Stay Up to Date
Submit your email address to receive the latest industry and Aerospace America news.
One of the great remaining accomplishments of flight would be creating an operational aircraft that can fly hypersonically, defined as Mach 5 or above, by gleaning oxygen for combustion from the air, just as conventional jets do. The U.S. has tested air-breathing hypersonic engines but not of the size required for aircraft that would carry passengers, weapons or intelligence equipment. Jan Tegler looks at the challenges of scaling up.
The crux of the technical issue facing the Pentagon’s hypersonics planners can be seen in old photos of NASA’s X-43A demonstrators and the U.S. Air Force X-51A Waveriders. Over the phone, Luca Maddalena, a hypersonic flight researcher at the University of Texas, Arlington, guides me online to one particular image of an X-51A hypersonic demonstrator from 2009. The vehicle is slung under the wing of a B-52H at Edwards Air Force Base in California, just before a captive-carry flight. A researcher has placed his hand near the inlet of the craft’s supersonic combustion ramjet, or scramjet, engine, so called because air and combustion gases must whoosh through the engine at supersonic speeds without snuffing the combustion.
This is what Maddalena wants me to note: “The capture area, the inlet opening, is the size of your hand,” Maddalena says.
Each of the four X-51A Waveriders was a small-scale, expendable research aircraft, as were the three NASA X-43A vehicles that flew six years earlier in the Hyper-X program.
Scaling up such designs to carry conventional bombs, cameras and eavesdropping equipment for the military or passengers in the civil context would require a larger inlet to provide more air and therefore oxygen to burn more fuel and generate more thrust. In fact, such an air-breathing engine might need to ingest 10 times more air than the X-51A engine, depending on the mission, and U.S. military researchers have made this 10X performance a top goal.
As with a conventional aircraft, the payoff of an air-breathing design would be greater range and simpler ground support, since the atmosphere supplies an endless amount of oxygen, and there would be no need to compress oxygen into liquid and lug it along. But scaling up raises a host of combustion and mechanical challenges that have yet to be fully addressed in the international race among China, Russia, the United States and others to create air-breathing hypersonic missiles, aircraft and space launch vehicles.
Here in the U.S., the Air Force Research Laboratory in Ohio hopes to resolve many of those challenges through a potential new program nicknamed Mayhem for its goal of disrupting the hypersonics status quo. If this Expendable Hypersonic Multi-Mission Air-Breathing Demonstrator Program proceeds, then in five years one or more expendable, air-launched Mayhem demonstrators could be streaking over a test range at over five times the speed of sound, equipped with storage bays capable of carrying three distinct kinds of payloads that AFRL has not specified. The lab would not discuss funding for the potential new program in fiscal 2021, except to say that hypersonics research dollars are being consolidated from various program elements.
It’s not just the U.S. military’s hypersonics advocates who are excited by the possibility of Mayhem. Maddalena, who is not affiliated with the program-in-waiting, wants each Mayhem to be “a flying workbench for academics” and also “government and industry” researchers who have aspirations for building a wide range of hypersonic aircraft, perhaps even commercial passenger versions.
AFRL’s Mayhem information request drew the attention of 30 companies who responded by the late September deadline, including Aerojet Rocketdyne, Lockheed Martin and Northrop Grumman. AFRL says that at this point the Mayhem program is still under development.
Mixing fuel and air
To sense the technical issues, consider that turbine engines and ramjets slow air to subsonic speeds for combustion. By contrast, scramjets have “only a millisecond to mix fuel and air in a combustor” as the air whooshes through the flow path supersonically, Maddalena explains. Getting the fuel-air mixture right was tricky enough in the comparatively small scramjets that powered the X-43 and X-51. Doing it in a scaled-up scramjet is “not an incremental problem,” Maddalena says. “We’ve probably been studying mixing for 60-plus years, and we don’t have an answer.”
He asks me to picture a scramjet whose combustor walls are lined with fuel injectors that introduce hydrocarbon fuel into the chamber to mix it with the air rushing by. The bigger the scramjet, the larger its combustor cross-section must be, and if it’s too big, the fuel “cannot penetrate deep enough near the center line of the cylinder, so a large portion of the entering air would not be involved in the mixing process,” Maddalena says.
Without thorough mixing at the molecular level, combustion cannot be ignited or sustained. Even when combustion can be sustained, “we want the fuel to spread as much as we can so to utilize all the air coming into the engine,” which maximizes thrust.
Maddalena says it might be tempting to think you can “photo-scale” an engine — enlarging it like a photograph. “But unfortunately, the fluid dynamics of turbulent mixing does not photo scale.”
He suggests that corporations and the U.S. government involve university researchers more than they have so far on mixing and other scalability issues.
Research to date
There could well be more to learn, but on Mayhem engineers would not be starting from zero on the fuel-air mixing problem and other challenges of scaling up. Last month, Aerojet Rocketdyne reported generating in excess of 58 kilonewtons of thrust, during nearly a year of tests that ended in November. That would be enough thrust, the company says, to accelerate “a vehicle approximately 10 times the size of the X-51.” A rival design by Northrop Grumman also generated over 58 kN of thrust in 2019 during tests at the Air Force Arnold Engineering Development Complex in Tennessee under the same Medium Scale Critical Components program. MSCC managers are targeting a notional 9-meter vehicle.
For comparison, the X-51A scramjets (built by Rocketdyne when it was part of Pratt and Whitney) generated a maximum of 4.4 kN of thrust. The new engines are 5.5-meters long, making them seven times longer than the X-43A engines and longer than the entire X-51A cruiser, which measured 4 meters. Because of the Arnold experiments, “the government is confident in our ability to design” scramjets “at any scales,” says AFRL’s Edgardo Santiago-Maldonado, whose portfolio as the lab’s next-generation hypersonic lead includes scramjet testing. In Maddalena’s view, the “chapter on scalability, from a scientific perspective, is not yet closed as it requires much more work and understanding.” But there’s no doubt the results of the MSCC program are “exciting” and “constitute a very significant contribution to the scalability challenge.”
Alternative architecture
Bigger engines aside, there may be a way to ease the scaling problem. “You could potentially take something that was the size of the X-51 engine and just put three of them on a vehicle,” says NASA’s Chuck Leonard, who manages NASA’s Hypersonic Technology Project. Researchers under that effort are investigating concepts for hypersonic aircraft that would be powered by turbine-based combined cycle engines that would include a turbine-ramjet-scramjet cycle.
“Maybe you can put multiple smaller engines on it, what we sometimes call modules,” Leonard says.
There would be a host of structural considerations to be evaluated, but “at least you could fully test that X-51-size engine on the ground,” he says, alluding to the few American wind tunnels capable of testing larger scramjets.
Testing smaller engines might help researchers gain an understanding of the tradeoffs between one larger engine or multiple engines, although fully grasping the advantages and drawbacks would require creating a “whole-vehicle concept,” he adds.
DARPA’s contribution
DARPA, as part of its Advanced Full Range Engine program, also has been examining the challenges of creating a larger scramjet engine capable of propelling payload-carrying aircraft at hypersonic speed.
The goal is platform scale propulsion, meaning an engine capable of propelling an aircraft. By contrast, weapons scale would be “something smaller that would drop off a wing,” explains Nathan Greiner, who manages the program.
Aerojet Rocketdyne with Lockheed Martin as a subcontractor, is working with DARPA on the program, aiming to demonstrate the individual components that make up a TBCC engine at aircraft scale. “We’ve executed tests for the inlet, the turbine and for the nozzle, and we’re leading into testing on the dual mode ramjet in the near future,” Greiner explains.
Greiner says each of the TBCC components “have their own challenges with respect to scaling.”
He describes the challenge of scaling the TBCC engine’s common inlet and nozzle as “tractable” but says the challenge grows as scale grows. As an example, he cites “the actuation required to modulate the inlet geometry and maintain operability over a wide range of Mach numbers.”
Changing the geometry inside the inlet by moving a series of surfaces (NASA’s Leonard calls them “flaps”) in a timely fashion directs airflow to the turbine, ramjet and scramjet at the right moments as the aircraft accelerates or decelerates. The inlet surfaces or flaps also control the speed of the airflow being funneled to the different engines by creating shockwaves that slow airflow to subsonic velocity for the turbine and ramjet or allow it to flow at supersonic speed for the scramjet.
“Actuating the variable inlet surfaces at aircraft scale with flight-weight actuators is very challenging and requires intense engineering,” Greiner says.
No one I interviewed could say for sure whether the Aerojet Rocketdyne and Northrop Grumman engines or the technologies in developent by DARPA and NASA will make it into the Mayhem program, if the Air Force indeed starts it. But the research to date has given contractors new confidence about the propulsion challenges.
Raymond Toth, who leads Northrop Grumman’s Advanced Propulsion and Control Systems business strategy team, points to the engine his company tested in Tennessee. “Given a desire by the Department of Defense to put a scramjet of that size into a system and given the right investment, we think we could bring something like that to a flight stage within the next five years,” he says.
The question, he says, “is what is the vehicle that it’s going to fly in?”

About Jan Tegler
Jan covers a variety of subjects, including defense, for publications internationally. He’s a frequent contributor to Defense Media Network/Faircount Media Group and is the author of the book “B-47 Stratojet: Boeing’s Brilliant Bomber,” as well as a general aviation pilot.
Related Posts
Stay Up to Date
Submit your email address to receive the latest industry and Aerospace America news.
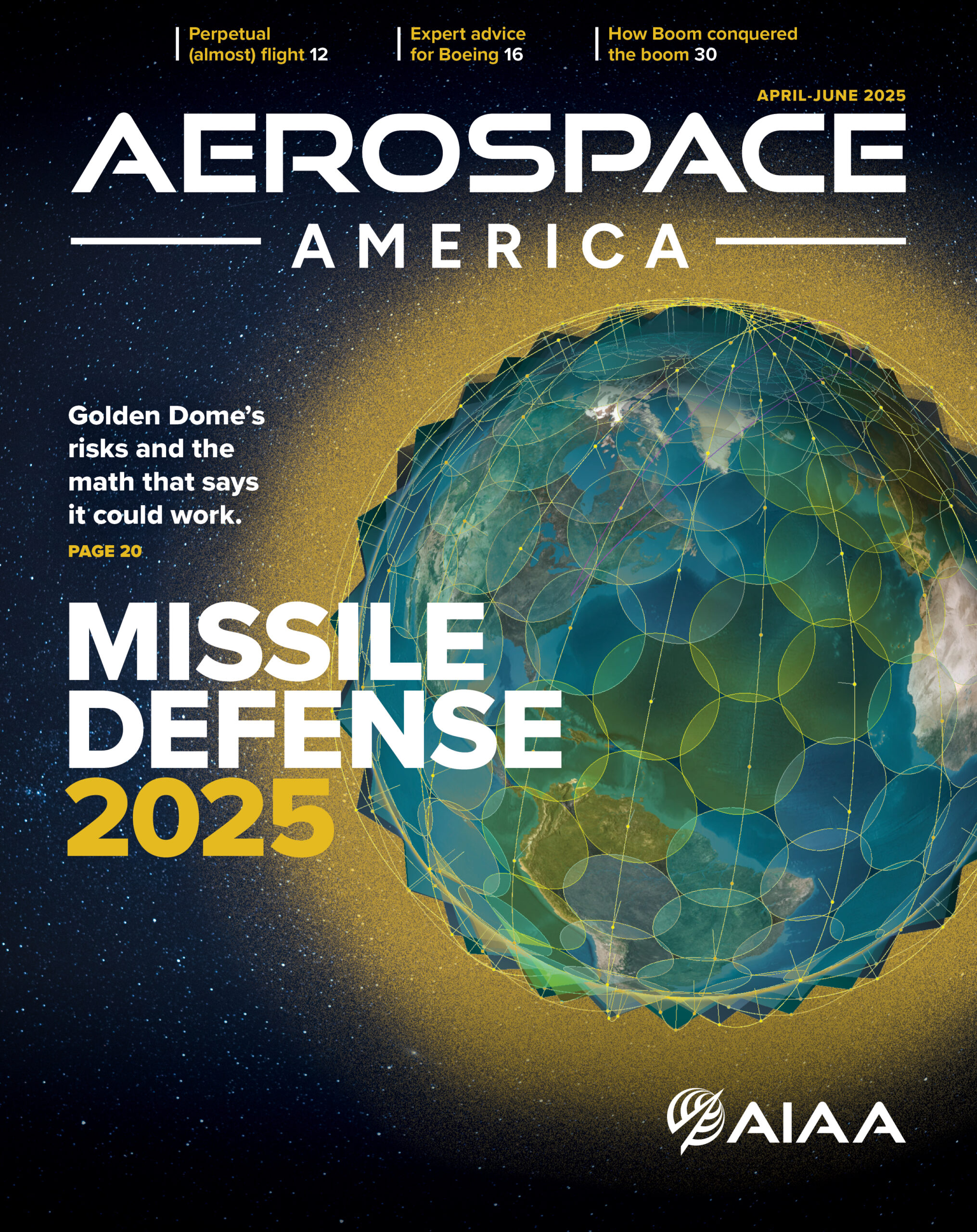
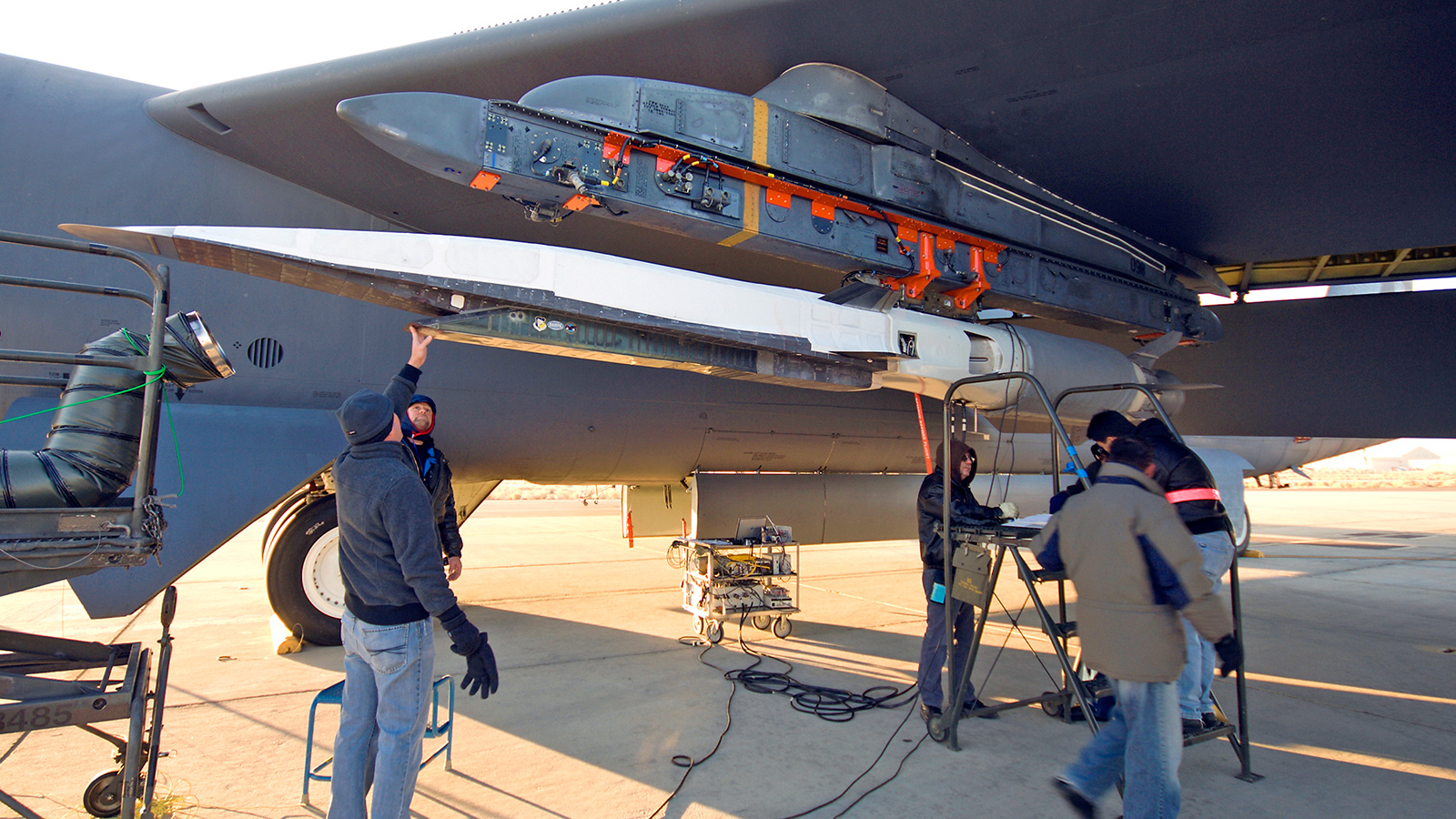
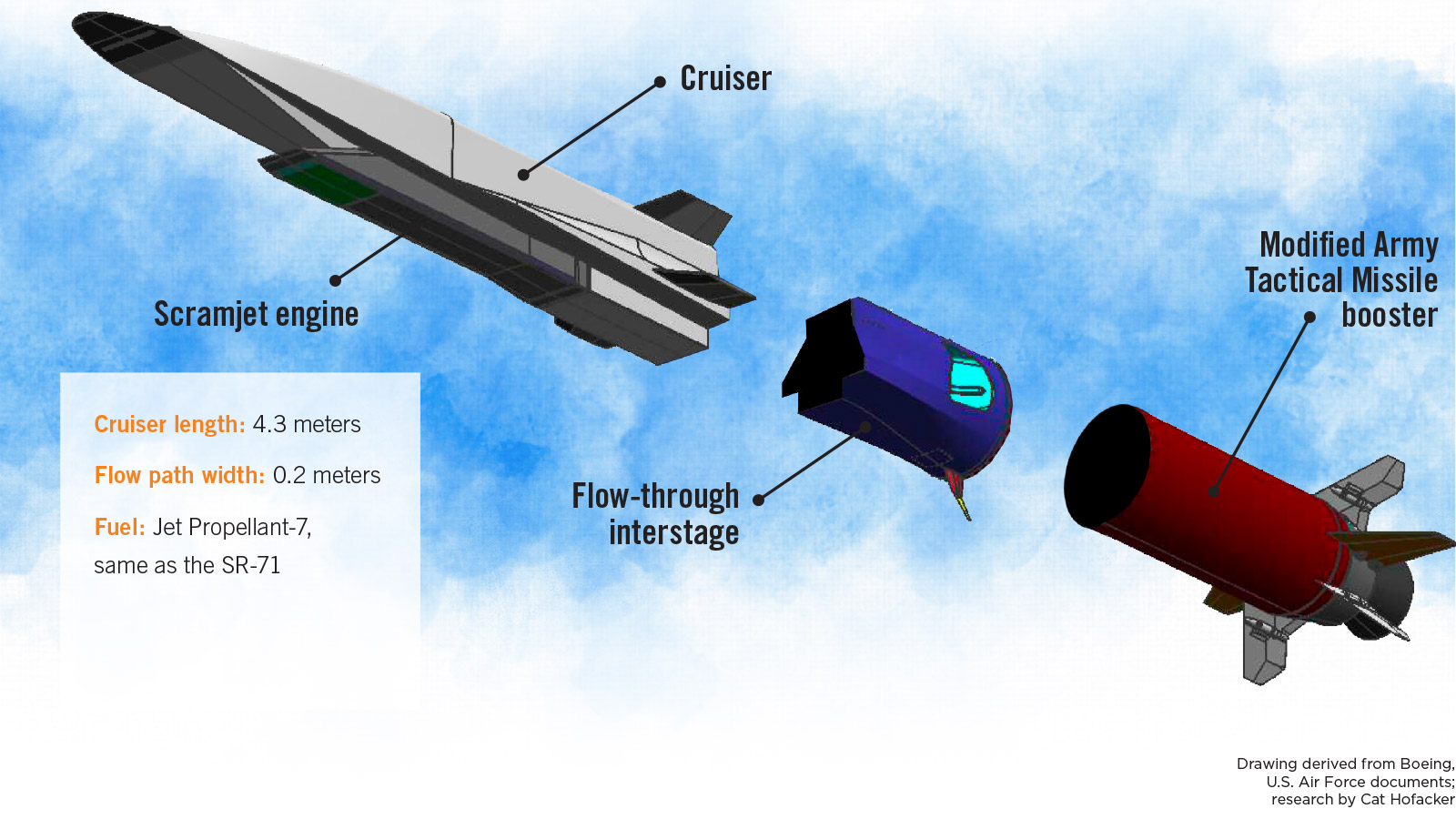
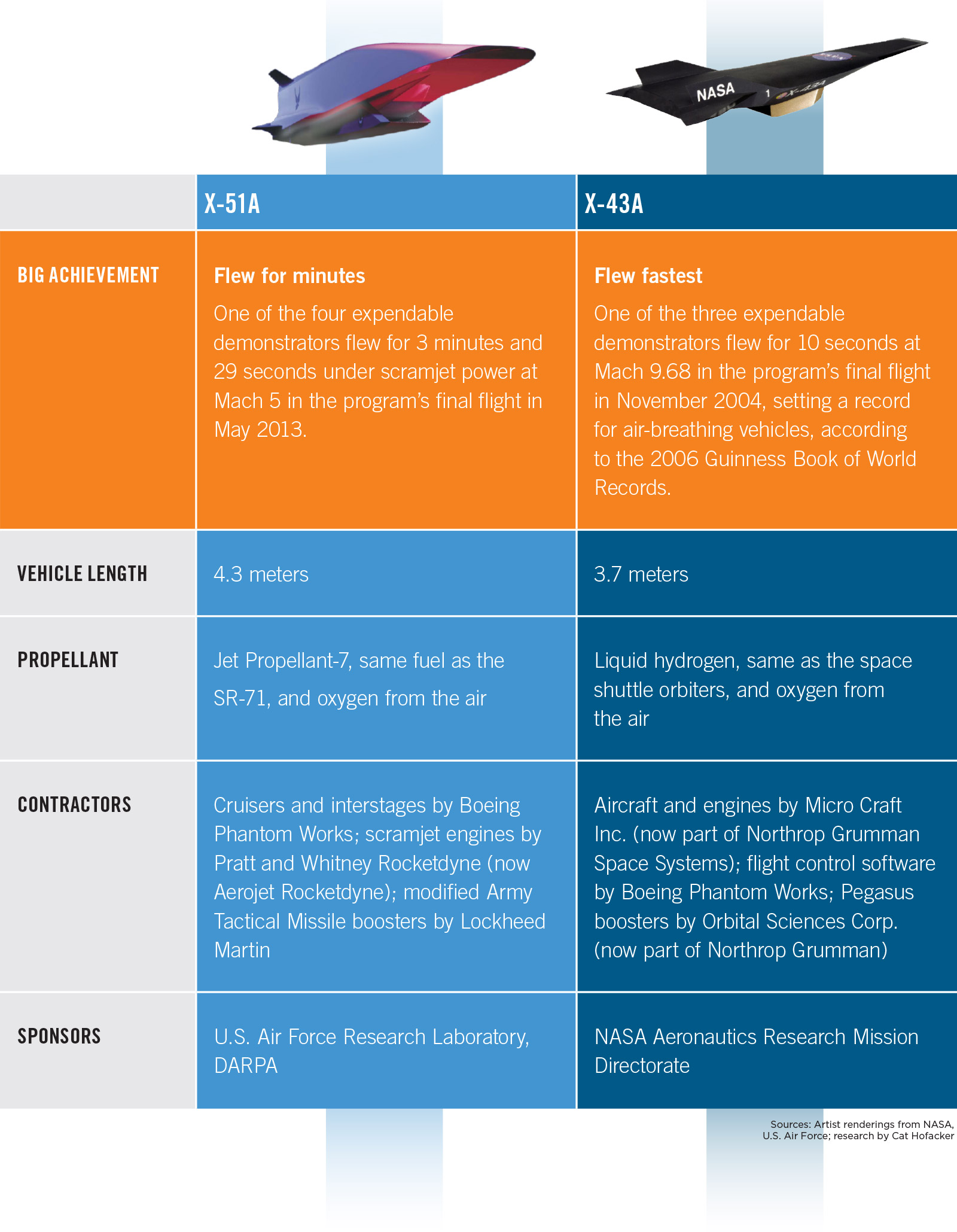
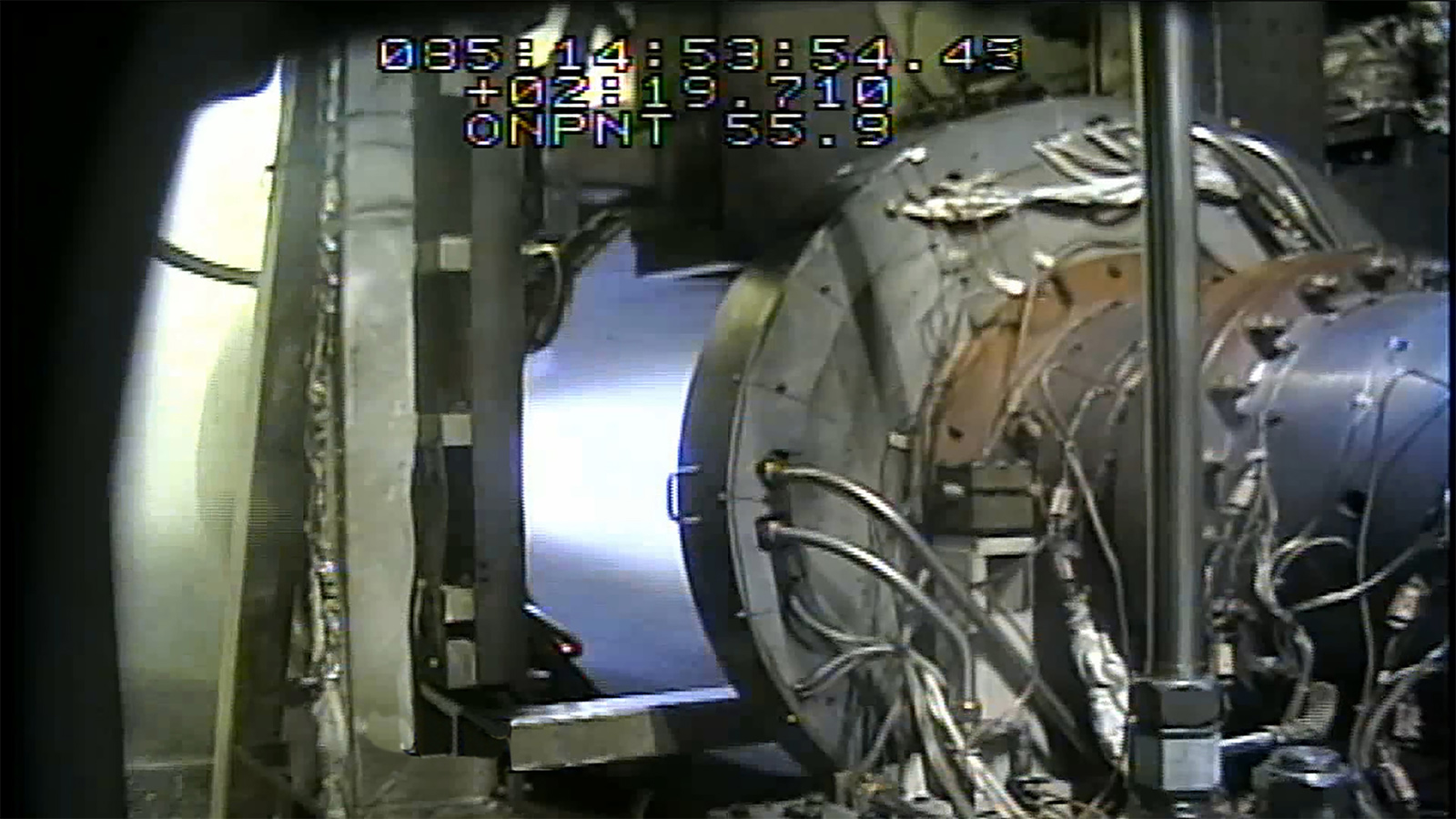