Stay Up to Date
Submit your email address to receive the latest industry and Aerospace America news.
Hundreds of startups are betting that electric aviation will finally provide safe, affordable urban air mobility services. But certifying the airworthiness of their myriad vertical takeoff architectures faces some stiff challenges.
On a Monday evening in May 1977, the landing gear on one side of a New York Airways commuter helicopter collapsed as it was picking up passengers atop Manhattan’s 59-
story Pan Am Building. The spinning rotors struck bystanders and passengers waiting to board, killing four. A fifth victim died on the ground, a block away, when falling rotor debris struck her as she waited for a bus.
That gruesome accident saw the Pan Am Building’s heliport closed forever. But the tragedy has had a further effect: It has become a talismanic example of the risks inherent in trying to use conventional helicopters, with their massive, high-energy rotary parts, to supply gridlock-busting air taxi services in heavily peopled urban areas.
Among those familiar with this case is Mary “Missy” Cummings, a former U.S. Navy F/A-18 pilot with a doctorate in systems engineering who researches transportation safety at Duke University in North Carolina. In studying the economics of such helicopter-based on-demand urban air mobility operations, her research group has found that business models tend to demand that they operate at high flight volumes — and that raises the chances of an accident with their unforgiving, high-energy rotor blades in urban spaces packed with people.
“We’ve tried to have helicopter air taxi services in the past, and they’ve all failed. History has taught us something very important about the economies of scale of rotorcraft-based air taxi services,” says Cummings.
But that situation may not prevail for much longer: At least 100 energetic startups believe urban air mobility vehicles are not only about to become viable in the next few years, but that they will be safer, quieter and greener than anything conventional helicopters can ever offer — due to an ingenious twist in the way vertical takeoff and landing vehicles are designed, powered and fueled.
That twist? With the advent of distributed electric propulsion, tomorrow’s air taxis and other forms of urban air mobility won’t need a single, massive, high-energy, turbine-driven rotor disk plus a tail rotor to counter the resulting torque and assure stability. This emerging breed of lithium-battery-powered electric vertical takeoff and landing, or eVTOL, aircraft will be lighter and propelled by small, electric-motor-driven rotors, located strategically around the airframe, collectively providing lift, thrust and vectoring control.
An accident like the one atop the Pan Am building would be less deadly because there would not be giant rotors slicing toward bystanders or hurtling toward pedestrians below. And, the control architectures of these eVTOL designs might make such a crash even be less likely to happen in the first place.
Simplifying flight controls
With the action of these far smaller, lighter rotors choreographed by software — no rotorcraft pilot could possibly control them all manually — the opportunity exists to greatly simplify rotorcraft flight controls in the short term, and in the very long term move toward fully automated, pilotless eVTOL flight if the public were to accept that automation can, in fact, be safer than a person at the controls.
There is no one-size-fits-all here: The eVTOL concept lends itself to myriad aircraft designs with rotors or ducted fans and counts of such propulsors varying from six to 36. Each design can be geared to different mission profiles, such as intercity or intracity air taxi flights. And as Aerospace America wrote in the July/August issue, plans are already in place to build the vertiports that the eVTOL revolution will demand.
Some companies developing eVTOL technology are experiencing feverish investor interest, especially from special purpose acquisition companies, which are firms with no commercial operations and that exist solely to raise funds through an initial public offering. The cash raised is then used to acquire a target company and to give it the funds to develop its product.
The eVTOL industry’s apparent front-runner, Joby Aviation, for example, was acquired by just such a SPAC, called Reinvent Technology Partners, in August, raising $1 billion on the New York Stock Exchange to fuel Joby’s manufacturing plans. Other eVTOL makers that have announced plans to raise funds via SPACs include Lilium of Germany, Vertical Aerospace in the United Kingdom and Archer Aviation in the U.S.
Driving this interest, in part, are the mind-boggling financial predictions from analysts. Investment bank Morgan Stanley, for example, predicts that the global eVTOL/urban air mobility market will be worth $1 trillion by 2040 and $9 trillion by 2050. And McKinsey, a management consultancy, projects that UAM firms worldwide will need to hire and train 60,000 eVTOL pilots by 2028.
But the analysts are getting ahead of themselves, cautions Cummings, and one should be deeply skeptical of their claims. “I wouldn’t trust them as far as I can throw them,” she says. One reason: Before the eVTOL market can take off, manufacturers have a mountain to climb in the form of gaining airworthiness safety certification from regulators including FAA, the European Aviation Safety Agency and Britain’s Civil Aviation Authority.
But because there are so many ways to design eVTOL aircraft, and since some of their components are pretty new to aviation — such as high-power lithium battery packs, electric motors and electric propulsor/wing tilt mechanisms — many have not been flown in safety-critical air applications before, so airworthiness certification could potentially be a more arduous process than for regular aircraft.
“Distributed electric propulsion is a great idea, a fantastic concept,” says Cummings. She cautions that going from a concept to “some kind of operational, mature technology” is difficult. “Companies need to be in this for the long haul because the certification process is going to be long and costly.”
Promise of improved safety
But proponents say that improved safety should be viewed as an almost innate property of most eVTOL formats.
By distributing lift and thrust across a number of propulsors on an airframe, eVTOL makers automatically provide a critical safety feature that helicopters lack: propulsor redundancy, says aeronautics engineer Mark Moore, founder and CEO of Whisper Aero, a Tennessee startup formed in February to develop ultraquiet propulsors for UAM aircraft. Moore pioneered the concept of distributed electric propulsion in a 30-year career at NASA’s Langley Research Center in Virginia, and then spent four years evangelizing eVTOL concepts at Uber Elevate, which was acquired by Joby Aviation in December.
On a six- or eight-rotor eVTOL, for instance, losing a propulsor to a motor or gear failure, or a birdstrike, would leave enough lift margin for the aircraft to continue flying to a safe landing. And that would be even more the case on designs with as many as 18 or 36 propulsors, as some eVTOL vendors are proposing.
“The vast majority of helicopters are single turbine, so that’s critical. And helicopters have all sorts of different parts that are flight critical, where if any one of them fails, like the tail rotor, it can’t fly,” Moore says. And while a helicopter’s rotors can autorotate and crash land without engine power, its pilot cannot choose where it will land, whereas an eVTOL, due to redundancy, can.
On top of this basic, in-built contribution to safety, he says, there is also the safety proffered by the utter simplicity of electric motors versus that of complex turbines and reciprocating engines. “The true beauty of eVTOL is that these electric motors are very compact, ultrareliable, have one moving part and are amazingly efficient. And once you use them to distribute propulsion, you can distribute thrust and control across the aircraft wherever you want it, very, very nicely.”
“And that,” Moore says, “changes the rules of aircraft design.”
How have those rules changed? Well, the four chief architectures for eVTOL aircraft that address the rotor arrangements, means of propulsion and other factors throw this into sharp relief. See graphic above.
Each of those architectures can in turn be varied in many ways, perhaps by adding lifting surfaces, or attaching more propulsors along wings, or maybe running with combinations of open rotors, tiltrotors and ducted fans.
So how are the backers of some of these architectures attempting to assure safety? One company adopting two of those formats is Volocopter of Karlsruhe, Germany. At the EAA Airventure show in Wisconsin in July, the company flew the Volocopter 2X, a prototype of its planned VoloCity eVTOL, a two-seat, 18-rotor multicopter with a range of 35 kilometers (with today’s battery technology). The company’s winged VoloConnect aircraft, which is still in the concept phase, will be a four-seat lift-and-cruise eVTOL with a range of 100 km, propelled by six lifting rotors and two ducted fans either side of the tail to push it forward.
Oliver Reinhardt, Volocopter’s chief risk and certification officer, says that although eVTOLs are a novel type of vehicle, certifiable standards exist for all of the types of components in their designs, be it motors, on-board electronics or safety-critical flight software. For instance, he says, although the design of the motors in the VoloCity differ in size, shape and electrical characteristics, the certification requirements for the electric motors flown today in some electric light aircraft, like the Pipistrel, apply to VoloCity’s version.
“There is a lot of commonality in the generic set of requirements and the levels of safety that we need to meet,” Reinhardt says.
Volocopter opted for a lift-and-cruise design, rather than vectored thrust, for its VoloConnect eVTOL in part because of the U.S. military’s experience with its V-22 Osprey tiltrotors. Perhaps most infamously, an Osprey crashed into the Potomac River south of Washington, D.C., in 1992 in front of VIPs who had reportedly assembled to watch the new aircraft land in the D.C. area for the first time. All seven aboard were killed. “When you look into the history of the Osprey, military certification development started sometime in the 1980s. But since then, no manufacturer has been able to obtain a civilian type certificate for any tiltrotor or tilt-wing design.” So adopting such technology for civilian eVTOLs, Reinhardt says, might have made gaining certification “extremely complex.”
Vertical Aerospace, however, is going for a tiltrotor-based, thrust vectoring design for its VA-X4, a winged, eight-rotor, 160 km-range eVTOL. The VA-X4 will have four lift-only rotors behind the wing but four tiltable thrusters on the front of the wing that transition from vertical to horizontal flight and vice versa. The firm has major league technology partners, too, in the form of Rolls-Royce, which is supplying its motors, and Honeywell, which is providing eVTOL fly-by-wire control systems.
The company rejected a straight lift-and-cruise design early on, says Paul Harper, head of certification at Vertical Aerospace, because “the vertical takeoff and landing part is, clearly, only used during takeoff and landing. So for the rest of the flight regime, you’re lugging around dead weight.”
“We needed to be able to minimize the amount of pure VTOL kit onboard the aircraft. And the tilting rotors at the front allow us to do that. They buy their place onto the aircraft mass budget by providing the forward cruise thrust. It adds some complexity, but it saves significant weight,” Harper says.
And Vertical Aerospace is unfazed by the Osprey’s record in the military sphere, says Harper. “At the end of the day, the tilting system is an actuation system, and there are safety critical actuators on existing [commercial] aircraft — such as on elevators. We just need to make sure that the consequence of a single actuator failing is benign to the aircraft.”
At Joby Aviation in Santa Cruz, California, the choice of eVTOL architecture eschews Vertical Aerospace’s back line of lift-only propulsors; it is a fully thrust vectoring machine, with all six of its propulsors tiltable for the lift-to-thrust (and vice versa) transition.
Joby’s chief test pilot, Justin Paines, says they “analyzed and tested many, many configurations, including constructing and testing a wide range of subscale aircraft” before homing in on that configuration.
Joby’s road to proving airworthiness, he says, has for a decade been based on engineering “certifiable solutions” — in consultation with FAA. As a former Harrier jump jet pilot, and someone who has worked on the X-35 strike fighter and F-35 human interfaces, simplifying the Joby eVTOL’s controls is a key aim for Paines. “By making the aircraft simple to fly, we can lower pilot workload, thereby reducing pilot error,” he says.
But like most other eVTOL makers, Paines says Joby is in no hurry to go autonomous. “The current design of the Joby aircraft is designed to be flown by a pilot, and capabilities like fly-by-wire enhance operational safety. Clearly there is tremendous potential for increased automation and autonomy over the coming years, and Joby is taking a staged approach to that ultimate goal,” he says.
Moore agrees that autonomy is a ways off yet. “It’s going to be a slow evolution in terms of achieving that fully autonomous eVTOL capability. I’m convinced it’s going to take another 10 years.”
Challenges to eVTOL certification
Despite the general bullishness from eVTOL manufacturers, Jacek Kawecki, former safety lead at Uber Elevate — and now a partner with Moore at Whisper Aero — says there remains a number of challenging aspects to eVTOL certification.
“One is understanding how to certify lithium-ion batteries; understanding their lifetime is a little bit difficult. But when the regulator is unsure, they tend to think more conservatively in the interests of public safety. With time, they’ll understand how to better qualify such unknowns,” says Kawecki.
There is also a trans-Atlantic sticking point in eVTOL certification, says Volocopter’s Reinhardt. EASA wants all eVTOLs certified to the same level of safety as commercial airliners are worldwide, which allows one catastrophic event every 1 billion flight hours (a 10-9 probability).
But the FAA is considering allowing eVTOLs that have a wing to improve energy efficiency in cruise flight — and which can be used to glide to a safe landing after a power loss — to be certified to a 10-7 probability, or one catastrophic event every 10 million flight hours, the same as light aircraft must adhere to, rather than an airliner.
But Volocopter does not see the logic in the FAA allowing 100 times more catastrophic failures in UAM. “That doesn’t make sense with the high numbers of eVTOL vehicles that we all want to have in the air,” says Reinhardt. He hopes EASA’s 10-9 probability will prevail worldwide for eVTOL.
EASA and the FAA are talking it through, both sides confirmed.
“The two authorities are in continuous exchange and dialogue to ensure that the respective regulatory environments will allow a fair and level playing field so as to enable the growth of the global eVTOL market,” says Janet Northcote, head of communication at EASA in Munich. The FAA confirmed that it is working “to align and define” the certification requirements for eVTOL with “international aviation authorities.”
With the Pan Am Building catastrophe in mind, agreeing to raise the threshold of acceptable accident limits might be the best thing the regulators could do. Everybody in the eVTOL community knows that any repeat of that tragic event with their new breed of electric aircraft will leave the UAM industry dead in the water. In May, Morgan Stanley cautioned in its latest UAM industry analysis that the marketing materials of eVTOL companies strongly echo the way New York Airways advertised its commuter helicopter service back in 1962. It is up to the eVTOL industry, and the regulators, to show that, this time, it’s going to be different.
Gauging public acceptance of UAM
The European Union Aviation Safety Agency hired consulting firm McKinsey & Co. to produce a study on societal acceptance of urban air mobility operations. The company surveyed 3,690 people across six European cities between November 2020 and April 2021. Among the top concerns were safety, environmental impact, noise and security.
Among other key findings, 64% said they were rather or very likely to try out delivery drones, and 49% said they would be rather or very likely to try air taxis.
Respondents indicated they were more comfortable with the idea of crewed urban air mobility vehicles than uncrewed. Here are the percentages who agreed with the following statements from the survey:
“As a pedestrian on the ground, I would feel safe with unmanned delivery drones potentially flying above me.” 56%
“As a pedestrian on the ground, I would feel safe with manned air taxis potentially flying above me.” 70%
“I would be interested in trying out a manned air taxi myself.” 75% “I would be interested in trying out an unmanned air taxi myself.” 43%
Source: “Study on the Societal Acceptance of Urban Air Mobility
In Europe,” EASA

About Paul Marks
Paul is a London journalist focused on technology, cybersecurity, aviation and spaceflight. A regular contributor to the BBC, New Scientist and The Economist, his current interests include electric aviation and innovation in new space.
Related Posts
Stay Up to Date
Submit your email address to receive the latest industry and Aerospace America news.
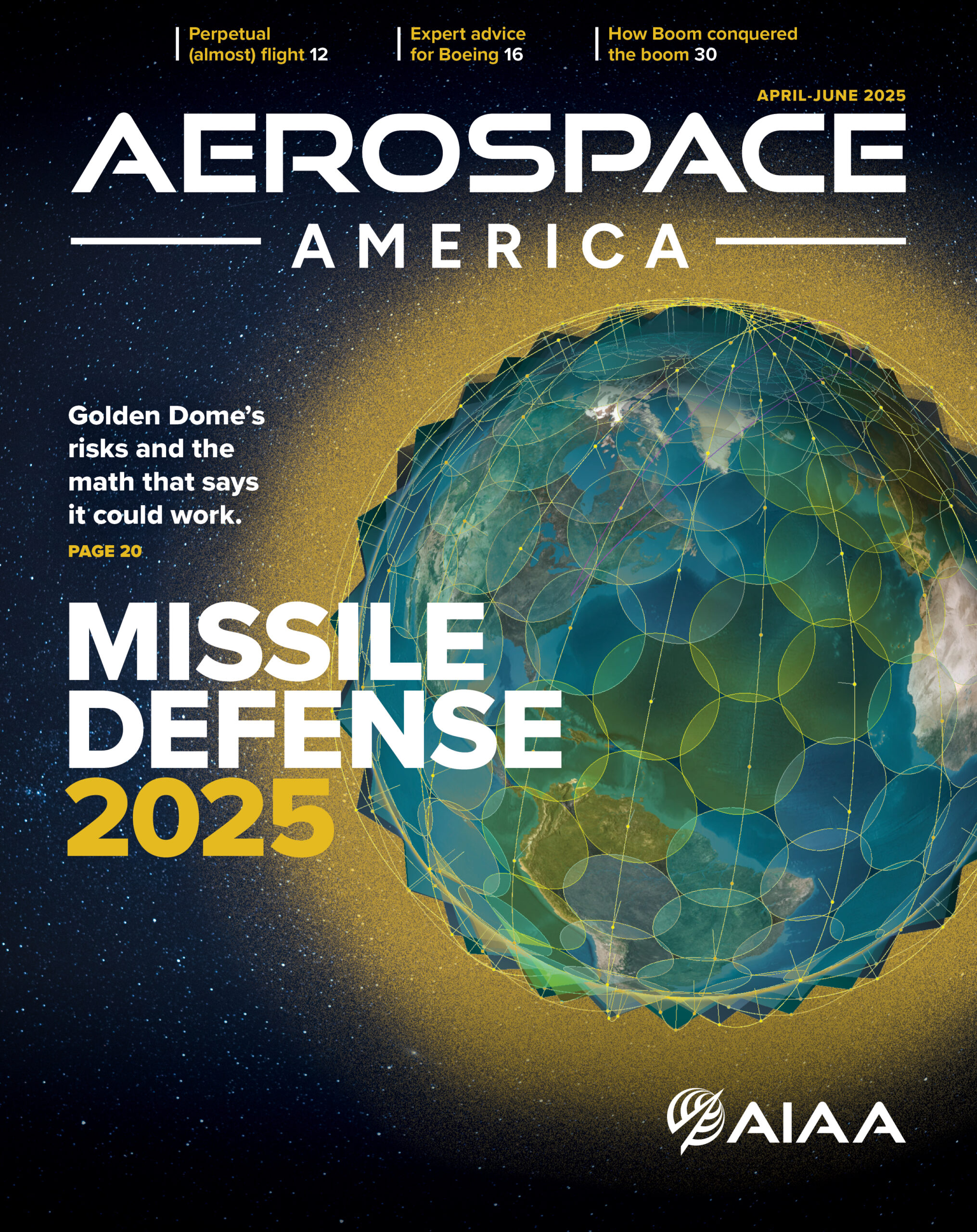

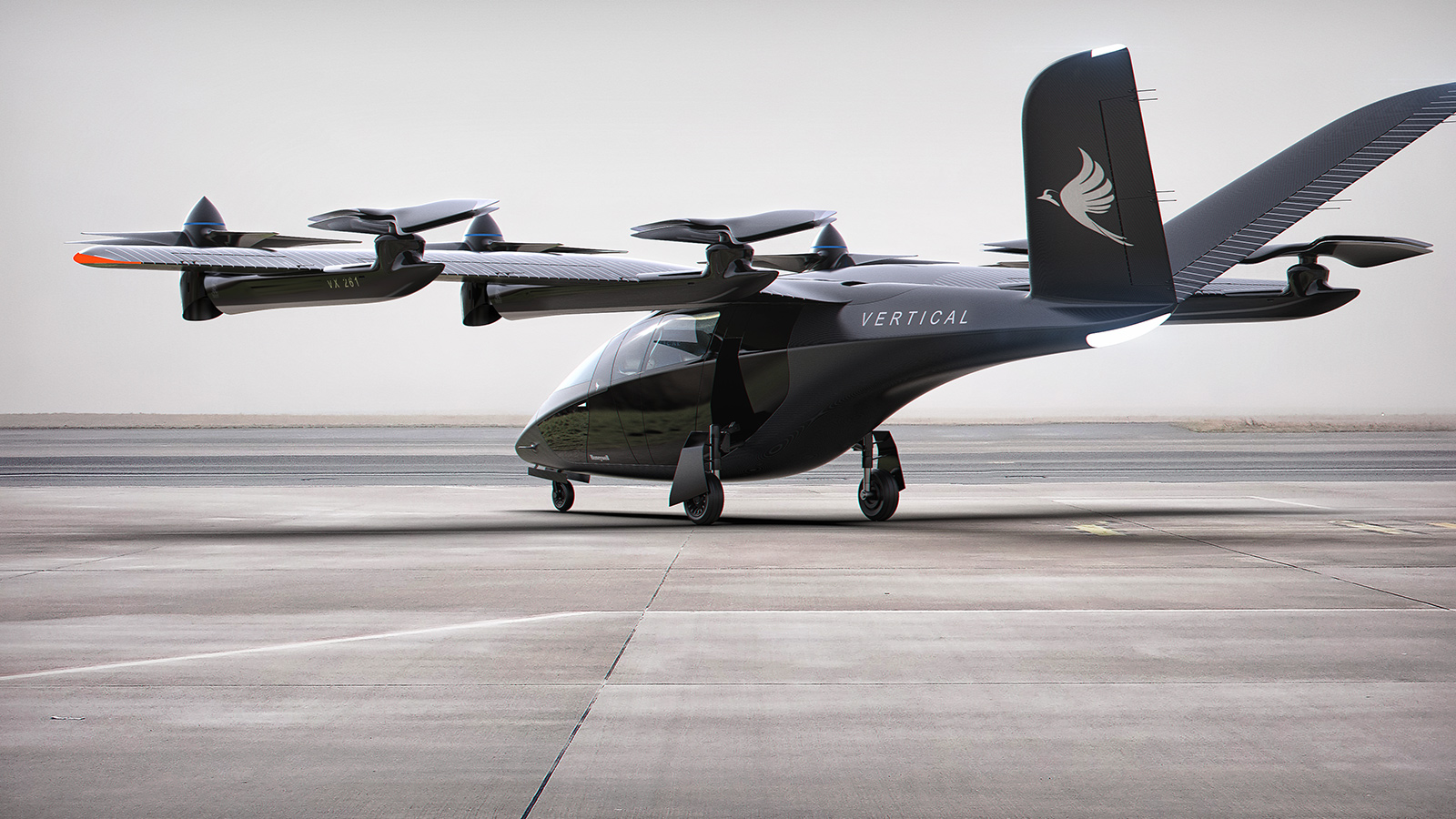
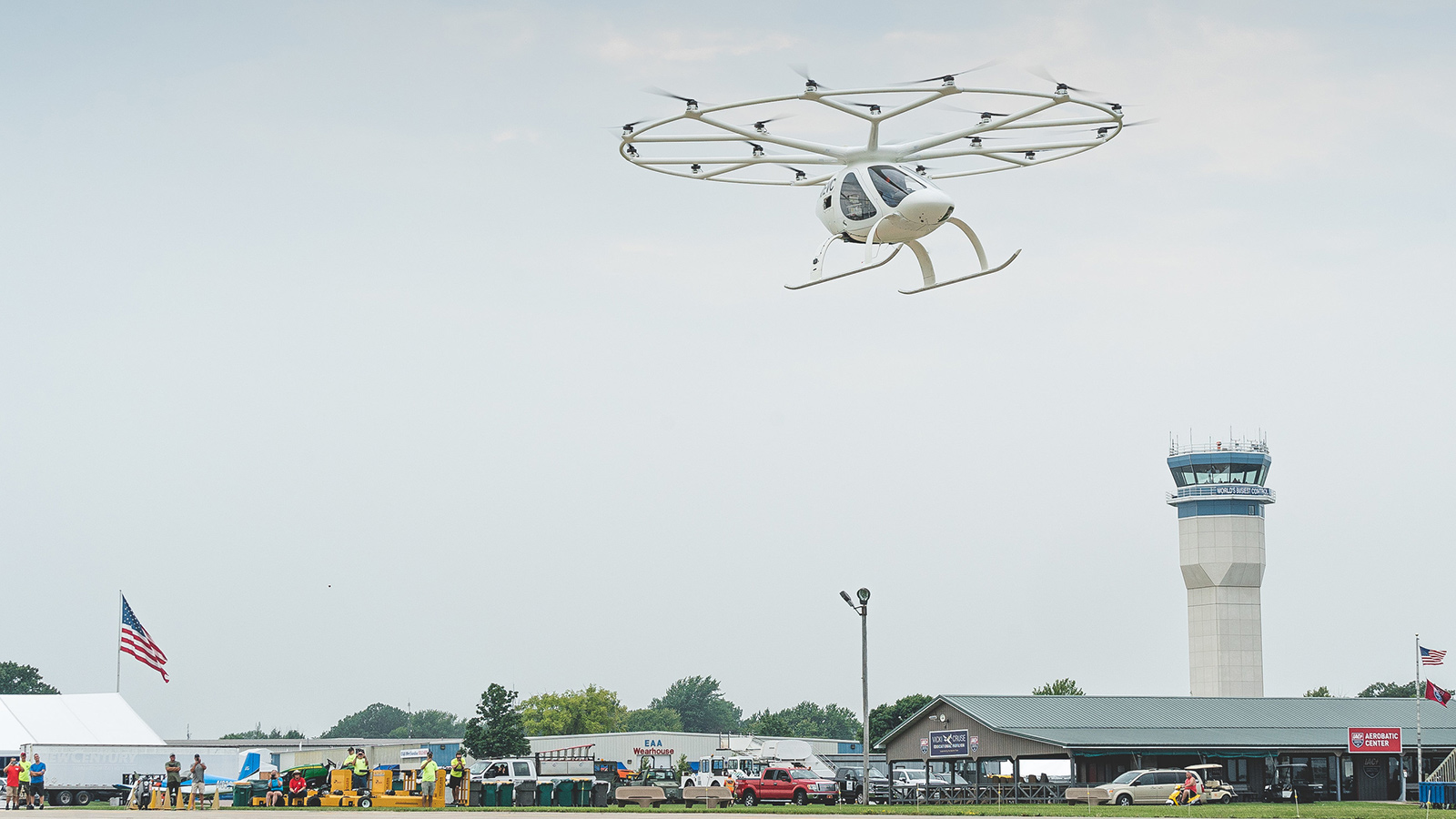
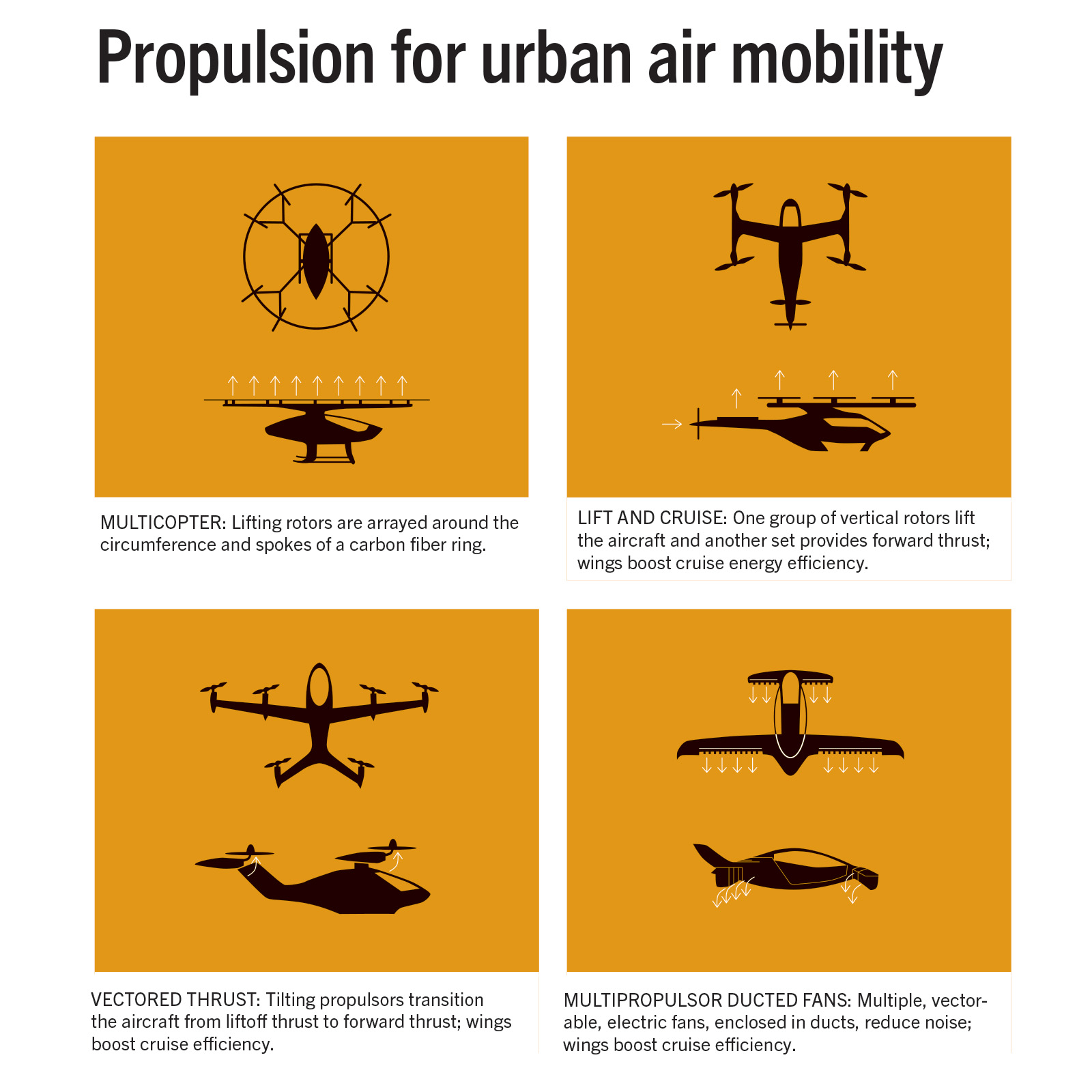