mechanical vibration in the control yoke that warns the pilot.
“It was thought that was good enough,” explains Dann Runik, executive director of advanced training at FlightSafety International, a New York-based company that builds simulators and operates dozens of learning centers around the world for pilots of airliners and business planes.
In the view of most observers, Air France and Colgan Air proved that this traditional approach was inadequate. The U.S. Congress in 2010 ordered the FAA to enhance pilot training. In 2012, the FAA issued an “Advisory Circular” listing recommended steps pilots should take if they find themselves in a stall. In 2013, the FAA released a final rule that required U.S.-certified airlines to begin training their pilots on recovery from stalls and other upsets by March 2019 and train all their pilots by the end of March 2020. To improve safety, many business aircraft operators also seek this training. In announcing the final rule, the FAA noted an irony: Just a month before the Colgan crash, the agency, in accordance with the federal rulemaking process, had issued a notice of proposed rulemaking for training improvements. Vulnerability to stalls also has been a concern in Europe, and since May 2016, the European Aviation Safety Agency, or EASA, has required all European airline pilots to receive training, chiefly in stall detection and prevention.
Meeting the mandate
Why is the FAA mandate still two years off? One reason is the complexity of simulating the interactions of a specific model of plane during a stall and recovery. Most stalls begin as nose-up incidents. If a pilot raises the plane’s nose and wings too high relative to the direction of flight, called a high angle of attack, or AOA, the air flowing across the wings separates from the surface. This reduces lift and increases drag, and the plane starts to fall. The exact angle at which a stall begins depends on the type of plane, airspeed, banking angle, air density and many other considerations. FlightSafety’s Runik says his company takes into account about 120 parameters to create a full-stall simulation, which is one that spans from the start of a stall through recovery.
To convey the scope of the problem ahead of the mandate, David Gingras, vice president of Bihrle Applied Research, a 26-person company in Virginia, estimates that today only about five simulators out of 100 or so full-flight simulators in the U.S. contain the data necessary for full-stall simulation. No one has an exact count, because the industry does not keep an official record of simulators and their attributes.
The FAA has put the cost of upgrading these simulators for scheduled airlines at about $80 million.
As yet, there is no consensus about the best strategy for updating all those simulators. Some airlines and simulation companies are talking with aircraft manufacturers about the availability and cost of obtaining stall data collected during testing of each model of plane. Before a new kind of plane carries passengers, manufacturers typically fly an instrumented test version to the brink of stall, or in some cases past stall, and record the data.
Obtaining that data is FlightSafety’s strategy, and the company has started with the business-aircraft market. Its simulators can now emulate Gulfstream and Dassault business jets and Pilatus turboprops. The first such data obtained came from a partnership with Gulfstream, and the experience afforded lessons for FlightSafety. “It was massive data we never had before and nearly choked our computers,” Runik says. It took seven months of data cleaning and computer upgrades to exploit the data wealth, but now it takes much less time to load new aircraft data.
To apply the same approach for the airlines, the firm says it will have to obtain test data from more manufacturers, including Boeing, Airbus, Bombardier, Embraer and ATR. FlightSafety is now in discussion with airline prospects, and will be seeking test data from manufacturers.
Training for recovery
FlightSafety starts its full-stall training by teaching pilots to distinguish stalls from other potential sources of upset, including wind shear, wake turbulence and the buffeting that can happen when a subsonic plane approaches Mach 1. In some cases, pilots have only four to five seconds to recognize the specific threat and begin correct recovery actions.
If the plane is in a stall, pilots must immediately reduce AOA. Therefore, one key is for a pilot to always know the AOA. This angle is not displayed in most aircraft, so FlightSafety trains students to derive AOA from the flight path vector shown on the attitude director indicator cockpit display or on the head-up display, if the plane is equipped with one. AOA is the difference between the pitch of the nose and the flight-path vector.
If the vector is unavailable on these displays, the firm trains students to estimate AOA using pitch and vertical velocity. For example, descent to an airport at approach speed yields a vertical velocity of about 700 feet per minute, roughly a minus-3.0 degree flight-path angle. If pitch is positive 3.0 degrees, the AOA would be about 6.0 degrees.
Apart from slowness in identifying and reacting to dangers, Runik says the most common error happens when stalls occur close to the ground, as in a banking or circling approach. “They see trees rushing up, and the reflex is to pull back on the stick.” That is a fatal reflex in a stall.
Runik cautions against relying on stall warning and recovery aids in the cockpit, even though full-flight simulators replicate stick pushers, the software that automatically moves the stick forward to reduce the AOA, and stick shakers, the vibration alert. “Stick pushers and other stall-avoidance equipment can be defeated by icing on exterior sensors,” he says.
Runik says pilots who have been through the company’s stall recovery course want to retain “muscle memory” of its lessons, so would like a refresher course every one to two years.
Compromise might be needed
Nick Leontidis, CAE’s group president for civil aviation training, says it will be able to meet FAA’s mandated 2019 and 2020 deadlines, provided it gets the manufacturer test data in time, and he is hopeful that will be the case.
Manufacturers like Boeing and Airbus devote significant efforts to supporting simulators with accurate test data. Even so, Leontidis worries that data on some older aircraft, for example the Boeing 767, may be difficult to obtain. He says the FAA might have to compromise on its recommendation of validating simulations with aircraft-specific flight test data. Luckily, a simulator can be loaded with other aerodynamic data, and a company can be confident that a stall recovery simulation derived this way will be fairly accurate, Leontidis says.
So far, CAE has been doing well with business-aviation operators. TAG Aviation Holdings, one of Europe’s largest aircraft management companies, and another large-fleet European operator, have selected CAE as their training partner. And Dassault has endorsed the firm for upset training to meet the EASA standards.
CAE is focusing first on meeting the European goals of detecting and preventing stalls. “A lot can be taught without data validation,” Leontidis says. “The main emphasis of our training is teaching the science of what causes a stall and the conditions to avoid.” The training includes a four-hour simulation session.
Alternative approach gains traction
Another firm and an airline are moving forward with a different technique, and one that was blessed last year by the FAA. Rather than obtaining actual stall data from manufacturers, Bihrle Applied Research combined its years of experience with military planes with data from computational aerodynamics models and its wind tunnel capabilities. This data was loaded into a separate computer that the company calls a StallBox. This computer was then plugged by Ethernet cable to an Alaska Airlines simulator that replicates the airline’s Boeing 737-800 aircraft. The StallBox alleviates the need to upgrade the computing power of the simulator. Last May, Alaska Airlines announced that the FAA had certified this simulator for training pilots to recognize and recover from stalls.
“We showed stall modeling could be done separate from [manufacturer] data,” Gingras says.
Gingras predicts that data may be unavailable for older aircraft like the Fokker 100, and he says it may be of limited value in many other cases. A stall simulation derived from a small number of actual stalls may be accurate only for those stalls. “The aircraft may not stall that way all the time,” he says.
Although the FAA approved the StallBox only for the 737, Bihrle is working on versions for the Airbus A320 and A330 and Gulfstream G450. He says the firm is receiving many inquiries about its stall model and instructor display as the 2019 deadline gets near. Gingras notes that manufacturer validation data has always been an FAA recommendation, not a requirement, for simulation training. “We provide an alternative.” ★
The FAA required U.S.-certified airlines to begin training their pilots on recovery from stalls and other upsets by March 2019 and train all their pilots by
the end of March 2020.
Related Posts
Stay Up to Date
Submit your email address to receive the latest industry and Aerospace America news.
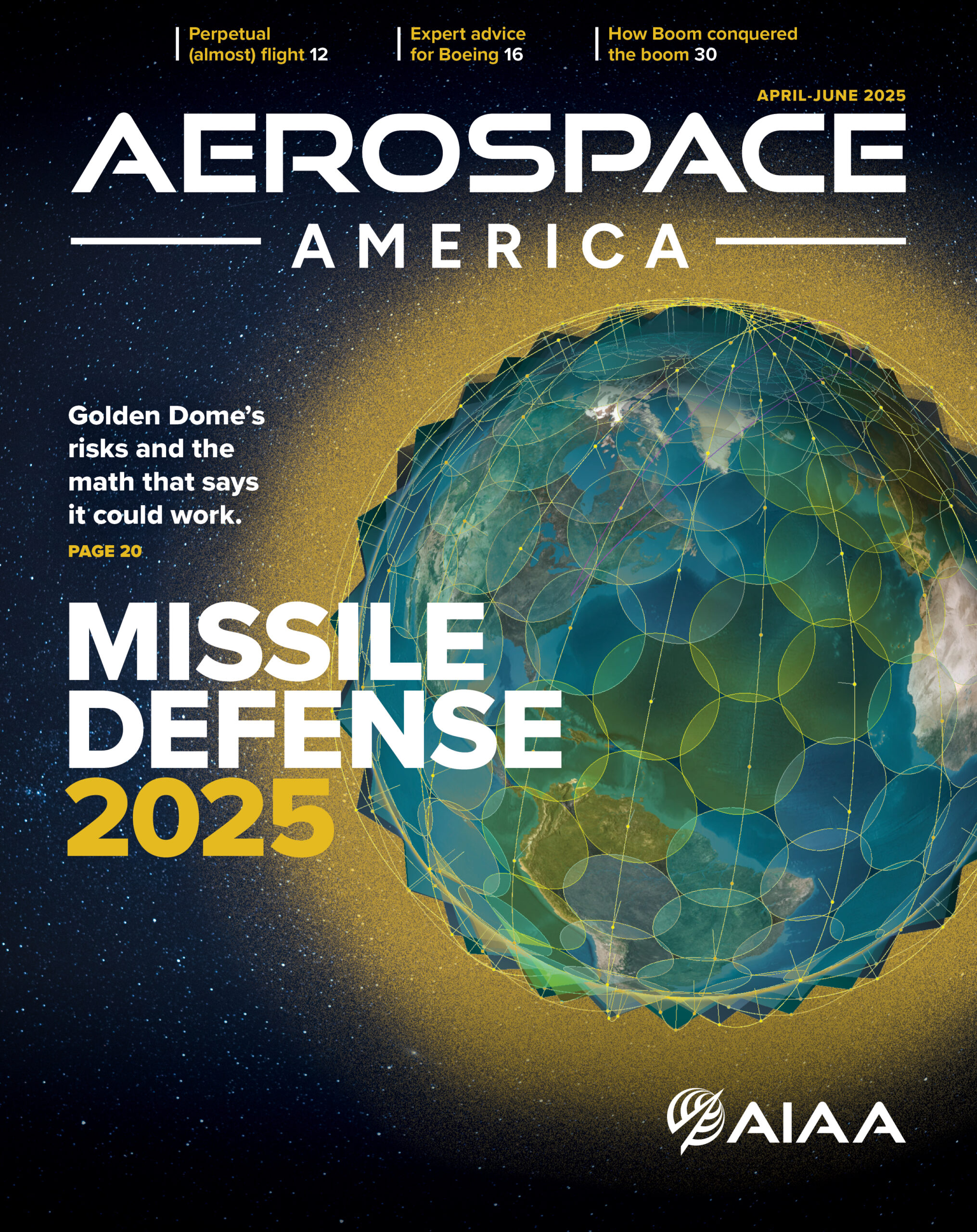
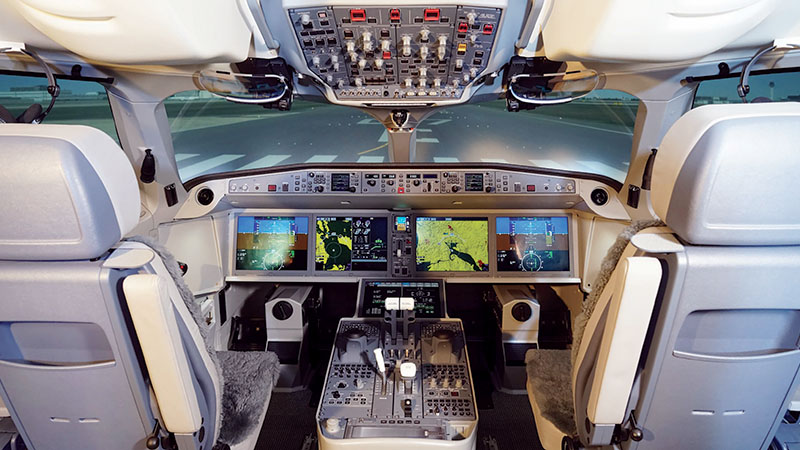
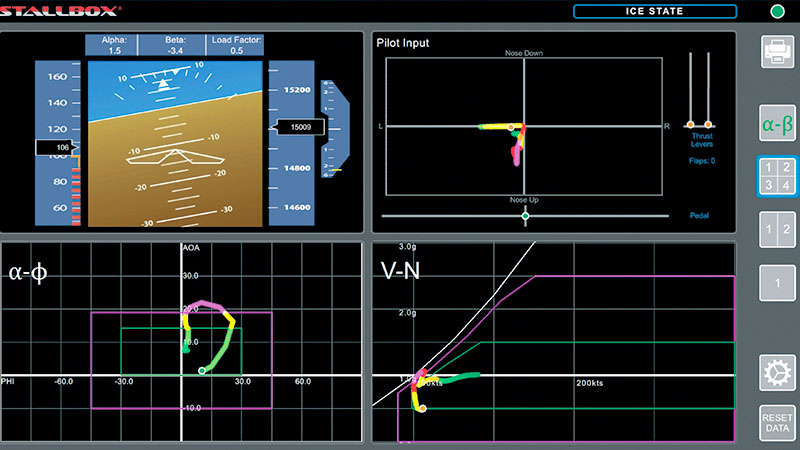
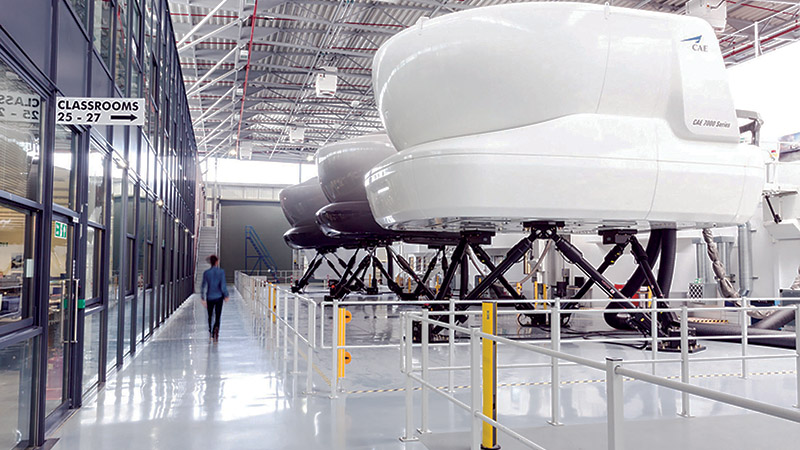