Stay Up to Date
Submit your email address to receive the latest industry and Aerospace America news.
Society has changed in the years since NASA announced it would commission construction of an experimental plane to target sonic booms. Environmental sustainability is now the mantra among commercial aircraft designers and operators, and the industry’s zest for supersonic flight has cooled. With the X-59’s first flight approaching, Paul Marks tells the story of the plane’s remarkable engineering and why NASA still believes it can catalyze supersonic flight for all.
Editor’s note: A previous version of this story incorrectly capitalized one of the letters in the Quesst name.
Sometime in the next few months, Lockheed Martin chief test pilot Dan “Dog” Canin will advance the throttle on a curious-looking paper dart of an airplane and, all being well, take off from a dusty runway at the U.S. Air Force Plant 42 Airport in Palmdale, California. But it will be a very different kind of takeoff roll: With the aircraft’s elongated, super-skinny nose, Canin will have no forward windshield to see the view ahead of him. Instead, he’ll only see images fed by external cameras to a high-definition computer screen in the cockpit. This is just one of many novel features of this bizarre airplane.
The aircraft is, of course, NASA’s X-59, which is being built at Lockheed Martin Skunk Works beside that Palmdale airport. This synthetic vision system is but one tactic for achieving the project’s overarching purpose: to demonstrate that a clever fuselage design can guarantee that someone barbecuing in their backyard or putting their baby down for a nap will hear at most a soft thump, rather than a loud sonic boom, as the plane soars overhead at 55,000 feet, thereby winning community acceptance of overland supersonic passenger flight.
When I finished reporting this story in October, the X-59’s first flight had just been pushed back from December to “early 2023.” After loading and stress tests in Fort Worth, Texas, the engineless and noseless fuselage was back at Skunk Works, awaiting the empennage’s removal so its single engine could be installed and the nose reattached. The result will be a sleekly sculpted, $247.5 million airframe. And everything from the hyper-stretched nose to the T-shaped tail, stubby delta wings, movable control surfaces, horizontal stabilators, swept-back canards and even its engine inlet and exhaust structure are designed to reduce the power of the shockwaves that cause the iconic sonic booms of supersonic jets.
“We are basically tailoring the shockwaves around the entire configuration so that by the time noise reaches the ground, it’s 30 to 40 decibels quieter than any conventional supersonic airplanes you might think of, like Concorde,” explains Mike Buonanno, lead engineer for X-59 at the storied Skunk Works. Hence the program’s official name: Quesst, short for Quiet Supersonic Technology.
If, as hoped, the X-59 produces only a gentle thump in community flight tests over a wide variety of rural and urban locations across the continental United States — which have yet to be selected — that could prompt the United Nations’ International Civil Aviation Organization, and the national regulators who follow ICAO’s lead, to embrace supersonic flight over land later this decade. The first chance to make the case with X-59’s community acceptance results will be in 2028 at the earliest, according to Peter Coen, Quesst mission integration manager at NASA, who leads the agency’s interactions with FAA, and through them with ICAO’s Committee on Aviation Environmental Protection, CAEP.
CAEP, Coen says, has been working for “a number of years” on drafting standards and recommended practices, or SARPs, for supersonic en route noise. “Community response data from NASA’s Quesst mission is key to helping define the noise limits that will be part of that SARP,” he says.
NASA has made a “commitment” to FAA and ICAO to supply the results from the test flights in time for the new SARP to be proposed at the 2028 meeting, he adds.
If booms can indeed be hushed, and ICAO goes for it — and you can afford it, of course — overland trips at Mach 1.4 could seriously cut flight times, with a trip from Los Angeles to New York, for instance, taking just two and a half hours, against the five hours it takes on today’s subsonic airliners.
But, tantalizing as that might sound, the world has changed in at least two relevant ways since June 2016, when NASA announced its intention to commission construction of a series of X-planes, including one dedicated to quietening supersonic technology — X-59.
The first is climate change. The issue was thrust into public consciousness when 15-year-old Swedish schoolgirl Greta Thunberg began a solo sit-in outside the parliament in Stockholm in 2018, demanding action on climate change. As her campaign gathered steam, environmental activists soon began flygskam-ing — “flight shaming” — frequent fliers, and in 2021 the International Air Transport Association ended up calling for net-zero carbon emissions for air travel by 2050. The second blow also came in 2021, when a fierce competition to build supersonic jets fizzled to one active company.
NASA officials are aware of all this, and they and Lockheed Martin Skunk Works have forged ahead with their low-boom innovations.
“There’s a lot of challenges to supersonic transport, and one of the key enablers is suppressing sonic boom noise,” says Jay Brandon, chief engineer for X-59 at NASA’s Langley Research Center in Virginia. “We’re taking one barrier at a time — and we’ll see where it goes.”
Along with being a veteran test pilot, Brandon, not surprisingly, is a student of sonic booms and the long efforts of scientists and engineers to design them away. The U.S. Air Force received some 40,000 noise damage claims in the 1950s and 1960s from Americans regularly harassed by sonic booms from military jets. In 1973, with the British and French Concordes undergoing test flights, FAA banned overland supersonic commercial flights.
“Since the 1960s, this stumbling block for supersonic transportation became a subject of continuous interest and a focus area for NASA, just trying to figure it out. And it took many years of research to come up with this approach that we’re trying to demonstrate here,” Brandon says.
That approach? Although a tech-savvy observer might imagine it would involve the X-59 being peppered with adaptive, boom-killing devices on a fuselage made from a raft of supersmart shape-shifting materials, that’s absolutely not the case.
“It has nothing to do with the materials technology,” says Buonanno of Skunk Works. “On X-59, we’re actually using very, very conventional materials — ones that are very similar to those used on other airplanes, even subsonic airplanes.
“There’s nothing magic about it. It really comes down to the way that we design the airplane’s shape: The way the wings are shaped, the long nose, the canards that help balance the lift that we need to carry on the tail, the way that we integrate the engine inlet and the nozzle,” he says. “The devil’s in the detail — and every single detail matters.”
Shockwave whack-a-mole
Those aerostructural details have to combine to do one crucial aeroacoustic job, says David Richwine, X-59 deputy project manager for technology at NASA Langley: They must kill the N-wave.
Picture a supersonic aircraft such as the Concorde or a warplane side on. In cruise mode, above the speed of sound, shockwaves are generated along the fuselage, but by far the most dominant are the two shockwaves generated by the nose and the tail structures, known as the forward and aft shocks.
Richwine says the message is clear from decades of aeroacoustic analysis, supercomputer-powered computational fluid dynamics simulations and schlieren photography in supersonic wind tunnels equipped with backlighting: The loud sonic booms that so upset people on the ground are caused by the forward and aft shocks merging to create one large boom as the aircraft flies over.
On the ground, this additive process creates a single, loud, disturbing sound pulse, lasting about half a second, and when plotted as pressure against time has a capital N shape — hence the wave’s name. When flying at Mach 2, Concorde created an N-wave sonic boom of 105 decibels — about the same noise level somebody sitting in a car would hear when the vehicle’s door is slammed.
Shockwaves must coalesce beneath the plane to reach that volume, and so the trick is to prevent them from ever coming together. The different aerodynamic shaping of the space shuttle orbiters compared to airplanes, for instance, prevented the aft and forward shocks from coalescing, and people on the ground would hear two distinct sonic booms on their Mach 1.5 landing approach. These booms were loud, but neither was as loud as if they had coalesced into one.
“So what we have done with the X-59 is create an airplane that, because of its volume distribution and lift distribution, smooths out the shocks so that, in general, they are of smaller amplitude and are also of similar strength,” says Richwine. “And so they don’t coalesce and form that N-wave.”
Instead, all their predictions suggest the X-59’s sonically sculpted architecture will produce a “thump” of about 75 decibels — equivalent to hearing a car door shut from about 6 meters away.
A packed pick ’n’ mix plane
By “volume distribution,” Richwine is referring to how broad and tall the aircraft cross section can be along its length. And because it needs its long, slender nose to avoid creating high-pressure-generating frontal airflow obstructions that might generate a large forward shockwave, that has presented problems in the build process.
“It’s a long, skinny airplane, and so we don’t have a lot of normal fuselage cross section to put all the systems in,” says Brandon. “So it’s a real packing and integration challenge to get everything in that we need to fly a supersonic piloted airplane.”
And because the innovation with X-59 is its sonically sculpted shape and not the systems within it, Brandon says they decided “not to invent a whole bunch of new things. So we tried to use all the parts that we could from other airplanes.”
And they have done that, as you can see in the box.
Turning to off-the-shelf components saved the program cash, but that’s not the whole story.
“It’s an opportunity, but one that also presents challenges: The opportunity is that we don’t need to fund development of bespoke systems for this aircraft, so that’s good, because it allows us to minimize investment while delivering the product,” says Buonanno.
“The challenge comes in the integration, because now we’re taking systems from different aircraft, which haven’t necessarily worked together before. So making sure we have good interface control, both in terms of hardware and software, is a large amount of work. It’s not inventing new technology, but it requires a lot of diligence and attention to detail.”
Synthetic vision
Where the X-59 team has most definitely invented new technology is in that artificial vision system that test pilot Dan Canin will be using in the cockpit. Aviation fans may immediately find this part reminiscent of the Spirit of St. Louis, the single prop Ryan monoplane that Charles Lindbergh flew from New York to Paris in 1927. Because Lindbergh chose to have a capacious fuel tank forward of his cockpit, he had no vision straight ahead — and so had to use a periscope to see where he was going.
Similarly, the X-59 will have no optical forward vision because the cockpit sits so low in the slim, dart-like fuselage, there is nowhere on the elongated nose to site a forward cockpit windshield with any useful amount of a view. So NASA developed a synthetic imaging system, which it calls the eXternal Vision System, XVS. Two cameras — one topside in a small raised bump on the nose between the aluminum canards and another beneath the fuselage — feed video of the external world to a 4K widescreen monitor right in front of the pilot.
The camera on top is a higher-resolution imager, designed for “see-to-avoid” type tasking, says Richwine, while the one beneath the plane is largely used for “see-to-land.”
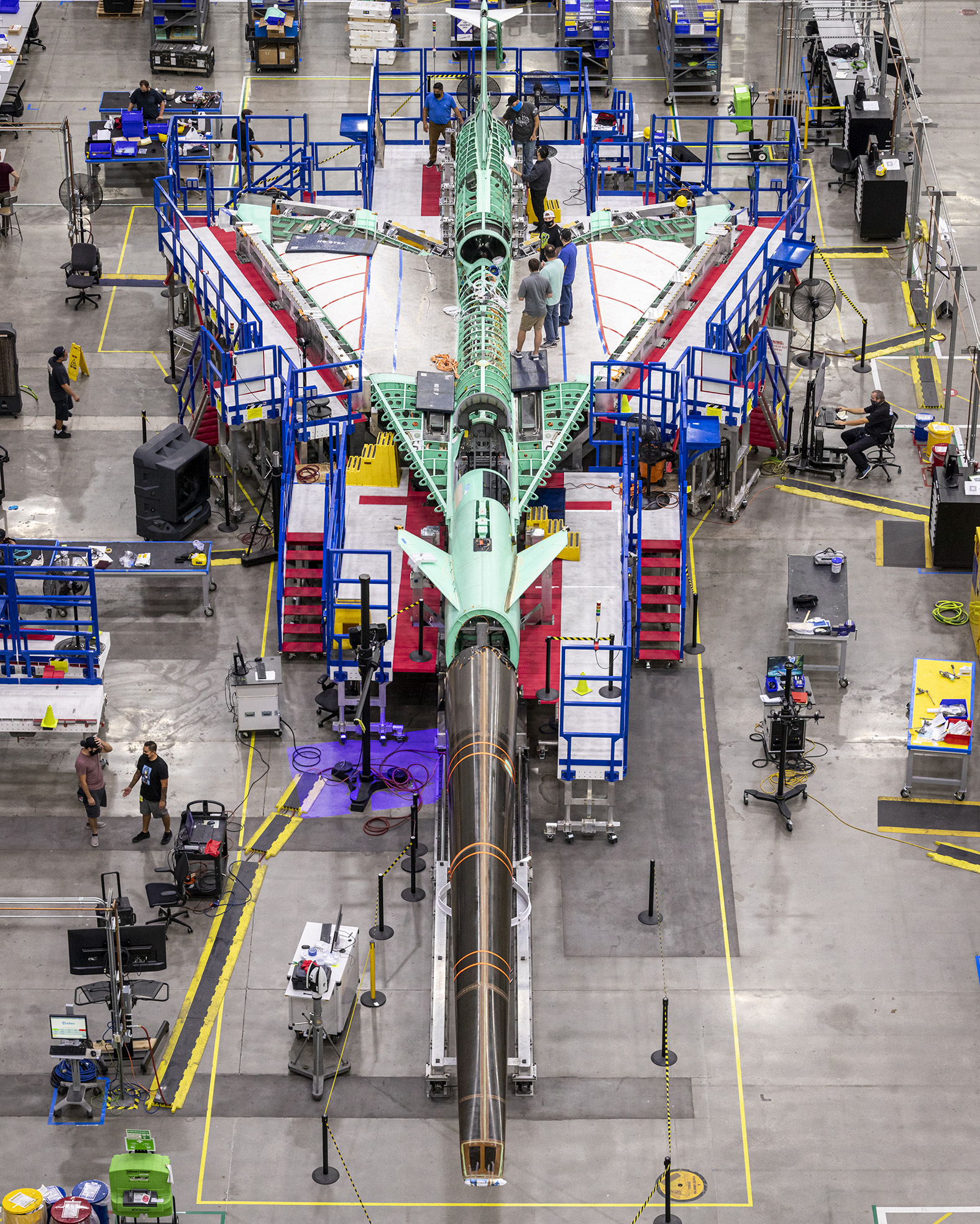
“The beauty of this computer imagery is that you can merge the camera with ADS-B technology and your head-up display and fuse an image that gives you a lot more information than even a pilot would have regularly,” he says, referring in part to Automatic Dependent Surveillance-Broadcast, the GPS and identity broadcasts that are transmitted and received by commercial aircraft and received by air traffic control antennas.
“For example, we box cooperative traffic that the pilot can’t even see yet. We can tell them that it’s there.” That said, like the Spirit of St. Louis had side windows, the X-59 also has small “eyebrow” windows at the pilot’s sides, so the pilot has some peripheral vision should the XVS fail.
Nozzles on deck
Although X-59 is not replete with multitudes of novel gadgets like XVS and the aircraft is made from conventional aviation-grade aluminum and carbon fiber composites, there is still much innovation in the choices the team made about its structure. For instance, right at the back, there is a small flat area behind the engine outlet nozzle called the aft deck that works alongside adaptive elements of the engine to limit boom magnitude.
“We have a variable nozzle on our engine,” says Buonanno, “so as the pilot changes the throttle setting, the nozzle changes both the amount of thrust it makes and also its external shape. And so we had to carefully integrate that nozzle with the aft deck to attenuate the impact of the nozzle on the sonic boom.”
Another boom-limiting decision was to mount the engine atop the delta wing jet, rather than sling it underneath it in a nacelled pod.
“The airflow that goes into the inlet is hard to model. So if the engine were below the wing, it would be a big modeling problem. But since it’s above the wing, the shocks from it are going to go upwards, not downwards,” says Brandon.
The result: They don’t have to be so precise in their computer modeling of the engine.
While that helped the Quesst team, how useful might it be to would-be commercial supersonic operators? The answer is not much immediately, but perhaps a lot later in the decade.
Boom Supersonic, the Denver startup borne out of the same Silicon Valley business incubator Y Combinator that spawned Airbnb and Reddit, is targeting 2025 for the rollout of the first prototype of its Overture supersonic airliner, a design that would fly at Mach 1.7 over water and Mach 0.94 over land to comply with FAA’s prohibition.
With four podded engines slung beneath a delta wing, Overture won’t have much resemblance to X-59 — visually or audibly.
“Because Overture will only fly supersonic over water, it does not include low-boom design features,” Troy Follak, senior vice president in Boom’s Engineering and Program Office, told me by email. “In future generations of Overture, we may explore different engine placements and configurations.”
Also, Spike Aerospace of Boston tweeted in August that it is “getting ready to reveal its plans for supersonic flight,” which center around a mooted, 18-seat business jet. Founder and CEO Max Kachoria said in response to emailed questions that its S-512 design “already incorporates advanced aerodynamics that will reduce the sonic boom tremendously,” but the company is “looking forward to the data [X-59] will provide regarding supersonic aircraft design and overland noise tolerance.”
It’s in these future generations of aircraft that the X-59 team might see the results of the forthcoming test flights. Also, work will continue on the analytical tools (which NASA will open source) that led to the flights. For now, they seem supremely confident that the results from their community flights will presage a new era of faster flight.
So it’s eyes on the skies for the new year: Five to 10 checkout flights will be made from Palmdale, says Richwine, followed by envelope expansion to subsonic and then supersonic flight over the next seven to nine months. After that, there are nine months of atmospheric tests above Edwards Air Force Base, with an instrumented F-15 following X-59 to probe its near field shockwaves.
After that, it’s down to that most serious of tests. The air data can say what they like; it’s the ears of the American public that will have the final say.

About Paul Marks
Paul is a London journalist focused on technology, cybersecurity, aviation and spaceflight. A regular contributor to the BBC, New Scientist and The Economist, his current interests include electric aviation and innovation in new space.
Related Posts
Stay Up to Date
Submit your email address to receive the latest industry and Aerospace America news.
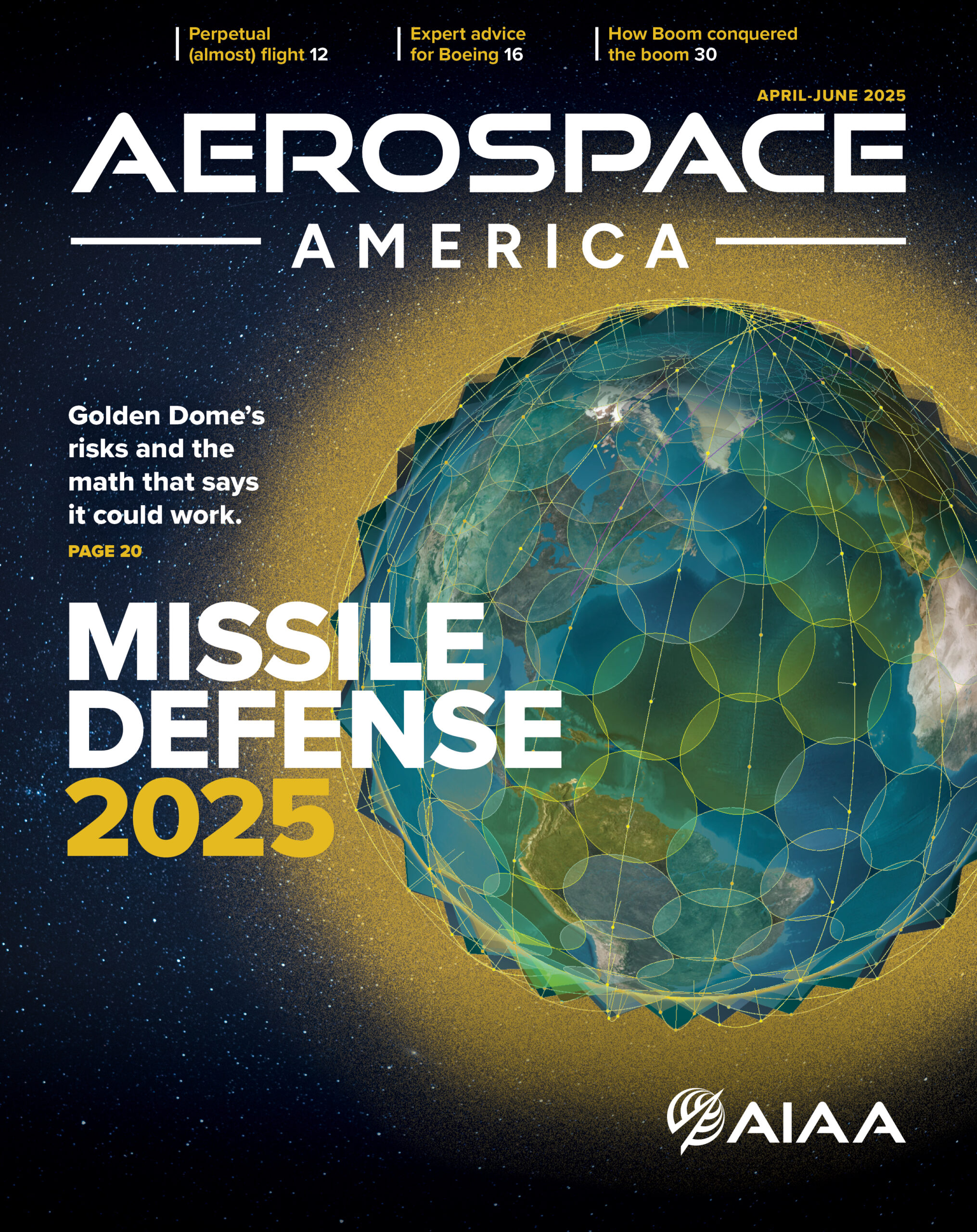