Stay Up to Date
Submit your email address to receive the latest industry and Aerospace America news.
Whether electric rotorcraft will whisk passengers across town in the near future will depend largely on the performance limits of lithium-ion batteries. Will superior lithium batteries be ready in time to meet the urban air mobility demands? Keith Button went looking for answers.
In one vision of urban air mobility, passengers will wait in line for their turn to ride across town in an electric rotorcraft, much like skiers waiting in line for the next gondola to take them up the mountain.
Ella Atkins, director of the Autonomous Aerospace Systems Lab at the University of Michigan and an avid skier, sees a problem with this vision. Most of the UAM concepts she’s familiar with assume that the aircraft will be powered by lithium-ion batteries, but as matters stand today, those batteries will need to be recharged regularly, probably even after every flight. Once a UAM touches down, “there’s going to be this whole: ‘All right, get comfortable while we recharge or replace the batteries,’” Atkins says.
That’s just one example of how Atkins and others want UAM entrepreneurs and developers to look realistically at their business plans in light of the pace of development of lithium-ion battery technology. Topping the list is energy density, the all-important ratio of electric power to a battery’s weight or volume. If the ratio is too low, then the plane can’t fly far enough with enough passengers to make the business case close.
Opinions vary, but some see a great reckoning coming, one that could leave UAM entrepreneurs scurrying to revamp their cost projections and business plans.
The UAM universe is so large that it’s perhaps impossible to make one statement about power requirements that would hold true for every design. The World eVTOL Aircraft Directory counts 226 vertical takeoff and landing concepts with battery electric power or hybrid-electric power in which combustion engines contribute to the propulsion. That count doesn’t include defunct designs, hover bikes or personal flying devices. For the larger designs, the Advanced Air Mobility Reality Index compiled by Phoenix-based SMG Consulting identifies the 20 UAM manufacturers that SMG believes are most likely to bring their aircraft into service for passenger flight. To make the list, a company’s design must target at least 227 kilograms of payload capacity, which typically equates to four to six passengers. Currently on the list are 14 electric and six hybrid-electric designs.
Battery predictions
Battery scientist Venkat Viswanathan, a Carnegie Mellon University assistant professor, is one of those who is upbeat about battery technology. By 2025, he predicts, UAM aircraft designers will have plenty of lithium-ion designs to choose from, each offering enough peak power and a high enough energy density for the aircraft to meet goals for range and speed. Viswanathan and 24M Technologies Inc., a Cambridge, Massachusetts, battery developer, are developing batteries for a UAM company that’s asked them not to disclose its identity.
In Viswanathan’s view, 400 watt-hours per kilogram at the cell level is the “magic number” for energy density that will unlock the potential for most electric-powered UAM designs in the 2025 time frame. Viswanathan says he has helped develop battery cells — separate from the 24M Technologies work — at close to the 400 mark. With more engineering and design work, thousands of such cells could be assembled to form a battery with an energy density of 250 Wh/kg. The battery for a Tesla Model 3, a benchmark for current technology because it is by far the most produced and analyzed electric car battery, falls well short: An energy density of 250 to 270 Wh/kg at the cell level and about 170 Wh/kg for the battery itself, Viswanathan says. Today’s aviation batteries flown in scaled-down UAM prototype aircraft have energy densities that are better than Tesla 3 batteries at the cell level — 280 to 300 Wh/kg — but only about the same energy densities for the batteries — 160 to 180 Wh/kg. That’s because each aircraft has multiple batteries, which are less efficient than having one battery per vehicle, and they require more battery packaging than in electric cars to meet stricter aviation safety requirements.
Perhaps Viswanathan and others will prove to be right, but the question for UAM entrepreneurs is how closely they should tailor their plans to such best-case scenarios. Some startups are counting on the necessary energy densities being available by a certain year, along with FAA certification in that year, without accounting for the fact that the FAA will require them to freeze their designs before beginning the certification process that will likely take four or five years, says Glenn McDonald, a principal at AeroDynamic Advisory, an aerospace consulting firm in Ann Arbor, Michigan. And even aside from the battery projection issue, nearly every UAM entrepreneur is failing to factor into their business plans the yearslong commitment required by the FAA or its European equivalent, the European Union Aviation Safety Agency.
“I haven’t seen any real timeline out there that has a reasonable development and certification timeline associated with it,” McDonald says.
Making unrealistic assumptions about future batteries can also drive up costs, says Gur Kimchi, who co-founded Amazon Prime Air, the proposed drone delivery service, and now serves on the board of Ascent Aerosystems, a Massachusetts drone builder. If the batteries aren’t already available and the UAM company is counting on a unique aerospace battery to be developed just for its aircraft, then the vehicle is probably going to be too expensive for UAM passengers to fly in it, he says. Also, the UAM designer can’t know for sure the energy densities of the batteries, how much peak power they will provide, whether enough batteries will be available for purchase, their cost and how many recharge cycles they’ll have. If the batteries can’t provide 1,000 to 1,200 recharges, then the UAM operator will have to buy new batteries too frequently for the economics to make sense. A UAM operations model developed by AeroDynamic Advisory estimates that batteries will be capable of providing energy density of 200 to 300 Wh/kg by 2025 at a cost of $400 per kilowatt hour of capacity, which is about four times the cost per kilowatt hour of a current Tesla 3 battery. That would put the total cost of a 2025 UAM battery at $40,000 to $80,000.
Also critical is the amount of energy that a battery can retain as it ages. An electric car with an 8-year-old battery might lose 20% of its original 500-kilometer range, but the remaining 400-kilometer range is still valuable to the owner, because there are numerous destinations within that range. But for an electric aircraft battery, the same 20% loss would leave the aircraft with an effective range of zero, because so much energy must be expended on takeoff that the battery could not deliver enough electricity for the almost equally energy-hungry landing phase. “Pretty much all aviation batteries today for the UAM applications are currently limited by their inability to land once the battery ages,” Viswanathan says.
Fire safety will also affect the future battery energy density numbers. Battery developers don’t know yet what aircraft safety regulators will require for UAM battery packaging that prevents thermal runaway — a fire in one cell that spreads to other cells. The packaging adds to the weight of the battery, reducing its energy density. Current aircraft lithium battery packaging requirements are so strict that those that provide backup power on airliners have an energy density of only 64 Wh/kg, partly because the cells are separated by polymer barriers and each battery is encased in a stainless-steel box. UAM designers and their battery developers see the current regulations as an overreaction to the Boeing Dreamliner 787 lithium battery fires in 2013, and they are betting that regulators will allow UAM batteries to have more lenient standards, Viswanathan says.
Cooling the UAM batteries could also add weight to the battery designs. The batteries designed for UAM aircraft rely on passive cooling from air flow, but they may need liquid cooling piped through the batteries, like the glycol cooling loops for Tesla batteries, Viswanathan says.
Budgeting battery energy
Batteries will be able to provide only a limited amount of energy during the course of a UAM flight, even with the energy densities predicted in a few years. That means analysts are paying close attention to predictions by UAM designers of how much time their aircraft will spend taking off, the most energy-depleting portion of the flight. For David Wyatt, an eVTOL analyst at IDTechEx, a research firm in the United Kingdom, the electric UAM aircraft that can demonstrate with prototype flights that they can take off without spending a lot of energy will have the best chances to be deployed by the end of the decade. Those aircraft will have more flexibility to handle longer flights and emergency situations.
In their attempts to accommodate limited battery energy densities, some UAM aircraft developers have made unrealistic assumptions in budgeting power and time for the vertical takeoff and landing portions of flights, Kimchi says. By understating the length of time in these power-draining flight periods and underestimating adverse flight conditions due to things like high temperatures, bad weather, wind gusts and aborted landings, they’re not providing an accurate depiction of their proposed flight operations.
“You can make a given airplane design look better than it is by limiting some of the worst-case scenarios that it needs to handle,” Kimchi says. “I care about how you handle off-nominals and emergencies; that’s really the only thing I care about.” The designer can’t just tell the certification agency that under certain flight conditions, “Well, I’m sorry, I can’t land.”
To cope with range uncertainties, regulators might need to require eVTOL aircraft to operate out of conventional airports whose runways would provide some margin for error. An aircraft that ran out of power toward the end of a flight or that needed to make an emergency return, could at least reach the end of a runway. Right now, most UAM developers plan to fly in and out of vertiports constructed on the ground or the tops of buildings.
If an aircraft can’t operate in adverse conditions, its dispatch reliability — the percentage of time it flies without delays or cancellations — goes down. And if your dispatch reliability dips below 90%, customers will abandon you, Kimchi says.
Airplane safety certification will require that UAM aircraft always maintain a minimum battery energy reserve to reach a nearby airport, though it seems likely that the FAA and EASA will be open to a shorter time than the 20 minutes now required for commercial air taxi service or charter flights, says Martha Neubauer, a senior analyst at AeroDynamic Advisory in Ann Arbor.
Batteries could make matters easier for UAM developers in one respect: The distributed propulsion designs of electric UAM aircraft provide some safety advantages over traditional designs, Viswanathan says. The UAM designs typically allocate one battery for every two rotors, so if a battery fails, the aircraft can continue flying.
Adapting business plans
UAM manufacturers and operators could be prompted to adapt their business models once they discover the limitations of their batteries in real-world operational scenarios. The companies that raise enough capital from investors will get their aircraft certified and bring their aircraft to market, even if the aircraft don’t make sense economically, Kimchi predicts.
But a good business case can be made even when battery limitations dictate short flights, Atkins says. “I suspect that those who have the financial means to fly regularly on a helicopter are going to be all over an eVTOL alternative because it’s going to be quieter; it’s going to be cooler, sleeker, fun.”
Some companies might modify their business plans by switching from electric-only designs to battery-plus-combustion-engine hybrid designs for added propulsion and generation to lengthen their flights. But doing so will erase one of the main UAM selling points, Wyatt says. “To sell a concept which still results in CO2 emissions is probably not quite as desirable,” he says. “When it comes to the kind of environmental-credentials side of things, everything is going zero emissions and lower emissions.”
And some companies — Piasecki Aircraft of Essington, Pennsylvania, and Russia-based Bartini Aero, for example — are developing electric UAM aircraft powered by hydrogen fuel cells, which in theory would avoid the range and performance problems that battery-only-powered designs present.
Hybrid-electric UAM designs — those generating electric power with combustion engines and those generating electric power with hydrogen fuel cells — would be giving up one of their main cost advantages: running only on electricity instead of paying for aviation fuel or hydrogen, Wyatt says. “Suddenly you’re paying for fuel, and the fuel overhead becomes a part of that calculation as well,” he says. “That’s going to be an issue for operators as well, whether they can make a viable business while they’re still having to pay high fuel prices.”
In the future, aerospace engineers might reflect on today’s lithium-ion batteries and their shortcomings like engineers now look at the star-shaped piston engines that powered World War II-era planes. Tomorrow’s energy storage solution might be a better lithium-ion battery design or something else entirely.
“We created things like radial engines that were all the rage,” Atkins says. “When we go to an air show, we want to hear them. But now we look back at that and we’re like: ‘You know, these things sounded cool, but they were really inefficient and unreliable. But they were useful, and they got the jobs done.’”

About Keith Button
Keith has written for C4ISR Journal and Hedge Fund Alert, where he broke news of the 2007 Bear Stearns hedge fund blowup that kicked off the global credit crisis. He is based in New York.
Related Posts
Stay Up to Date
Submit your email address to receive the latest industry and Aerospace America news.
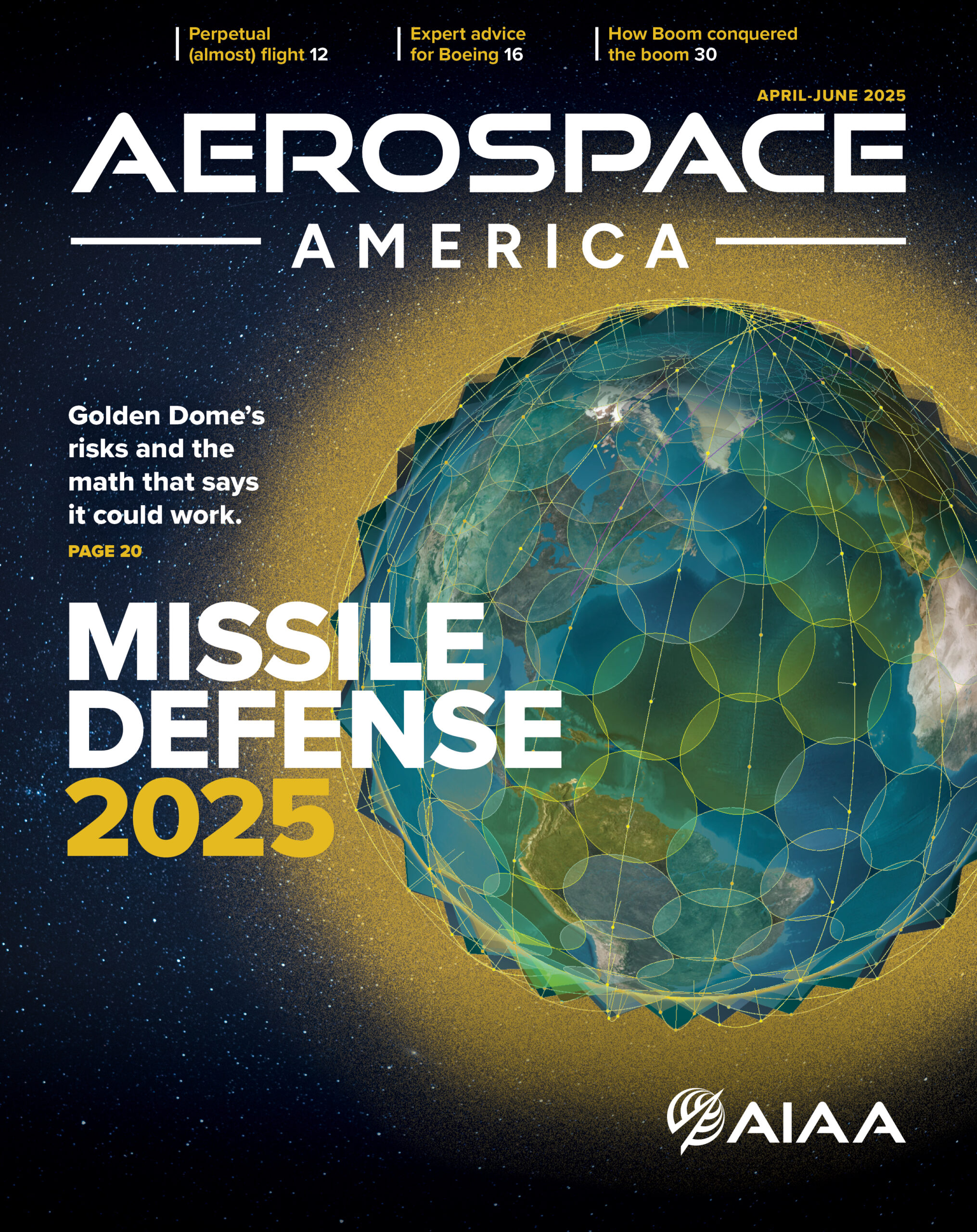
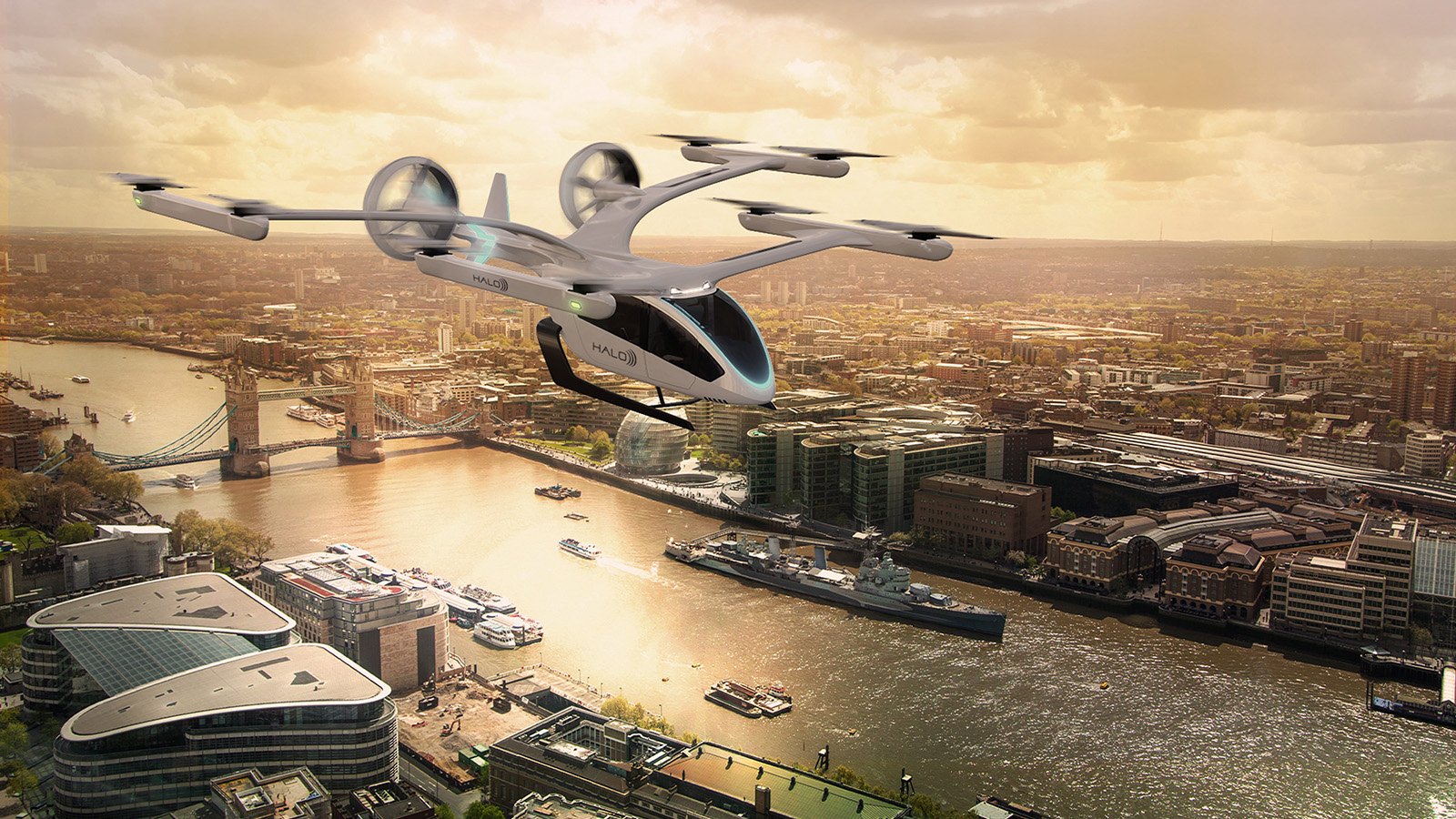
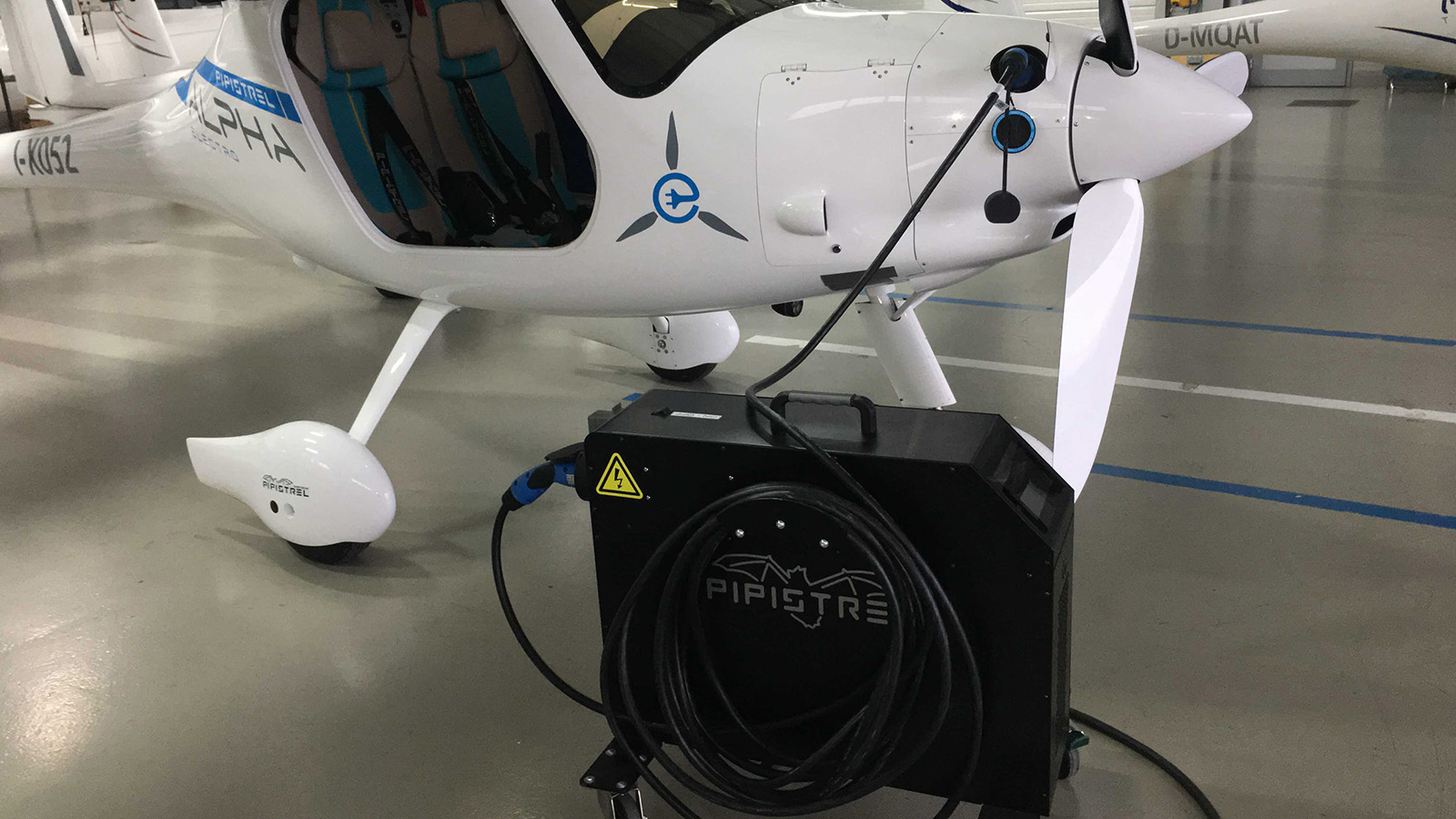