Stay Up to Date
Submit your email address to receive the latest industry and Aerospace America news.
A deep look at one company's plan to go up against satellites with stratospheric balloons
Satellites are famously expensive to build and launch, and once in orbit they can’t be repaired or upgraded except in the most extraordinary of cases. Many have tried to find a more satisfying option, among them were former U.S. Secretary of State Alexander Haig and his son, Alex. In the 1990s, they led a failed effort to hoist networks of dirigibles into the stratosphere to beam internet and phone service to the farthest reaches of the world.
Among the latest to take up the challenge is World View Enterprises, a small company formed in 2012 in Tucson, Arizona. The company originally planned some day to charge tourists $75,000 each for rides to the stratosphere in balloons, but in 2015, sensing pent-up demand in the space industry, the company toggled to focus on a nearer-term goal of carrying cameras and other instruments in the stratosphere. World View has now grown to 70 employees and is flight-testing helium-filled, stratospheric balloons that it calls Stratollites, each steered with a novel ballasting concept.
Getting to this point was not easy. Designers had to adjust their thinking about balloons and innovate in some unexpected ways.
Co-founder Taber MacCallum, who in 2014 helped then-Google executive Alan Eustace set a sky diving record, says that when he and his colleagues first started looking at the technology for World View, their thinking was, “it’s a big sack of gas” so “how hard can this be?” As it turned out, pretty hard. For the camera or communications applications, they must keep each balloon properly positioned for months at a time; and each balloon’s electricity-generating solar arrays must stay pointed at the sun. These days, MacCallum describes balloons as “complex and full of little subtleties.”
If World View can push its technology beyond testing, Stratollites might be stationed high over cities or regions to deliver fine resolution imagery on demand. That can’t be done from space today, because low Earth orbit satellites whiz over their imaging targets at intervals and geostationary satellites must fly at 35,000 kilometers above the equator. World View says Stratollites would cost an estimated 1 percent of a conventional satellite’s price to operate, while adding greater maneuverability and the advantage of returning payloads to the ground for repairs or updates.
For World View, 2017 could turn out to be a turning point year. In collaboration with Ball Aerospace of Colorado, one of the world’s leading manufacturers of satellite cameras and satellites, World View sent a Stratollite to an altitude of 75,000 feet with Ball’s visible-light and near-infrared cameras on flights in February and August. U.S. Southern Command was the client for the August flight. In June, a Stratollite tested solar-panel-pointing software in the stratosphere and also drew publicity by carrying a sandwich from the KFC fast food chain. NASA has taken notice too. In July, the agency’s Space Technology Mission Directorate collected 27 hours of data during a Stratollite flight. The directorate is interested in the possibility of controlling exploratory balloons on Mars with World View’s altitude control technique.
Navigating with wind
When World View engineers got to work, they knew they would need a method for keeping the balloons over specific coverage areas for long periods. Propellers weren’t an option because of their weight and energy demands, plus they would need to reach up to 3 meters across to push the thin air at that altitude.
MacCallum and his colleagues drew lessons from their participation in Eustace’s record-breaking parachute jump in 2014, called the StratEx Space Dive. They gained first-hand experience with the stratification of wind currents in the stratosphere, meaning that currents at one altitude flow in one direction and in different directions at other altitudes.
MacCallum and his World View team decided they could keep a balloon crisscrossing over a coverage area by moving it up or down in the stratosphere. The question was how to do it. At first, MacCallum considered pumping helium between the balloon and a ballast tank. Compressing the helium into the tank would lower the balloon’s buoyancy and it would sink to a lower altitude. Blowing helium back into the balloon and letting it expand would make the balloon rise. That technique wouldn’t work for the Stratollite because the compressor would have to expend too much energy trying to pump the light helium molecules at high altitude.
Also rejected was the idea of having the balloon enclose the helium for lift and also draw in or expel air from the atmosphere as ballast, as Google was doing to steer its Project Loon balloons, which aim to deliver high speed internet. The Google approach turned out to be problematic because the Stratollites must be larger than the Project Loon balloons. Each must inflate to 40 meters tall and 23 meters across, dwarfing conventional weather balloons, to carry about 500 kilograms of equipment. That includes batteries, solar panels, flight control electronics, tanks, heaters, a GPS transponder to alert other aircraft as it ascends and descends through commercial airspace, 50 to 100 kilograms of cameras or other cargo, and a parachute to return everything to Earth at the end of the flight. As the World View engineers tried to scale up the concept of inflating a balloon with helium and ballast air, the balloon’s altitude was too hard to control through the day-night temperature changes.
The team came up with a different steering strategy. Helium continues to provide the lift, but each Stratollite controls its altitude by compressing air from the atmosphere and packing it into ballast tanks, making those tanks heavier and pulling the balloon down. Or the ballast tanks can release air, making them lighter so the Stratollite rises. World View says it has flown about 50 test flights, dating back to 2015. Along the way, engineers found a wide gulf between how their balloon should work in theory and how it actually performed in the thin air and extreme temperature swings at altitude. They bridged that gulf with flight testing and creative ground tests.
Staring at the sun
Another complexity the engineers had to figure out was how to keep the solar-electric arrays pointed at the sun from their position on tethers below the balloon. It would be tricky because the air is so thin in the stratosphere that momentum is transferred easily from the arrays to the balloon and vice versa.
“You’re spinning yourself underneath the balloon, but every time you rotate around underneath the balloon to go point at something, you make the balloon rotate above you,” MacCallum says. “And when you try to stop rotating, the balloon starts to rotate. There’s this constant dance going on with the momentum of the balloon.”
On top of that are the unforeseen forces from air currents and moving parts — MacCallum calls them perturbations. “You can make it all work fairly well when everything is perfectly still, and there’s no perturbations,” he explains. “But as soon as you introduce a perturbation, now the system has to react to the perturbation and recover from the perturbation, and then relock on the sun, and then as things start to slow down, keep reacting to this changing set of momentums,” he says. The engineers solved the problem by writing computer models that accounted for the balloon’s rotation and the rate at which that rotation would slow. The computer code controls motors that will slightly turn the solar array, or let the balloon’s rotation do the work.
The engineers started with a model that described how they thought the balloon would rotate against and with the solar array. They then confirmed that model with actual measurements from four steel I-beams, 1 to 4 meters long, that they hung on a single vertical wire at World View’s Tucson offices, to stand in for the Stratollite solar array, balloon and other appendages. The aerospace engineers poked at the I-beams with sticks, trying to turn the beams, which were balanced at their midpoints and separated from each other on the wire by bearings that allowed them to turn freely and tiny motors that tried to keep one of them facing in one direction. Once their computer code could keep the I-beam stand-in for the solar array pointed in the desired direction in spite of their poking, the engineers were ready to test it in flight.
The first successful in-flight test of the solar array pointing code was the KFC sandwich flight in June, which lasted about 17 hours — cut short from a planned four-day flight because of a leak in the balloon. “That was the first time we had ever accomplished getting the solar array properly pointing at the sun,” MacCallum says. “That was a huge one for us.”
Picking up bad vibrations
Ball Aerospace had its own engineering hurdles to solve for its Stratollite flights. Ball is interested in the potential new markets for its sensors that Stratollites could open up for the company.
Bill Good, Ball’s airborne initiatives technical lead, says the company’s engineers knew how to smooth out vibration for their sensors taking images while flying on drones or satellites, or combating the extreme temperatures of space for the satellite cameras. But designing adaptations for sensors to work in the stratosphere, where there is neither the vacuum of space nor the significant atmosphere present at ground level, is a unique hurdle.
“This is a region right in the middle, where you don’t have zero atmosphere but you have some fraction of it,” Good says. “That actually can be more difficult to model, and it’s a challenge.”
Ball put its analysts to work writing computer models that could simulate the stratosphere’s thin air and temperatures, as low as minus 50 degrees Celsius. They designed heaters for their sensors based on the computer model and then they tried the sensors and heaters in a test chamber in Boulder, Colorado, that simulated the partial vacuum and cold of the stratosphere. They put the sensors and heaters to the test in February by recording images from a Stratollite at altitudes up to 76,900 feet with resolutions of less than 5 meters, and for one sensor in the sub 1-meter range. During the Stratollite flight in August, they transmitted images to the ground.
Another challenge was that a Stratollite creates vibrations in flight that are different from those encountered by cameras on airplanes or satellites. So Ball’s engineers measured and evaluated the vibrations of the February test flight. At the start of Ball’s collaboration with World View, Ball’s engineers knew nothing about the level of vibrations on a stratospheric balloon flight. “To avoid image blur, we needed to understand what the platform was providing,” Good says. “Airborne, satellite and Stratollite have this issue that they have to deal with.”
The vibrations during the balloon flight were distinct from those of a mechanical plane engine, but not necessarily less challenging, he says.
Good declined to reveal the specific adaptations that Ball engineers made to dampen the vibrations on Stratollites. But, he says, in the past they’ve molded rubber fittings as shock absorbers for the cameras and adopted jitter- or image-stabilization software, similar to what’s available from off-the-shelf digital cameras.
As World View edges toward offering weeks- or months-long flights for imaging services, science experiments, communications links or other cargo, more innovations are likely to be needed. “It feels a lot like the ‘Mythbusters’ TV show around here. Someone’s got an idea, and they’re going to go test it,” MacCallum says.
Inspiring record
On Oct. 24, 2014, then-Google executive Alan Eustace set a sky diving record by jumping from a helium-filled balloon that carried him to an altitude of 135,890 feet. The StratEx Space Dive jump-started interest in high-altitude balloons as alternatives to satellites. During the run-up to the record attempt, Google started Project Loon, a planned fleet of balloons that would provide internet services. A friend of Eustace’s, Taber MacCallum, helped create a company called World View, which aims to image Earth with balloons called Stratollites.
“There’s this constant dance going on with the momentum of the balloon.”
Taber MacCallum, World View co-founder and chief technology officer, describing the difficulty of keeping the Stratollite’s solar-electric arrays pointed at the sun from their position on tethers below the balloon.

About Keith Button
Keith has written for C4ISR Journal and Hedge Fund Alert, where he broke news of the 2007 Bear Stearns hedge fund blowup that kicked off the global credit crisis. He is based in New York.
Related Posts
Stay Up to Date
Submit your email address to receive the latest industry and Aerospace America news.
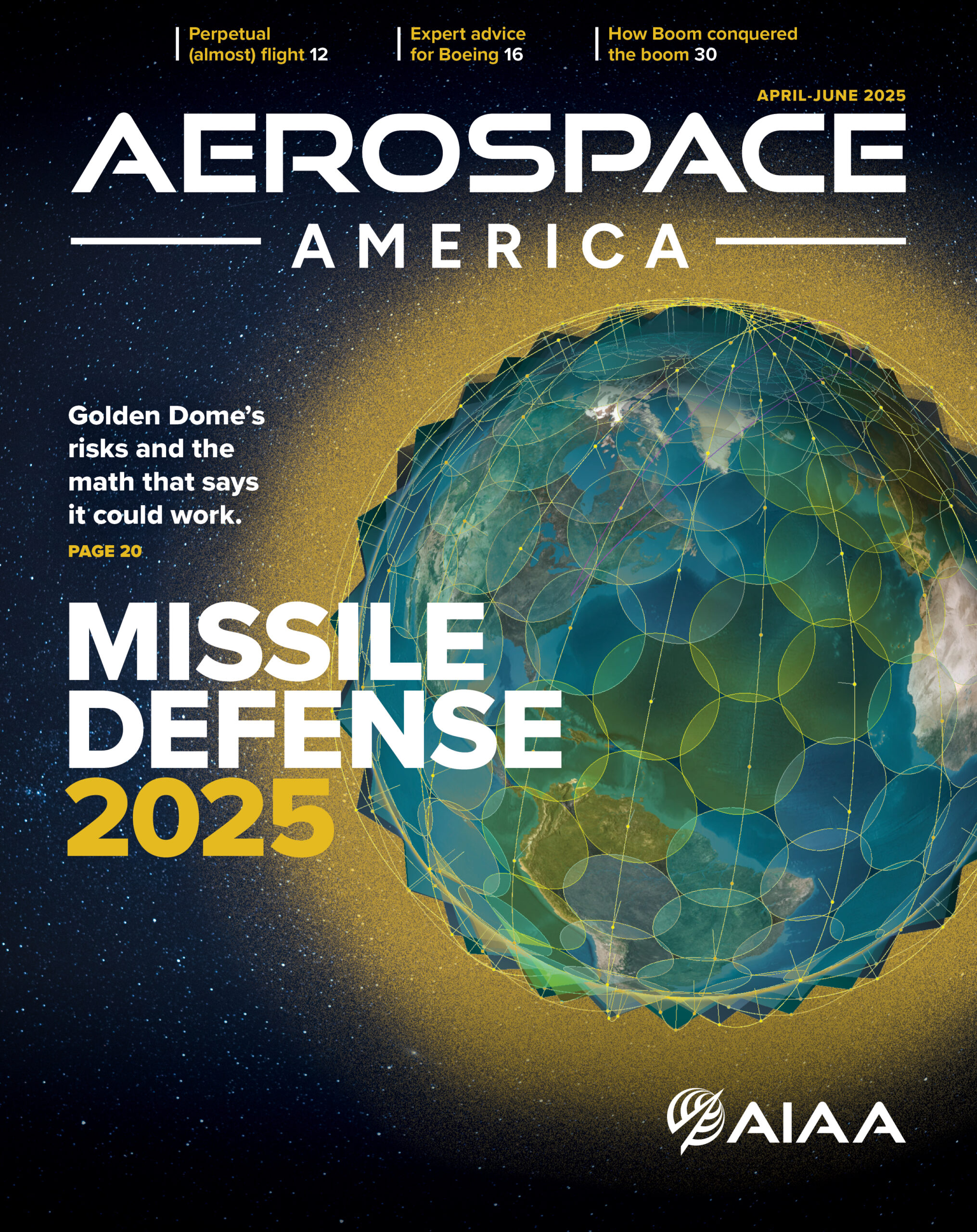
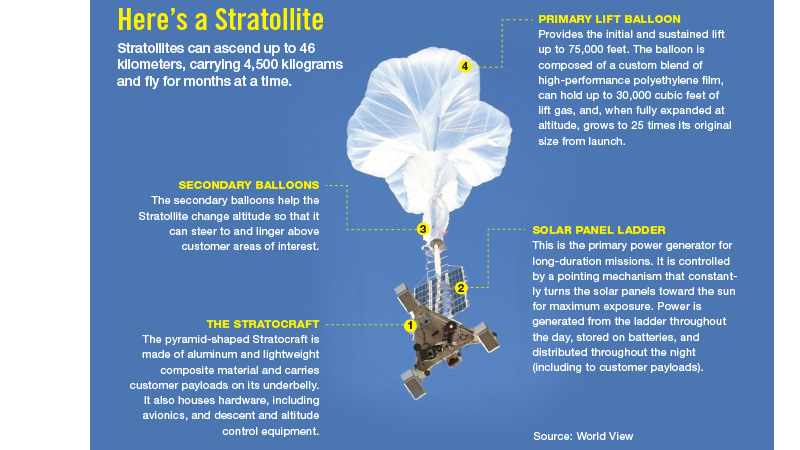
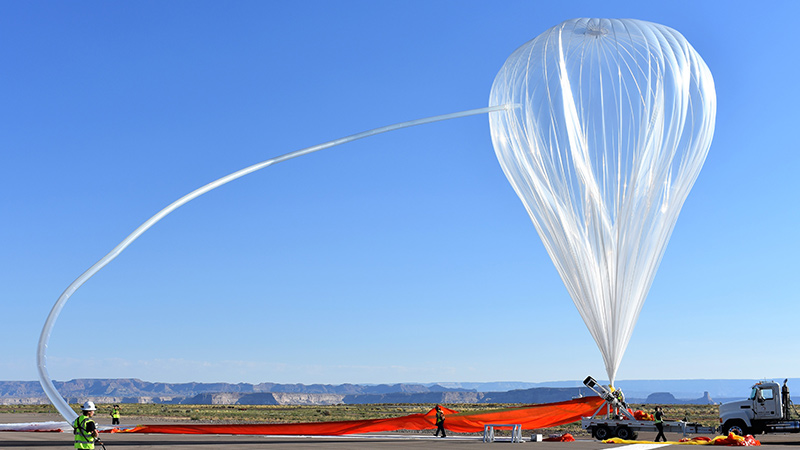

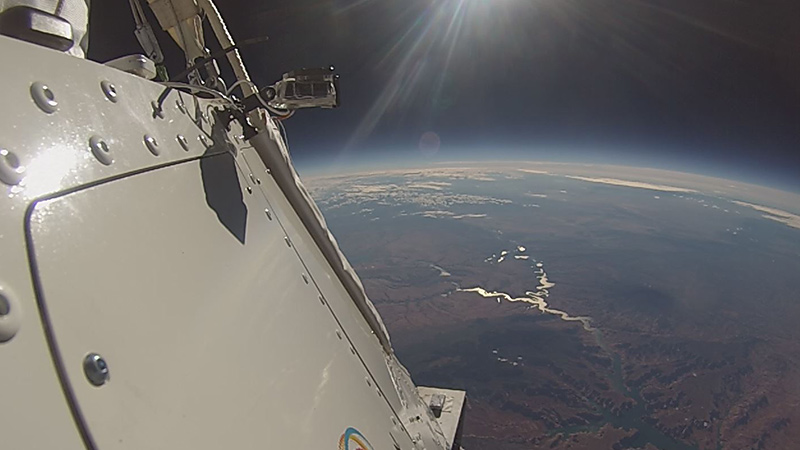