Stay Up to Date
Submit your email address to receive the latest industry and Aerospace America news.
With their unique properties, carbon nanotubes have generated hype as big as they are small. Adam Hadhazy finds that after three decades of fitful development, these microscopic tubes are making their way into aerospace applications, even if not the most grandiose ones yet.
If you shrank yourself by a factor of several hundred million and grasped a long carbon nanotube as if it were a steel rod, it would feel surprisingly light. If you slammed the slender, hollow tube against some nearby molecules, it would not break, even though its walls look delicate, a mere single atom thin. But be careful and don’t touch the tube against something hot or electrified, because depending on how its atoms are arranged, it would conduct heat and current stunningly well and you’d be toast.
Materials scientists have been touting these and other properties of nanotubes since the early 1990s, promising a revolution in aerospace and other sectors. Lab tests show that carbon nanotubes have hundreds of times the tensile strength of an equivalent diameter span of steel, yet with just a sixth of steel’s density. Bind nanotubes with resin into fibers, weave those fibers into sheets, and cure those sheets into shapes, and the resulting structures — superstrong and superlight compared to aluminum and conventional composites — would revolutionize performance and open new designs for aircraft and satellites. It might even be possible to make giant cables of nanotubes that could be unfurled from space toward Earth to create a space elevator, an ultradurable conduit for shuttling material up and down.
Flash forward 30 years, however, and none of that is remotely reality. Researchers are still laboring to retain the attractive properties displayed by individual nanotubes at size scales relevant to human technologies.
“The real challenge is how to take something at a molecular level and apply it and convert it into a macroscopic form that then delivers a system-level capability in a commercial environment,” says Joe Sprengard Jr., president, CEO and co-founder of Veelo Technologies, an Ohio-based startup developing new materials — some based on nanotubes — for boosting the performance of next-generation aircraft.
For that reason, the first applications for carbon nanotubes are likely to be less grandiose than those originally envisioned three decades ago. They include heating devices that, ironically, would aid in manufacturing and repairing the conventional composites that carbon nanotube versions might someday replace. Others include airborne de-icing for wings and leading edges, along with durable sensors that could hold up in tough environmental conditions that aircraft encounter.
“We’ve finally learned how to work with these materials, getting them into the forms and scale that allow us to do meaningful things,” says Michael Meador, who retired last year after a 36-year career at NASA, where he worked on nanomaterials as a manager for the agency’s Game Changing Development Program at Glenn Research Center in Ohio.
“We’re getting beyond the hype of the ’90s,” Meador adds. “Carbon nanotubes are not a one-size wonder material that’s going to solve everyone’s problems, but there’s a lot of potential and they’re close to reality.”
Tiny but mighty
A carbon nanotube is actually a rolled-up version of graphene, another buzz-worthy substance that is intensively researched in materials science.
The tubes’ diameter is usually in the range of several tenths to a few tens of nanometers (billionths of a meter, or ten-thousandths the diameter of a human hair) for the common, single-walled variety of tube; concentrically nested tubes, or multiwalled tubes, can be significantly wider and are likewise being explored for their potential utility.
Reports of chemists observing narrow carbon tubules date back to the 1950s, but it was not until the early 1990s with the clear discovery of single-walled carbon nanotubes that interest in them skyrocketed.
Based on the angle of the lattice that the nanotube’s carbon atoms form, the material can be highly conducting of electricity, semiconducting, or non-conducting. Carbon nanotubes are also about five times better at conducting heat than the industry workhorse, copper, and even exceed
diamonds.
So why can’t tubes be turned into materials that would simply be dropped into aerospace products? “Carbon nanotubes are finicky,” Sprengard says.
For starters, while the raw manufacturing of carbon nanotubes has come a long way, with many companies producing the tubes for an array of niche commercial purposes, quality is sometimes a concern. High-end nanotubes — distinguished by their purity, uniformity and consistency within batches — remain relatively costly. “All carbon nanotubes are not created equal,” says Sprengard. Nanotubes also do not behave like metals that can be simply melted down and molded into desired shapes; instead, nanotubes must be bound together in a matrix, for instance with resin, in order to transfer loads for structural purposes and to deliver their conductive properties at scale. Irksomely, though, nanotubes tend to agglomerate instead of evenly dispersing when added to another material; for instance, when adding the manufactured nanotubes (which in bulk look like a powder) to composites, the formulations grow too viscous and unworkable, limiting the numbers of tubes that can be added and ultimately the material property gains being sought.
Enhancing composite manufacture and repair
Yet progress is being made on all these fronts, with ever-improving manufacturing techniques and the use of dispersants to more evenly distribute nanotubes in their binders. The upshot is that non-structural applications in heating for conventional composite manufacture and de-icing are becoming increasingly well-developed and ready for service.
Sprengard knows the challenges presented by nanotubes well. In 2008, he formed a company called General Nano (later renamed Veelo) with two scientists at the University of Cincinnati who had figured out how to grow centimeter-long nanotubes, then the longest in the world, in a chemical vapor deposition chamber in their lab. The company initially sought to produce high-strength fibers from these long nanotubes, but years of effort could not economically deliver on that objective. Along the way, Sprengard and colleagues did learn some of the ins-and-outs of nanotubes, though, and pivoted to adding the tubes, now purchased in bulk powder form from outside vendors, into formulations for materials with other aerospace applications.
One such material formulation is silicon- and polymer-based heating blankets, which can aid in the manufacture and repair of composite materials reinforced by a different carbonaceous material, carbon fibers. These are a thousand times thicker than carbon nanotubes and are made of graphite.
Carbon fiber-reinforced and other composites are a hot market these days in aerospace, with the materials increasingly taking the place of conventional structural metals. The Boeing 787 and the Airbus A350 XWB are cases in point, with around half of each airframe composed of composites. Composites are composed of layers of material that must be fused together during a curing process at a few hundred degrees Celsius. For aircraft, the conventional approach has been to put components ranging from massive fuselages to tail fins in warehouse-sized ovens or, depending on the manufacturer, in autoclaves that both pressurize and heat the parts as part of the curing process. As a result, a large volume of air ends up being pointlessly and expensively heated.
“It’s really super-inefficient,” says Seth Kessler, founder of Massachusetts-based Metis Design Corp. which, like Veelo, is developing nanotube-based heating blanket alternatives to ovens and autoclaves, among other applications. Kessler points out that the energy consumption involved in running ovens and autoclaves is as much as half of the cost of manufacturing a composite part.
The heating blankets Metis is working on, in collaboration with the Massachusetts Institute of Technology and MIT’s funding support from Airbus, Embraer, Lockheed Martin, Saab AB, and other aerospace and defense organizations, would be put directly onto a component that needs curing, versus heating a component in a giant room. Simply adding an electric current heats the blanket — sort of like an electric blanket one might use for aching muscles. Because carbon nanotubes have excellent thermal conduction, the electrical energy required for this blanket-based curing is three orders of magnitude less than equivalent curing through standard manufacturing. “If you’re taking the largest cost element of manufacturing composites and reducing it to less than a percent of its original cost,” says Kessler, “that has tremendous implications for the cost of the part.”
At MIT, materials scientists are investigating ultrathin film versions of carbon nanotube blankets that could be wrapped around a component of any size. Sprengard at Veelo emphasizes how these kinds of blankets could help in re-curing the often-nicked-up small sections of aircraft that need to be fixed. “Imagine your car: When it gets banged up, you go to the autobody shop,” says Sprengard. “With [aircraft] composites, it’s the same thing. You’re constantly having to repair them. The plane flies and it’s hit by a bird strike or a hailstorm, or a technician drops a hammer on it. You have to repair and re-cure that damaged area.”
For these sorts of repairs, metal wire-based blankets have long been the norm. But besides being energy inefficient, these metallic blankets take longer to heat up and do not heat as evenly as carbon nanotube-doped blankets, Sprengard says.
The heating blankets are nowhere near mass-market yet, but Sprengard says Veelo counts numerous aerospace and defense firms as customers.
Ice be gone
The inherent material advantages to carbon nanotubes have further poised them as a key enabler for next-generation de-icing devices built into aircraft wings and other leading edges and surfaces to protect against ice buildup during flight.
Most de-icing today for commercial aircraft involves a chemical sprayed on wings before takeoff that cuts down on ice formation and on ducting hot air from the aircraft engines in flight to melt ice before it gets too thick and threatens performance. A newer kind of de-icing, incorporated in the Boeing 787, for example, involves conducting electricity into meshes of copper wire embedded under the skin to heat the leading edges. As with the curing blankets, this electrothermal de-icing arrangement leads to time-consuming and uneven heating as the metal slowly diffuses ice-eliminating warmth into the mesh gaps. Compared to metallic-based de-icing systems, carbon nanotube-based ones would heat up very rapidly, about 10 times faster for a given area, says Kessler. The nanotubes’ remarkably low weight also shaves off hundreds of kilograms on an aircraft wing, for example. “Carbon nanotubes are much, much lighter than other electrothermal mechanisms,” Kessler says. That lighter weight can also translate into far greater de-icing system coverage over a given expanse of an aerial vehicle.
Nanotube-based de-icing should ultimately require about 10 times less energy than conventional approaches, Kessler says. Furthermore, hardy nanotubes would not suffer from corrosion and could withstand much higher strain and deformation, flexing and returning to shape better than their copper counterparts.
The debut of nanotube-based de-icers on crewed military and commercial aircraft could be near. Embraer, the Brazil-based aerospace conglomerate, has tested the Metis-pioneered carbon nanotube de-icing heaters on the leading edge of a model of a horizontal tail in a wind tunnel. A different major commercial aircraft manufacturer and a major rotorcraft maker, both of which Kessler says he cannot disclose for proprietary reasons, have also purchased the heaters for testing, and the U.S. Navy is likewise interested. Metis ultimately licensed its electrothermal technology to Goodrich Deicing, part of Collins Aerospace, in 2017, and there have not been further announcements. Veelo, for its part, is also developing nanotube-based de-icers, and though Sprengard did not disclose customers at this time, he characterizes them as being in commercial aerospace and defense sectors.
In parallel, researchers are developing nanotube-based de-icers for unmanned aerial systems. Be-cause these aircraft have fewer regulatory hurdles, they could provide confidence that then translates to broader deployment. In this vein, the Ohio-based science and technology development company Battelle is continuing work on a product called HeatCoat [first reported in “De-icing with nanotubes,” Aerospace America, July/August 2016].
Sponsored by the U.S. Special Operations Command, or SOCOM, HeatCoat is an ultrathin, lightweight, nanotube-doped layer sprayed onto surfaces underneath a regular coat of paint. Electrical leads connected to a drone’s wiring system serve as a power source to disperse de-icing heat through the layer. Because HeatCoat is so close to the wing surface, it requires little energy to achieve de-icing, says Greg Kimmel, the national security business line manager for Battelle who is overseeing HeatCoat’s continued development. Furthermore, because it’s a spray-on layer, HeatCoat can be applied to components and areas with complex geometries, such as nosecones and engine intakes.
Over the past few years, Battelle has conducted ice tunnel and environmental tests with HeatCoat. Plans call for flight tests next year with a Navmar Applied Sciences Corp. TigerShark UAS, with the eventual goal of putting lightweight de-icers on MQ-9 Reaper drones — a mainstay hunter-killer for the U.S. Air Force.
A critical aspect of the ongoing development work has involved software controllers, which enable the heating device to autonomously activate when it detects ice buildup. “One of the complicated parts of de-icing systems, especially on unmanned aircraft, is knowing when you’re in icy conditions so you don’t run the system when you don’t need to,” says Kimmel. For drones operating on limited battery life, appropriate de-icer activation is important.
Knowing when things aren’t right
Sensing is another area where the properties of nanotubes also make materials based on them promising candidates for development. Researchers at Metis and MIT came up with this concept of how a carbon nanotube-outfitted sensor embedded within an aircraft wing, for example, could register changes in a baseline level of electrical resistance caused by structural fatigue or damage. Accordingly, these devices could work very well as crack gauges, monitoring wing structural integrity. The data would be diagnostically helpful for both maintenance and post-mission repair. “You can easily correlate the change in resistance to the length of the crack needed to cause that change in resistance,” says Kessler.
Analogs for such sensors that rely on metal foil have been around a long time, says Kessler, but carbon nanotube-based sensors would exceed their performance. “The nice thing about carbon nanotubes, they’re really durable and inert,” says Kessler. He and his colleagues have done tests subjecting carbon nanotube sensor prototypes to seawater and jet fuel exposure for a full year, among other extreme conditions, and the sensors have come out just fine. “Carbon nanotubes don’t really care about the environment they’re in at all,” says Kessler.
The Air Force’s F-15 fighter jet program is pursuing flight testing of the crack gauge sensors. Meanwhile, development is continuing for both strain and corrosion sensors.
Seizing upon strength and lightness
Perhaps the most obvious use case for carbon nanotubes, given their strength and lightness, would be in structural applications, especially for spaceflight. Reducing the weight of structural components, from the buses of satellites to the skins of rockets, would cut launch costs or translate into delivering significantly more useful mass to space.
“Every pound matters to us,” says Emilie “Mia” Siochi, a research scientist with the Advanced Materials and Processing Branch at NASA’s Langley Research Center in Virginia, who is coordinating agency efforts to devise structural carbon nanotube-based materials with academia and industry. “When people say launch costs are $10,000 a pound, that’s just to launch to low-Earth orbit,” adds Siochi. “To go to the moon and Mars, that cost escalates.”
The dream of structural nanotubes has certainly not been abandoned. Toward these mass- and cost-reduction goals, NASA started work two decades ago on developing new kinds of composites reinforced by nanotubes. The agency has targeted getting the nanomaterials to the point where they have approximately twice the tensile strength of the current material of choice, carbon fiber-reinforced composites. That, in turn, could enable a reduction in vehicle mass on the order of 50%. “It would be a game changer in terms of weight savings,” says NASA’s Meador.
Mixing in nanotube powder to today’s best composites to achieve even lower weight has proven problematic, however, due to agglomeration. A more promising tack, started in parallel about a decade ago, has been to weave nanotubes into fibers that could act as a drop-in replacement for carbon fiber in composite manufacturing. To that end, NASA has continued to award contracts to New Hampshire-based Nanocomp Technologies Inc., which produces nanotube yarns and sheets, among other products. NASA obtained hundreds of meters of this material to fashion a composite overwrap pressure vessel. The vessel contained cold gas as part of a thruster system. In 2017, that pressure vessel went to space aboard a sounding rocket launched from NASA’s Wallops Flight Facility in Virginia; the launch marked the first flight test of a structural component made from a carbon nanotube composite material. The vessel ably withstood the loads of launching and landing. NASA is seeking to improve upon the achieved properties of the material — Siochi says strength has been boosted by around 2.5 times in the past few years — while maturing the processes needed for the large-scale, economical composite manufacture relevant for aerospace.
“People are used to building with metallics and carbon fiber composites, and both of those have decades of head start” on nanotubes, says Siochi. “We’re trying to build up the confidence in this new material.”
On Earth and beyond
Besides those applications already mentioned, nanotubes look set to appear in numerous other places that will impact aerospace. Many groups, for instance, are researching nanotubes for enhanced batteries, which are of course integral for advancing the state of electric aircraft. Computer engineers are also devising processor architectures that would incorporate nanotubes instead of silicon, with implications in particular for UAS and spacecraft.
Still other avenues of interest include shielding composites against electrostatic discharges and other electromagnetic interference. That need for protection extends beyond Earth’s atmosphere as well. For example, and in an ahead-of-its-time use case, Nanocomp-built shields were incorporated into the Juno spacecraft ahead of its launch in 2011 to study Jupiter. The shielding has helped protect the main engine housing and attitude control motor struts from discharge events in the giant planet’s intense radiation belts.
As for structures made of nanotubes, Siochi hopes to have those technologies ready soon enough to play a role in NASA’s Artemis lunar landings, scheduled to start this decade, and from there, onward to becoming a major enabler of interplanetary exploration.
“I hope there is an opportunity to actually put something involving carbon nanotubes on the moon that helps us understand what it takes to be part of a system architecture, however small,” says Siochi. “Then we can truly be part of the mission to Mars.”
“We’re getting beyond the hype of the ’90s. Carbon nanotubes are not a one-size wonder material that’s going to solve everyone’s problems, but there’s a lot of potential and they’re close to reality.”
Michael Meador, formerly at NASA

About Adam Hadhazy
Adam writes about astrophysics and technology. His work has appeared in Discover and New Scientist magazines.
Related Posts
Stay Up to Date
Submit your email address to receive the latest industry and Aerospace America news.
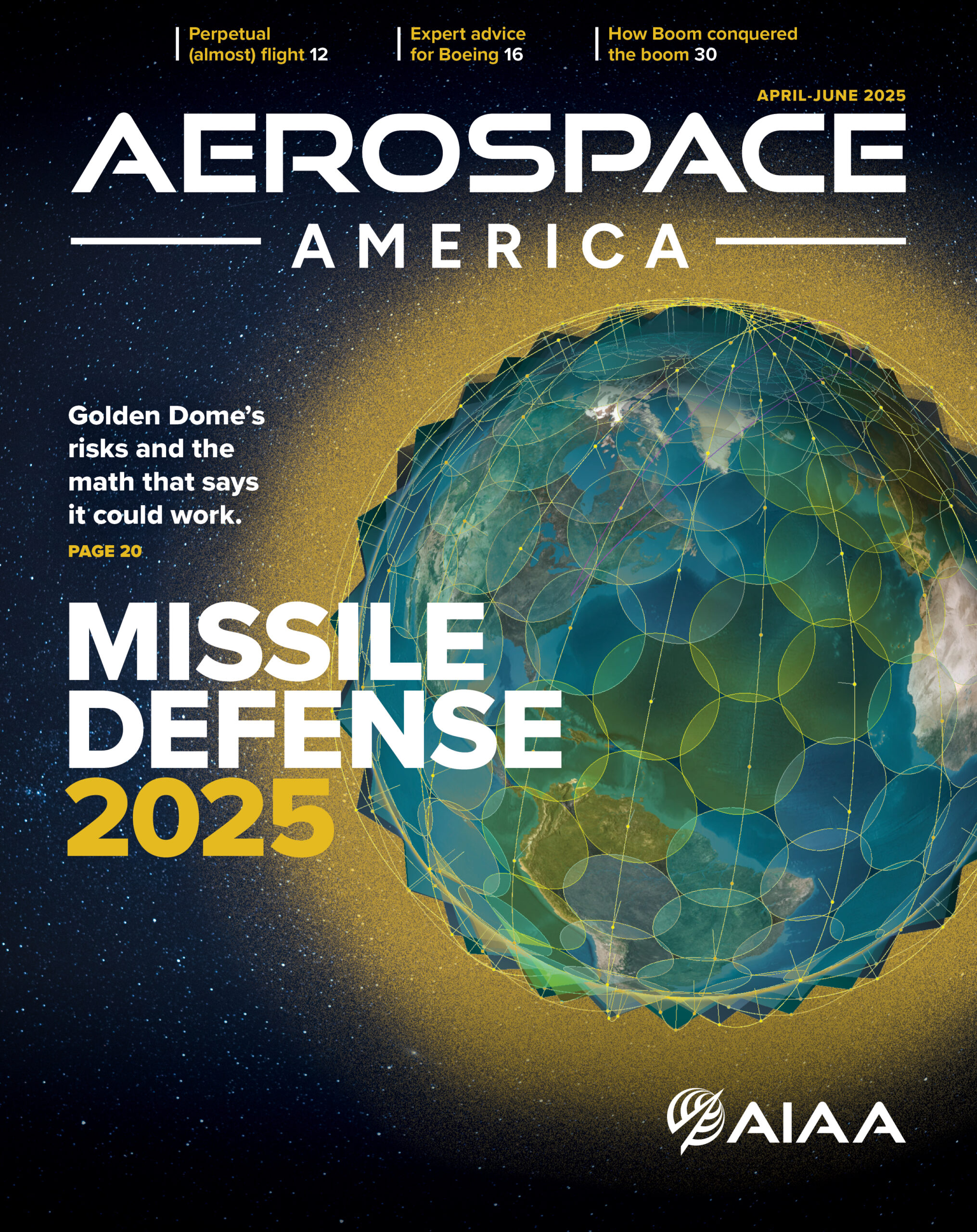
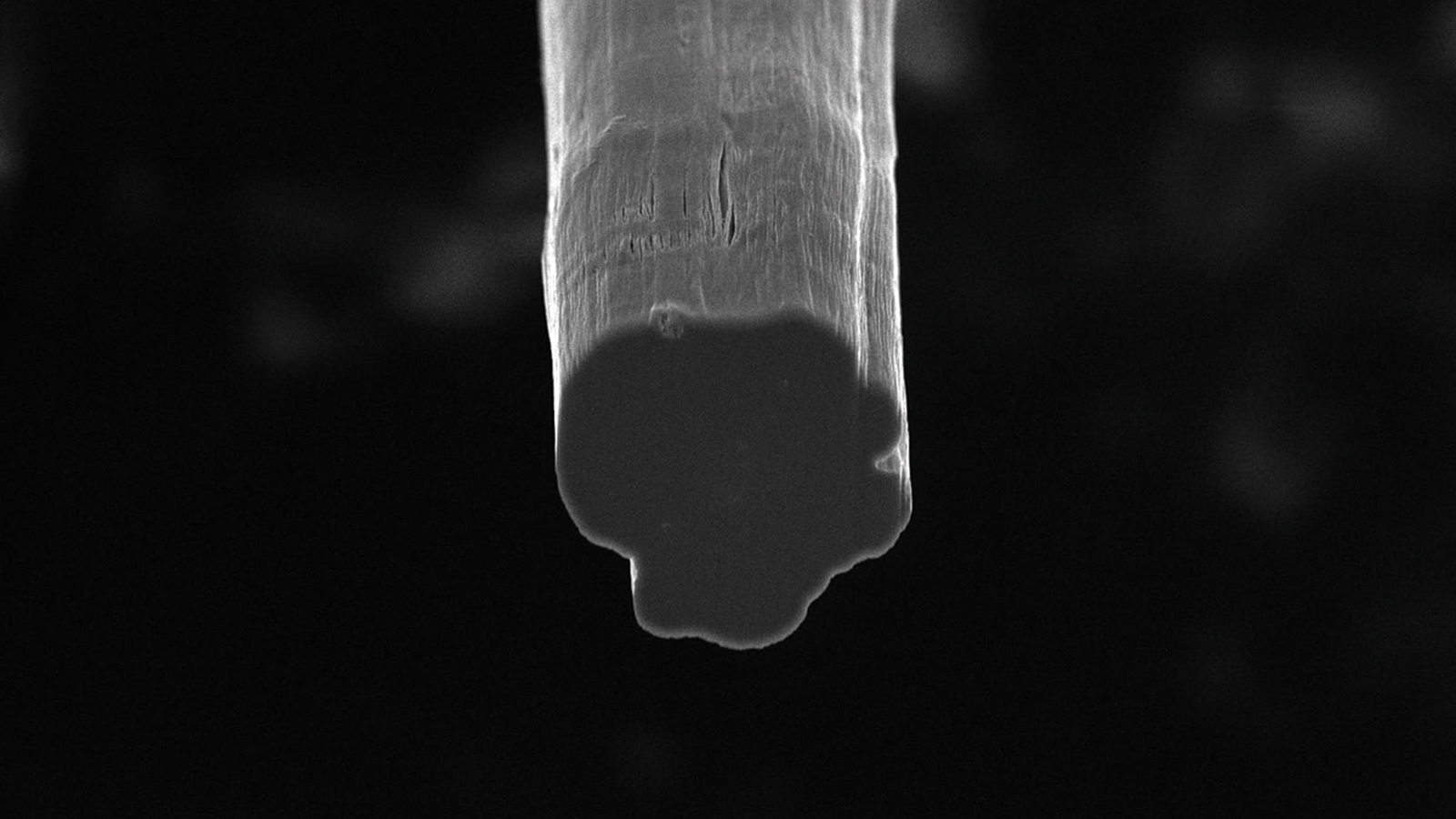
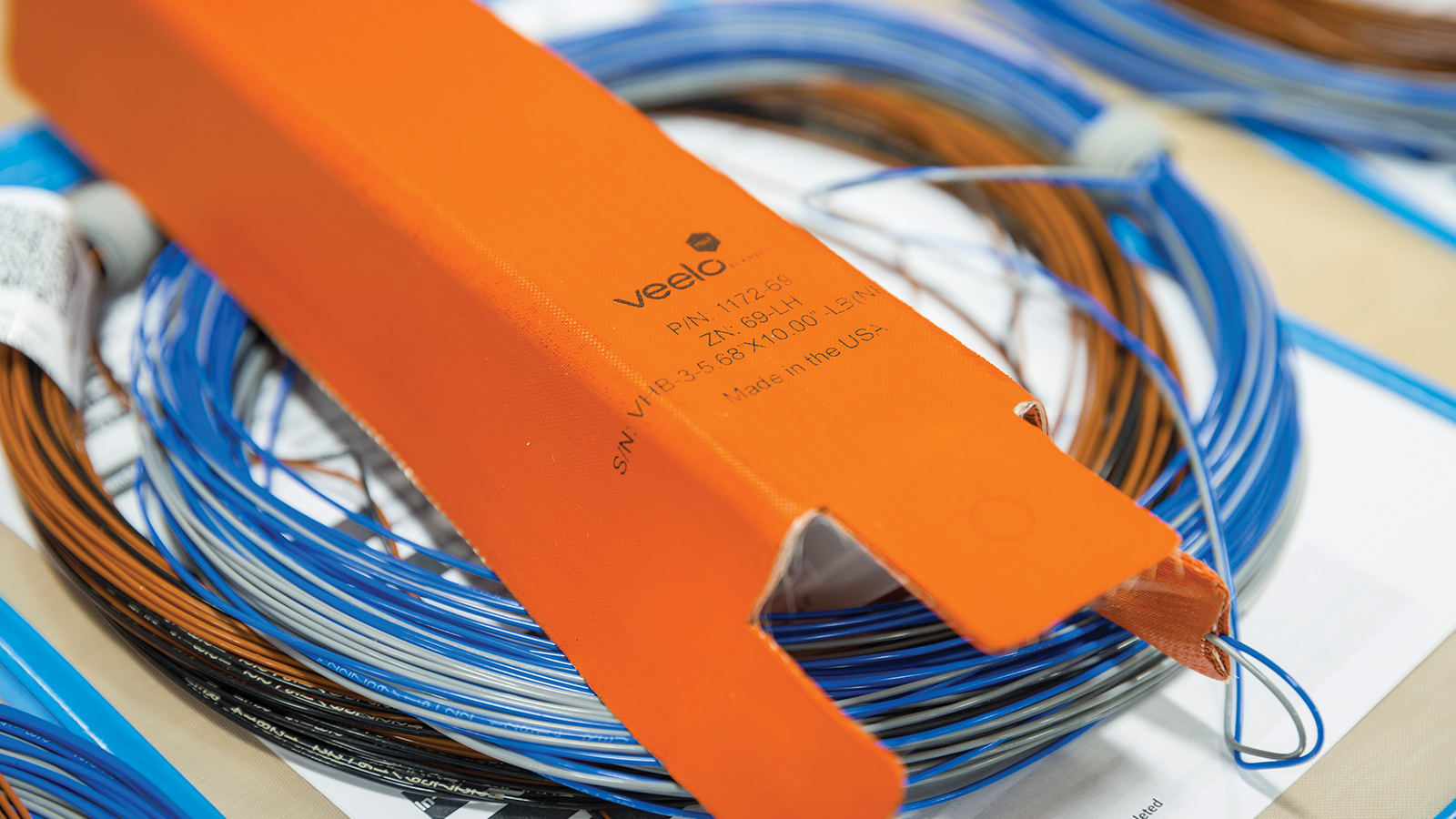
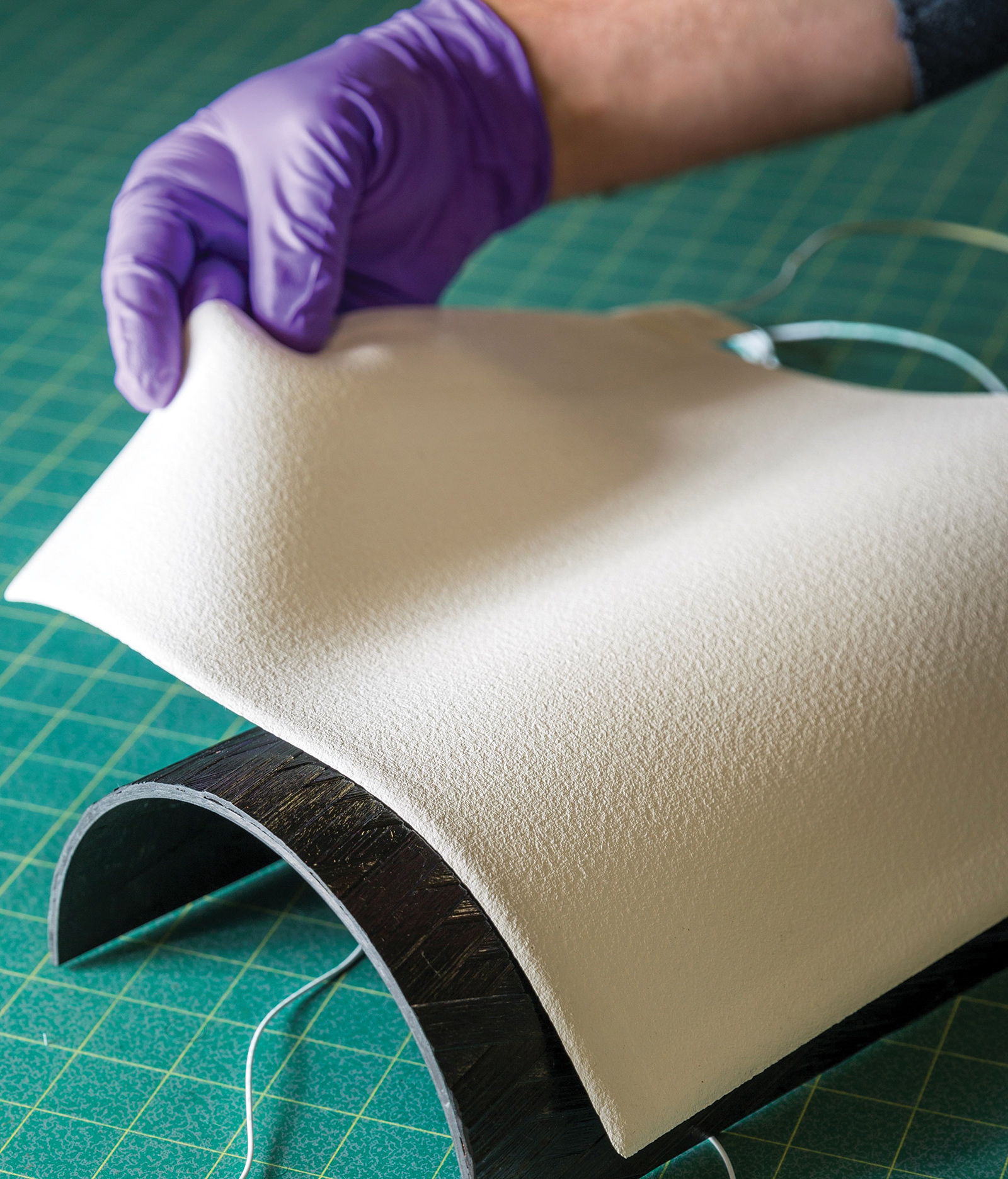
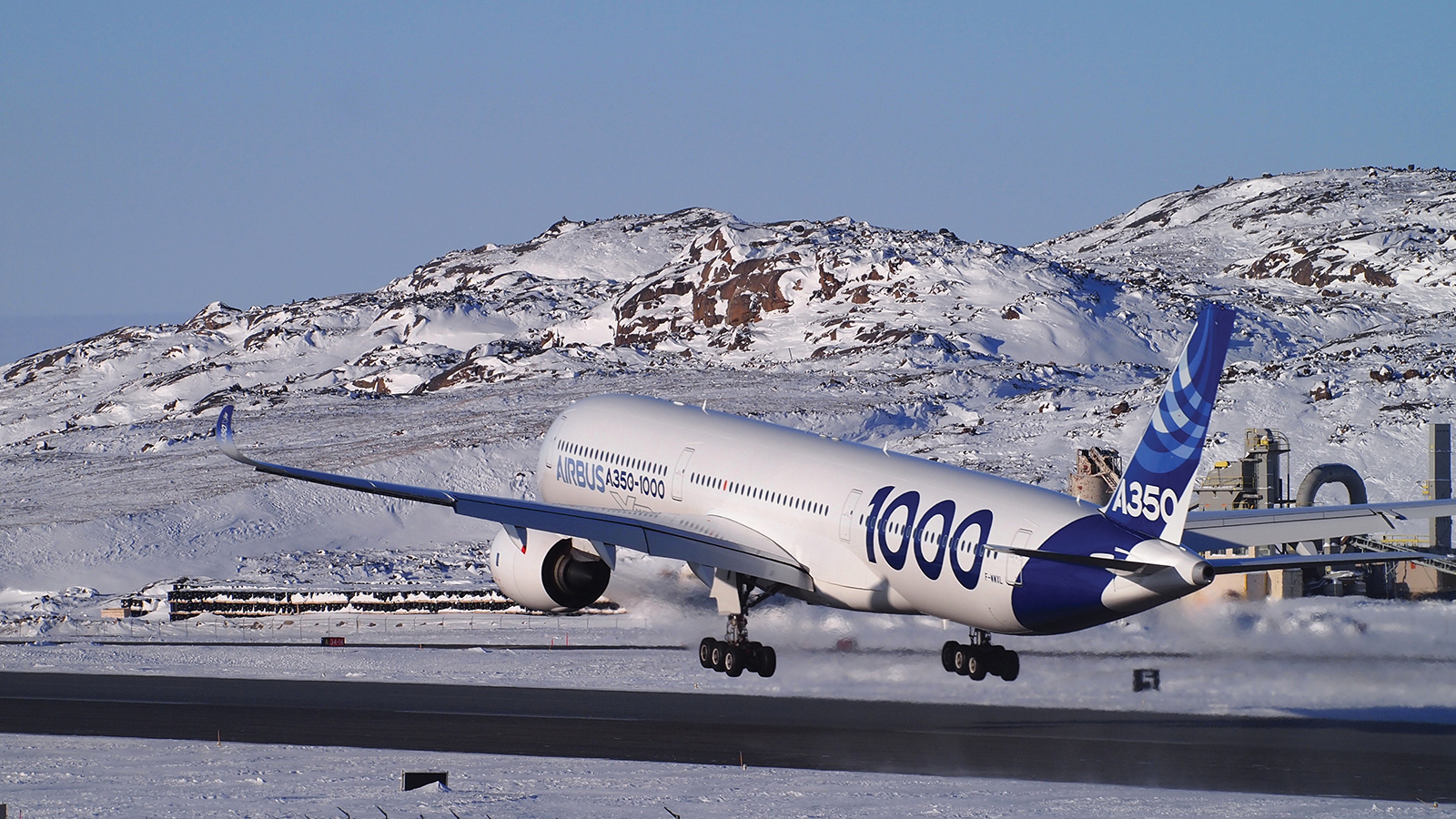