Stay Up to Date
Submit your email address to receive the latest industry and Aerospace America news.
Thirty-five thousand kilometers is a long way up, and that’s the home of nearly 400 satellites that do anything from sending and receiving telephone, internet and television signals to spotting missile launches. Today, those satellites can’t be repaired, upgraded, refueled or rescued if their propulsion fails.
The Pentagon’s first Advanced Extremely High Frequency satellite looked like a $1 billion lost cause when it was dropped off in space in 2010 with a malfunctioning apogee engine. The U.S. Air Force and its contractors are a resourceful bunch, and they figured out how to get the satellite to its final geosynchronous orbit with its less powerful engines. The bad news was that the ride took 14 months.
For decades, operators of expensive and hard-to-reach geosynchronous satellites have wanted the ability to latch onto a wounded satellite like AEHF-1 and maneuver it to its proper orbit. That would be just one scenario. On-orbit servicing would give them the power to replace faulty or out-of-date parts and refuel a satellite to extend its operating life by years, something especially attractive to commercial operators because of the revenue that could be generated.
On-orbit servicing looked like it would soon be a normal part of business in 1997, when Japan’s Engineering Test Satellite-7 (also known as Kiku-7) released a smaller target satellite, chased it down and docked with it, ultimately from as far away as 12 kilometers. Another milestone came a decade later in DARPA’s Orbital Express mission, when a pair of satellites rendezvoused from 400 kilometers away and docked with each other to practice refueling and swapping out batteries and computers.
Now, two decades after the Japanese mission and a decade after Orbital Express, industry executives and DARPA officials say the community is truly on the cusp of making on-orbit servicing a reality in the geosynchronous belt.
Notable this time is the vigorous participation of commercial satellite operators and builders. For industry, the choice is between a brute-force option that could be ready soon to restore propulsion for old or wounded satellites, and other, more complex options that are at least a few years off but could deliver a host of services beyond propulsion.
The nearest term option, a service that Orbital ATK of Virginia plans to debut late this year or early 2019, calls for capturing a client satellite with a Mission Extension Vehicle spacecraft that would take over the propulsion. Intelsat, the Luxembourg-based communications satellite giant, has signed two contracts for the service. Intelsat plans to service its Intelsat-901 satellite, launched in 2001, with this life-extension technology. Orbital ATK also has an idea that’s still years off for a more elaborate strategy, involving propulsion pods that would be attached to satellites. DARPA, meanwhile, is working with Space Systems Loral on a “DARPA hard” concept involving RSVs — robotic servicing vehicles that would be stationed in geosynchronous orbit, the first in 2021. The program is called Robotic Servicing of Geosynchronous Satellites, or RSGS. SES, another Luxembourg-based operator, is considering having one of its satellites serviced under this program.
Dock and drive
When Orbital ATK’s Mission Extension Vehicle satellite arrives in orbit, it will rendezvous with the client and push a probe into the nozzle of the satellite’s main propulsion engine. The probe’s
mechanical fingers will expand to hold the client satellite while the Mission Extension Vehicle pulls it closer at a rate of a few centimeters per second. The adapter ring that once held the client to its launch vehicle will press on the servicer’s three stanchions, locking the two spacecraft together. For the next five years, the servicer’s ion thrusters will keep the satellite in its correct orbit with its antennas properly oriented.
“It’s a pragmatic, proven technology. And lots of satellites run out of fuel in 15 years, but still work. Docking can give them five more years of life,” Intelsat CEO Stephen Spengler says.
Orbital ATK, which is testing the technology at a lab in Virginia, designed the Mission Extension Vehicle from its GEOstar 3 commercial satellite frame, or bus. Engineers equipped the 2,500-kilogram servicing satellite with optical and infrared video cameras to spot the client satellite from 40 to 50 kilometers out, with the precise distance measured by a LIDAR laser-ranging device. These sensors will feed data to an onboard computer and ground controllers who steer the servicer through a series of waypoints to the client satellite.
Orbital ATK CEO David Thompson told an audience at the 2018 Satellite conference in Washington, D.C., in March that the servicer can work with about 80 percent of current geosynchronous satellites. Orbital is prioritizing this class of satellites because they represent the biggest value in commercial satellites and it is easy to move among the similar orbits. Low Earth orbiters move in different planes, which would require an orbiter to have lots of fuel to maneuver among those different planes. Another executive said Orbital ATK may eventually provide a servicing vehicle for those satellites too.
Orbital ATK is not alone with the capture approach. United Kingdom-based Effective Space plans to have its 400-kilogram Space Drone per-form a similar life-extension capture of a geosynchronous satellite by 2020.
Orbital ATK’s next step, due in 2021, would be to create a version of the Mission Extension Vehicle with 12 mission-extension propulsion pods and a robotic arm. The robotic arm would attach the Xenon-fueled ion pods, each weighing about 200 kg, to client satellites in the same fashion as the extension vehicle does: by pushing a probe into the nozzle. The vehicle would then draw the nozzle and the pod together. The Mission Extension Vehicle would leave, with the pod attached to the satellite for propulsion. The pods can extend the life of a 2,000-kg satellite, which is relatively small for a communications satellite, by five years. The robotic arm will also do simple repairs of stuck antennas or solar arrays.
This enhanced servicer might someday attach pods carrying new batteries or other internal components, but that would require new satellites to be designed to accept those components.
Refuel and repair
Also in 2021, DARPA and Space Systems Loral plan to launch their Robotic Servicing Vehicle. It will work with a client satellite to conduct a six- to nine-month demonstration. After that, if all goes as planned, the RSV will be declared operational. Under a partnership agreement, the U.S. government would get a discount from Space Systems Loral on servicing of its satellites until the public investment is repaid. Space Systems Loral would then own the RSV entirely, explains DARPA’s Gordon Roesler, the RSGS program manager. Ultimately, he expects an RSV to last eight to 15 years and service a ratio of approximately five commercial satellites to each U.S. government satellite. That ratio would reflect today’s 5-to-1 ratio of commercial to U.S. government satellites in orbit.
Between now and then, Space Systems Loral will build the RSV based on its SSL 1300 satellite bus, a design that can weigh 3,500 to 7,000 kg, depending on the components added to it. DARPA, working with its contractors, will equip the RSV with servicing tools, including two robotic arms.
Roesler sees an array of goals. For starters, he expects this servicing spacecraft to examine satellites from “inches away”; modify orbits by docking and applying thrust; free stuck antennas and solar panels by applying gentle pressure; and upgrade satellites by attaching new components. Space Systems Loral added a fifth, tougher capability: refueling satellites. This would be done in cautious steps through the same fill-and-drain valve used before launch. Due to insulation and locking wires, the servicer must carefully prepare the client satellite to receive the fuel. “Our robotic arms have tool changers, like socket wrenches,” Roesler explains. “That gives us tremendous flexibility.”
Refueling, in addition to extending a satellite’s operating life, would give ground controllers a new flexibility to maneuver a satellite without fear of running out of fuel. Close inspections could tell commanders whether malfunctions are due to nature, design flaws or hostile action. Such attribution could amount to a powerful deterrent, Roesler says.
Over the long term, Roesler expects satellite manufacturers to redesign satellites to house equipment in modules that can be replaced by an RSV.
The stakes are large. Roesler estimates there are about 300 commercial geosynchronous satellites in orbit costing an average of about $300 million apiece, plus $100 million in launch costs. The U.S. government has put up 50-60 geosynchronous satellites, each worth from $600 million to well over $1 billion. Then there are a few dozen satellites put up by other nations. A bit less than 10 percent of all these satellites could be candidates for life extension or simple repairs, according to Ruy Pinto, deputy technology officer at SES, which has a fleet of 55 geosynchronous satellites and another 12 low Earth orbiters. SES is considering the RSV option.
Assembly of spacecraft in space is not part of the mission set. But Roesler says, “If NASA wants to set up a telescope with big reflectors, they could put a package up and we could manipulate it to show the concept is valid.”
Al Tadros, vice president of space infrastructure at Space Systems Loral, notes that his firm has extensive experience with space robotics, having built components for Mars landers (including an arm for NASA’s upcoming Mars 2020 rover); the space shuttle fleet and the International Space Station. And it built 86 of those 300 commercial GEO satellites.
“Our vehicle will have very flexible robotics, with seven degrees of freedom,” Tadros stresses. He describes the RSV as “the first general-purpose servicing satellite.”
He acknowledges refueling in space will be hard, but says: “Everything in space is hard. We demonstrated refueling on the space station, and we refuel on launch when caps are sealed [and must be robotically opened].” Tadros points to U.S. Navy refueling at sea and Air Force refueling in flight as similarly difficult challenges that have been met.
Pinto acknowledges, “Refueling is tricky, requiring grabbing a satellite, manipulating it to open a valve and inject fuel, all for satellites not designed for in-orbit refueling.”
Benjamin Reed, who was deputy director of NASA’s Satellite Servicing Projects Division from 2010 to early 2018, observes that NASA designed the space station to be robotically refueled and was able to safely access the oxidizer valve. However, “propulsion oxidizers are nasty, corrosive, toxic and explosive.” For satellites not designed for refueling, Reed says approach sensors must be tested in the lighting of Earth orbit, “which cannot be duplicated in laboratories.”
Tadros hopes his first commercial customer will be SES, which is evaluating the proposal. Pinto, the SES technology officer, believes the plan has the advantage of one-shot refueling, after which the servicing satellite moves on to its next client. The best candidates for on-orbit servicing are GEO satellites that were designed to last 20 years, still have a working payload but are running short of fuel.
NASA’s near-term servicing focus has been on life extension, repair and augmentation. Medium-term, NASA wants to design satellites to be more cooperative. “We are intensely focused on making future satellites serviceable,” Reed says. The agency has already developed a cooperating fuel valve, about the same size, weight and cost as existing noncooperating valves. “In the past, it has been excruciating to cut wires and remove caps.”
Further out, NASA wants to assemble equipment in space, for example, to look for life on exoplanets. “Looking into their atmospheres requires a very large light-collection bucket, many times the size of James Webb,” Reed notes, referring to NASA’s James Webb Space Telescope currently scheduled to launch in 2020. One possibility is assembling stacked mirrors in orbit.
Another long-term goal might be redirecting a dangerous asteroid to miss Earth. This could require technologies similar to those used in servicing satellites. So Reed is eager to see servicing develop. “We are on the cusp of doing much more with less.”
The first risk is technology. Rebecca Reesman, a policy analyst at Aerospace Corp., a federally funded research firm in California, argues that well-proved autonomy, navigation, flight software and ground operations are necessary to avoid collisions that create debris. “Companies like Orbital ATK and Loral will set precedents for future on-orbit operations. There is a risk of this industry tanking if something goes wrong.” DARPA’s demonstration tests will be important. Orbital says its mission planning, concept of operations, ground controls and on-board autonomous fault protection will prevent accidents.
In the NASA illustration at the top of this story, the Restore-L, NASA’s conceptual servicing spacecraft, extends its robotic arm to grab and refuel a satellite.
“Refueling is tricky, requiring grabbing a satellite, manipulating it to open a valve and inject fuel, all for satellites not designed for in-orbit refueling.”
Ruy Pinto, deputy technology officer at SES
Related Posts
Stay Up to Date
Submit your email address to receive the latest industry and Aerospace America news.
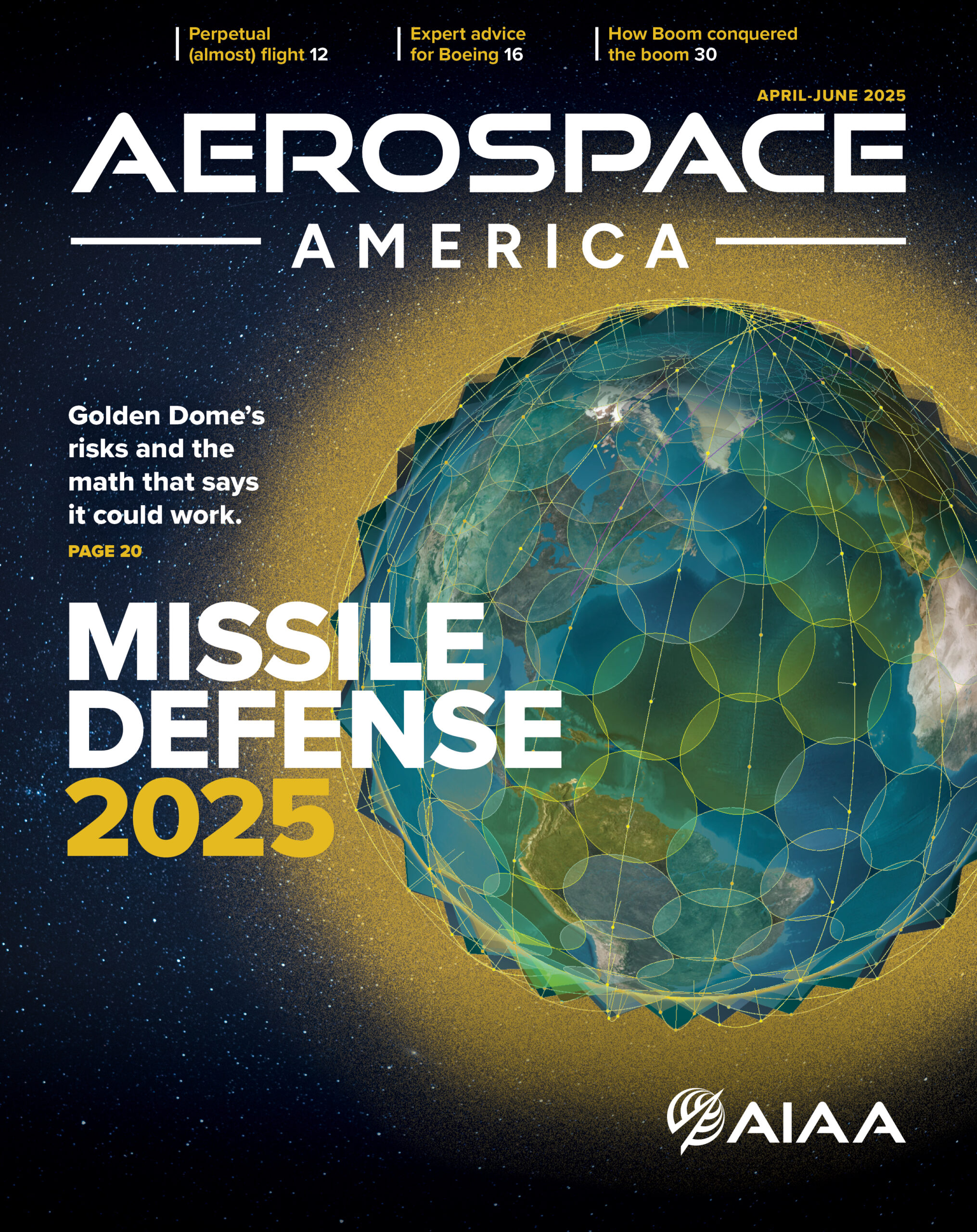

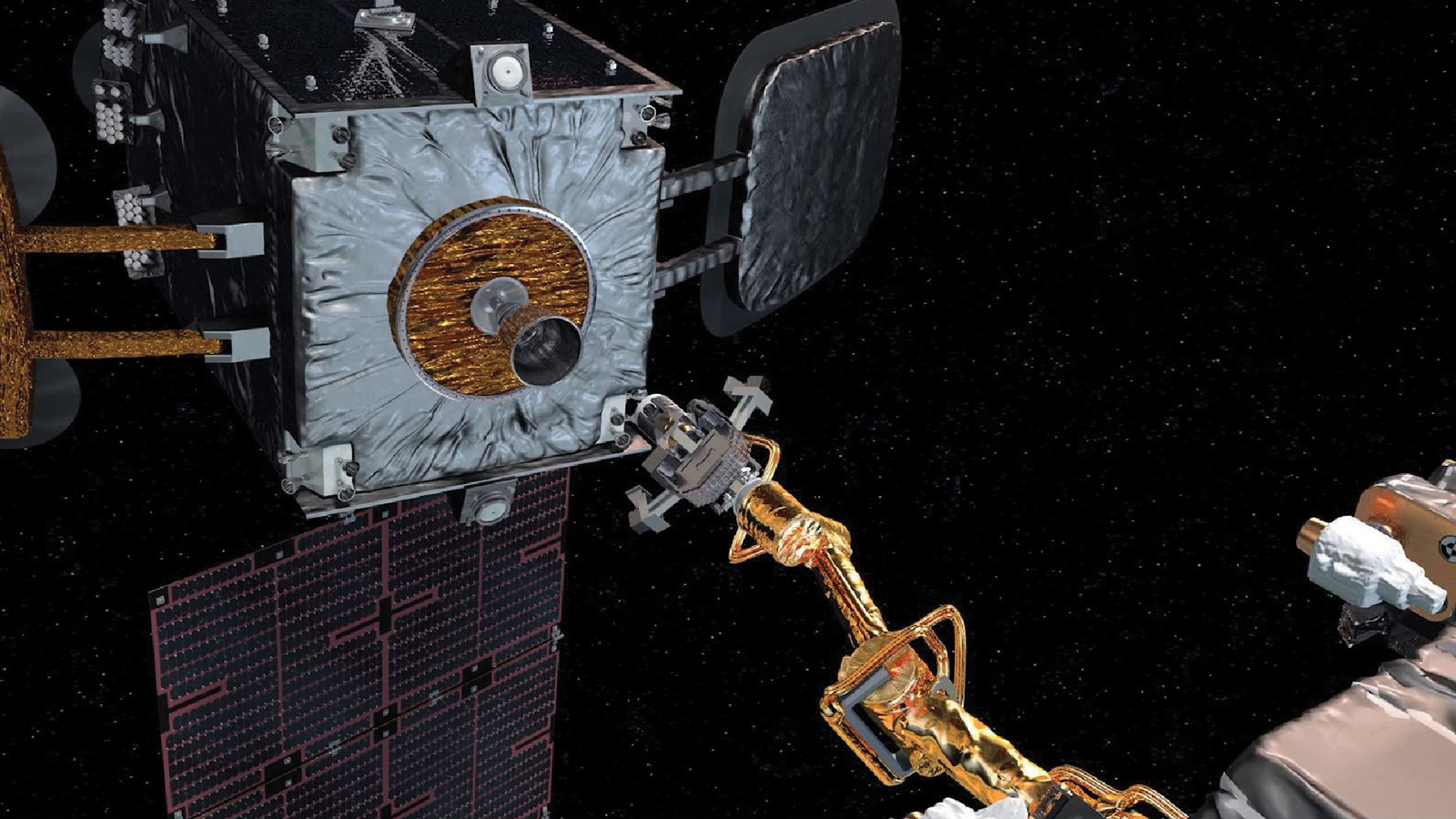